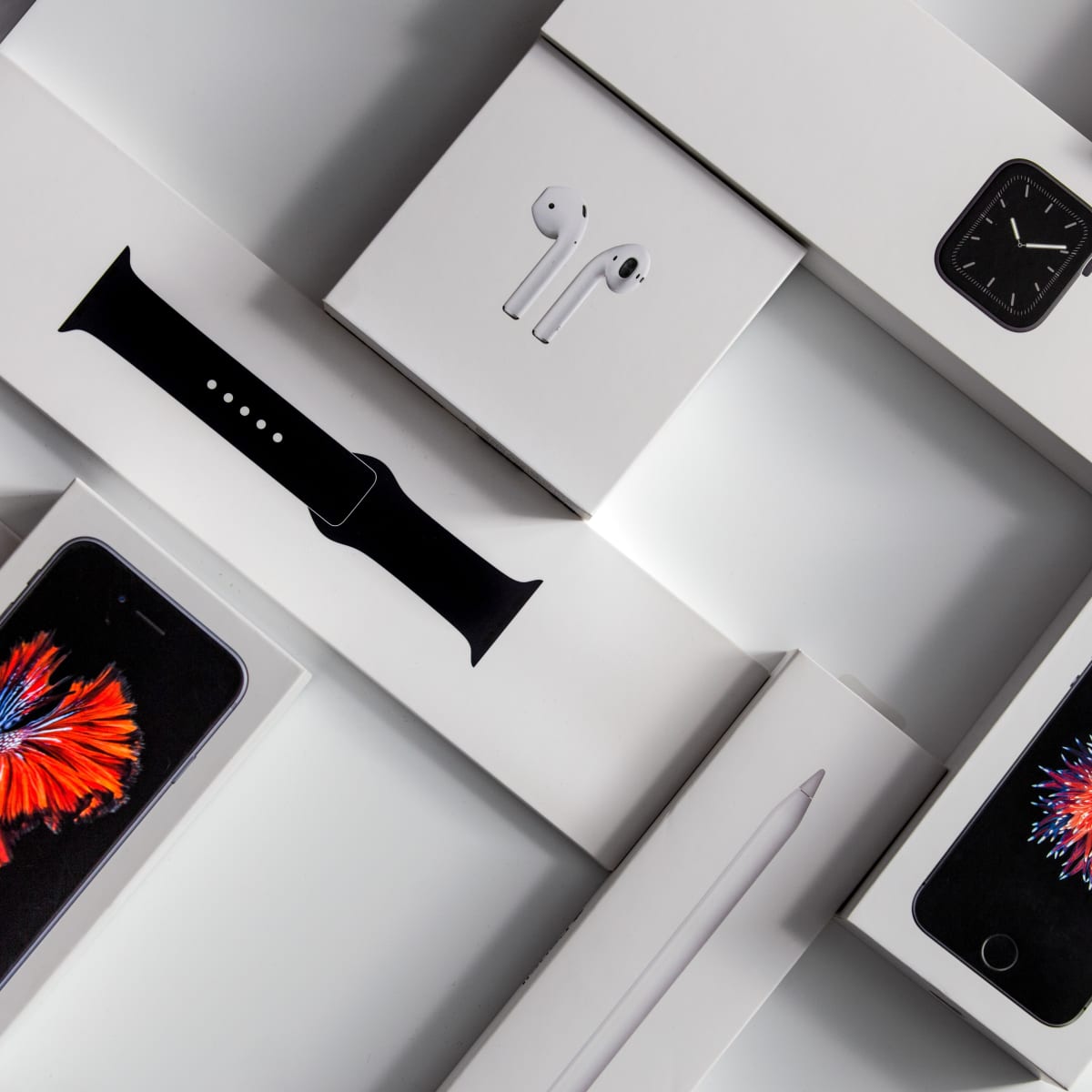
The facts about manufacturing will help you to understand the importance of manufacturing in our country's economy. The industry is responsible for 30% national energy consumption, employs many people with no college degrees and earns a living wage. Manufacturing also creates jobs for workers with low incomes. It is an important part the second sector of the economy.
