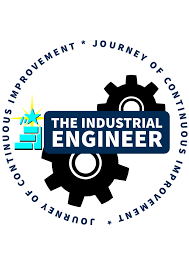
A planning engineer (also known as a building planner) is responsible for the planning and scheduling of the construction process. They plan every aspect of the project, such as determining when it will be completed and finding the correct materials. They will also decide the best order for each stage in a project.
Career Plans for a Planning Engineer
If you want to pursue a career in planning engineering, it is important that you learn about the position and what skills are required. You will need to have a bachelor's in engineering, or a field related, and several years of relevant experience. You may also be required to obtain certification from an organization in the industry.
How to become a planning engineer
A bachelor's or master's degree is required to work in this field. Additionally, you will need good computer skills as well as knowledge of construction techniques and sites. You must be able to perform quality control on your projects, manage a team, and ensure that projects are completed on time and on budget.
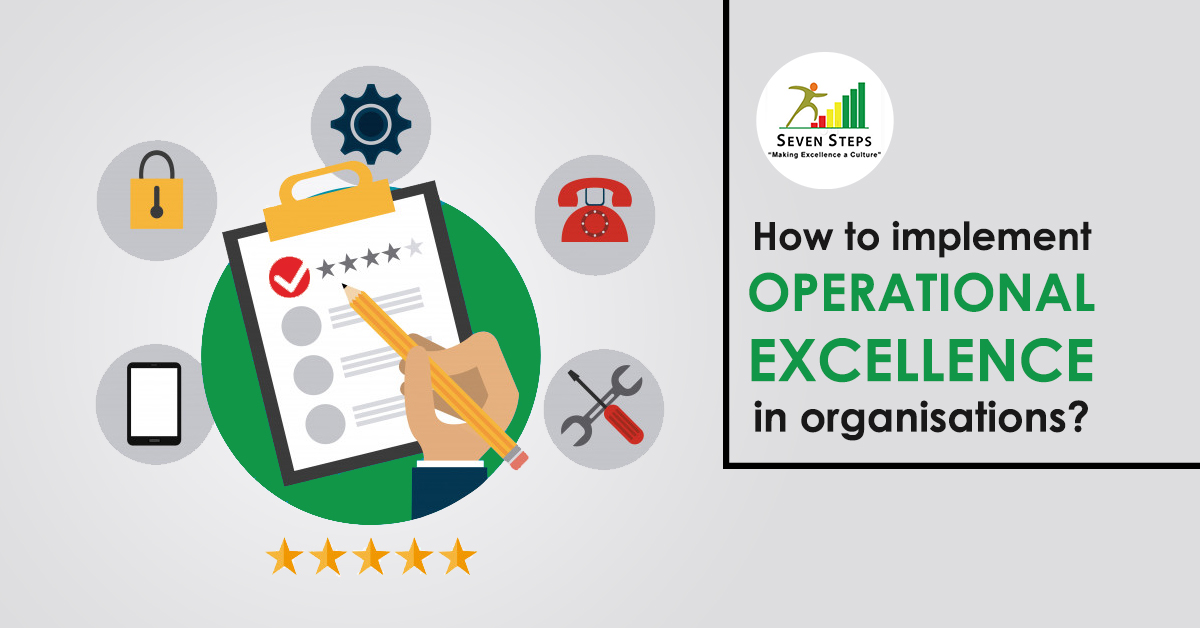
What to Look For in a Planning Engineering
When reviewing your resume, it is important to know what the hiring manager wants. Some of the most common skills that you should include are good organizational and communication skills, the ability to meet deadlines, and experience with construction sites.
What to Expect in a Planning Engineer Role
Planning engineers work in offices and use computers extensively. However, they may need to travel to various construction sites to ensure that all work is done properly and on time. Some jobs require workers to be present on the site of construction.
What to Expect in a Career as a Planning Engineer
As you gain experience, your career will usually begin with an entry level position. You could become an operations or project manager. Some planning engineers choose to pursue careers in sales or marketing with an engineering firm.
What can you expect in your professional life as a planning engineer
The average planning engineer's salary is around $150,000. However, it may vary based on their experience and company size and industry. Many planning engineers earn bonuses or other incentives for meeting deadlines and completing projects.
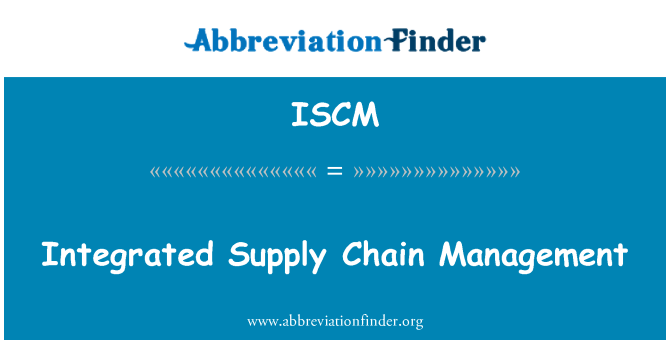
How to Find a Planning Engineering Job
A planning engineer's job is to design and plan all aspects of the project, starting from the beginning. They oversee a team that includes other engineers and designers who create plans to achieve business goals. They create long-term strategies to help their companies achieve their goals, like identifying new technologies or deciding where to invest.
