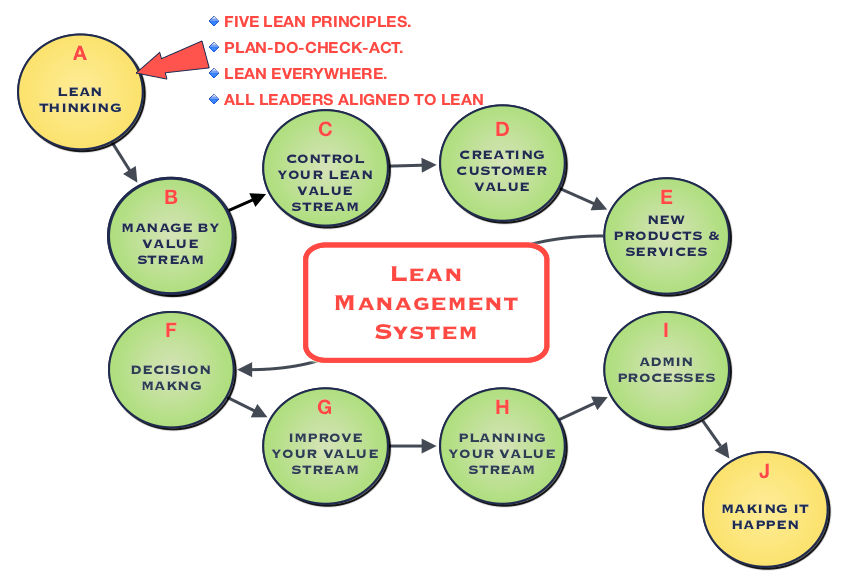
Historically, the demand of consumers has driven manufacturing. However, this is changing. Technology is also transforming the manufacturing industry. This is due in part to advances in predictive analytics, which enable manufacturers to move production closer to consumers. Despite these advances, manufacturing faces many risks, including shortages and high demand. Manufacturers may lose customers if they do not meet consumers' demand. If they produce too many, the market could become saturated. To preserve their brand image manufacturers must comply with quality control standards.
Manufacturers can use a variety of manufacturing methods, but they all have similar characteristics. Most common manufacturing processes include repetitive manufacturing, batch production, and process manufacture. These processes are very efficient and allow for mass production.
Repetitive Manufacturing is a process where the same or similar items are produced on a dedicated production line all year. Repetitive production production lines can be set up quickly and easily changed over, which makes them perfect for short runs of production that requires little capital investment. They can also run 24 hours a day.
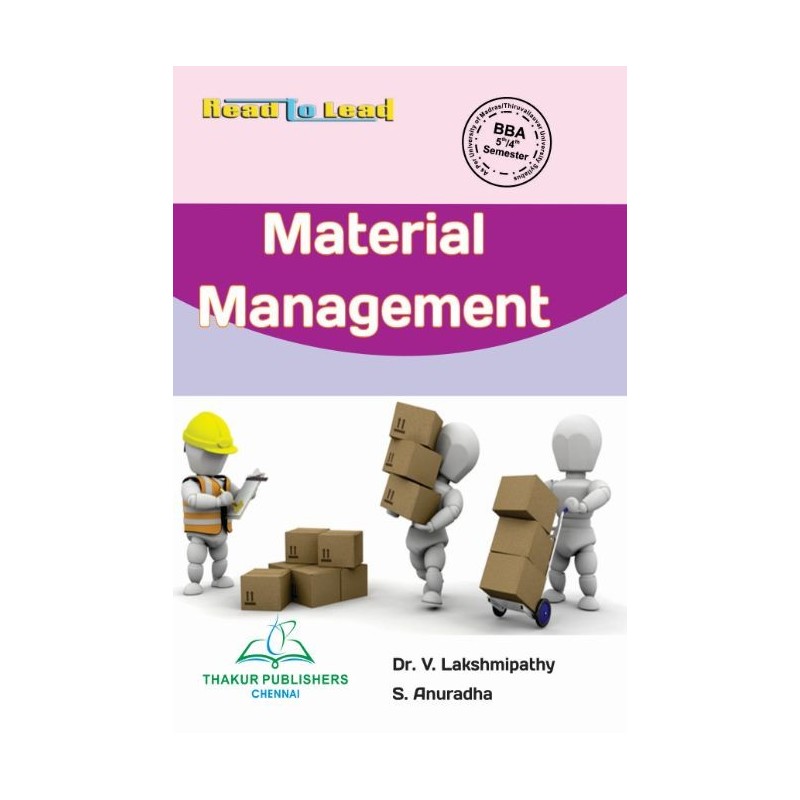
Batch manufacturing is similar, but works in small, discrete quantities. It is generally faster and requires less automation. It is however not suitable to all types of production. It's a good choice for products that are subject to frequent changes. It can also make custom products. It can be used for manufacturing products from materials that aren't easily broken down.
