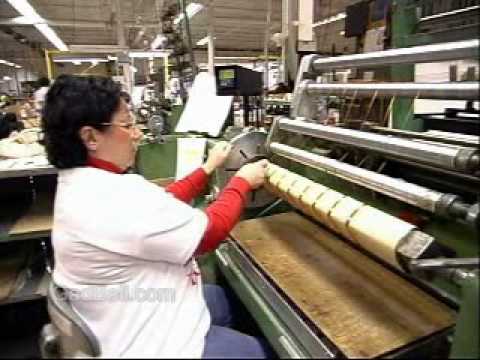
There are many kinds of manufacturers. How do you choose the right one for your business? Learn more about Continuous manufacturing, Process manufacturing and Job shop manufacturing. Each type has its pros and cons. This article will describe the differences among these four types. Based on your industry, location and product type, you will be able to choose the right model for your business. After you have decided which model is right for you, you will need to think about your sales, production, quality control, and customer service.
Discrete manufacturing
Discrete Manufacturing is the process of producing distinct products. Some examples of such products include aeroplanes, automobiles, and toys. Discrete Manufacturing allows companies to focus more on their individual products than on mass production. Distinct manufacturing, for example, allows the creation of unique parts for aeroplanes by integrating several manufacturing processes. Discrete manufacturing is a popular way to manufacture high-tech items.
Discrete manufacturing produces distinct items. Instead of making many identical products, discrete production produces unique items that can be easily identified with serial numbers, labels and other numerical attributes. For example, a smartphone may consist of different parts manufactured in multiple factories in different states, and the individual parts are assembled only once the finished product is ready to be sold. The bag of your smartphone is the same. It could contain parts from different plants, such as the Missouri plant headquarters.
Manufacturing process
The process manufacturing branch is one that deals with formulas or recipes. This term contrasts with discrete manufacture, which is concerned only with the production of individual units and bills of materials. The process manufacturing concept also includes the assembly of parts. Because of this, they have very different manufacturing goals. Each of these methods is important in the manufacturing process. Here are three methods to distinguish between discrete and process manufacturing. Let's examine each one.
Batch process manufacturing can be compared to continuous process production. It uses larger batches of raw materials, and works around the clock. Batch process manufacturing is used in many industries, including pharmaceuticals, paper production and bookbinding. However, this method isn't the best fit for every industry. This method can be too difficult and expensive to use by small businesses. Therefore, most companies use this method when they need to create large quantities of the same product.
Factory job shop
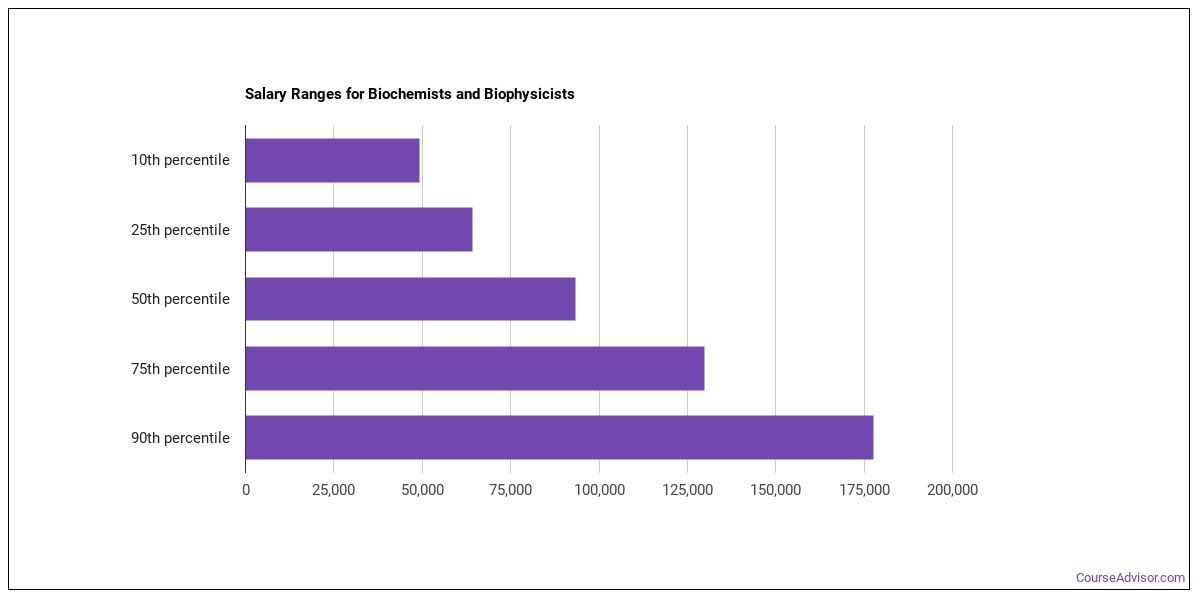
Job shop manufacturing can be described as a small-scale production system that specializes only in custom, batch and semi-custom manufacturing. Once each job is done, the job shop system can move onto the next. This method of production is also called lean manufacturing, as a single-shift operation is more efficient than many other methods. These are just a few of the many benefits of job-shop manufacturing. Read on to learn more about this method of manufacturing. You might consider this for your service or product needs.
