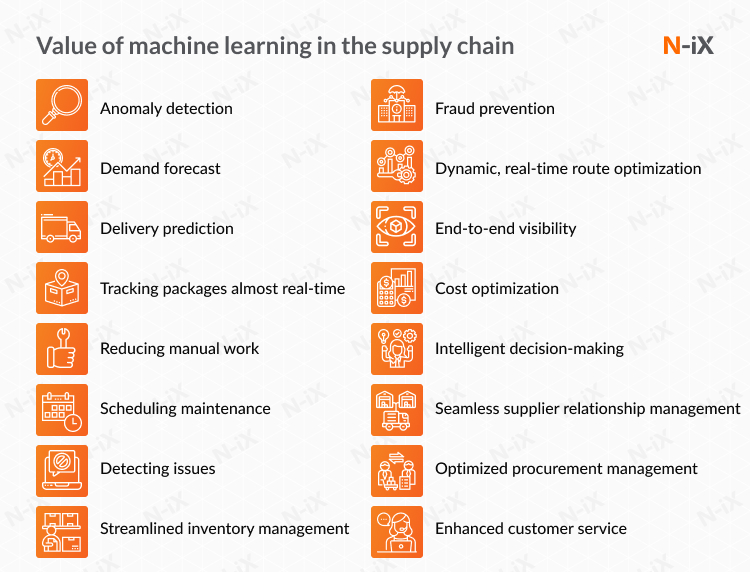
Supply Dynamics, a multi-enterprise supply channel analytics suite, was established in Loveland Ohio in 2003. It provides technology solutions to manufacturers operating in highly distributed manufacturing environments. Supply Dynamics works in partnership with the Navy and the Defense Logistics Agency (DLA). It provides visibility and control of an organization's end-to-end supply chain. It helps manufacturers plan production and reduce the costs of raw materials. Supply Dynamics works with a variety of industries including aerospace, defense, manufacturing, and transportation.
Dynamics 365 Supply Chain Management (powered by Microsoft Cloud) is a Microsoft Cloud-powered software that enables organizations improve operational efficiency, streamline manufacturing, and build strong supply chain networks. It provides flexibility, predictive analytics, and unparalleled visibility into all aspects of the supply chain. Its modules ensure that products reach their customers on-time and provide functionality for the entire product lifecycle.
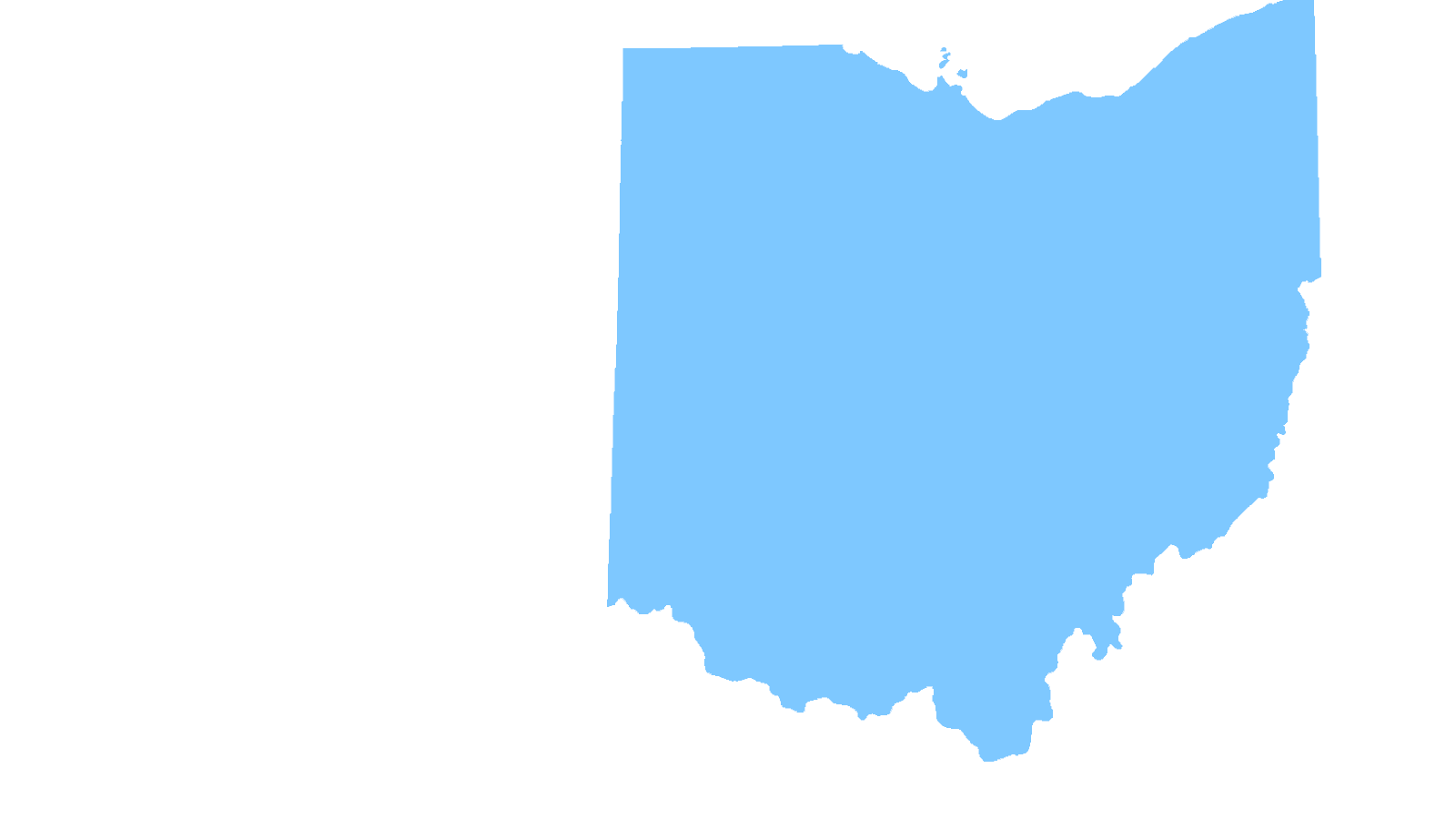
The Dynamics Supply Chain module includes features that allow users to configure items for process or discrete manufacturing, submit RFQs, test product quality, and submit purchase orders. Gantt charts can be created to show transparency and allow users to plan all operations. Using the Visual Supply Schedule, users can see a forecast of inventory levels and anticipated supply and demand. When supply chain problems arise, they can adjust the schedules. It allows managers to monitor the progress of job functions across different areas of a production floor.