Discrete manufacturing is the other side of process manufacturing. It involves using a bill and instructions to make finished goods. It may include items like toys and automobiles. It can also involve the use of software and computers. The main difference is that process manufacturing requires fewer interruptions and higher quality control.
Injection molding is the most popular method for mass-producing plastic parts. This involves melting small plastic pellets and injecting them into a mold. After cooling, the mold is mechanically ejected. To ensure uniform coating, the mold is also heated and rotated. This method is used to make a wide variety of products, from pipes to straws.
A third type of manufacturing process is atomic manufacturing. This process is also known as "bottom-up" manufacturing. This method allows components to interact naturally. You can also make products out of biological materials. Parts can be manually added or automated in some cases.
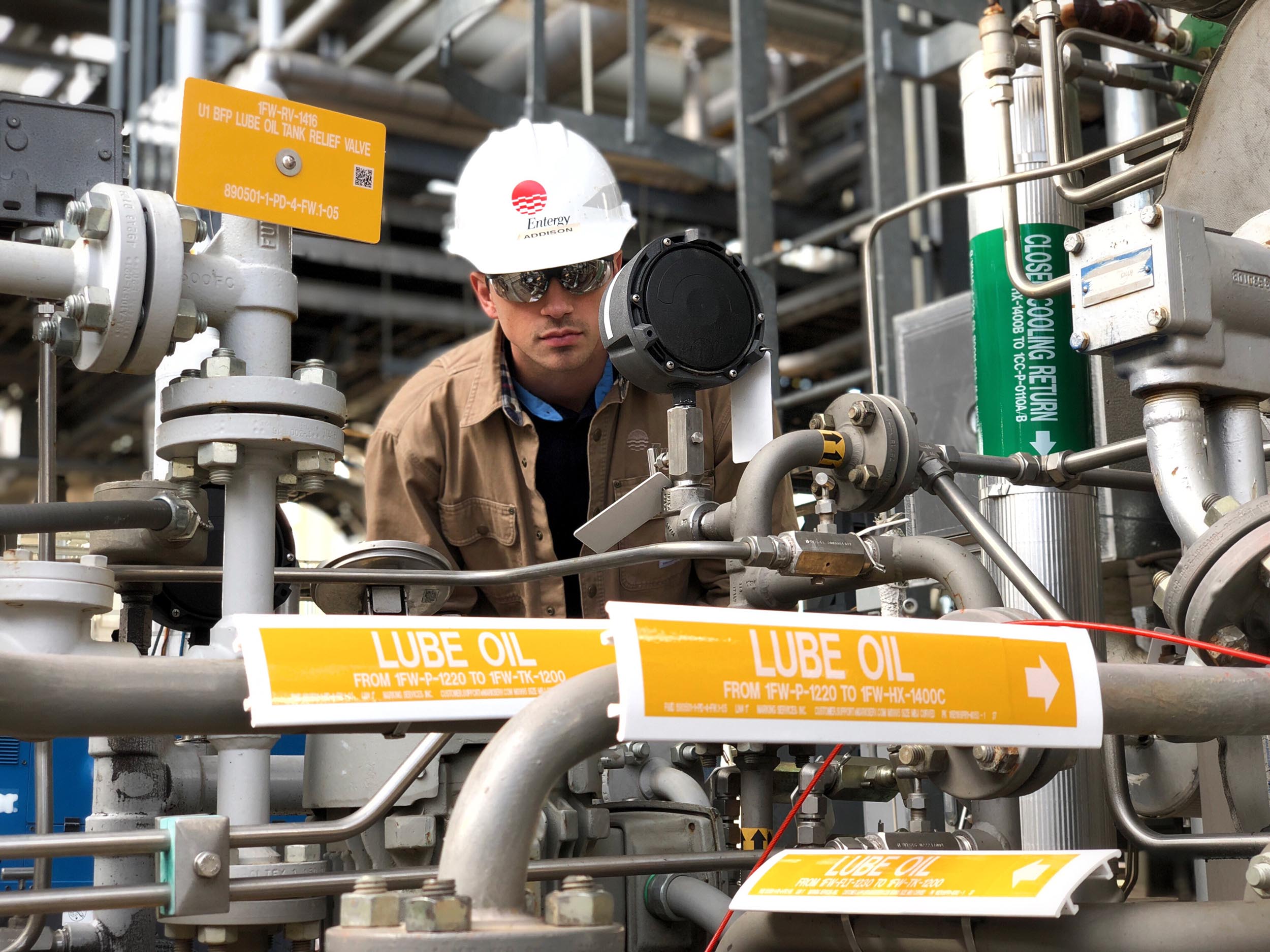
Another form of process manufacturing is intermittent manufacturing. This method can produce many identical items simultaneously, making it especially useful for small-volume production runs. However, this method is difficult to customize and not suitable for all product types.
A process manufacturing includes items that cannot be broken down such as ceramics and glass. Process manufacturing offers the main advantage of producing a wide range of products at high quality. Also, there are fewer interruptions and a lower defect incidence in process manufacturing.
FAQ
Can some manufacturing processes be automated?
Yes! Automation has been around since ancient times. The Egyptians discovered the wheel thousands and years ago. We now use robots to help us with assembly lines.
There are many applications for robotics in manufacturing today. They include:
-
Automation line robots
-
Robot welding
-
Robot painting
-
Robotics inspection
-
Robots that create products
Automation can be applied to manufacturing in many other ways. 3D printing is a way to make custom products quickly and without waiting weeks or months for them to be manufactured.
What is production planning?
Production Planning is the creation of a plan to cover all aspects, such as scheduling, budgeting. Location, crew, equipment, props and other details. This document ensures that everything is prepared and available when you are ready for shooting. It should also provide information about how best to produce the best results while on set. This includes information on shooting times, locations, cast lists and crew details.
