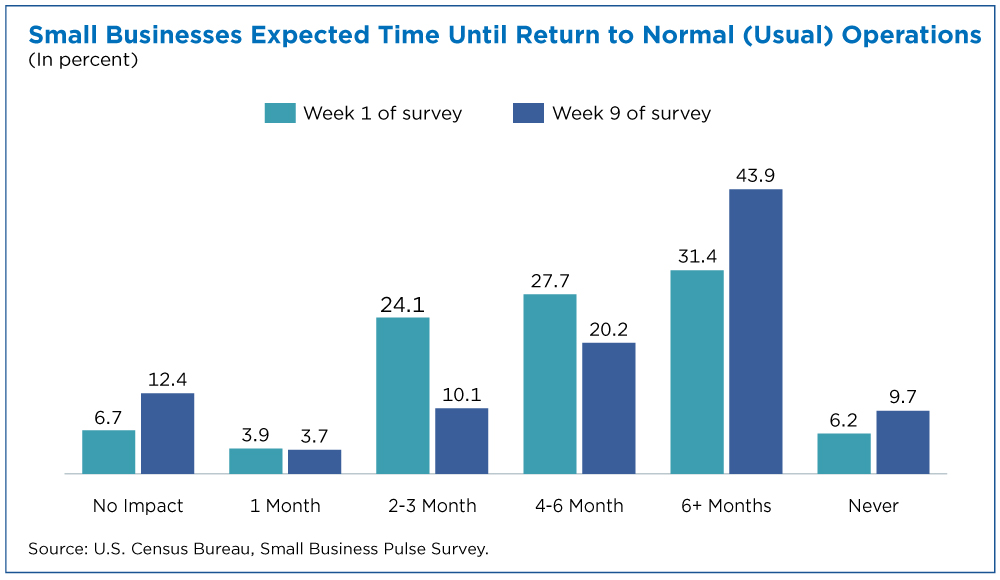
If you want to be an industrial engineer, you should have strong math skills as well as a background of physical science. These individuals may work in several sectors, including manufacturing and construction. They may work in offices or on the factory floor.
Industrial engineers design and implement manufacturing processes to increase efficiency. They also develop quality control procedures. They may also be responsible for creating manufacturing standards and training staff. People who want to become industrial engineers need to be open-minded and willing work with others. They should have a passion for improving efficiency and streamlining processes. They should have great communication and leadership skills.
Industrial engineers design cost analysis systems. They also create systems that make robots more efficient. They also analyze data to determine whether processes are effective or not. They may also develop manufacturing standards and design standards, and they will be responsible for ensuring that processes meet safety standards. They will develop procedures for equipment, inventory control, and create documentation. They might present their plans in written reports or oral presentations.
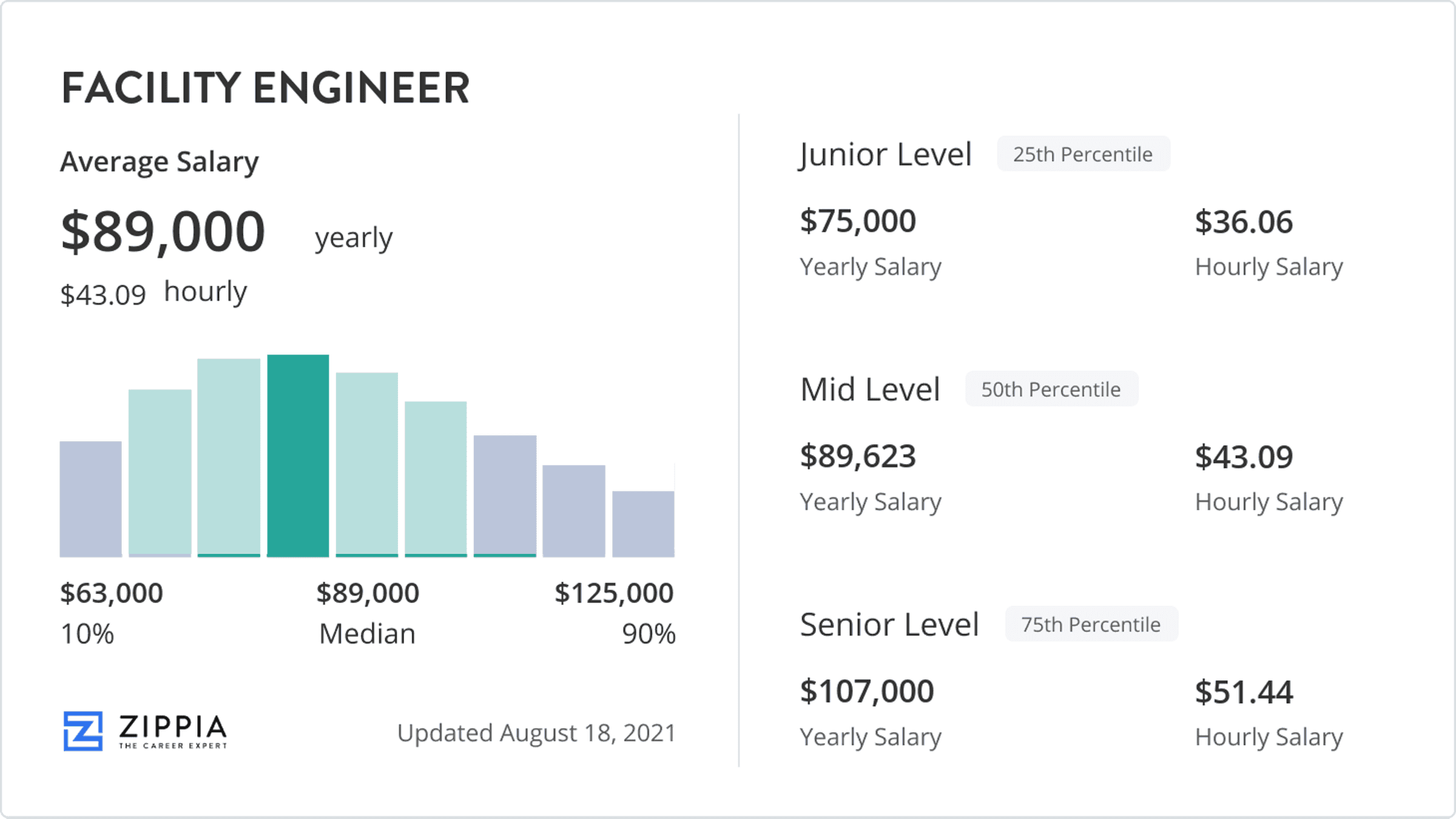
Industrial engineers can work in factories, offices, or warehouses. They may also travel to their clients' sites. They may have to work in cramped and noisy environments. They might also require protective safety clothing. Sometimes they might have to work for longer hours than usual to meet production deadlines.
The industrial engineer is responsible for the design and implementation process, assuring that it runs efficiently and producing high-quality products. They may also be responsible for solving production problems. Some industrial engineers can also start manufacturing businesses. They might have to train employees and ensure they know how the work. They may also have the responsibility of ensuring that raw materials meet certain quality standards before they can be used in manufacturing.
Industrial engineers are part of other departments that create integrated systems to manage industrial production. They may also specialize within a specific engineering field. They may be required to work in an unorganized or noisy environment. They might need to travel to construction sites or warehouses to collect data. Sometimes, they will have to collaborate with other professionals in order to solve manufacturing problems.
