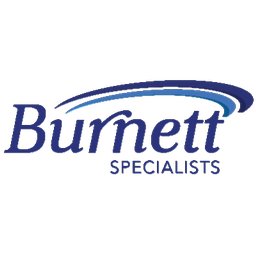
Watts, when he finished high school, had no idea he'd end up at Towson University as a major in supply chain. Jack Jensen's, managing director of Moore School's program in supply chain management, convinced Watts that the program was for him by promising him an opportunity to work with the school's capstone consultancy project.
The capstone project, one of the more prestigious courses in undergraduate business school curriculum, lets students dig deep into supply chain problems on real-world projects for companies and nonprofits. Jensen said that in the last eight-years, Moore School undergraduate students worked with over 150 companies to identify cost saving totaling more $175 million.
During their courses, students work closely together with advisors in the classroom and organizations on real-world issues relating to supply chains. They use data science tools including Lean Manufacturing (Lean Manufacturing) and Six Sigma. They learn how to prepare, transform, and organize data, create models, and evaluate the results.
Students complete a capstone course project after completing their studies. They present the problem and its significance for theory and business, the background of the project, the research, the method and the results.
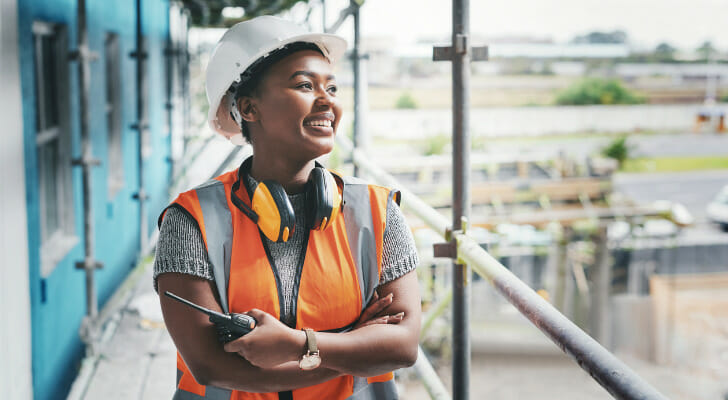
A capstone project can be a wonderful way to learn and demonstrate your commitment to education.
Many schools now offer students the chance to complete a capstone as part of graduation requirements. These projects can be very challenging, and students often need to spend a significant amount of time and effort to complete them.
The project may be completed over the course a semester, or even longer. It should generally take 100-120 working hours to complete.
Towson Place is a student community with studios, two-bedrooms and three-bedrooms located a short distance from the campus. Professionally managed by Capstone Management, residents enjoy a variety of amenities designed to meet their needs.
Millennium Hall consists of three separate buildings, each with 400 beds. The design was created in partnership between Towson and the University. Students at both the undergraduate level and graduate school are housed in this building. The complex consists of studios as well one and two bedroom units. There is also a central mailbox and a laundry facility.
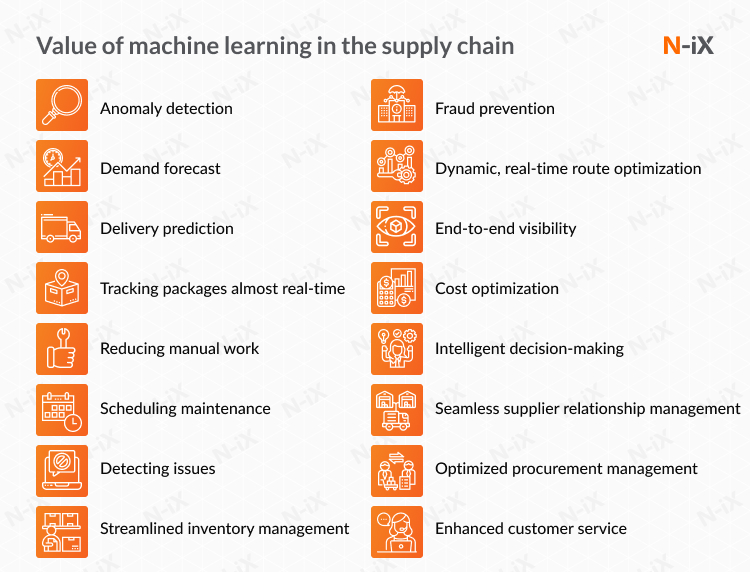
MEDCO leases Millennium Hall and Paca and Tubman Houses from TU. Capstone Properties Inc. manages the day-today activities for MEDCO.
Several families have sued MEDCO, claiming breach of contract. They claim that their lease agreements are holding them hostage as TU moves to distance learning. They claim that MEDCO is refusing to release their leases and refunds, despite that they follow the guidelines of TU Housing and Residence Life's Campus Living Services and Center for Disease Control's (CDC).
The lawsuit was first filed in march 2018 but has not yet been settled. Lucchi plans to continue the case after receiving responses from MEDCO legal council.
FAQ
What is the difference between Production Planning and Scheduling?
Production Planning (PP), also known as forecasting and identifying production capacities, is the process that determines what product needs to be produced at any particular time. Forecasting and identifying production capacity are two key elements to this process.