U.S. manufacturers contribute $2.17 trillion to their economy
American society has a strong manufacturing sector. It not only contributes to the economy, but also fuels innovation and creativity. The United States has strong manufacturing sectors, with over 12 million employees. Many manufacturing facilities are now desirable places to be employed, as new technology is being applied to improve the quality and safety of products.
The US is the ninth-largest economy in the world, with more than $2.17 trillion being contributed by manufacturing companies. The industry has been experiencing ups and downs as job losses, offshoring, and other economic factors have changed the way manufacturing businesses operate. However, today manufacturing is a highly developed industry that has seen innovations in robotics automation.
It consumes 30% national energy
The industrial sector in the U.S. uses heat in a wide variety of processes, consuming one-third of the nation's delivered energy supply. Process heating applications account for 36 per cent of total energy consumption. This makes industrial heat a great opportunity to find renewable energy.
While solar and wind power usage has grown rapidly over recent years, this only accounts for a small proportion of the nation’s energy consumption. Coal, natural gas and oil accounted the bulk of our energy consumption for 2018.
It pays a living wages
Companies that offer a living wage to their employees are more attractive than their competitors and will attract more workers. This is a key way to improve morale, employee retention and job security as manufacturing suffers from declining exports and job losses. In the UK, around 45% of manufacturers are considering redundancies, making it all the more important for companies to invest in their workforces and boost employee retention rates.
In order to embed living wage benchmarks in pricing, companies can ask suppliers to use these. By doing so, companies ensure that their suppliers are receiving enough money to pay their workers a living wage. Additionally, these companies send a clear message to production-country governments that they are willing to pay a living wage without risking losing business.
It employs many workers with no college degree.
The manufacturing sector is one of the largest employers of workers without college degrees, but it's also the sector with the most unfilled positions. Because most jobs require advanced skills, fewer high school students are choosing manufacturing as their career. Since the mid-1990s, the percentage of manufacturing jobs held by workers without a college degree declined from more than 60% to less than 45%. In the next few years, workers with a college degree will overtake those with a high school diploma.
Manufacturing jobs might not have the glamour and high-tech industry appeal, but they are vital for many communities. More than 130 manufacturing businesses are located in Henderson County. Many of these companies aren't well-known, and they may be tucked away in out-of-the-way places where prospective employees may not know where to look.
It has seen a tremendous increase in its popularity over the past two decades.
The Midwest does not have the only opportunity for manufacturing growth. Over the past 20 decades, there have been two waves of American manufacturing employment. The first began in the 1980s when firms migrated to the region from New England, and the second started in the 1990s when foreign automotive firms arrived.
This growth is due to changes in consumer demand, and the economics behind production. Manufacturing is now shifting its focus from making physical products to delivering value at a lower cost. Consumers now have many options to customize their products thanks to new technologies. Added sensors and connectivity transform dumb products into smart products, allowing them to provide more value for the consumer. Manufacturers will have to rethink how they work in this new manufacturing environment.
FAQ
Are there any Manufacturing Processes that we should know before we can learn about Logistics?
No. It doesn't matter if you don't know anything about manufacturing before you learn about logistics. Understanding the manufacturing process will allow you to better understand logistics.
How can manufacturing prevent production bottlenecks?
To avoid production bottlenecks, ensure that all processes run smoothly from the moment you receive your order to the time the product ships.
This includes both quality control and capacity planning.
Continuous improvement techniques like Six Sigma are the best way to achieve this.
Six Sigma Management System is a method to increase quality and reduce waste throughout your organization.
It seeks to eliminate variation and create consistency in your work.
Why automate your warehouse?
Automation has become increasingly important in modern warehousing. E-commerce has increased the demand for quicker delivery times and more efficient processes.
Warehouses must adapt quickly to meet changing customer needs. To do so, they must invest heavily in technology. Automation of warehouses offers many benefits. Here are some benefits of investing in automation
-
Increases throughput/productivity
-
Reduces errors
-
Improves accuracy
-
Safety increases
-
Eliminates bottlenecks
-
Allows companies scale more easily
-
Workers are more productive
-
Gives you visibility into all that is happening in your warehouse
-
Enhances customer experience
-
Improves employee satisfaction
-
Reduces downtime and improves uptime
-
Ensures quality products are delivered on time
-
Removes human error
-
Assure compliance with regulations
What is the best way to learn about manufacturing?