They can move up the ladder by gaining experience or education. They might open their own consultancy firms or become technical specialists in a particular field. They might also be skilled in facility planning or quality control. They could also be responsible in designing production layouts. They might also be responsible for creating wage and salary administration programs. They could also be responsible for scheduling deliveries according to production forecasts and storage and handling facilities. They can also travel to other areas and complete administrative tasks. They can also supervise technicians.
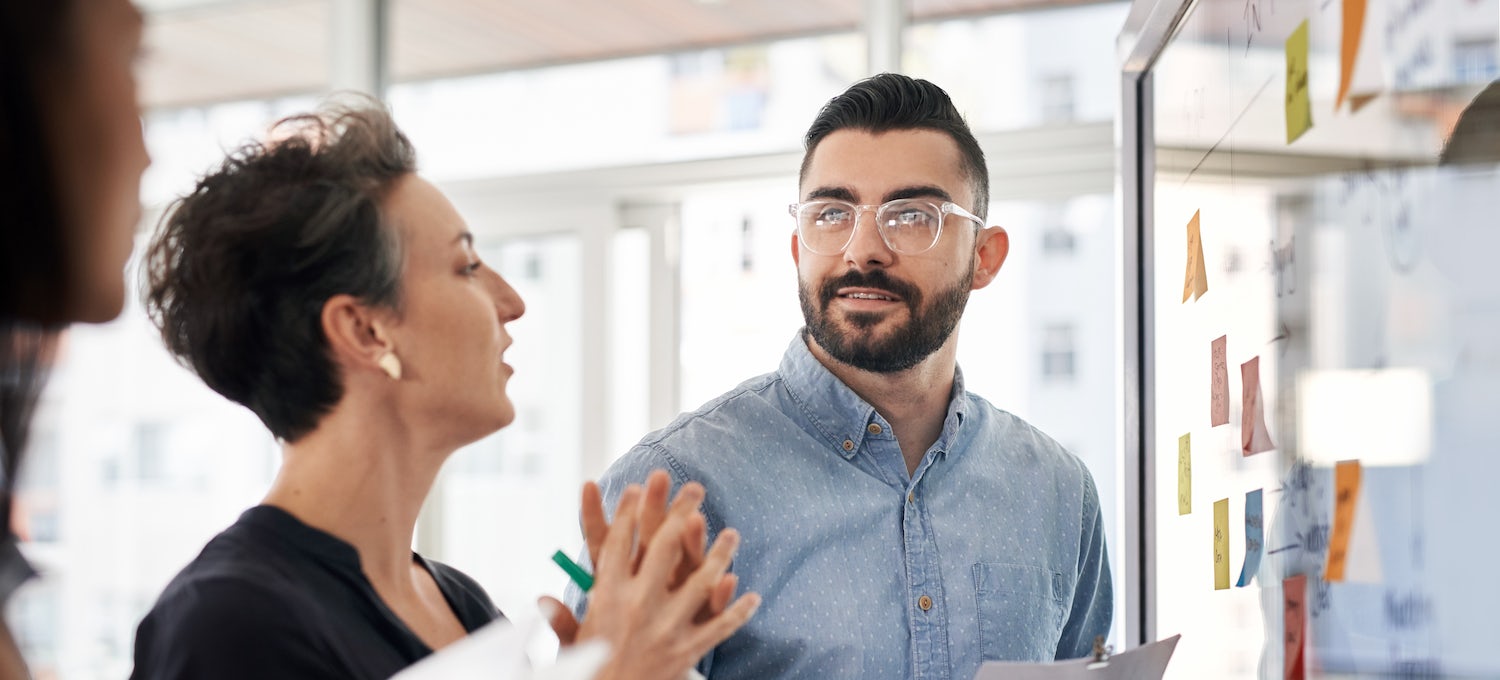
An industrial engineer may work for a company, or as a consultant. The company's requirements may dictate that they work an average 40-hour week. They may also be required to work for more hours in a consultancy service, if they are providing technical assistance for a business.
FAQ
What are manufacturing and logistic?
Manufacturing refers the process of producing goods from raw materials through machines and processes. Logistics covers all aspects involved in managing supply chains, including procurement and production planning. Manufacturing and logistics are often considered together as a broader term that encompasses both the process of creating products and delivering them to customers.
What is the job of a logistics manger?
Logistics managers ensure that goods arrive on time and are unharmed. This is achieved by using their knowledge and experience with the products of the company. He/she should make sure that enough stock is on hand to meet the demands.
What does it mean to be a manufacturer?
Manufacturing Industries refers to businesses that manufacture products. These products are sold to consumers. This is accomplished by using a variety of processes, including production, distribution and retailing. They create goods from raw materials, using machines and various other equipment. This includes all types manufactured goods such as clothing, building materials, furniture, electronics, tools and machinery.
What is the importance of logistics in manufacturing?
Logistics are an integral part any business. They enable you to achieve outstanding results by helping manage product flow from raw materials through to finished goods.
