
Logistics coordinators are responsible for ensuring goods arrive at their destination on time, and in the most cost-effective manner possible. You'll be responsible for ensuring that goods get delivered to the customer in a timely fashion. Our article provides more information on logistics. In this article, you'll learn more about the roles and responsibilities of inventory analysts, customer service specialists, and supply-chain managers. Below are the most prominent jobs in logistics.
Logistics coordinator
Monster has thousands of job opportunities for logistics coordinators. This type of job requires you to be hands-on. Candidates with little to no experience are generally expected to take up the training from an apprenticeship or internship, but they can also have previous industry experience. You might also be interested in applying for a job at the logistics coordinator position if your previous experience is extensive.
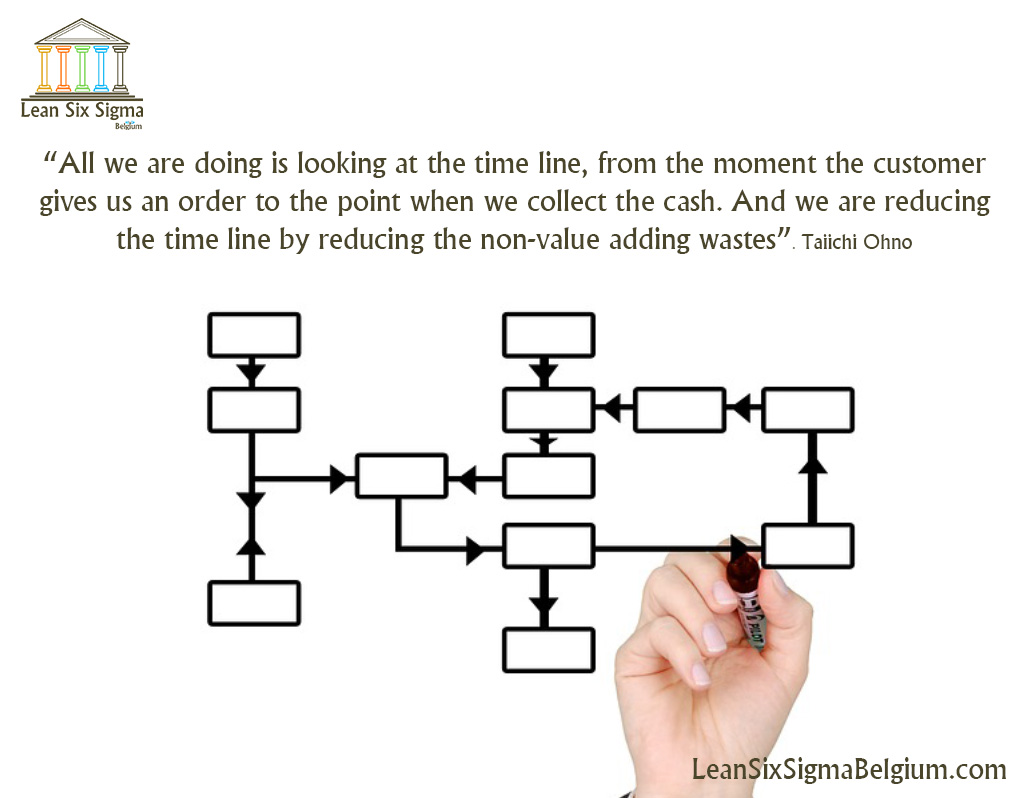
Customer service specialist
Customer service specialists are responsible for managing and delivering customer service. They maintain contact with customers, coordinate inland transport, and address customer concerns and complaints. They also manage customer relationships and coordinate appointments. As a customer support specialist, you will also coordinate all necessary documents and documentation to ensure timely and affordable delivery.
Analyst for inventory
An Inventory Analyst is responsible to maintain service level and improve inventory productivity. Their primary responsibilities include order fulfillment for TSC Feed programmes, as well managing the day to day activities of inventory replenishment. They support assortment and merchandise plans by managing inventory levels in their assigned product categories. They monitor trends and make plans for article-site replenishment. They may also assist with marketing and promotional activities. They often analyze sales data and create new strategies to improve business efficiency.
Manager Supply Chain
The role of a supply chain manager involves managing the flow and movement of materials from suppliers to manufacturers and customers. The role requires a wide range of skills, and a bachelor's degree is typically required. Many employers prefer candidates who have a master's in business administration. There are several ways to be a supply-chain manager. This career field is available to learn more. Consider getting an associate's in business administration if you are interested in a career in supply chain management.
