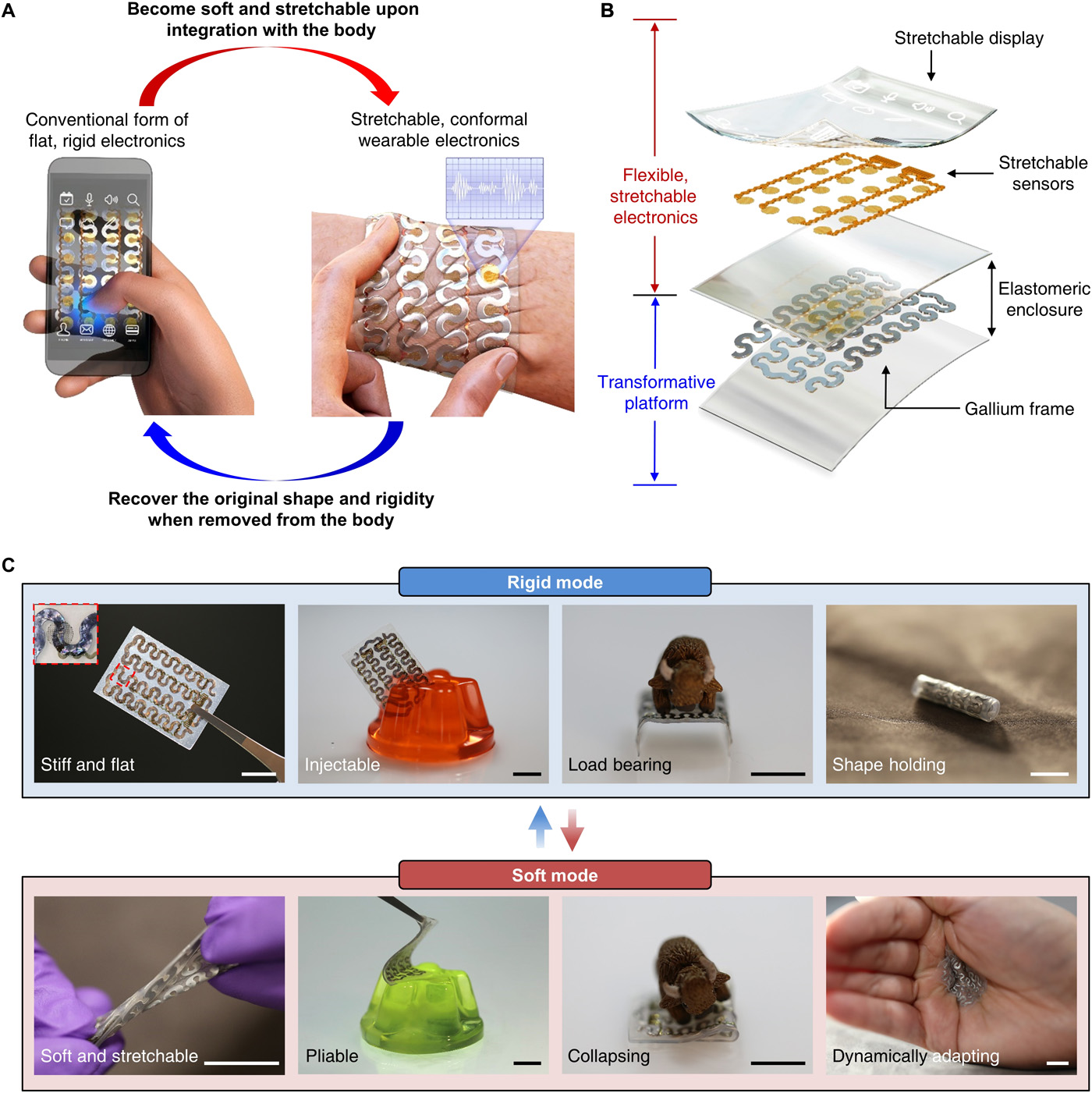
Typically, tool and die makers work in machine shops. They use lathes, milling machine, and other types to operate machines. They also repair tools and dies for machinists. They may also design tools for customers.