Logistics plays a significant role in reducing cost and increasing efficiency.
What are the requirements to start a logistics business?
A successful logistics business requires a lot more than just knowledge. Good communication skills are essential to effectively communicate with your suppliers and clients. You will need to know how to interpret data and draw conclusions. You must be able to work well under pressure and handle stressful situations. To increase efficiency and creativity, you need to be creative. You will need strong leadership skills to motivate and direct your team members towards achieving their organizational goals.
It is also important to be efficient and well organized in order meet deadlines.
What does warehouse refer to?
A warehouse is a place where goods are stored until they are sold. You can have it indoors or outdoors. It could be one or both.
What is production plan?
Production planning is the process of creating a plan that covers all aspects of production. This includes scheduling, budgeting and crew, location, equipment, props, and more. This document ensures that everything is prepared and available when you are ready for shooting. This document should include information about how to achieve the best results on-set. This includes location information, crew details, equipment specifications, and casting lists.
The first step is to outline what you want to film. You may have already decided where you would like to shoot, or maybe there are specific locations or sets that you want to use. Once you have identified the scenes and locations, you can start to determine which elements are required for each scene. You might decide you need a car, but not sure what make or model. If this is the case, you might start searching online for car models and then narrow your options by selecting from different makes.
Once you have found the right vehicle, you can think about adding accessories. Are you looking for people to sit in the front seats? Or perhaps you need someone walking around the back of the car? Perhaps you would like to change the interior colour from black to white. These questions will help you determine the exact look and feel of your car. The type of shots that you are looking for is another thing to consider. What type of shots will you choose? Maybe you want to show the engine and the steering wheel. This will allow you to determine the type of car you want.
