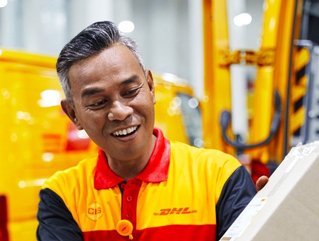
Industrial Engineers earn a good salary but there are many opportunities to advance in this field. You can move to a higher paying job, earn an advanced degree, or get managerial experience. These options can help increase your earning potential and give you the opportunity to get promoted. You might also be interested in an industrial engineer position at a research laboratory or design firm, where you can learn about the latest technology.
Job description
Industrial engineers can use their creativity and ingenuity to develop new production methods. They strive to reduce waste and improve efficiency. They must be able explain complex ideas to other members in the production department in a clear and concise fashion. Industrial engineers need to communicate well and be able listen to the concerns and needs of all stakeholders.
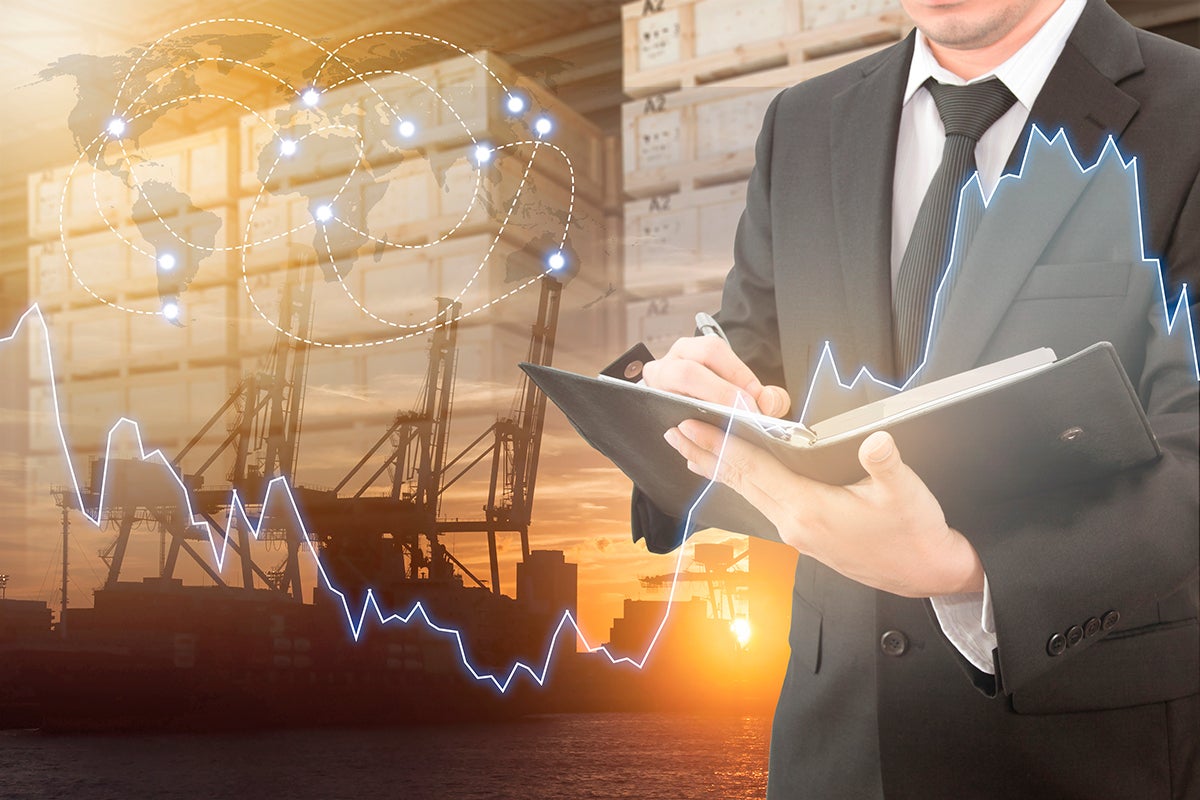
For industrial engineers, a Bachelor's Degree in Industrial Engineering or a related field is required. Employers prefer candidates who have some work experience. Students in this field may also find it beneficial to participate in cooperative education programs. Other degrees that industrial engineers might have, such as computer science or mathematics, may also be available.
Salary
NYC's industrial engineers earn an average annual salary $59,820. You can increase your income by moving to a company that pays higher wages, getting advanced degrees, and gaining additional experience. You can also improve your earning potential by having managerial experience. It can be hard to find an industrial engineer job in NYC with a competitive salary.
There are many factors that affect the salary of industrial engineers in NYC. A senior industrial engineer earns an average of $145,000. While entry-level engineers can earn $82,657. The average bonus for industrial engineers is $3.939.
Education is required
Industrial engineers are multi-disciplinary professionals who design and implement new production processes to increase efficiency. They are able to use logic and creativity in solving complex problems. They work in many industries including healthcare, finance and risk management. A bachelor's degree in a STEM area is required. Industrial engineers should have experience, in addition to meeting the educational requirements.