First, job shop efficiency must be improved. The incorporation of new manufacturing principles is crucial to creating a lean manufacturing environment. These principles focus on quality control and justin-time production and are especially relevant for high-volume operations. Employing new manufacturing principles can help a job shop increase productivity and lower costs. Additionally, jobs should proceed through each process one at a time, so there should be no queues.
Continuous manufacturing
Continuous manufacturing has the advantage of flexible tracking, which is one of its greatest benefits. This is especially beneficial when it concerns product failure. Since the production line's time stamp and the raw material quantity can help identify when a batch has gone wrong, continuous manufacturing allows for more flexible tracking. The manufacturer also has a reduced risk of product shortages due to increased tracking. Continuous manufacturing is also becoming more popular in the pharmaceutical sector.
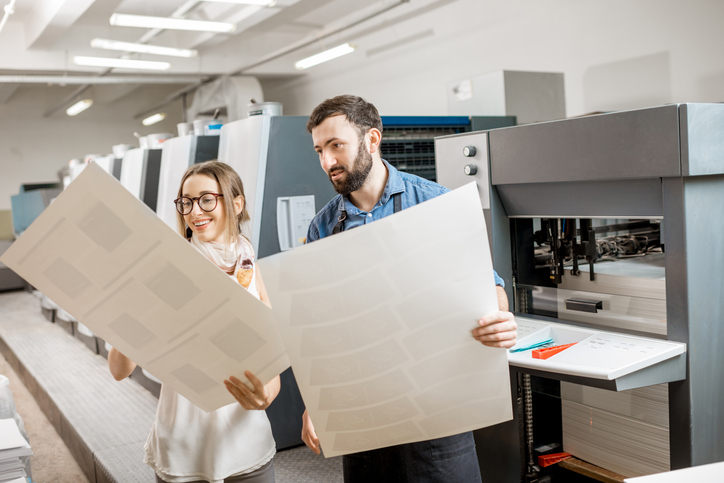
The benefits of continuous production are obvious, but implementation can be slow. Implementation can be difficult because the process is not fully integrated within the company. Continuous manufacturing has the potential of being a game changer in the pharmaceutical business, despite the limitations. Continuous manufacturing is only possible if the process integrates with end-to–end integration and continuous flow. Although the benefits of continuous production have been recognized by the pharmaceutical industry for many years, implementation has been slow.
FAQ
How can manufacturing efficiency improved?
First, determine which factors have the greatest impact on production time. Next, we must find ways to improve those factors. If you don’t know how to start, look at which factors have the greatest impact upon production time. Once you have identified them, it is time to identify solutions.
What can I do to learn more about manufacturing?
Experience is the best way for you to learn about manufacturing. If that is not possible, you could always read books or view educational videos.
Why automate your factory?
Modern warehousing is becoming more automated. The rise of e-commerce has led to increased demand for faster delivery times and more efficient processes.
Warehouses must be able to quickly adapt to changing demands. To do so, they must invest heavily in technology. Automation of warehouses offers many benefits. Here are some of the reasons automation is worth your investment:
-
Increases throughput/productivity
-
Reduces errors
-
Accuracy is improved
-
Safety Boosts
-
Eliminates bottlenecks
-
This allows companies to scale easily
-
This makes workers more productive
-
Provides visibility into everything that happens in the warehouse
-
Enhances customer experience
-
Improves employee satisfaction
-
It reduces downtime, and increases uptime
-
You can be sure that high-quality products will arrive on time
-
Eliminates human error
-
Helps ensure compliance with regulations
What are the responsibilities of a logistic manager?
A logistics manager makes sure that all goods are delivered on-time and in good condition. This is accomplished by using the experience and knowledge gained from working with company products. He/she must also ensure sufficient stock to meet the demand.
Is it possible to automate certain parts of manufacturing
Yes! Automation has been around since ancient times. The Egyptians invented the wheel thousands of years ago. To help us build assembly lines, we now have robots.
