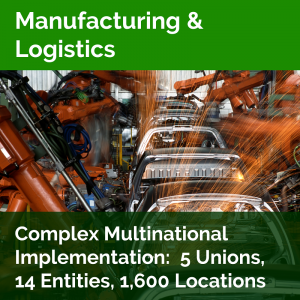
Facilities engineers, also referred to as maintenance engineers, are professionals who provide a variety of engineering and construction support for operations and buildings. They are responsible for developing and implementing procedures and recommending repairs and upgrades. They also coordinate routine and emergency maintenance. They can be involved in a variety of engineering disciplines including plumbing, electrical, and mechanical. Aside from their technical expertise, they have a good understanding of construction law, safety standards and other regulatory requirements.
Facilities engineers can start at the entry-level and quickly move up to more senior roles. The best way to stand out in the field is to build a strong portfolio, which may include engineering projects, research, and articles. Facilities engineers must continue to study their specialty. This will enable them to stand out in a job application.
Even though certification is not necessary for all facilities engineers it can make a difference when you apply for a new job. Professional engineers should have a solid understanding of engineering concepts and principles, and the ability to interpret data and create compelling presentations. Facility engineers must have knowledge in areas such as predictive maintenance, asset reliability and maintenance strategies, as well the design of facilities.
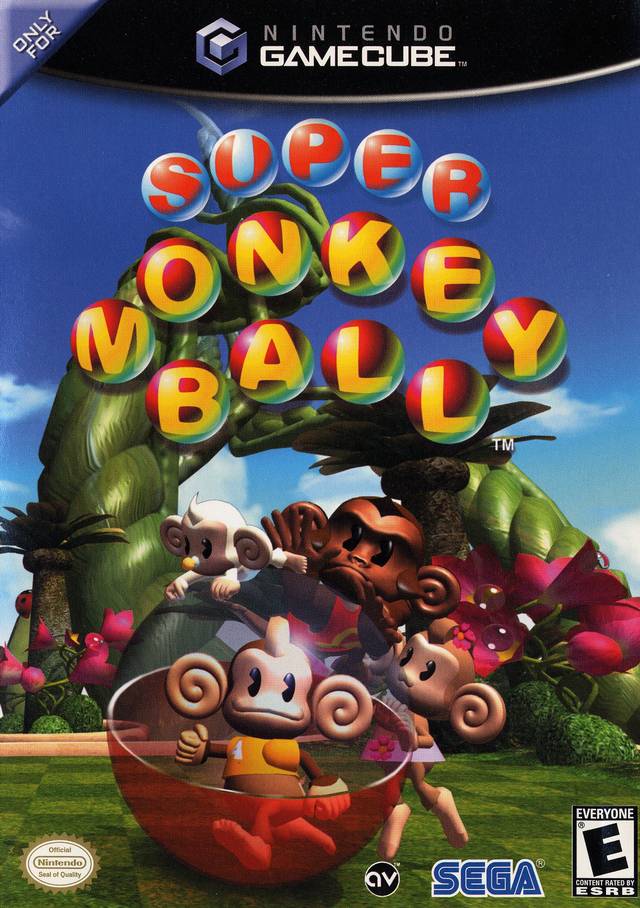
Facilities engineers typically work in the office, construction, or manufacturing setting. They manage and implement processes that ensure safe, efficient, effective, and reliable operation of utility systems. Facilities engineers are often able to work with managers and engineers, creating efficient work hours and addressing any issues that may arise.
The responsibilities of a facilities engineer will differ depending on the type and size of the facility they are assigned to. The job requires excellent time management, problem-solving skills, and the ability of working well with others. In a typical workday, a facilities engineer could perform hundreds upon tasks. An engineer who is responsible for the maintenance and repair of electrical, mechanical and plumbing equipment must be capable of troubleshooting and fixing malfunctions.
Many websites offer information and news about the field, including the Association of Facility Engineers' (AFE) website. You can find a sample resume, salary information, and job-related articles on these websites.
Other than these websites, facilities engineers can also read books and articles, participate in training courses, and connect with other engineers. In order to be a successful facilities engineer, you should have good organizational skills, a good understanding of various engineering and construction disciplines, and a solid understanding of building and safety codes.
