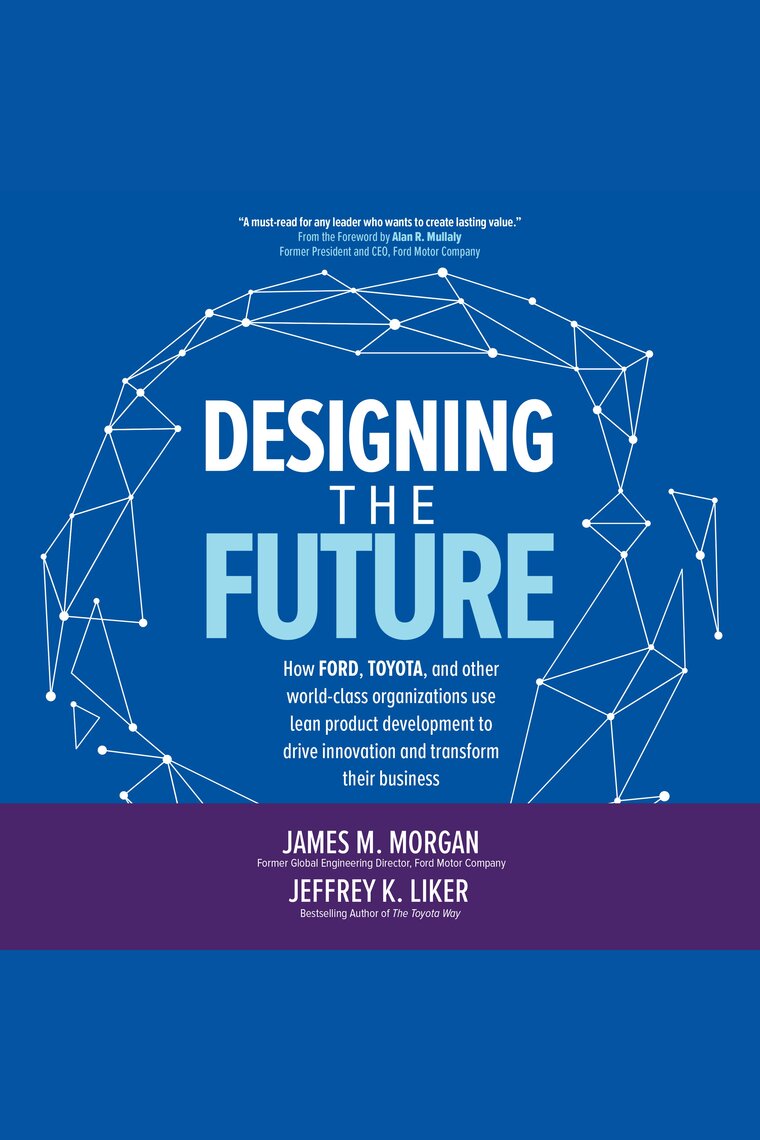
For your company to be able to attract the best and most sought-after talent at the right price and time, it is important that you have a strong talent supply chain. It is also crucial to gaining a competitive edge in the global marketplace.
It takes time to build a strong supply chain of talent. This involves continuous monitoring and updating of talent pools and needs. It also requires the collaboration of several groups of people, including HR, operations and IT leaders. It is crucial that everyone has a common business strategy so that the talent supply chain can be aligned with the organization’s goals.
One of the biggest challenges for HR leaders today is building diverse teams. Companies should reexamine their HR processes to make sure they can attract and retain the best talent. To do this, companies must embrace new technologies. The latest technological advances can reduce time spent recruiting. Your company can use data to find and optimize talent.