There are many uses of robotics today in manufacturing. These include:
-
Automation line robots
-
Robot welding
-
Robot painting
-
Robotics inspection
-
Robots that create products
Automation can be applied to manufacturing in many other ways. For instance, 3D printing allows us make custom products and not have to wait for months or even weeks to get them made.
What does it mean to be a manufacturer?
Manufacturing Industries refers to businesses that manufacture products. The people who buy these products are called consumers. These companies use various processes such as production, distribution, retailing, management, etc., to fulfill this purpose. They make goods from raw materials with machines and other equipment. This covers all types of manufactured goods including clothing, food, building supplies and furniture, as well as electronics, tools, machinery, vehicles and pharmaceuticals.
What is the difference in Production Planning and Scheduling, you ask?
Production Planning (PP) refers to the process of determining how much production is needed at any given moment. This is done through forecasting demand and identifying production capacities.
Scheduling refers the process by which tasks are assigned dates so that they can all be completed within the given timeframe.
Statistics
- You can multiply the result by 100 to get the total percent of monthly overhead. (investopedia.com)
- According to a Statista study, U.S. businesses spent $1.63 trillion on logistics in 2019, moving goods from origin to end user through various supply chain network segments. (netsuite.com)
- According to the United Nations Industrial Development Organization (UNIDO), China is the top manufacturer worldwide by 2019 output, producing 28.7% of the total global manufacturing output, followed by the United States, Japan, Germany, and India.[52][53] (en.wikipedia.org)
- It's estimated that 10.8% of the U.S. GDP in 2020 was contributed to manufacturing. (investopedia.com)
- Many factories witnessed a 30% increase in output due to the shift to electric motors. (en.wikipedia.org)
External Links
How To
How to Use Lean Manufacturing for the Production of Goods
Lean manufacturing refers to a method of managing that seeks to improve efficiency and decrease waste. It was first developed in Japan in the 1970s/80s by Taiichi Ahno, who was awarded the Toyota Production System (TPS), award from KanjiToyoda, the founder of TPS. Michael L. Watkins published the original book on lean manufacturing, "The Machine That Changed the World," in 1990.
Lean manufacturing is often described as a set if principles that help improve the quality and speed of products and services. It is about eliminating defects and waste from all stages of the value stream. Lean manufacturing is also known as just in time (JIT), zero defect total productive maintenance(TPM), and five-star (S). Lean manufacturing seeks to eliminate non-value added activities, such as inspection, work, waiting, and rework.
Lean manufacturing can help companies improve their product quality and reduce costs. Additionally, it helps them achieve their goals more quickly and reduces employee turnover. Lean manufacturing can be used to manage all aspects of the value chain. Customers, suppliers, distributors, retailers and employees are all included. Lean manufacturing is widely used in many industries. Toyota's philosophy is a great example of this. It has helped to create success in automobiles as well electronics, appliances and healthcare.
Five principles are the basis of lean manufacturing:
-
Define Value - Determine the value that your business brings to society. Also, identify what sets you apart from your competitors.
-
Reduce waste - Get rid of any activity that does not add value to the supply chain.
-
Create Flow: Ensure that the work process flows without interruptions.
-
Standardize & Simplify - Make processes as consistent and repeatable as possible.
-
Build Relationships- Develop personal relationships with both internal as well as external stakeholders.
Although lean manufacturing isn't a new concept in business, it has gained popularity due to renewed interest in the economy after the 2008 global financial crisis. Many businesses are now using lean manufacturing to improve their competitiveness. Some economists even believe that lean manufacturing can be a key factor in economic recovery.
Lean manufacturing, which has many benefits, is now a standard practice in the automotive industry. These include improved customer satisfaction, reduced inventory levels, lower operating costs, increased productivity, and better overall safety.
It can be applied to any aspect of an organisation. It is especially useful for the production aspect of an organization, as it ensures that every step in the value chain is efficient and effective.
There are three main types:
-
Just-in Time Manufacturing: This lean manufacturing method is commonly called "pull systems." JIT stands for a system where components are assembled on the spot rather than being made in advance. This approach aims to reduce lead times, increase the availability of parts, and reduce inventory.
-
Zero Defects Manufacturing (ZDM),: ZDM is a system that ensures no defective units are left the manufacturing facility. If a part is required to be repaired on the assembly line, it should not be scrapped. This also applies to finished products that need minor repairs before being shipped.
-
Continuous Improvement (CI),: Continuous improvement aims improve the efficiency and effectiveness of operations by continuously identifying issues and making changes to reduce waste. It involves continuous improvement of processes, people, and tools.