Microsoft Dynamics 365 Supply Chain Management allows organizations to use a single, predictive and unified way to manage customer demand. It also ensures that the right materials arrive at the right time. It also helps businesses anticipate customer demands and changes in capacity. It can be used to integrate logistics, purchasing, production, and can even be used for multiple warehouses or sites. It supports vendor-specific pricing and multiple inventory costing methods. It can also be used for transportation management. The solution can also be used to optimize inventory and use predictive analytics.
Dynamics 365 also offers self-service for suppliers. Suppliers are able to accept or reject buy orders, issue POs with invoices, and enter shipment information. It supports multiple inventory costing methods such as vendor-specific pricing, item level, item group, and item-level pricing. It also includes several inventory optimization features, including the ability to create an inventory allocation plan for an order.
Supply Dynamics also offers unique metals benchmarking solutions. With this technology, manufacturers are able to respond quicker to fluctuations in marketplace prices. They can also anticipate and predict fluctuations in production costs. This technology is able to reduce raw material costs, which in turn reduces waste. It also provides manufacturers with a blueprint for the bill-of-material data conversion process.
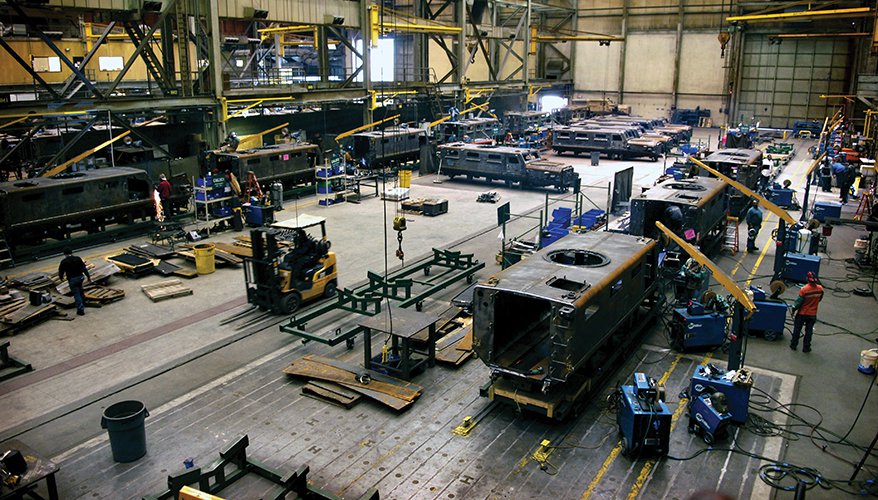
Its master planning feature allows for the automatic creation of Production Orders using open purchase orders. It also features an optimization plugin that lets users forecast changes in customer needs. It also uses AI capabilities to increase the flow and distribution of goods. Microsoft has certified Dynamics Supply Chain Management as a solution for companies looking for a strong supply chain.