The first step is to decide what you want. You may already know where you want the film to be shot, or perhaps you have specific locations and sets you wish to use. Once you have identified the scenes and locations, you can start to determine which elements are required for each scene. For example, you might decide that you need a car but don't know exactly what model you want. This is where you can look up car models online and narrow down your options by choosing from different makes and models.
After you have selected the car you want, you can begin to think about additional features. What about additional seating? Perhaps you have someone who needs to be able to walk around the back of your car. You might want to change your interior color from black and white. These questions can help you decide the right look for your car. Also, think about what kind of shots you would like to capture. What type of shots will you choose? Maybe the engine or steering wheel is what you are looking to film. All of these things will help you identify the exact style of car you want to film.
Once you have established all the details, you can create a schedule. You can use a schedule to determine when and where you need it to be shot. Every day will have a time for you to arrive at the location, leave when you are leaving and return home when you are done. So everyone is clear about what they need to do. If you need to hire extra staff, you can make sure you book them in advance. It's not worth paying someone to show up if you haven't told him.
You will need to factor in the days that you have to film when creating your schedule. Some projects may only take a couple of days, while others could last for weeks. It is important to consider whether you require more than one photo per day when you create your schedule. Multiplying takes in the same area will result both in increased costs and a longer time. You can't be certain if you will need multiple takes so it is better not to shoot too many.
Budgeting is another important aspect of production planning. It is important to set a realistic budget so you can work within your budget. You can always lower the budget if you encounter unexpected problems. It is important to not overestimate how much you will spend. You will end up spending less money if you underestimate the cost of something.