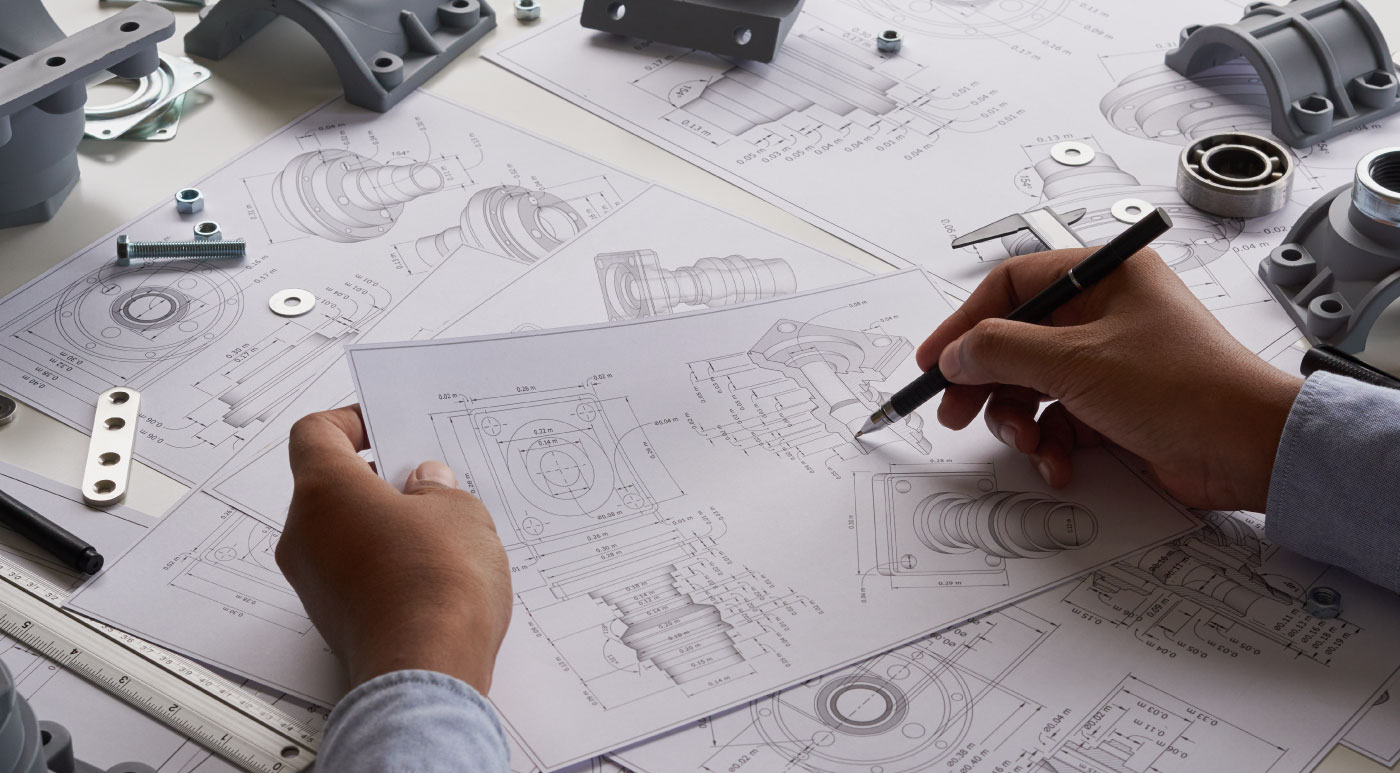
Identifying talent pools will be the first step. Once you have identified your talent pool, you can then use the data to assess your needs. By assessing your talent pools, you will be able to determine where you need to recruit and how to recruit effectively. You can also upskill your employees to round out your talent pipeline.
Your organization can track political and market trends by using existing data. These data can help you find talent strategies that match your business goals and provide insights. To maintain candidate profiles, you can also use existing data.
Using a talent supply chain can help your organization improve the quality of your workforce and increase its retention rate. You can also reduce the time and cost of your operations. The talent supply chain can help you reduce time and costs to hire talent and keep a stable, productive workforce.
The talent supply chain can be used for short-term or long-term solutions, such IT projects. You can also use a talent supply chain to help regions with limited employment opportunities. A global talent supply network can offer a greater pool of diverse candidates and cut down on the time required for talent retention and hiring.