FAQ
Why is logistics important in manufacturing
Logistics are essential to any business. Logistics can help you achieve amazing results by helping to manage product flow from raw materials to finished products.
Logistics play an important role in reducing costs as well as increasing efficiency.
How can overproduction in manufacturing be reduced?
The key to reducing overproduction lies in developing better ways to manage inventory. This would decrease the time that is spent on inefficient activities like purchasing, storing, or maintaining excess stock. This will allow us to free up resources for more productive tasks.
Kanban systems are one way to achieve this. A Kanban board, a visual display to show the progress of work, is called a Kanban board. A Kanban system allows work items to move through several states before reaching their final destination. Each state represents an individual priority level.
If work is moving from one stage to the other, then the current task can be completed and moved on to the next. However, if a task is still at the beginning stages, it will remain so until it reaches the end of the process.
This allows you to keep work moving along while making sure that no work gets neglected. Managers can view the Kanban board to see how much work they have done. This allows them the ability to adjust their workflow using real-time data.
Lean manufacturing can also be used to reduce inventory levels. Lean manufacturing works to eliminate waste throughout every stage of the production chain. Anything that doesn't add value to the product is considered waste. Here are some examples of common types.
-
Overproduction
-
Inventory
-
Unnecessary packaging
-
Overstock materials
These ideas can help manufacturers improve efficiency and reduce costs.
What's the difference between Production Planning & Scheduling?
Production Planning (PP), also known as forecasting and identifying production capacities, is the process that determines what product needs to be produced at any particular time. This is accomplished by forecasting the demand and identifying production resources.
Scheduling is the process that assigns dates to tasks so they can get completed within a given timeframe.
What are the four types of manufacturing?
Manufacturing is the process of transforming raw materials into useful products using machines and processes. Manufacturing involves many activities, including designing, building, testing and packaging, shipping, selling, service, and so on.
Statistics
- (2:04) MTO is a production technique wherein products are customized according to customer specifications, and production only starts after an order is received. (oracle.com)
- According to the United Nations Industrial Development Organization (UNIDO), China is the top manufacturer worldwide by 2019 output, producing 28.7% of the total global manufacturing output, followed by the United States, Japan, Germany, and India.[52][53] (en.wikipedia.org)
- Job #1 is delivering the ordered product according to specifications: color, size, brand, and quantity. (netsuite.com)
- Many factories witnessed a 30% increase in output due to the shift to electric motors. (en.wikipedia.org)
- You can multiply the result by 100 to get the total percent of monthly overhead. (investopedia.com)
External Links
How To
Six Sigma: How to Use it in Manufacturing
Six Sigma can be described as "the use of statistical process control (SPC), techniques to achieve continuous improvement." Motorola's Quality Improvement Department created Six Sigma at their Tokyo plant, Japan in 1986. Six Sigma's main goal is to improve process quality by standardizing processes and eliminating defects. Many companies have adopted this method in recent years. They believe there is no such thing a perfect product or service. Six Sigma seeks to reduce variation between the mean production value. You can calculate the percentage of deviation from the norm by taking a sample of your product and comparing it to the average. If the deviation is excessive, it's likely that something needs to be fixed.
The first step toward implementing Six Sigma is understanding how variability works in your business. Once you understand that, it is time to identify the sources of variation. Also, you will need to identify the sources of variation. Random variations occur when people make mistakes; systematic ones are caused by factors outside the process itself. You could consider random variations if some widgets fall off the assembly lines. However, if you notice that every time you assemble a widget, it always falls apart at exactly the same place, then that would be a systematic problem.
Once you've identified the problem areas you need to find solutions. That solution might involve changing the way you do things or redesigning the process altogether. Once you have implemented the changes, it is important to test them again to ensure they work. If they don't work, you will need to go back to the drawing boards and create a new plan.