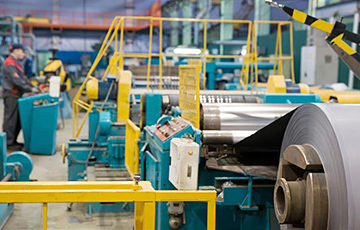
Freight agent
While you're creating your job description, make sure to include a section on your cargo and freight agent responsibilities. A job description should list the essential responsibilities of the position so that potential applicants are able to easily see what they will need to do each day. Strong action verbs are important in your job description to attract qualified applicants. It is important to include in the job description a list detailing all qualifications needed for this position.
FAQ
What are the 7 Rs of logistics?
The acronym 7R's for Logistics stands to represent the seven basic principles in logistics management. It was developed and published by the International Association of Business Logisticians in 2004 as part of the "Seven Principles of Logistics Management".
The acronym is composed of the following letters.
-
Responsible - ensure that actions are in compliance with legal requirements and do not cause harm to others.
-
Reliable – have faith in your ability and capability to keep promises.
-
Reasonable - use resources efficiently and don't waste them.
-
Realistic - Consider all aspects of operations, including environmental impact and cost effectiveness.
-
Respectful - treat people fairly and equitably.
-
Be resourceful: Look for opportunities to save money or increase productivity.
-
Recognizable - Provide value-added services to customers
What is the role of a logistics manager
Logistics managers are responsible for ensuring that all goods arrive in perfect condition and on time. This is achieved by using their knowledge and experience with the products of the company. He/she should ensure that sufficient stock is available in order to meet customer demand.
What are the four types of manufacturing?
Manufacturing refers to the transformation of raw materials into useful products by using machines and processes. Manufacturing involves many activities, including designing, building, testing and packaging, shipping, selling, service, and so on.
What is the difference between Production Planning and Scheduling?
Production Planning (PP), or production planning, is the process by which you determine what products are needed at any given time. Forecasting demand is one way to do this.
Scheduling refers the process by which tasks are assigned dates so that they can all be completed within the given timeframe.
What is the role of a manager in manufacturing?
The manufacturing manager should ensure that every manufacturing process is efficient and effective. They should be alert for any potential problems in the company and react accordingly.
They should also know how to communicate with other departments such as sales and marketing.
They should be informed about industry trends and be able make use of this information to improve their productivity and efficiency.
Statistics
- In 2021, an estimated 12.1 million Americans work in the manufacturing sector.6 (investopedia.com)
- According to a Statista study, U.S. businesses spent $1.63 trillion on logistics in 2019, moving goods from origin to end user through various supply chain network segments. (netsuite.com)
- You can multiply the result by 100 to get the total percent of monthly overhead. (investopedia.com)
- Job #1 is delivering the ordered product according to specifications: color, size, brand, and quantity. (netsuite.com)
- (2:04) MTO is a production technique wherein products are customized according to customer specifications, and production only starts after an order is received. (oracle.com)
External Links
How To
How to Use Six Sigma in Manufacturing
Six Sigma is defined as "the application of statistical process control (SPC) techniques to achieve continuous improvement." Motorola's Quality Improvement Department, Tokyo, Japan, developed it in 1986. The basic idea behind Six Sigma is to improve quality by improving processes through standardization and eliminating defects. In recent years, many companies have adopted this method because they believe there is no such thing as perfect products or services. Six Sigma aims to reduce variation in the production's mean value. It is possible to measure the performance of your product against an average and find the percentage of time that it differs from the norm. If you notice a large deviation, then it is time to fix it.
Understanding how your business' variability is a key step towards Six Sigma implementation is the first. Once you understand this, you can then identify the causes of variation. These variations can also be classified as random or systematic. Random variations are caused by human errors. Systematic variations can be caused by outside factors. These are, for instance, random variations that occur when widgets are made and some fall off the production line. However, if you notice that every time you assemble a widget, it always falls apart at exactly the same place, then that would be a systematic problem.
Once you have identified the problem, you can design solutions. It might mean changing the way you do business or redesigning it entirely. Test them again once you've implemented the changes. If they don't work you need to rework them and come up a better plan.