Production planning is a complicated process. But once you understand how everything works together, it becomes much easier to plan future project.
What's the difference between Production Planning & Scheduling?
Production Planning (PP), is the process of deciding what production needs to take place at any given time. This can be done by forecasting demand and identifying production capabilities.
Scheduling refers the process by which tasks are assigned dates so that they can all be completed within the given timeframe.
Statistics
- According to the United Nations Industrial Development Organization (UNIDO), China is the top manufacturer worldwide by 2019 output, producing 28.7% of the total global manufacturing output, followed by the United States, Japan, Germany, and India.[52][53] (en.wikipedia.org)
- It's estimated that 10.8% of the U.S. GDP in 2020 was contributed to manufacturing. (investopedia.com)
- Job #1 is delivering the ordered product according to specifications: color, size, brand, and quantity. (netsuite.com)
- According to a Statista study, U.S. businesses spent $1.63 trillion on logistics in 2019, moving goods from origin to end user through various supply chain network segments. (netsuite.com)
- [54][55] These are the top 50 countries by the total value of manufacturing output in US dollars for its noted year according to World Bank.[56] (en.wikipedia.org)
External Links
How To
How to Use Lean Manufacturing in the Production of Goods
Lean manufacturing (or lean manufacturing) is a style of management that aims to increase efficiency, reduce waste and improve performance through continuous improvement. It was created in Japan by Taiichi Ohno during the 1970s and 80s. He received the Toyota Production System award (TPS), from Kanji Toyoda, founder of TPS. Michael L. Watkins published the book "The Machine That Changed the World", which was the first to be published about lean manufacturing.
Lean manufacturing, often described as a set and practice of principles, is aimed at improving the quality, speed, cost, and efficiency of products, services, and other activities. It is about eliminating defects and waste from all stages of the value stream. The five-steps of Lean Manufacturing are just-in time (JIT), zero defect and total productive maintenance (TPM), as well as 5S. Lean manufacturing emphasizes reducing non-value-added activities like inspection, rework and waiting.
Lean manufacturing is a way for companies to achieve their goals faster, improve product quality, and lower costs. Lean manufacturing can be used to manage all aspects of the value chain. Customers, suppliers, distributors, retailers and employees are all included. Lean manufacturing is widely used in many industries. Toyota's philosophy has been a key driver of success in many industries, including automobiles and electronics.
Lean manufacturing is based on five principles:
-
Define Value - Identify the value your business adds to society and what makes you different from competitors.
-
Reduce Waste - Remove any activity which doesn't add value to your supply chain.
-
Create Flow. Ensure that your work is uninterrupted and flows seamlessly.
-
Standardize and Simplify – Make processes as consistent, repeatable, and as simple as possible.
-
Building Relationships – Establish personal relationships with both external and internal stakeholders.
Although lean manufacturing has always been around, it is gaining popularity in recent years because of a renewed interest for the economy after 2008's global financial crisis. Many businesses have adopted lean manufacturing techniques to help them become more competitive. Many economists believe lean manufacturing will play a major role in economic recovery.
With many benefits, lean manufacturing is becoming more common in the automotive industry. These include improved customer satisfaction, reduced inventory levels, lower operating costs, increased productivity, and better overall safety.
Lean manufacturing can be applied to almost every aspect of an organization. Because it makes sure that all value chains are efficient and effectively managed, Lean Manufacturing is particularly helpful for organizations.
There are three types of lean manufacturing.
-
Just-in-Time Manufacturing (JIT): This type of lean manufacturing is commonly referred to as "pull systems." JIT refers to a system in which components are assembled at the point of use instead of being produced ahead of time. This strategy aims to decrease lead times, increase availability of parts and reduce inventory.
-
Zero Defects Manufacturing (ZDM),: ZDM is a system that ensures no defective units are left the manufacturing facility. Repairing a part that is damaged during assembly should be done, not scrapping. This is true even for finished products that only require minor repairs prior to shipping.
-
Continuous Improvement (CI): CI aims to improve the efficiency of operations by continuously identifying problems and making changes in order to eliminate or minimize waste. Continuous Improvement involves continuous improvement of processes.