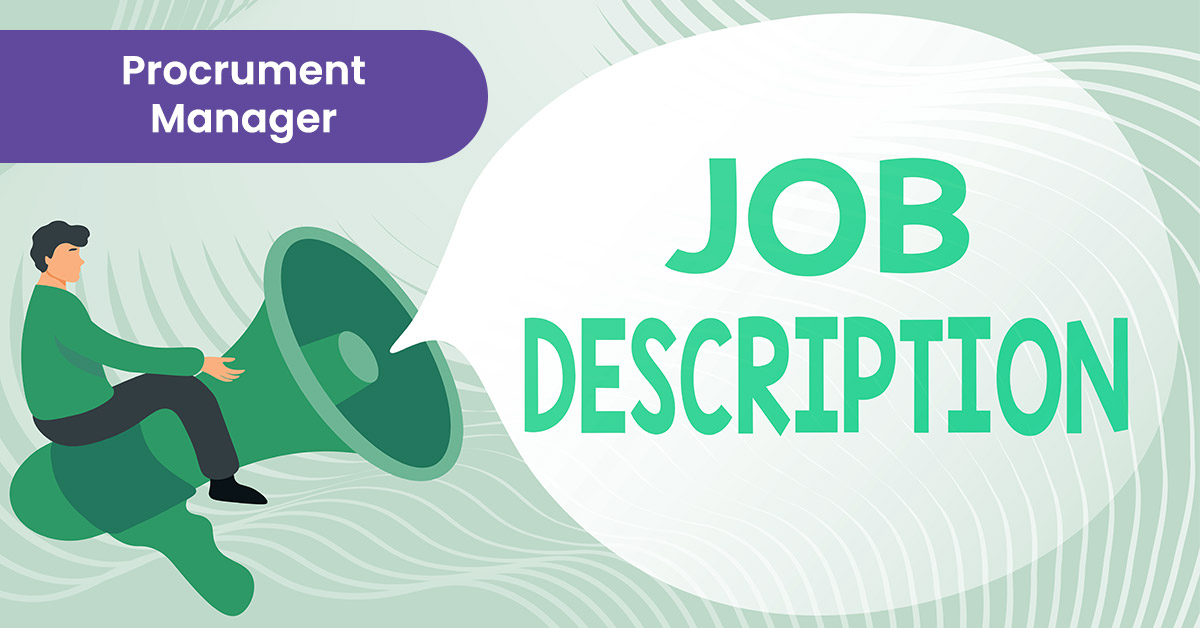
The supply chain is a complex web of people, organizations and technology that moves materials from a supplier to a consumer. The supply chain is composed of three parties: the supplier who provides the raw materials; the manufacturer who makes the parts and offers the services necessary to create a final product; and the distributor who distributes the product to the consumer.
Companies struggle to build more resilient supply chains during the global economic slowdown, with a weakened environment of demand and increased competition. Stock accumulation makes it more difficult for businesses to forecast, plan, and execute their logistics.
Since the supply chain is ever changing, it is important to read up on the most recent news regarding supply chain and logistics. You can stay up to date on current trends by reading the top news sources in supply chain management and logistics.
A great place to start is Supply Chain Digest, which reviews hundreds of news articles, research reports and analyst opinions every week and summarizes the key points in a streamlined format for busy supply chain and logistics professionals. Alternatively, you can sign up for their weekly newsletter and get supply chain management and logistics news delivered to your inbox.
