
If you're interested in a career as a maintenance engineer, you need to have the right qualifications. These certifications are required and what you can expect to earn. For people with a keen eye for details, the maintenance engineer position is an ideal fit. Maintenance engineers are responsible to maintain a building's infrastructure, and make sure it is operating at peak performance.
Qualifications for a career in maintenance engineering
You should consider these key points if you're looking for a job as a maintenance engineer. Although a high-school diploma will give you the necessary foundational skills, it is also possible to take a college course about engineering. Working experience and courses in chemistry, physics and math will prove to be valuable. A technical school might be an option, depending on your company's needs.
The maintenance engineer is responsible for the maintenance of machinery and equipment, as well as systems, infrastructures, and systems. Their job is keeping industrial machinery running as efficiently and safely as possible. They also manage the supply of spare part and supplies. Some jobs, especially those in manufacturing, require shift work. Depending on what type of work they do, maintenance engineers could move up to management positions or seek other opportunities in related fields. After they have gained experience, they may be able to start their own business.
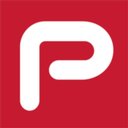
Maintenance engineers are paid between PS20,000 and PS25,000 in an average year. Salary ranges can vary depending on industry, size, and location. You can also become a maintenance engineer and move up to management roles, which require leadership skills. Chartered status may also help with career progression.
Certifications are required
As a maintenance engineer, you may be required to hold several certifications. These certifications could be specific to a particular system or pertain to handling hazardous materials. The International Maintenance Institute offers professional certification in several levels. These include certified maintenance technicians at lower levels, and maintenance managers at higher levels.
If you're interested in becoming a maintenance engineer, it's important to first consider your educational background. Most certification providers do not require specific educational qualifications. However, some recommend high school diplomas or GEDs. Employers and recruiters typically require this minimum requirement. However, you can also obtain a certification without a degree if you've had previous work experience in a similar industry.
Although a bachelor's degree does not necessarily mean you can become a maintenance engineer or vice versa, a degree in a relevant field will make you stand out among the rest. An engineering degree in mechanical engineering, electrical engineering or facilities management might be helpful. Even if an engineering degree is not required, it's possible to get work as a maintenance technician.
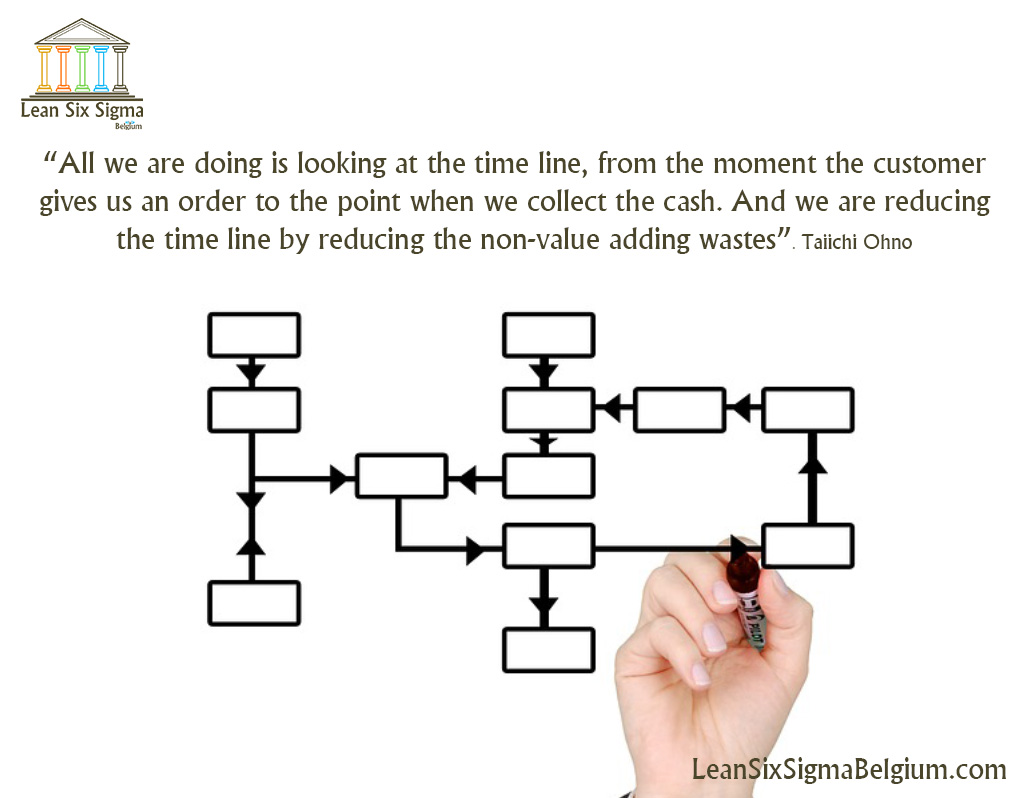
Salary
The Bureau of Labor Statistics cannot monitor the salary of maintenance technicians, but they do project that there will be job growth in similar fields. In general maintenance, engineers and mechanical technicians are expected to see eight percent growth, while construction management managers might see an 11 percent increase in their employment. If you are interested in a career as maintenance engineer, then you should look for entry-level jobs within industries that have high job growth.