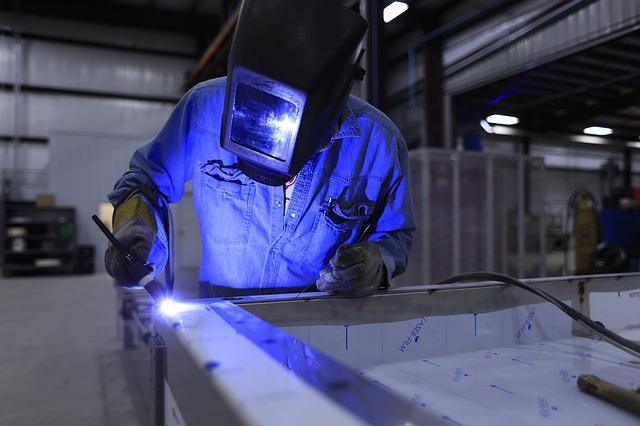
Human Resources and other functions have always worked together to secure talent. Today's companies must compete on the global market. This means that they must have access to the best and most sought-after talent from all sections of their workforce. To ensure that the company's goals are met, it is crucial to identify the skills and talents required by the organization.
Companies face new challenges as technology advances. Companies must adapt to these changes by reassessing their talent needs, acquiring new skills and becoming more agile. This new talent acquisition strategy is an important part of the future of many companies.
FAQ
What is it like to manage a logistics company?
It takes a lot of skills and knowledge to run a successful logistics business. Good communication skills are essential to effectively communicate with your suppliers and clients. It is important to be able to analyse data and draw conclusions. You must be able and able to handle stress situations and work under pressure. In order to innovate and create new ways to improve efficiency, creativity is essential. You must be a strong leader to motivate others and direct them to achieve organizational goals.
It is important to be organized and efficient in order to meet tight deadlines.
What does "warehouse" mean?
A warehouse or storage facility is where goods are stored before they are sold. It can be indoors or out. Sometimes, it can be both an indoor and outdoor space.
Is automation important for manufacturing?
Not only are service providers and manufacturers important, but so is automation. It allows them to offer services faster and more efficiently. It also helps to reduce costs and improve productivity.
What are the 4 types of manufacturing?
Manufacturing refers to the transformation of raw materials into useful products by using machines and processes. Manufacturing involves many activities, including designing, building, testing and packaging, shipping, selling, service, and so on.
Statistics
- [54][55] These are the top 50 countries by the total value of manufacturing output in US dollars for its noted year according to World Bank.[56] (en.wikipedia.org)
- You can multiply the result by 100 to get the total percent of monthly overhead. (investopedia.com)
- In the United States, for example, manufacturing makes up 15% of the economic output. (twi-global.com)
- Many factories witnessed a 30% increase in output due to the shift to electric motors. (en.wikipedia.org)
- According to the United Nations Industrial Development Organization (UNIDO), China is the top manufacturer worldwide by 2019 output, producing 28.7% of the total global manufacturing output, followed by the United States, Japan, Germany, and India.[52][53] (en.wikipedia.org)
External Links
How To
How to use 5S to increase Productivity in Manufacturing
5S stands for "Sort", 'Set In Order", 'Standardize', & Separate>. The 5S methodology was developed at Toyota Motor Corporation in 1954. It assists companies in improving their work environments and achieving higher efficiency.
This method has the basic goal of standardizing production processes to make them repeatable. This means that tasks such as cleaning, sorting, storing, packing, and labeling are performed daily. Through these actions, workers can perform their jobs more efficiently because they know what to expect from them.
Implementing 5S involves five steps: Sort, Set in Order, Standardize Separate, Store, and Each step requires a different action, which increases efficiency. For example, when you sort things, you make them easy to find later. When items are ordered, they are put together. Once you have separated your inventory into groups and organized them, you will store these groups in easily accessible containers. Labeling your containers will ensure that everything is correctly labeled.
Employees will need to be more critical about their work. Employees must understand why they do certain tasks and decide if there's another way to accomplish them without relying on the old ways of doing things. They must learn new skills and techniques in order to implement the 5S system.
The 5S method increases efficiency and morale among employees. They are more motivated to achieve higher efficiency levels as they start to see improvement.