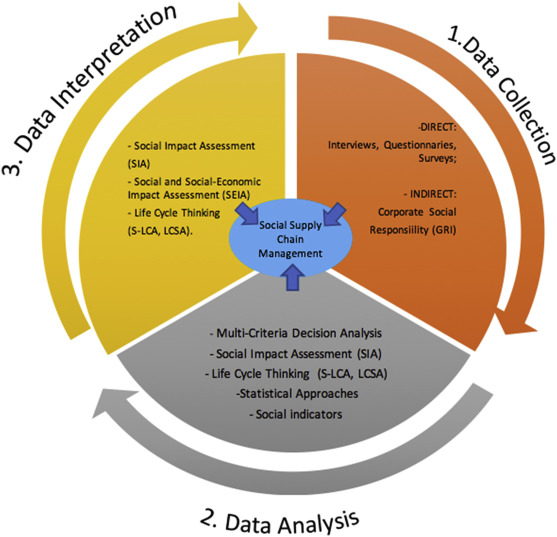
Supply Chain Digital offers a wealth of information on the supply chain, logistics, and related topics. This includes digital procurement innovation and risk management. This site features a digital magazine as well as news articles, blogs, podcasts and virtual events.
One Network – A revolutionary network-based approach to solving supply chains problems.
The One Network is a leading network of innovative organizations that helps companies reduce their inventory and streamline their reverse logistics processes, so they can better manage obsolete goods. The One Network has been featured by some of the most influential supply-chain publications in the world, and its technology can be found at a number major companies.
One Network offers you the opportunity to invest your money in the future growth of your organization.
To remain competitive in a world that is constantly changing, it is important to implement and adapt new technologies and methods. A network of technology suppliers can help companies increase their productivity, efficiency, and reduce their environmental impact.
Vyas believes that decoupling the supply chain, which involves encouraging companies to produce in multiple countries at once, will strengthen the system and help it be more resilient. This is done by moving production from the main hubs of manufacturing to smaller, diverse locations.
Decoupling is a strategy that has gained popularity in recent years as a result of changes in consumer behavior and growing awareness about global environmental concerns. This strategy also requires large investments in the infrastructure required to support it.
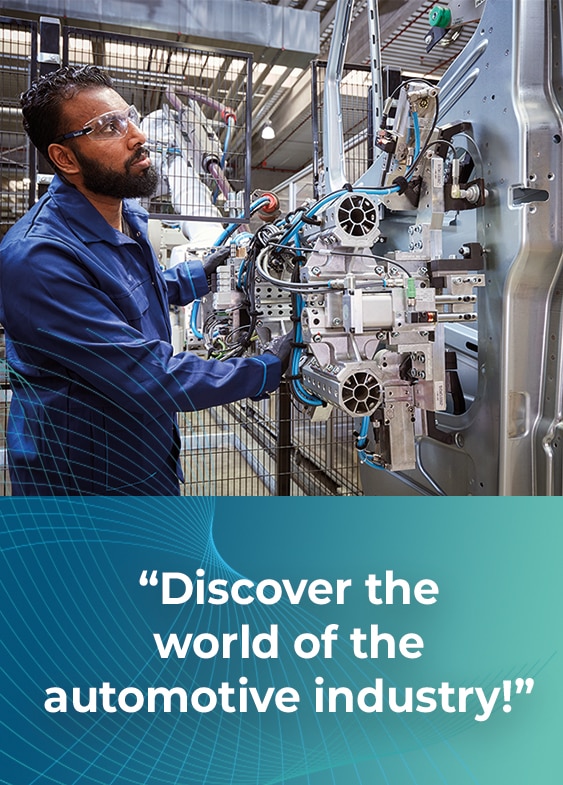
A more robust, resilient supply chain is good for both businesses and consumers. This also reduces costs and protects the environment for all parties.
Steps to strengthen the supply chains can help prepare businesses for the next major disruption. For example, the Covid-19 pandemic in 2021 that affected the supply of medical supplies, pharmaceuticals and other commodities. It can also help ensure that, in the event of a disaster, businesses and consumers can recover quickly.
FAQ
What are the main products of logistics?
Logistics refers to the movement of goods from one place to another.
They include all aspects associated with transport including packaging, loading transporting, unloading storage, warehousing inventory management customer service, distribution returns and recycling.
Logisticians ensure the product reaches its destination in the most efficient manner. They provide information on demand forecasts as well stock levels, production schedules and availability of raw material.
They can also track shipments in transit and monitor quality standards.
How can manufacturing efficiency improved?
