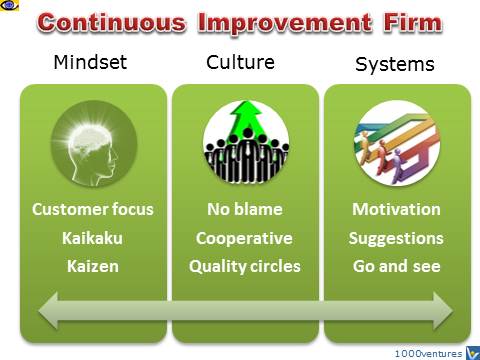
Over the years, global supplies chains have been subject to many changes. They have changed from being a problem for industrial purposes to becoming a serious economic risk. It is important to stay up-to-date with the latest developments. Global supply chain systems are complex, interdependent systems.
Global value chains contain a combination of capital, intangibles, flows, and other resources. They reflect economies of size, long-standing relationships, and specialization. Some value chains have high capital requirements, but others are more regionalized.
Global supply chains have become more complex, dynamic and multidimensional. They are vital for the functioning of economies and global trade. They are also vulnerable for disruptions. These disruptions can either be short-term, or more permanent. It is essential to have a diverse, flexible, and resilient supply network in order to avoid these disruptions. This requires a comprehensive approach which includes structural reforms and prudent risk management. The first step to building a supply system that can withstand the next storm, is identifying the biggest problems and evaluating the solutions.
Additionally to considering the risks from supply chain disruptions companies need to consider the associated risks with manufacturing, energy, materials. They should also simulate extreme supply/demand disruptions in an effort to gauge their impact. They need to review their critical materials inventories and ensure that they have enough supply to meet any foreseeable demand. Developing a resilient supply chain requires a strategic approach, which may include reprioritizing production, shifting manufacturing to more flexible locations, improving supply chain technology and implementing guaranteed sources of supply.
The COVID-19 pandemic caused significant disruptions to global supply chains. While some countries placed tariffs on one another, others imposed penalties against the other. These tariffs or sanctions have created trade frictions that made it harder for the United States, China, and other countries to export certain products. These disruptions have caused price inflation. They have made companies more aware about the fragility and potential dangers of their supply chain and forced them to rethink their design and implementation.
The COVID-19 epidemic caused severe disruption in global supply chain operations, but the effects of the pandemic are still being felt. For example, disruptions to supply chains caused by the Suez Canal's blockage have been lasting up to six month. The freight costs have also increased dramatically as a result. The UK has seen an increase in inflation of 9% annually.
It's hard to ignore the fact that the United States and China are facing a trade war. Supply chain managers need to question why they rely so heavily on outsourced networks. They should also consider the risks associated with labor shortages associated with economic shocks. They should also think about the potential benefits of cross border finance and regulation which could expand global integration.
Despite the turbulence, the world remains a deeply interconnected place. Global integration can be realized when firms take a holistic approach to their supply chain.
FAQ
How can manufacturing efficiency improved?
First, we need to identify which factors are most critical in affecting production times. Next, we must find ways to improve those factors. You can start by identifying the most important factors that impact production time. Once you've identified them, try to find solutions for each of those factors.
Why is logistics important in manufacturing
Logistics are essential to any business. Logistics can help you achieve amazing results by helping to manage product flow from raw materials to finished products.
Logistics are also important in reducing costs and improving efficiency.
How does manufacturing avoid bottlenecks in production?
You can avoid bottlenecks in production by making sure that everything runs smoothly throughout the production cycle, from the moment you receive an order to the moment the product is shipped.
This includes planning for both capacity requirements and quality control measures.
This can be done by using continuous improvement techniques, such as Six Sigma.
Six Sigma is a management method that helps to improve quality and reduce waste.
It's all about eliminating variation and creating consistency in work.
Statistics
- In the United States, for example, manufacturing makes up 15% of the economic output. (twi-global.com)
- [54][55] These are the top 50 countries by the total value of manufacturing output in US dollars for its noted year according to World Bank.[56] (en.wikipedia.org)
- According to a Statista study, U.S. businesses spent $1.63 trillion on logistics in 2019, moving goods from origin to end user through various supply chain network segments. (netsuite.com)
- Job #1 is delivering the ordered product according to specifications: color, size, brand, and quantity. (netsuite.com)
- You can multiply the result by 100 to get the total percent of monthly overhead. (investopedia.com)
External Links
How To
How to Use Lean Manufacturing for the Production of Goods
Lean manufacturing (or lean manufacturing) is a style of management that aims to increase efficiency, reduce waste and improve performance through continuous improvement. It was developed in Japan during the 1970s and 1980s by Taiichi Ohno, who received the Toyota Production System (TPS) award from TPS founder Kanji Toyoda. Michael L. Watkins published the "The Machine That Changed the World", the first book about lean manufacturing. It was published in 1990.
Lean manufacturing is often defined as a set of principles used to improve the quality, speed, and cost of products and services. It is about eliminating defects and waste from all stages of the value stream. The five-steps of Lean Manufacturing are just-in time (JIT), zero defect and total productive maintenance (TPM), as well as 5S. Lean manufacturing emphasizes reducing non-value-added activities like inspection, rework and waiting.
Lean manufacturing is a way for companies to achieve their goals faster, improve product quality, and lower costs. Lean manufacturing is a great way to manage the entire value chain including customers, suppliers, distributors and retailers as well as employees. Lean manufacturing is widely practiced in many industries around the world. Toyota's philosophy is a great example of this. It has helped to create success in automobiles as well electronics, appliances and healthcare.
Five fundamental principles underlie lean manufacturing.
-
Define Value- Identify the added value your company brings to society. What makes you stand out from your competitors?
-
Reduce Waste – Eliminate all activities that don't add value throughout the supply chain.
-
Create Flow: Ensure that the work process flows without interruptions.
-
Standardize and simplify – Make processes as repeatable and consistent as possible.
-
Build relationships - Develop and maintain personal relationships with both your internal and external stakeholders.
Lean manufacturing is not a new concept, but it has been gaining popularity over the last few years due to a renewed interest in the economy following the global financial crisis of 2008. To increase their competitiveness, many businesses have turned to lean manufacturing. According to some economists, lean manufacturing could be a significant factor in the economic recovery.
Lean manufacturing is now becoming a common practice in the automotive industry, with many benefits. These include improved customer satisfaction, reduced inventory levels, lower operating costs, increased productivity, and better overall safety.
You can apply Lean Manufacturing to virtually any aspect of your organization. This is because it ensures efficiency and effectiveness in all stages of the value chain.
There are three main types:
-
Just-in-Time Manufacturing: Also known as "pull systems", this type of lean manufacturing uses just-in-time manufacturing (JIT). JIT means that components are assembled at the time of use and not manufactured in advance. This strategy aims to decrease lead times, increase availability of parts and reduce inventory.
-
Zero Defects Manufacturing (ZDM): ZDM focuses on ensuring that no defective units leave the manufacturing facility. If a part is required to be repaired on the assembly line, it should not be scrapped. This also applies to finished products that need minor repairs before being shipped.
-
Continuous Improvement (CI: Continuous improvement aims to increase the efficiency of operations by constantly identifying and making improvements to reduce or eliminate waste. It involves continuous improvement of processes, people, and tools.