Once you have determined all of the above, you can move on to creating a schedule. You can create a schedule that will outline when you must start and finish your shoots. Each day will include the time when you need to arrive at the location, when you need to leave and when you need to return home. So everyone is clear about what they need to do. If you need to hire extra staff, you can make sure you book them in advance. There is no point in hiring someone who won't turn up because you didn't let him know.
Your schedule will also have to be adjusted to reflect the number of days required to film. Some projects may only take a couple of days, while others could last for weeks. When creating your schedule, be aware of whether you need more shots per day. Multiple takes at the same place will result in higher costs and longer completion times. It's better to be safe than sorry and shoot less takes if you're not certain whether you need more takes.
Budgeting is another important aspect of production planning. You will be able to manage your resources if you have a realistic budget. You can always lower the budget if you encounter unexpected problems. It is important to not overestimate how much you will spend. If you underestimate how much something costs, you'll have less money to pay for other items.
Production planning is a very detailed process, but once you understand how everything works together, it becomes easier to plan future projects.
Statistics
- You can multiply the result by 100 to get the total percent of monthly overhead. (investopedia.com)
- Job #1 is delivering the ordered product according to specifications: color, size, brand, and quantity. (netsuite.com)
- [54][55] These are the top 50 countries by the total value of manufacturing output in US dollars for its noted year according to World Bank.[56] (en.wikipedia.org)
- In 2021, an estimated 12.1 million Americans work in the manufacturing sector.6 (investopedia.com)
- (2:04) MTO is a production technique wherein products are customized according to customer specifications, and production only starts after an order is received. (oracle.com)
External Links
How To
How to Use Lean Manufacturing in the Production of Goods
Lean manufacturing (or lean manufacturing) is a style of management that aims to increase efficiency, reduce waste and improve performance through continuous improvement. It was developed in Japan during the 1970s and 1980s by Taiichi Ohno, who received the Toyota Production System (TPS) award from TPS founder Kanji Toyoda. The first book published on lean manufacturing was titled "The Machine That Changed the World" written by Michael L. Watkins and published in 1990.
Lean manufacturing, often described as a set and practice of principles, is aimed at improving the quality, speed, cost, and efficiency of products, services, and other activities. It emphasizes the elimination and minimization of waste in the value stream. The five-steps of Lean Manufacturing are just-in time (JIT), zero defect and total productive maintenance (TPM), as well as 5S. Lean manufacturing eliminates non-value-added tasks like inspection, rework, waiting.
Lean manufacturing can help companies improve their product quality and reduce costs. Additionally, it helps them achieve their goals more quickly and reduces employee turnover. Lean Manufacturing is one of the most efficient ways to manage the entire value chains, including suppliers and customers as well distributors and retailers. Many industries worldwide use lean manufacturing. For example, Toyota's philosophy underpins its success in automobiles, electronics, appliances, healthcare, chemical engineering, aerospace, paper, food, etc.
Lean manufacturing is based on five principles:
-
Define Value - Identify the value your business adds to society and what makes you different from competitors.
-
Reduce waste - Get rid of any activity that does not add value to the supply chain.
-
Create Flow - Ensure work moves smoothly through the process without interruption.
-
Standardize and Simplify – Make processes as consistent, repeatable, and as simple as possible.
-
Build Relationships- Develop personal relationships with both internal as well as external stakeholders.
Lean manufacturing, although not new, has seen renewed interest in the economic sector since 2008. To increase their competitiveness, many businesses have turned to lean manufacturing. In fact, some economists believe that lean manufacturing will be an important factor in economic recovery.
With many benefits, lean manufacturing is becoming more common in the automotive industry. These include improved customer satisfaction, reduced inventory levels, lower operating costs, increased productivity, and better overall safety.
Lean manufacturing can be applied to almost every aspect of an organization. Lean manufacturing is most useful in the production sector of an organisation because it ensures that each step in the value-chain is efficient and productive.
There are three types of lean manufacturing.
-
Just-in-Time Manufacturing (JIT): This type of lean manufacturing is commonly referred to as "pull systems." JIT is a process in which components can be assembled at the point they are needed, instead of being made ahead of time. This approach reduces lead time, increases availability and reduces inventory.
-
Zero Defects Manufacturing (ZDM),: ZDM is a system that ensures no defective units are left the manufacturing facility. If a part is required to be repaired on the assembly line, it should not be scrapped. This applies to finished products, which may need minor repairs before they are shipped.
-
Continuous Improvement (CI): CI aims to improve the efficiency of operations by continuously identifying problems and making changes in order to eliminate or minimize waste. Continuous Improvement (CI) involves continuous improvement in processes, people, tools, and infrastructure.