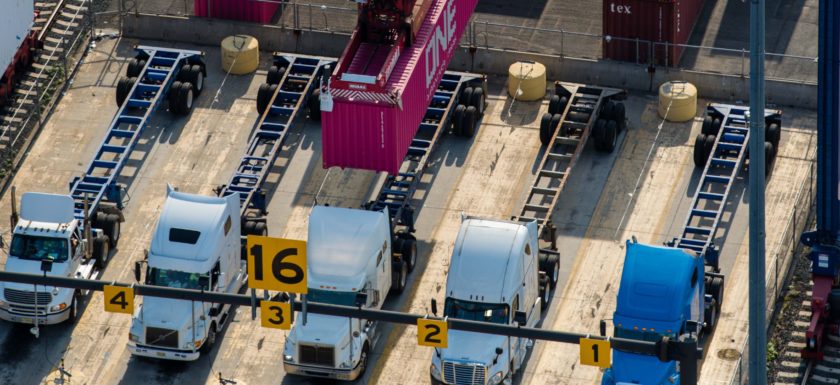
It is important to know that many of the most talented facilities engineers can perform multiple tasks at once and analyze data. To accomplish this, they need a working knowledge of design software, such as AutoCAD, as well as construction techniques, such as the CAM method. Other skills that are beneficial include project management, critical thinking, and problem-solving.
A facilities engineer job offers many benefits. You can work with a wide range of people. Many engineers in this field are skilled at working with different materials and can coordinate the work of others.
FAQ
What is the job of a manufacturer manager?
A manufacturing manager has to ensure that all manufacturing processes work efficiently and effectively. They should also be aware of any problems within the company and act accordingly.
They should also learn how to communicate effectively with other departments, including sales and marketing.
They must also keep up-to-date with the latest trends in their field and be able use this information to improve productivity and efficiency.
What are the differences between these four types?
Manufacturing refers to the transformation of raw materials into useful products by using machines and processes. Manufacturing involves many activities, including designing, building, testing and packaging, shipping, selling, service, and so on.
How can I find out more about manufacturing?
Experience is the best way for you to learn about manufacturing. But if that is not possible you can always read books and watch educational videos.
What are manufacturing and logistic?
Manufacturing refers to the process of making goods using raw materials and machines. Logistics includes all aspects related to supply chain management, such as procurement, distribution planning, inventory control and transportation. Sometimes manufacturing and logistics are combined to refer to a wider term that includes both the process of creating products as well as their delivery to customers.
What skills do production planners need?
Production planners must be flexible, organized, and able handle multiple tasks. Communication skills are essential to ensure that you can communicate effectively with clients, colleagues, and customers.
Statistics
- Job #1 is delivering the ordered product according to specifications: color, size, brand, and quantity. (netsuite.com)
- (2:04) MTO is a production technique wherein products are customized according to customer specifications, and production only starts after an order is received. (oracle.com)
- Many factories witnessed a 30% increase in output due to the shift to electric motors. (en.wikipedia.org)
- According to a Statista study, U.S. businesses spent $1.63 trillion on logistics in 2019, moving goods from origin to end user through various supply chain network segments. (netsuite.com)
- In the United States, for example, manufacturing makes up 15% of the economic output. (twi-global.com)
External Links
How To
Six Sigma and Manufacturing
Six Sigma refers to "the application and control of statistical processes (SPC) techniques in order to achieve continuous improvement." Motorola's Quality Improvement Department created Six Sigma at their Tokyo plant, Japan in 1986. Six Sigma's core idea is to improve the quality of processes by standardizing and eliminating defects. In recent years, many companies have adopted this method because they believe there is no such thing as perfect products or services. Six Sigma seeks to reduce variation between the mean production value. This means that if you take a sample of your product, then measure its performance against the average, you can find out what percentage of the time the process deviates from the norm. If this deviation is too big, you know something needs fixing.
Understanding the nature of variability in your business is the first step to Six Sigma. Once you understand that, it is time to identify the sources of variation. You'll also want to determine whether these variations are random or systematic. Random variations occur when people do mistakes. Symmetrical variations are caused due to factors beyond the process. For example, if you're making widgets, and some of them fall off the assembly line, those would be considered random variations. If however, you notice that each time you assemble a widget it falls apart in exactly the same spot, that is a problem.
Once you've identified the problem areas you need to find solutions. You might need to change the way you work or completely redesign the process. To verify that the changes have worked, you need to test them again. If they don't work you need to rework them and come up a better plan.