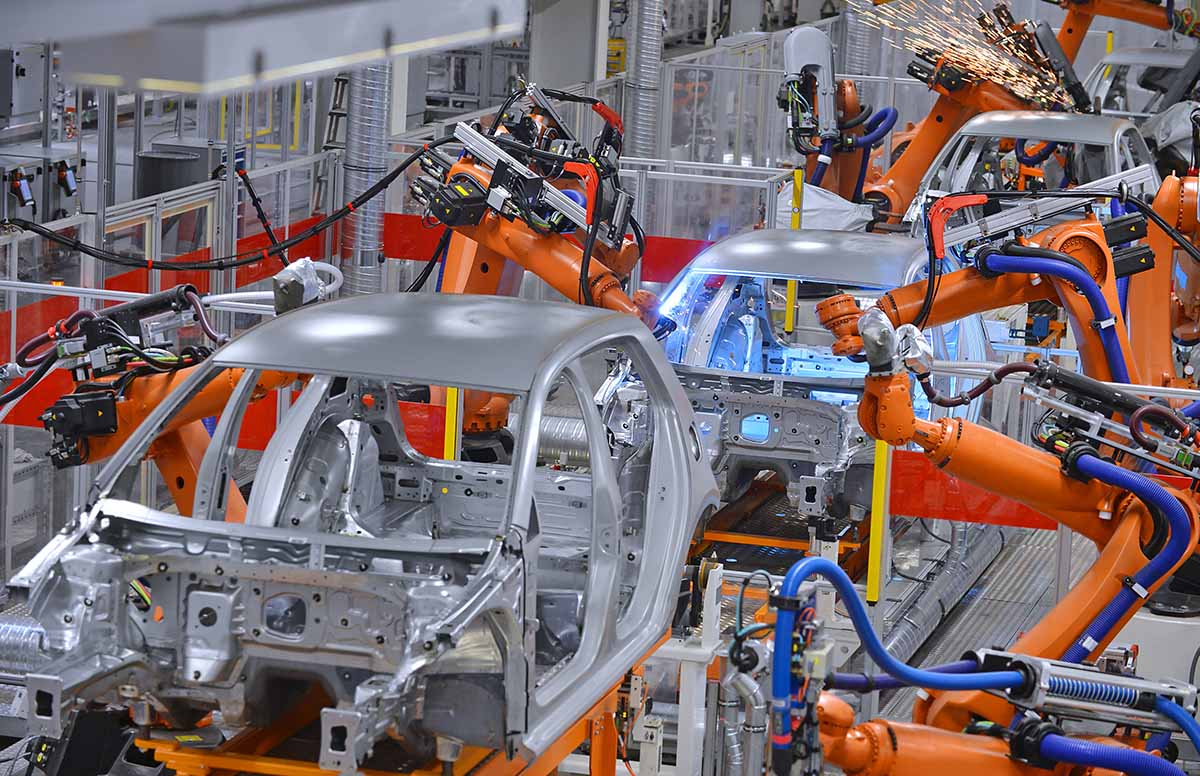
San Diego is home to many of the country's top logistics jobs, so if you're a newcomer to the area or are looking to change careers, this city may be the place for you. The positions available range from entry level to director positions that pay over $100,000 per year.
Logistics jobs are an important part of any company's supply chain. They help move goods from manufacturers to clients. These jobs also include those that deal with warehousing, storage, inventory management and distribution.
Some of the most prominent companies in America have their own logistic departments. General Dynamics is one of them, as are BAE Systems or NASSCO, shipbuilders and repairs.
Your career as a logistics professional could take you to any part of the globe. Many job opportunities exist in the logistics field. It is a great option for those with a passion for organization and structure.
Many industries offer entry-level positions in logistics that don't need a degree. You may need a higher degree if you want to supervise a large department or supply chain.
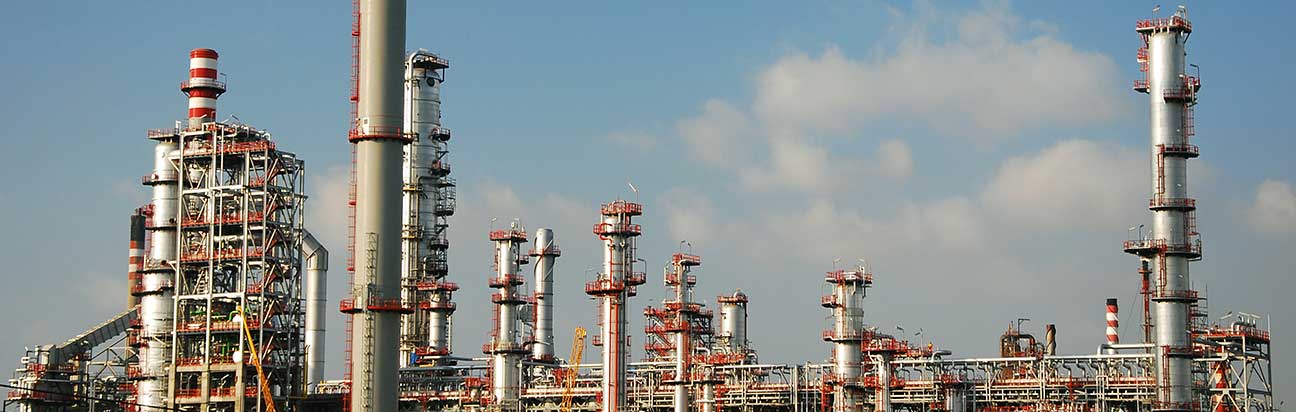
Various logistics jobs in san diego involve analyzing transportation information and using that data to determine the most efficient routes for products. These jobs can be a great way to build your resume and earn a good salary while you advance in your career.
