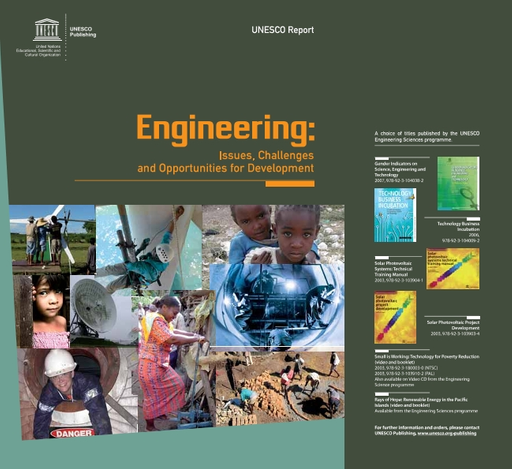
Lean training is an effective tool to reduce waste, streamline processes and improve efficiency. It empowers teams to work more efficiently, and produce more product with less effort. But it is crucial that every person in an organization understands lean. It is possible to do this with a customized training program that meets the individual needs of each team member.
Lean training is often delivered in classrooms with a hands-on approach, combining classroom instruction and intensive hands-on experience. A typical course involves 4 to 8 hours per week of involvement by trainees. Participants should be able make suggestions for improvement. Participants can improve the performance in their organization's processes using tools such as value streaming mapping and Plan-Do-Check-Act.
Many organizations prefer to use either professional or in house services for their Lean Training needs. For example, Clemson University offers four different programs for their employees.
Lean training is a vital tool to help your organization achieve success. More companies are using the method. You need to look for training programs that cover all key elements of Lean.
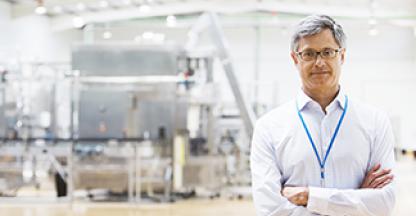
An introduction to lean should be the first step in your training. This workshop covers both the history and the principles of lean. It lasts approximately two hours. Learn how to use lean tools such as value stream mapping, kanban and kanban. You'll also learn how to improve customer experience.
Once you're comfortable with the basics, the Lean Thinking unit can be completed. This unit will teach you about continuous flow, value stream mapping, and error-proofing. All of these methods are essential to identifying and reducing waste in your business.
Afterwards, you will be introduced to Plan-Do-Check-Act. PDCA is a Lean improvement cycle that most practitioners use. You'll also learn the root causes of the problems during the course.
The final step is to learn how to make lean action plans. These plan outline your current state and highlight the improvements that you would like to make. You will receive a certificate of completion for your efforts. To obtain your certification, you must pass a multi-choice exam using the Lean Management Courseware.
Once you complete the program, it's time to start applying what you learned to your work. You'll learn how to lead and manage others, whether you're a technician, manager, or supervisor. You'll ultimately see positive results.
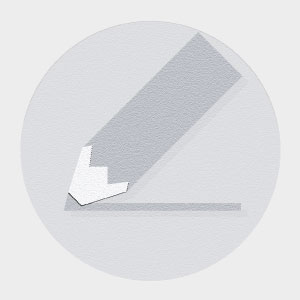
Finally, you can earn your Green Belt certificate. April Saunders oversees the Lean training at Virginia University Medical Center. She has over 12 year experience in manufacturing and teaches Lean.
Lean Fundamentals training programs are available in multiple languages. Participants will be taught how to quickly apply Lean concepts to their workplaces. This class is likely to have an immediate impact on your company.
This workshop will help you get started in lean implementing in your business, or to simply brush up your skills.
FAQ
Why is logistics important for manufacturing?
Logistics are an essential part of any business. They are essential to any business's success.
Logistics are also important in reducing costs and improving efficiency.
What skills does a production planner need?
A production planner must be organized, flexible, and able multitask to succeed. You must also be able to communicate effectively with clients and colleagues.
How can we reduce manufacturing overproduction?
The key to reducing overproduction lies in developing better ways to manage inventory. This would decrease the time that is spent on inefficient activities like purchasing, storing, or maintaining excess stock. We could use these resources to do other productive tasks.
Kanban systems are one way to achieve this. A Kanban board can be used to monitor work progress. Work items are moved through various states to reach their destination in a Kanban system. Each state represents an individual priority level.
To illustrate, work can move from one stage or another when it is complete enough for it to be moved to a new stage. If a task is still in its beginning stages, it will continue to be so until it reaches the end.
This allows for work to continue moving forward, while also ensuring that there is no work left behind. A Kanban board allows managers to monitor how much work is being completed at any given moment. This data allows them adjust their workflow based upon real-time data.