Experience is the best way for you to learn about manufacturing. If that is not possible, you could always read books or view educational videos.
How does a production planner differ from a project manager?
The difference between a product planner and project manager is that a planer is typically the one who organizes and plans the entire project. A production planner, however, is mostly involved in the planning stages.
What are the products of logistics?
Logistics is the process of moving goods from one point to another.
They include all aspects associated with transport including packaging, loading transporting, unloading storage, warehousing inventory management customer service, distribution returns and recycling.
Logisticians ensure that products reach the right destination at the right moment and under safe conditions. Logisticians assist companies in managing their supply chains by providing information such as demand forecasts, stock levels and production schedules.
They keep track and monitor the transit of shipments, maintain quality standards, order replenishment and inventories, coordinate with suppliers, vendors, and provide support for sales and marketing.
Statistics
- (2:04) MTO is a production technique wherein products are customized according to customer specifications, and production only starts after an order is received. (oracle.com)
- According to the United Nations Industrial Development Organization (UNIDO), China is the top manufacturer worldwide by 2019 output, producing 28.7% of the total global manufacturing output, followed by the United States, Japan, Germany, and India.[52][53] (en.wikipedia.org)
- In the United States, for example, manufacturing makes up 15% of the economic output. (twi-global.com)
- [54][55] These are the top 50 countries by the total value of manufacturing output in US dollars for its noted year according to World Bank.[56] (en.wikipedia.org)
- It's estimated that 10.8% of the U.S. GDP in 2020 was contributed to manufacturing. (investopedia.com)
External Links
How To
How to use the Just-In Time Method in Production
Just-in-time (JIT) is a method that is used to reduce costs and maximize efficiency in business processes. It allows you to get the right amount resources at the right time. This means that you only pay for what you actually use. Frederick Taylor, a 1900s foreman, first coined the term. After observing how workers were paid overtime for late work, he realized that overtime was a common practice. He decided that workers would be more productive if they had enough time to complete their work before they started to work.
The idea behind JIT is that you should plan ahead and have everything ready so you don't waste money. The entire project should be looked at from start to finish. You need to ensure you have enough resources to tackle any issues that might arise. You'll be prepared to handle any potential problems if you know in advance. This will prevent you from spending extra money on unnecessary things.
There are many JIT methods.
-
Demand-driven JIT: You order the parts and materials you need for your project every other day. This will let you track the amount of material left over after you've used it. This will let you know how long it will be to produce more.
-
Inventory-based: This allows you to store the materials necessary for your projects in advance. This allows you to predict how much you can expect to sell.
-
Project-driven: This method allows you to set aside enough funds for your project. You will be able to purchase the right amount of materials if you know what you need.
-
Resource-based JIT: This type of JIT is most commonly used. Here you can allocate certain resources based purely on demand. You will, for example, assign more staff to deal with large orders. If there aren't many orders, you will assign fewer people.
-
Cost-based: This is the same as resource-based except that you don't care how many people there are but how much each one of them costs.
-
Price-based pricing: This is similar in concept to cost-based but instead you look at how much each worker costs, it looks at the overall company's price.
-
Material-based is an alternative to cost-based. Instead of looking at the total cost in the company, this method focuses on the average amount of raw materials that you consume.
-
Time-based JIT: A variation on resource-based JIT. Instead of focusing on how much each employee costs, you focus on how long it takes to complete the project.
-
Quality-based JIT: Another variation on resource-based JIT. Instead of thinking about how much each employee costs or how long it takes to manufacture something, you think about how good the quality of your product is.
-
Value-based JIT : This is the newest type of JIT. This is where you don't care about how the products perform or whether they meet customers' expectations. Instead, you're focused on how much value you add to the market.
-
Stock-based: This is an inventory-based method that focuses on the actual number of items being produced at any given time. This method is useful when you want to increase production while decreasing inventory.
-
Just-intime (JIT), planning is a combination JIT management and supply chain management. It refers to the process of scheduling the delivery of components as soon as they are ordered. This is important as it reduces lead time and increases throughput.