Other careers in logistics include positions such as trucking or shipping. These involve delivering packages and freight to different destinations. You'll need to have a driver's license to qualify for these jobs, and you should be able to pass a background check.
For those who are interested in a career in logistics, becoming a warehouse manager may be an option. This is an excellent position that offers a good salary and the chance to work with a large amount of equipment and stock.
In San Diego there are many logistics companies that provide various services. These include warehousing, transportation, and more. These companies are a great option to ensure that your supplies arrive at your warehouse in good condition and on time.
Some of the most popular San Diego logistics companies include Omni Logistics, WWEX, and Worldwide Express. These companies provide a range of freight services ranging from domestic transport to international shipping.
They're known for their customer service, which is why they're a top choice among companies in San Diego. They'll go beyond the call of duty to make sure that your shipments reach you on time, and in perfect shape.
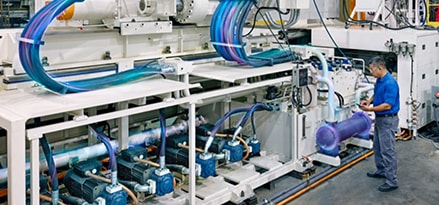
Zion Transport, a freight shipping firm in San Diego, offers a superior service and competitive rates. The company offers trucking and shipping solutions for a variety of businesses, from small startups to large corporations.
These services are a crucial part of any business, and they can often be difficult to manage. The services can be both time-consuming as well as costly. That's why it's important to work with a shipping firm that is reliable and can help you cut costs.
Our Salary Tools will help you determine what salary you can expect for different positions in San Diego. These details can help you decide whether this is the career for you.
FAQ
How can manufacturing avoid production bottlenecks
You can avoid bottlenecks in production by making sure that everything runs smoothly throughout the production cycle, from the moment you receive an order to the moment the product is shipped.
This includes planning for capacity requirements as well as quality control measures.
This can be done by using continuous improvement techniques, such as Six Sigma.
Six Sigma is a management system used to improve quality and reduce waste in every aspect of your organization.
It is focused on creating consistency and eliminating variation in your work.
Is automation important for manufacturing?
Automation is essential for both manufacturers and service providers. Automation allows them to deliver services quicker and more efficiently. It reduces human errors and improves productivity, which in turn helps them lower their costs.
What is the responsibility for a logistics manager
Logistics managers make sure all goods are delivered on schedule and without damage. This is achieved by using their knowledge and experience with the products of the company. He/she should make sure that enough stock is on hand to meet the demands.
What are the main products of logistics?
Logistics refers to all activities that involve moving goods from A to B.
They include all aspects associated with transport including packaging, loading transporting, unloading storage, warehousing inventory management customer service, distribution returns and recycling.
Logisticians ensure that the product is delivered to the correct place, at the right time, and under safe conditions. Logisticians help companies improve their supply chain efficiency by providing information about demand forecasts and stock levels, production schedules, as well as availability of raw materials.
They can also track shipments in transit and monitor quality standards.
How can manufacturing efficiency improved?
First, we need to identify which factors are most critical in affecting production times. We must then find ways that we can improve these factors. You can start by identifying the most important factors that impact production time. Once you've identified them all, find solutions to each one.
Statistics
- According to a Statista study, U.S. businesses spent $1.63 trillion on logistics in 2019, moving goods from origin to end user through various supply chain network segments. (netsuite.com)
- According to the United Nations Industrial Development Organization (UNIDO), China is the top manufacturer worldwide by 2019 output, producing 28.7% of the total global manufacturing output, followed by the United States, Japan, Germany, and India.[52][53] (en.wikipedia.org)
- Many factories witnessed a 30% increase in output due to the shift to electric motors. (en.wikipedia.org)
- Job #1 is delivering the ordered product according to specifications: color, size, brand, and quantity. (netsuite.com)
- (2:04) MTO is a production technique wherein products are customized according to customer specifications, and production only starts after an order is received. (oracle.com)
External Links
How To
How to Use 5S for Increasing Productivity in Manufacturing
5S stands for "Sort", 'Set In Order", 'Standardize', & Separate>. Toyota Motor Corporation created the 5S methodology in 1954. It allows companies to improve their work environment, thereby achieving greater efficiency.
The basic idea behind this method is to standardize production processes, so they become repeatable, measurable, and predictable. This means that every day tasks such cleaning, sorting/storing, packing, and labeling can be performed. This knowledge allows workers to be more efficient in their work because they are aware of what to expect.
There are five steps to implementing 5S, including Sort, Set In Order, Standardize, Separate and Store. Each step has a different action and leads to higher efficiency. You can make it easy for people to find things later by sorting them. Once you have placed items in an ordered fashion, you will put them together. Next, organize your inventory into categories and store them in containers that are easily accessible. Make sure everything is correctly labeled when you label your containers.
Employees will need to be more critical about their work. Employees must understand why they do certain tasks and decide if there's another way to accomplish them without relying on the old ways of doing things. They will need to develop new skills and techniques in order for the 5S system to be implemented.
In addition to improving efficiency, the 5S system also increases morale and teamwork among employees. Once they start to notice improvements, they are motivated to keep working towards their goal of increasing efficiency.