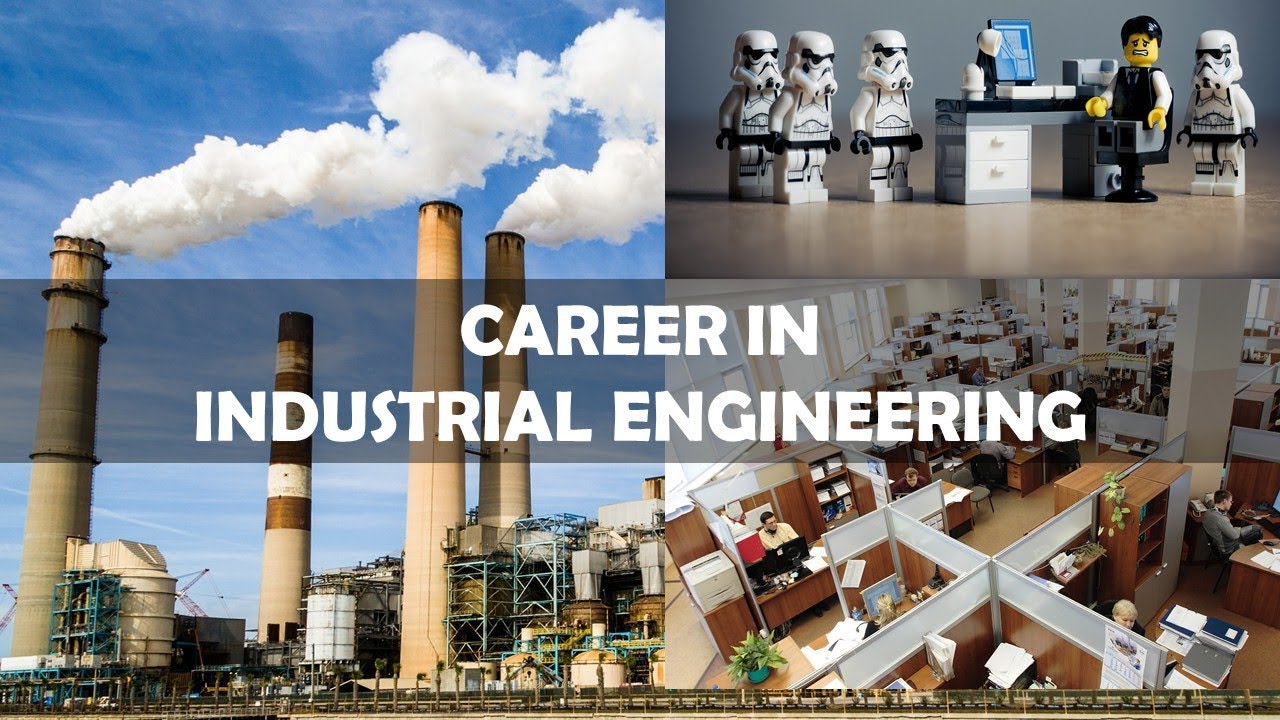
San Diego, whether you're new in the city or just looking to switch careers, is home to some the best logistics jobs nationwide. The jobs available in San Diego range from entry levels to directorships that pay well above $100,000 a yearly.
They are essential to the supply chain of any business. They help move goods from manufacturers to clients. These jobs also include those that deal with warehousing, storage, inventory management and distribution.
There are many large companies in the United States that have their own logistics departments. General Dynamics is one of them, as are BAE Systems or NASSCO, shipbuilders and repairs.
You can work anywhere in the globe with a career in logistics. This field offers many opportunities for people who are organized and enjoy structure.
Many industries offer entry-level positions in logistics that don't need a degree. If you are planning to run a larger department or supply-chain, then you might consider a university degree.
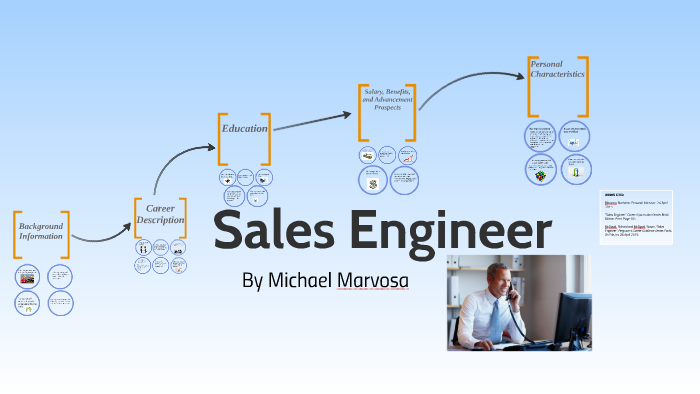
Logistics jobs in San Diego include analysing data about transportation and determining the most efficient routes to transport products. These jobs are a great opportunity to improve your resume while earning a decent salary.