Scheduling is the process that assigns dates to tasks so they can get completed within a given timeframe.
What is the responsibility of a manufacturing manager?
A manufacturing manager must ensure that all manufacturing processes are efficient and effective. They should be aware of any issues within the company and respond accordingly.
They should also know how to communicate with other departments such as sales and marketing.
They must also keep up-to-date with the latest trends in their field and be able use this information to improve productivity and efficiency.
What are the four types of manufacturing?
Manufacturing is the process by which raw materials are transformed into useful products through machines and processes. Manufacturing involves many activities, including designing, building, testing and packaging, shipping, selling, service, and so on.
What are the 7 Rs of logistics?
The acronym "7R's" of Logistics stands for seven principles that underpin logistics management. It was created by the International Association of Business Logisticians and published in 2004 under its "Seven Principles of Logistics Management".
The acronym is composed of the following letters.
-
Responsible – ensure that all actions are legal and don't cause harm to anyone else.
-
Reliable - have confidence in the ability to deliver on commitments made.
-
Use resources effectively and sparingly.
-
Realistic – Consider all aspects, including cost-effectiveness as well as environmental impact.
-
Respectful - treat people fairly and equitably.
-
Be resourceful: Look for opportunities to save money or increase productivity.
-
Recognizable - Provide value-added services to customers
Why is logistics important in manufacturing
Logistics are essential to any business. They are essential to any business's success.
Logistics also play a major role in reducing costs and increasing efficiency.
Statistics
- According to a Statista study, U.S. businesses spent $1.63 trillion on logistics in 2019, moving goods from origin to end user through various supply chain network segments. (netsuite.com)
- It's estimated that 10.8% of the U.S. GDP in 2020 was contributed to manufacturing. (investopedia.com)
- In the United States, for example, manufacturing makes up 15% of the economic output. (twi-global.com)
- [54][55] These are the top 50 countries by the total value of manufacturing output in US dollars for its noted year according to World Bank.[56] (en.wikipedia.org)
- According to the United Nations Industrial Development Organization (UNIDO), China is the top manufacturer worldwide by 2019 output, producing 28.7% of the total global manufacturing output, followed by the United States, Japan, Germany, and India.[52][53] (en.wikipedia.org)
External Links
How To
How to use Lean Manufacturing in the production of goods
Lean manufacturing is a management system that aims at increasing efficiency and reducing waste. It was developed by Taiichi Okono in Japan, during the 1970s & 1980s. TPS founder Kanji Takoda awarded him the Toyota Production System Award (TPS). Michael L. Watkins published the "The Machine That Changed the World", the first book about lean manufacturing. It was published in 1990.
Lean manufacturing can be described as a set or principles that are used to improve quality, speed and cost of products or services. It emphasizes the elimination and minimization of waste in the value stream. The five-steps of Lean Manufacturing are just-in time (JIT), zero defect and total productive maintenance (TPM), as well as 5S. Lean manufacturing eliminates non-value-added tasks like inspection, rework, waiting.
Lean manufacturing is a way for companies to achieve their goals faster, improve product quality, and lower costs. Lean manufacturing can be used to manage all aspects of the value chain. Customers, suppliers, distributors, retailers and employees are all included. Many industries worldwide use lean manufacturing. Toyota's philosophy is the foundation of its success in automotives, electronics and appliances, healthcare, chemical engineers, aerospace, paper and food, among other industries.
Five principles are the basis of lean manufacturing:
-
Define Value: Identify the social value of your business and what sets you apart.
-
Reduce waste - Get rid of any activity that does not add value to the supply chain.
-
Create Flow: Ensure that the work process flows without interruptions.
-
Standardize & Simplify - Make processes as consistent and repeatable as possible.
-
Build relationships - Develop and maintain personal relationships with both your internal and external stakeholders.
Although lean manufacturing has always been around, it is gaining popularity in recent years because of a renewed interest for the economy after 2008's global financial crisis. Many businesses have adopted lean manufacturing techniques to help them become more competitive. In fact, some economists believe that lean manufacturing will be an important factor in economic recovery.
With many benefits, lean manufacturing is becoming more common in the automotive industry. These include improved customer satisfaction, reduced inventory levels, lower operating costs, increased productivity, and better overall safety.
Lean manufacturing can be applied to almost every aspect of an organization. However, it is particularly useful when applied to the production side of an organization because it ensures that all steps in the value chain are efficient and effective.
There are three main types:
-
Just-in-Time Manufacturing: Also known as "pull systems", this type of lean manufacturing uses just-in-time manufacturing (JIT). JIT is a process in which components can be assembled at the point they are needed, instead of being made ahead of time. This approach reduces lead time, increases availability and reduces inventory.
-
Zero Defects Manufacturing: ZDM ensures that no defective units leave the manufacturing plant. If a part needs to be fixed during the assembly line, it should be repaired rather than scrapped. This also applies to finished products that need minor repairs before being shipped.
-
Continuous Improvement (CI): CI aims to improve the efficiency of operations by continuously identifying problems and making changes in order to eliminate or minimize waste. Continuous improvement refers to continuous improvement of processes as well people and tools.