Lean manufacturing, another method to control inventory levels, is also an option. Lean manufacturing focuses on eliminating waste throughout the entire production chain. Anything that does not contribute to the product's value is considered waste. These are some of the most common types.
-
Overproduction
-
Inventory
-
Unnecessary packaging
-
Materials in excess
These ideas will help manufacturers increase efficiency and lower costs.
What is the role of a production manager?
A production planner makes sure all project elements are delivered on schedule, within budget, as well as within the agreed scope. A production planner ensures that the service and product meet the client's expectations.
Are there any Manufacturing Processes that we should know before we can learn about Logistics?
No. It doesn't matter if you don't know anything about manufacturing before you learn about logistics. Understanding the manufacturing process will allow you to better understand logistics.
What is manufacturing and logistics?
Manufacturing is the process of creating goods from raw materials by using machines and processes. Logistics is the management of all aspects of supply chain activities, including procurement, production planning, distribution, warehousing, inventory control, transportation, and customer service. Logistics and manufacturing are often referred to as one thing. It encompasses both the creation of products and their delivery to customers.
What are the essential elements of running a logistics firm?
To be a successful businessman in logistics, you will need many skills and knowledge. You must have good communication skills to interact effectively with your clients and suppliers. You will need to know how to interpret data and draw conclusions. You need to be able work under pressure and manage stressful situations. To improve efficiency, you must be innovative and creative. You must be a strong leader to motivate others and direct them to achieve organizational goals.
It is also important to be efficient and well organized in order meet deadlines.
Statistics
- Many factories witnessed a 30% increase in output due to the shift to electric motors. (en.wikipedia.org)
- In the United States, for example, manufacturing makes up 15% of the economic output. (twi-global.com)
- According to a Statista study, U.S. businesses spent $1.63 trillion on logistics in 2019, moving goods from origin to end user through various supply chain network segments. (netsuite.com)
- It's estimated that 10.8% of the U.S. GDP in 2020 was contributed to manufacturing. (investopedia.com)
- You can multiply the result by 100 to get the total percent of monthly overhead. (investopedia.com)
External Links
How To
How to use Lean Manufacturing in the production of goods
Lean manufacturing is an approach to management that aims for efficiency and waste reduction. It was created in Japan by Taiichi Ohno during the 1970s and 80s. He received the Toyota Production System award (TPS), from Kanji Toyoda, founder of TPS. The first book published on lean manufacturing was titled "The Machine That Changed the World" written by Michael L. Watkins and published in 1990.
Lean manufacturing refers to a set of principles that improve the quality, speed and costs of products and services. It emphasizes the elimination of defects and waste throughout the value stream. The five-steps of Lean Manufacturing are just-in time (JIT), zero defect and total productive maintenance (TPM), as well as 5S. Lean manufacturing is about eliminating activities that do not add value, such as inspection, rework, and waiting.
Lean manufacturing is a way for companies to achieve their goals faster, improve product quality, and lower costs. Lean manufacturing has been deemed one of the best ways to manage the entire value-chain, including customers, distributors as well retailers and employees. Lean manufacturing is widely practiced in many industries around the world. Toyota's philosophy is a great example of this. It has helped to create success in automobiles as well electronics, appliances and healthcare.
Five principles are the basis of lean manufacturing:
-
Define Value: Identify the social value of your business and what sets you apart.
-
Reduce Waste - Eliminate any activity that doesn't add value along the supply chain.
-
Create Flow. Ensure that your work is uninterrupted and flows seamlessly.
-
Standardize and simplify - Make your processes as consistent as possible.
-
Building Relationships – Establish personal relationships with both external and internal stakeholders.
Lean manufacturing, although not new, has seen renewed interest in the economic sector since 2008. Many businesses have adopted lean production techniques to make them more competitive. Some economists even believe that lean manufacturing can be a key factor in economic recovery.
Lean manufacturing, which has many benefits, is now a standard practice in the automotive industry. These include higher customer satisfaction levels, reduced inventory levels as well as lower operating costs.
Any aspect of an enterprise can benefit from Lean manufacturing. Lean manufacturing is most useful in the production sector of an organisation because it ensures that each step in the value-chain is efficient and productive.
There are three main types:
-
Just-in Time Manufacturing: This lean manufacturing method is commonly called "pull systems." JIT is a process in which components can be assembled at the point they are needed, instead of being made ahead of time. This approach reduces lead time, increases availability and reduces inventory.
-
Zero Defects Manufacturing: ZDM ensures that no defective units leave the manufacturing plant. If a part needs to be fixed during the assembly line, it should be repaired rather than scrapped. This also applies to finished products that need minor repairs before being shipped.
-
Continuous Improvement (CI): CI aims to improve the efficiency of operations by continuously identifying problems and making changes in order to eliminate or minimize waste. It involves continuous improvement of processes, people, and tools.