Maintenance engineer salaries: The median 2008 salary for maintenance engineers stood at $88,570. The lowest 25 percent earned $48,270, while the top ten percent earned more than $110,310.
FAQ
How is a production manager different from a producer planner?
The difference between a product planner and project manager is that a planer is typically the one who organizes and plans the entire project. A production planner, however, is mostly involved in the planning stages.
What is the role of a manager in manufacturing?
A manufacturing manager has to ensure that all manufacturing processes work efficiently and effectively. They should be alert for any potential problems in the company and react accordingly.
They should also be able communicate with other departments, such as sales or marketing.
They must also keep up-to-date with the latest trends in their field and be able use this information to improve productivity and efficiency.
What is the responsibility of a production planner?
Production planners ensure that all project aspects are completed on time, within budget and within the scope. They also ensure the quality of the product and service meets the client's requirements.
What is the importance of automation in manufacturing?
Automation is essential for both manufacturers and service providers. It allows them to offer services faster and more efficiently. It reduces human errors and improves productivity, which in turn helps them lower their costs.
What does "warehouse" mean?
A warehouse is an area where goods are stored before being sold. You can have it indoors or outdoors. Sometimes, it can be both an indoor and outdoor space.
Statistics
- [54][55] These are the top 50 countries by the total value of manufacturing output in US dollars for its noted year according to World Bank.[56] (en.wikipedia.org)
- (2:04) MTO is a production technique wherein products are customized according to customer specifications, and production only starts after an order is received. (oracle.com)
- It's estimated that 10.8% of the U.S. GDP in 2020 was contributed to manufacturing. (investopedia.com)
- According to a Statista study, U.S. businesses spent $1.63 trillion on logistics in 2019, moving goods from origin to end user through various supply chain network segments. (netsuite.com)
- Many factories witnessed a 30% increase in output due to the shift to electric motors. (en.wikipedia.org)
External Links
How To
How to Use Just-In-Time Production
Just-intime (JIT), a method used to lower costs and improve efficiency in business processes, is called just-in-time. It's the process of obtaining the right amount and timing of resources when you need them. This means that you only pay for what you actually use. Frederick Taylor, a 1900s foreman, first coined the term. After observing how workers were paid overtime for late work, he realized that overtime was a common practice. He decided that workers would be more productive if they had enough time to complete their work before they started to work.
JIT is a way to plan ahead and make sure you don't waste any money. Look at your entire project, from start to end. Make sure you have enough resources in place to deal with any unexpected problems. You can anticipate problems and have enough equipment and people available to fix them. This way you won't be spending more on things that aren’t really needed.
There are several types of JIT techniques:
-
Demand-driven: This JIT is where you place regular orders for the parts/materials that are needed for your project. This will allow you to track how much material you have left over after using it. It will also allow you to predict how long it takes to produce more.
-
Inventory-based: This type allows you to stock the materials needed for your projects ahead of time. This allows you to forecast how much you will sell.
-
Project-driven: This is an approach where you set aside enough funds to cover the cost of your project. If you know the amount you require, you can buy the materials you need.
-
Resource-based: This is the most common form of JIT. Here you can allocate certain resources based purely on demand. You will, for example, assign more staff to deal with large orders. If you don't have many orders, you'll assign fewer people to handle the workload.
-
Cost-based : This is similar in concept to resource-based. But here, you aren't concerned about how many people your company has but how much each individual costs.
-
Price-based: This is very similar to cost-based, except that instead of looking at how much each individual worker costs, you look at the overall price of the company.
-
Material-based: This is very similar to cost-based but instead of looking at total costs of the company you are concerned with how many raw materials you use on an average.
-
Time-based JIT: This is another variant of resource-based JIT. Instead of focusing on how much each employee costs, you focus on how long it takes to complete the project.
-
Quality-based JIT - This is another form of resource-based JIT. Instead of focusing on the cost of each worker or how long it takes, think about how high quality your product is.
-
Value-based JIT is the newest form of JIT. In this case, you're not concerned with how well the products perform or whether they meet customer expectations. Instead, you are focused on adding value to the marketplace.
-
Stock-based: This inventory-based approach focuses on how many items are being produced at any one time. This method is useful when you want to increase production while decreasing inventory.
-
Just-intime planning (JIT), is a combination JIT/sales chain management. It is the process that schedules the delivery of components within a short time of their order. This is important as it reduces lead time and increases throughput.