Tool and Die makers must adhere to strict quality control and precision in all of their work. They verify the accuracy of their work, and inspect finished products. Engineers may be consulted by tool and die makers to improve their processes. They may also travel to a customer's plant to see how the tool is working. They must also keep their work areas clean and organized. They may be required to wear protective equipment. They may suggest additional tools to improve efficiency.
Tool and die makers typically work 40 hours a week. They may also be expected do moderately heavy lifting. A strong education background is also necessary. Employers may prefer an associate's, bachelor's, or master's degree in a similar field. They might also receive training on-the-job or apprentice programs.

Tool and die makers typically attend four-year apprenticeship programs with employers. They receive training on the job from an experienced worker during their apprenticeship program. They can also take technical college courses at night. The program includes hands-on training, as well as classroom instruction. They might also be able to program computer-controlled machines. They may also have the opportunity to advance to supervisory or managerial positions.
A high school diploma is usually required for tool and die makers. They may also have a degree that is technical in physics or engineering. They may have had prior training in science and math. This training can be very helpful.
Tool and diemakers need good eyesight. They must be patient and have excellent concentration. They need to have physical strength in order to work with machinery. They must have a strong work ethic, and be able to lift heavy loads. They should have the ability to read engineering drawings. They should also possess good interpersonal skills. They should also have strong computer skills. They might also be needed to maintain computer numerically controlled machines (CNC).
Tool and diemakers need to be analytical. They must understand how tools work and how to fix them. They must also be able to solve problems and have mechanical ability. They may also need to be able to learn new machining techniques. They will need to be proficient in digital skills like computer-aided planning (CAD) and computer aided manufacturing (CAM). They must also be able to sell. They should be able to work independently and with others.
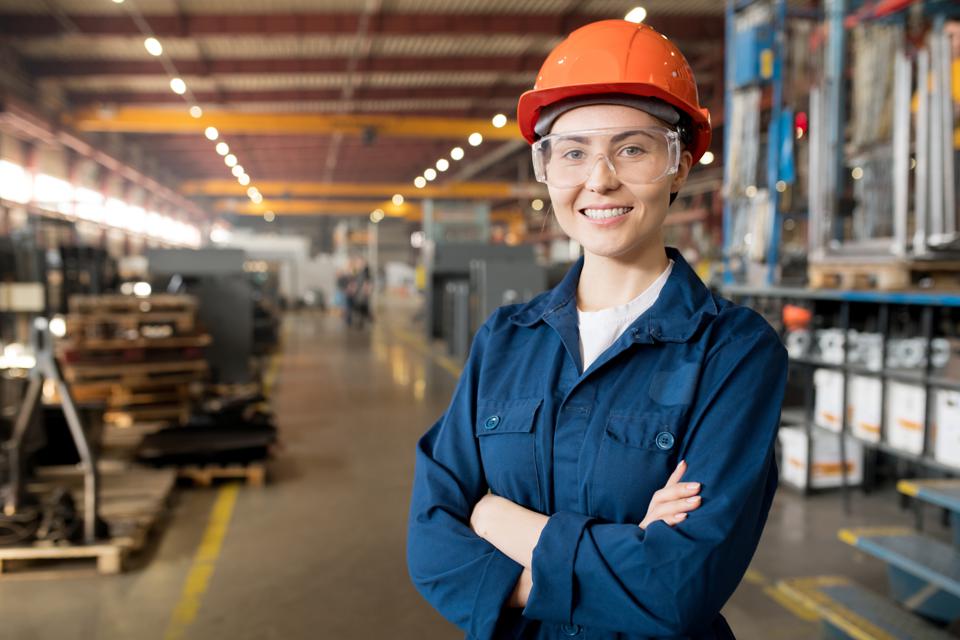
Apprentices usually work 40 hours per week in an apprenticeship program. They attend classroom courses at night and work on a job during the day. They eventually accept more challenging jobs. For most apprenticeships, you will need a high school diploma. They should also be able to learn science and math.