Other careers in logistics include positions such as trucking or shipping. These involve delivering packages and freight to different destinations. You'll need to have a driver's license to qualify for these jobs, and you should be able to pass a background check.
Another option for those interested in a logistics job is to become a warehouse manager. This is an excellent position that offers a good salary and the chance to work with a large amount of equipment and stock.
A number of logistics firms in san Diego provide a range of services, including storage and transportation. These companies offer a way to ensure that supplies are delivered on time and in good condition from the factory to your warehouse.
Omni Logistics, WWEX, Worldwide Express, and other San Diego-based logistics companies are popular. These companies offer a variety of freight services from domestic shipping to international transportation.
San Diego companies choose them because of their excellent customer service. They'll make every effort to ensure that you receive your shipments on time and with no damage.
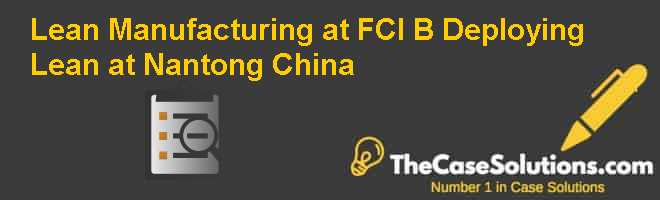
Zion Transport in San Diego is a freight company that offers superior service at affordable rates. The company offers trucking, shipping, and logistics solutions to businesses of all sizes.
They are an important part of every business and can be challenging to manage. It can be costly and time-consuming, so you need to find a shipping company who can save you money.
Our Salary Tools will help you determine what salary you can expect for different positions in San Diego. This information will allow you to determine whether or not this is a career that you want.
FAQ
What makes a production planner different from a project manger?
The major difference between a Production Planner and a Project Manager is that a Project Manager is often the person responsible for organizing and planning the entire project. While a Production Planner is involved mainly in the planning stage,
What jobs are available in logistics?
There are many jobs available in logistics. These are some of the jobs available in logistics:
-
Warehouse workers - They load and unload trucks and pallets.
-
Transport drivers - These are people who drive trucks and trailers to transport goods or perform pick-ups.
-
Freight handlers, - They sort out and pack freight in warehouses.
-
Inventory managers – These people oversee inventory at warehouses.
-
Sales representatives - They sell products.
-
Logistics coordinators – They plan and coordinate logistics operations.
-
Purchasing agents - They purchase goods and services needed for company operations.
-
Customer service representatives - They answer calls and emails from customers.
-
Ship clerks - They issue bills and process shipping orders.
-
Order fillers - They fill orders based on what is ordered and shipped.
-
Quality control inspectors (QCI) - They inspect all incoming and departing products for potential defects.
-
Other - Logistics has many other job opportunities, including transportation supervisors, logistics specialists, and cargo specialists.
What are the goods of logistics?
Logistics refers to the movement of goods from one place to another.
They include all aspects of transport, including packaging, loading, transporting, unloading, storing, warehousing, inventory management, customer service, distribution, returns, and recycling.
Logisticians ensure the product reaches its destination in the most efficient manner. Logisticians help companies improve their supply chain efficiency by providing information about demand forecasts and stock levels, production schedules, as well as availability of raw materials.
They coordinate with vendors and suppliers, keep track of shipments, monitor quality standards and perform inventory and order replenishment.
Are there ways to automate parts of manufacturing?
Yes! Yes! Automation has existed since ancient times. The Egyptians discovered the wheel thousands and years ago. To help us build assembly lines, we now have robots.
There are many applications for robotics in manufacturing today. These include:
-
Assembly line robots
-
Robot welding
-
Robot painting
-
Robotics inspection
-
Robots that create products
Manufacturing can also be automated in many other ways. For example, 3D printing allows us to make custom products without having to wait for weeks or months to get them manufactured.
What are the 7 Rs of logistics?