FAQ
How can I learn about manufacturing?
You can learn the most about manufacturing by getting involved in it. You can also read educational videos or take classes if this isn't possible.
Can we automate some parts of manufacturing?
Yes! Since ancient times, automation has been in existence. The Egyptians invented the wheel thousands of years ago. Robots are now used to assist us in assembly lines.
Actually, robotics can be used in manufacturing for many purposes. These include:
-
Line robots
-
Robot welding
-
Robot painting
-
Robotics inspection
-
Robots that create products
There are many other examples of how manufacturing could benefit from automation. 3D printing is a way to make custom products quickly and without waiting weeks or months for them to be manufactured.
Why automate your warehouse?
Modern warehouses have become more dependent on automation. E-commerce has brought increased demand for more efficient and quicker delivery times.
Warehouses have to be flexible to meet changing requirements. Technology investment is necessary to enable warehouses to respond quickly to changing demands. Automation warehouses can bring many benefits. These are just a few reasons to invest in automation.
-
Increases throughput/productivity
-
Reduces errors
-
Increases accuracy
-
Safety Boosts
-
Eliminates bottlenecks
-
Allows companies to scale more easily
-
Makes workers more efficient
-
Provides visibility into everything that happens in the warehouse
-
Enhances customer experience
-
Improves employee satisfaction
-
Reduces downtime and improves uptime
-
This ensures that quality products are delivered promptly
-
Removes human error
-
Assure compliance with regulations
Do we need to know about Manufacturing Processes before learning about Logistics?
No. It doesn't matter if you don't know anything about manufacturing before you learn about logistics. Understanding the manufacturing process will allow you to better understand logistics.
What kind of jobs are there in logistics?
Logistics can offer many different jobs. Some examples are:
-
Warehouse workers - They load trucks and pallets.
-
Transportation drivers – They drive trucks or trailers to transport goods and perform pick-ups.
-
Freight handlers: They sort and package freight in warehouses.
-
Inventory managers: They are responsible for the inventory and management of warehouses.
-
Sales reps - They sell products and services to customers.
-
Logistics coordinators - They plan and organize logistics operations.
-
Purchasing agents – They buy goods or services necessary to run a company.
-
Customer service representatives - Answer calls and email from customers.
-
Shipping clerks: They process shipping requests and issue bills.
-
Order fillers - They fill orders based on what is ordered and shipped.
-
Quality control inspectors - They check incoming and outgoing products for defects.
-
Other - Logistics has many other job opportunities, including transportation supervisors, logistics specialists, and cargo specialists.
What are the four types of manufacturing?
Manufacturing refers to the transformation of raw materials into useful products by using machines and processes. It involves many different activities such as designing, building, testing, packaging, shipping, selling, servicing, etc.
Statistics
- According to the United Nations Industrial Development Organization (UNIDO), China is the top manufacturer worldwide by 2019 output, producing 28.7% of the total global manufacturing output, followed by the United States, Japan, Germany, and India.[52][53] (en.wikipedia.org)
- (2:04) MTO is a production technique wherein products are customized according to customer specifications, and production only starts after an order is received. (oracle.com)
- It's estimated that 10.8% of the U.S. GDP in 2020 was contributed to manufacturing. (investopedia.com)
- You can multiply the result by 100 to get the total percent of monthly overhead. (investopedia.com)
- In 2021, an estimated 12.1 million Americans work in the manufacturing sector.6 (investopedia.com)
External Links
How To
Six Sigma: How to Use it in Manufacturing
Six Sigma can be described as "the use of statistical process control (SPC), techniques to achieve continuous improvement." It was developed by Motorola's Quality Improvement Department at their plant in Tokyo, Japan, in 1986. Six Sigma's core idea is to improve the quality of processes by standardizing and eliminating defects. In recent years, many companies have adopted this method because they believe there is no such thing as perfect products or services. Six Sigma's main objective is to reduce variations from the production average. If you take a sample and compare it with the average, you will be able to determine how much of the production process is different from the norm. If you notice a large deviation, then it is time to fix it.
Understanding how variability works in your company is the first step to Six Sigma. Once you understand that, it is time to identify the sources of variation. It is important to identify whether the variations are random or systemic. Random variations occur when people make mistakes; systematic ones are caused by factors outside the process itself. Random variations would include, for example, the failure of some widgets to fall from the assembly line. If however, you notice that each time you assemble a widget it falls apart in exactly the same spot, that is a problem.
Once you've identified the problem areas you need to find solutions. It might mean changing the way you do business or redesigning it entirely. Test them again once you've implemented the changes. If they didn't work, then you'll need to go back to the drawing board and come up with another plan.