Some tool or die makers continue on to pursue a bachelor’s or master’s degree. The average salary of tool and die makers is $56,186. However, automation is predicted to lower their chances of finding work in the future.
FAQ
What is the role of a production manager?
A production planner makes sure all project elements are delivered on schedule, within budget, as well as within the agreed scope. They ensure that the product or service is of high quality and meets client requirements.
Is it possible to automate certain parts of manufacturing
Yes! Since ancient times, automation has been in existence. The Egyptians created the wheel thousands years ago. Nowadays, we use robots for assembly lines.
There are many uses of robotics today in manufacturing. These include:
-
Automation line robots
-
Robot welding
-
Robot painting
-
Robotics inspection
-
Robots that create products
Manufacturing can also be automated in many other ways. For instance, 3D printing allows us make custom products and not have to wait for months or even weeks to get them made.
How can manufacturing efficiency be improved?
First, determine which factors have the greatest impact on production time. We must then find ways that we can improve these factors. You can start by identifying the most important factors that impact production time. Once you've identified them all, find solutions to each one.
Why is logistics important in manufacturing
Logistics are an integral part any business. They can help you achieve great success by helping you manage product flow from raw material to finished goods.
Logistics play an important role in reducing costs as well as increasing efficiency.
What are the essential elements of running a logistics firm?
You need to have a lot of knowledge and skills to manage a successful logistic business. Good communication skills are essential to effectively communicate with your suppliers and clients. It is important to be able to analyse data and draw conclusions. You must be able to work well under pressure and handle stressful situations. In order to innovate and create new ways to improve efficiency, creativity is essential. You must be a strong leader to motivate others and direct them to achieve organizational goals.
You should also be organized and efficient to meet tight deadlines.
What are the responsibilities of a logistic manager?
A logistics manager ensures that all goods are delivered on time and without damage. This is achieved by using their knowledge and experience with the products of the company. He/she should also ensure enough stock is available to meet demand.
What are the differences between these four types?
Manufacturing refers the process of turning raw materials into useful products with machines and processes. Manufacturing can include many activities such as designing and building, testing, packaging shipping, selling, servicing, and other related activities.
Statistics
- [54][55] These are the top 50 countries by the total value of manufacturing output in US dollars for its noted year according to World Bank.[56] (en.wikipedia.org)
- According to the United Nations Industrial Development Organization (UNIDO), China is the top manufacturer worldwide by 2019 output, producing 28.7% of the total global manufacturing output, followed by the United States, Japan, Germany, and India.[52][53] (en.wikipedia.org)
- In 2021, an estimated 12.1 million Americans work in the manufacturing sector.6 (investopedia.com)
- (2:04) MTO is a production technique wherein products are customized according to customer specifications, and production only starts after an order is received. (oracle.com)
- Many factories witnessed a 30% increase in output due to the shift to electric motors. (en.wikipedia.org)
External Links
How To
How to use 5S in Manufacturing to Increase Productivity
5S stands for "Sort", "Set In Order", "Standardize", "Separate" and "Store". The 5S methodology was developed at Toyota Motor Corporation in 1954. It improves the work environment and helps companies to achieve greater efficiency.
The basic idea behind this method is to standardize production processes, so they become repeatable, measurable, and predictable. This means that tasks such as cleaning, sorting, storing, packing, and labeling are performed daily. This knowledge allows workers to be more efficient in their work because they are aware of what to expect.
There are five steps to implementing 5S, including Sort, Set In Order, Standardize, Separate and Store. Each step is a different action that leads to greater efficiency. You can make it easy for people to find things later by sorting them. When you set items in an order, you put items together. Then, after you separate your inventory into groups, you store those groups in containers that are easy to access. Labeling your containers will ensure that everything is correctly labeled.
Employees will need to be more critical about their work. Employees must be able to see why they do what they do and find a way to achieve them without having to rely on their old methods. They must learn new skills and techniques in order to implement the 5S system.
The 5S Method not only improves efficiency, but it also helps employees to be more productive and happier. They will feel motivated to strive for higher levels of efficiency once they start to see results.