The acronym 7R's of Logistic is an acronym that stands for seven fundamental principles of logistics management. It was published in 2004 by the International Association of Business Logisticians as part of their "Seven Principles of Logistics Management" series.
The following letters make up the acronym:
-
Responsible – ensure that all actions are legal and don't cause harm to anyone else.
-
Reliable - Have confidence in your ability to fulfill all of your commitments.
-
Be responsible - Use resources efficiently and avoid wasting them.
-
Realistic - consider all aspects of operations, including cost-effectiveness and environmental impact.
-
Respectful - Treat people fairly and equitably
-
Resourceful - look for opportunities to save money and increase productivity.
-
Recognizable is a company that provides customers with value-added solutions.
Is there anything we should know about Manufacturing Processes prior to learning about Logistics.
No. It doesn't matter if you don't know anything about manufacturing before you learn about logistics. But, being familiar with manufacturing processes will give you a better understanding about how logistics works.
What are the essential elements of running a logistics firm?
A successful logistics business requires a lot more than just knowledge. You must have good communication skills to interact effectively with your clients and suppliers. It is important to be able to analyse data and draw conclusions. You must be able to work well under pressure and handle stressful situations. In order to innovate and create new ways to improve efficiency, creativity is essential. You must be a strong leader to motivate others and direct them to achieve organizational goals.
You must be organized to meet tight deadlines.
Statistics
- Job #1 is delivering the ordered product according to specifications: color, size, brand, and quantity. (netsuite.com)
- (2:04) MTO is a production technique wherein products are customized according to customer specifications, and production only starts after an order is received. (oracle.com)
- In the United States, for example, manufacturing makes up 15% of the economic output. (twi-global.com)
- In 2021, an estimated 12.1 million Americans work in the manufacturing sector.6 (investopedia.com)
- [54][55] These are the top 50 countries by the total value of manufacturing output in US dollars for its noted year according to World Bank.[56] (en.wikipedia.org)
External Links
How To
How to use the Just-In Time Method in Production
Just-in-time (JIT) is a method that is used to reduce costs and maximize efficiency in business processes. It is a process where you get the right amount of resources at the right moment when they are needed. This means you only pay what you use. Frederick Taylor developed the concept while working as foreman in early 1900s. After observing how workers were paid overtime for late work, he realized that overtime was a common practice. He concluded that if workers were given enough time before they start work, productivity would increase.
JIT teaches you to plan ahead and prepare everything so you don’t waste time. It is important to look at your entire project from beginning to end and ensure that you have enough resources to handle any issues that may arise. You will have the resources and people to solve any problems you anticipate. This will ensure that you don't spend more money on things that aren't necessary.
There are many JIT methods.
-
Demand-driven JIT: This is a JIT that allows you to regularly order the parts/materials necessary for your project. This will allow to track how much material has been used up. This will allow to you estimate the time it will take for more to be produced.
-
Inventory-based: This allows you to store the materials necessary for your projects in advance. This allows you to predict how much you can expect to sell.
-
Project-driven: This is an approach where you set aside enough funds to cover the cost of your project. When you know how much you need, you'll purchase the appropriate amount of materials.
-
Resource-based: This is the most common form of JIT. This is where you assign resources based upon demand. For instance, if you have a lot of orders coming in, you'll assign more people to handle them. If you don’t have many orders you will assign less people to the work.
-
Cost-based: This is the same as resource-based except that you don't care how many people there are but how much each one of them costs.
-
Price-based: This is very similar to cost-based, except that instead of looking at how much each individual worker costs, you look at the overall price of the company.
-
Material-based - This is a variant of cost-based. But instead of looking at the total company cost, you focus on how much raw material you spend per year.
-
Time-based: This is another variation of resource-based JIT. Instead of focusing only on how much each employee is costing, you should focus on how long it takes to complete your project.
-
Quality-based: This is yet another variation of resource-based JIT. Instead of thinking about the cost of each employee or the time it takes to produce something, you focus on how good your product quality.
-
Value-based JIT is the newest form of JIT. In this instance, you are not concerned about the product's performance or meeting customer expectations. Instead, you're focused on how much value you add to the market.
-
Stock-based is an inventory-based system that measures the number of items produced at any given moment. It's used when you want to maximize production while minimizing inventory.
-
Just-intime planning (JIT), is a combination JIT/sales chain management. It refers to the process of scheduling the delivery of components as soon as they are ordered. This is important as it reduces lead time and increases throughput.