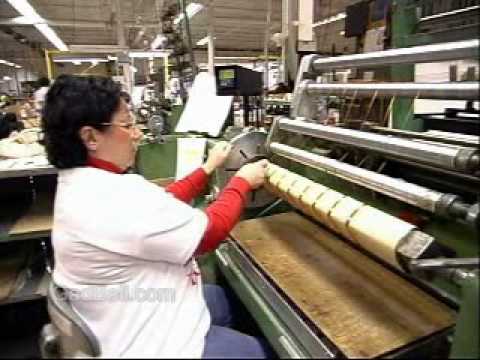
There are several reasons to become an engineer, including the satisfaction of a job that solves real-world problems and the prospect of helping people. Engineers are in a rapidly growing field, with high-paying positions and a good career path.
The average engineering technologist's salary is 52,171 dollars per year. This is 1% above the national average, which is $51,860. It equals $2174 for every hour worked. This pay is based off an estimated federal income tax rate of 22 percent.
The mechanical engineering technician works with engineers that design, test, and create machinery, appliances, or equipment. They often assist with manufacturing processes in factories or during development phases in research and development labs before production takes place. They can analyze product designs or prepare layouts of parts that need to be manufactured. They also may inspect test equipment for quality and calibrate new devices before they are put into use.
Other engineering technologist work with CAD programs to convert designs from engineers and architects in technical drawings. They are also responsible for entering job descriptions into the CAD system and making adjustments to existing drawing.

The education required for an engineering technologist is typically an associate's degree, but a bachelor's or master's degree in electrical or electronics engineering can increase your chances of finding a position. The majority of employers prefer to employ individuals with these degrees as they possess more experience and training within the field.
Salary ranges for manufacturing engineering technologists are from $32,295 up to $94,100 with a median of $61,260. The majority of these workers are aged between 26 and 30 years. About a third fall in the age bracket of 31 to 36.
These employees are employed by manufacturing companies, where they work with engineers to resolve issues that can affect the manufacturing processes and the layouts of facilities. You will find them in companies that produce consumer goods, food items, industrial equipment, etc.
The majority of them are employed full-time, and they're expected to put in more than forty hours per week. They have a variety of duties, depending on the company for which they work.
Under the supervision of a chemist engineer, chemical engineering technologists carry out experiments and develop chemical processes. They also perform inventories. Also, they may be required to estimate manufacturing costs.
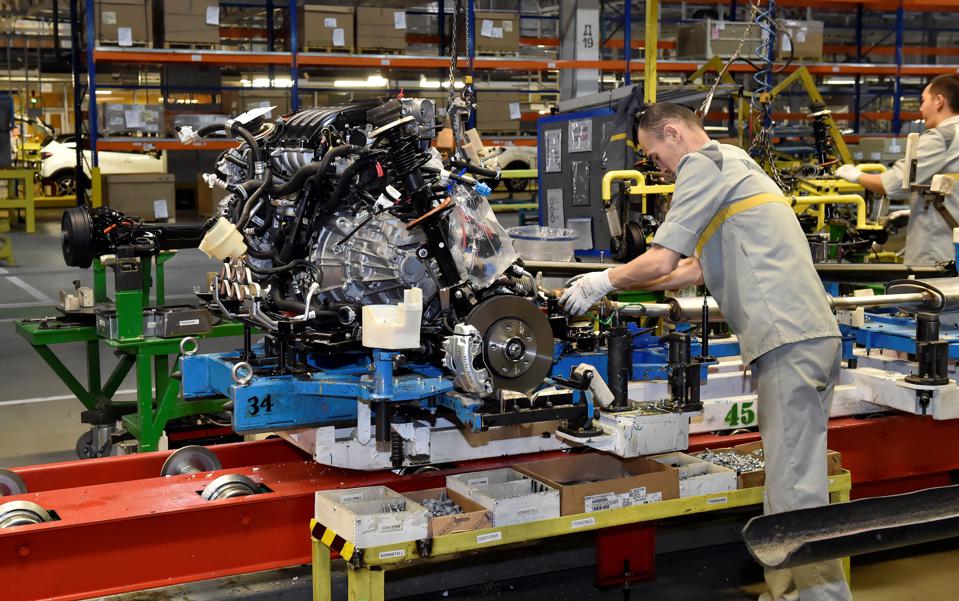
The group has a younger workforce, and the employment rate is lower than that of the total labor force. However, jobs are expected to increase slightly until 2031. In May 2021, the BLS reported a median wage of $60 220 for this occupation.
The Electronics Engineering Technology jobs will give you the opportunity to work with electronic components. These positions are very popular with recent graduates. You can find them in manufacturing, research laboratories or engineering services.
The average salary for engineering technologists is competitive, so it's worth considering before accepting a position. It is possible to increase your income in many ways. This includes changing employers that pay more money, gaining higher education, and managing experience.
FAQ
What is the role of a production manager?
Production planners ensure all aspects of the project are delivered within time and budget. A production planner ensures that the service and product meet the client's expectations.
Is there anything we should know about Manufacturing Processes prior to learning about Logistics.
No. No. Understanding the manufacturing process will allow you to better understand logistics.
What are my options for learning more about manufacturing
Experience is the best way for you to learn about manufacturing. You can read books, or watch instructional videos if you don't have the opportunity to do so.
What skills do production planners need?
A production planner must be organized, flexible, and able multitask to succeed. It is also important to be able communicate with colleagues and clients.
Statistics
- According to a Statista study, U.S. businesses spent $1.63 trillion on logistics in 2019, moving goods from origin to end user through various supply chain network segments. (netsuite.com)
- According to the United Nations Industrial Development Organization (UNIDO), China is the top manufacturer worldwide by 2019 output, producing 28.7% of the total global manufacturing output, followed by the United States, Japan, Germany, and India.[52][53] (en.wikipedia.org)
- Job #1 is delivering the ordered product according to specifications: color, size, brand, and quantity. (netsuite.com)
- It's estimated that 10.8% of the U.S. GDP in 2020 was contributed to manufacturing. (investopedia.com)
- (2:04) MTO is a production technique wherein products are customized according to customer specifications, and production only starts after an order is received. (oracle.com)
External Links
How To
Six Sigma in Manufacturing
Six Sigma is defined as "the application of statistical process control (SPC) techniques to achieve continuous improvement." It was developed by Motorola's Quality Improvement Department at their plant in Tokyo, Japan, in 1986. Six Sigma's basic concept is to improve quality and eliminate defects through standardization. Since there are no perfect products, or services, this approach has been adopted by many companies over the years. The main goal of Six Sigma is to reduce variation from the mean value of production. This means that you can take a sample from your product and then compare its performance to the average to find out how often the process differs from the norm. If there is a significant deviation from the norm, you will know that something needs to change.
Understanding the nature of variability in your business is the first step to Six Sigma. Once you've understood that, you'll want to identify sources of variation. These variations can also be classified as random or systematic. Random variations happen when people make errors; systematic variations are caused externally. Random variations would include, for example, the failure of some widgets to fall from the assembly line. It would be considered a systematic problem if every widget that you build falls apart at the same location each time.
Once you have identified the problem, you can design solutions. That solution might involve changing the way you do things or redesigning the process altogether. You should then test the changes again after they have been implemented. If they fail, you can go back to the drawing board to come up with a different plan.