The first step is to identify the most important factors affecting production time. We must then find ways that we can improve these factors. If you don’t know how to start, look at which factors have the greatest impact upon production time. Once you have identified them, it is time to identify solutions.
How can I learn about manufacturing?
Experience is the best way for you to learn about manufacturing. However, if that's not possible, you can always read books or watch educational videos.
What is the difference between manufacturing and logistics
Manufacturing refers to the process of making goods using raw materials and machines. Logistics encompasses the management of all aspects associated with supply chain activities such as procurement, production planning, distribution and inventory control. It also includes customer service. Sometimes manufacturing and logistics are combined to refer to a wider term that includes both the process of creating products as well as their delivery to customers.
Statistics
- Job #1 is delivering the ordered product according to specifications: color, size, brand, and quantity. (netsuite.com)
- You can multiply the result by 100 to get the total percent of monthly overhead. (investopedia.com)
- According to the United Nations Industrial Development Organization (UNIDO), China is the top manufacturer worldwide by 2019 output, producing 28.7% of the total global manufacturing output, followed by the United States, Japan, Germany, and India.[52][53] (en.wikipedia.org)
- Many factories witnessed a 30% increase in output due to the shift to electric motors. (en.wikipedia.org)
- According to a Statista study, U.S. businesses spent $1.63 trillion on logistics in 2019, moving goods from origin to end user through various supply chain network segments. (netsuite.com)
External Links
How To
How to Use the Just-In-Time Method in Production
Just-intime (JIT), a method used to lower costs and improve efficiency in business processes, is called just-in-time. It is a process where you get the right amount of resources at the right moment when they are needed. This means that only what you use is charged to your account. Frederick Taylor first coined this term while working in the early 1900s as a foreman. After observing how workers were paid overtime for late work, he realized that overtime was a common practice. He then concluded that if he could ensure that workers had enough time to do their job before starting to work, this would improve productivity.
JIT is an acronym that means you need to plan ahead so you don’t waste your money. Also, you should look at the whole project from start-to-finish and make sure you have the resources necessary to address any issues. You can anticipate problems and have enough equipment and people available to fix them. You won't have to pay more for unnecessary items.
There are many JIT methods.
-
Demand-driven JIT: This is a JIT that allows you to regularly order the parts/materials necessary for your project. This will enable you to keep track of how much material is left after you use it. It will also allow you to predict how long it takes to produce more.
-
Inventory-based: This is a type where you stock the materials required for your projects in advance. This allows you to forecast how much you will sell.
-
Project-driven: This approach involves setting aside sufficient funds to cover your project's costs. You will be able to purchase the right amount of materials if you know what you need.
-
Resource-based JIT: This is the most popular form of JIT. Here you can allocate certain resources based purely on demand. You might assign more people to help with orders if there are many. If you don't receive many orders, then you'll assign fewer employees to handle the load.
-
Cost-based: This is the same as resource-based except that you don't care how many people there are but how much each one of them costs.
-
Price-based: This is a variant of cost-based. However, instead of focusing on the individual workers' costs, this looks at the total price of the company.
-
Material-based: This approach is similar to cost-based. However, instead of looking at the total cost for the company, you look at how much you spend on average on raw materials.
-
Time-based JIT is another form of resource-based JIT. Instead of focusing on the cost of each employee, you will focus on the time it takes to complete a project.
-
Quality-based JIT is another variant of resource-based JIT. Instead of looking at the labor costs and time it takes to make a product, think about its quality.
-
Value-based JIT: This is the latest form of JIT. In this instance, you are not concerned about the product's performance or meeting customer expectations. Instead, you're focused on how much value you add to the market.
-
Stock-based: This is an inventory-based method that focuses on the actual number of items being produced at any given time. This is used to increase production and minimize inventory.
-
Just-in-time (JIT) planning: This is a combination of JIT and supply chain management. This refers to the scheduling of the delivery of components as soon after they are ordered. It's important because it reduces lead times and increases throughput.