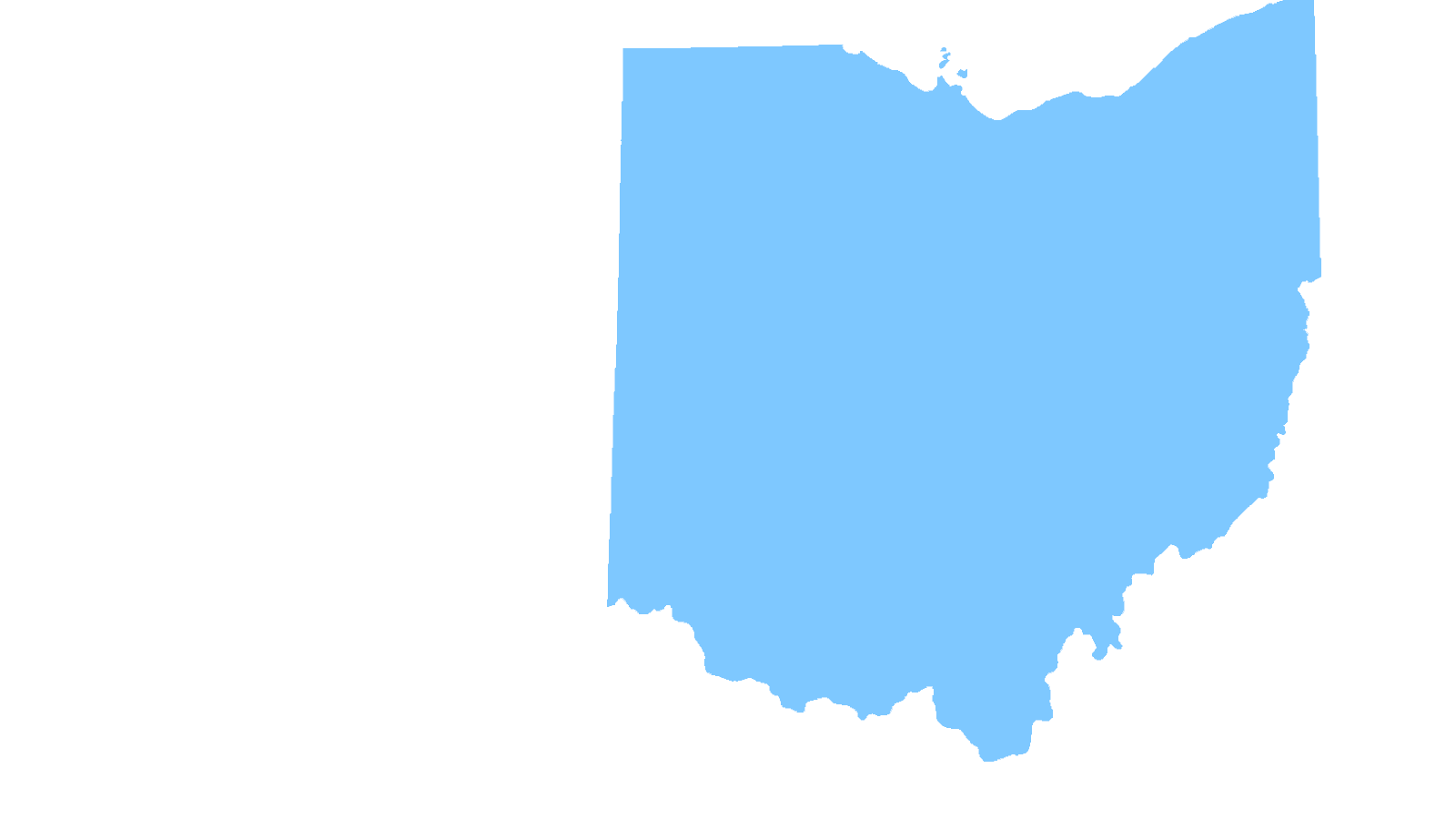
There is a demand for industrial engineering professionals across industries. The industry's job growth is expected to increase by 14% over 10 years. This may give them an edge over other job seekers due to their education and experiences. They should also have a broad range of skills and knowledge in order to manage production, analyze supply chain and educate workers on new policies.
FAQ
What are the 4 types of manufacturing?
Manufacturing is the process by which raw materials are transformed into useful products through machines and processes. Manufacturing involves many activities, including designing, building, testing and packaging, shipping, selling, service, and so on.
What makes a production planner different from a project manger?
The difference between a product planner and project manager is that a planer is typically the one who organizes and plans the entire project. A production planner, however, is mostly involved in the planning stages.
How important is automation in manufacturing?
Automation is essential for both manufacturers and service providers. It allows them provide faster and more efficient services. In addition, it helps them reduce costs by reducing human errors and improving productivity.
Statistics
- It's estimated that 10.8% of the U.S. GDP in 2020 was contributed to manufacturing. (investopedia.com)
- [54][55] These are the top 50 countries by the total value of manufacturing output in US dollars for its noted year according to World Bank.[56] (en.wikipedia.org)
- Many factories witnessed a 30% increase in output due to the shift to electric motors. (en.wikipedia.org)
- Job #1 is delivering the ordered product according to specifications: color, size, brand, and quantity. (netsuite.com)
- (2:04) MTO is a production technique wherein products are customized according to customer specifications, and production only starts after an order is received. (oracle.com)
External Links
How To
How to Use Six Sigma in Manufacturing
Six Sigma is defined as "the application of statistical process control (SPC) techniques to achieve continuous improvement." Motorola's Quality Improvement Department in Tokyo, Japan developed Six Sigma in 1986. Six Sigma is a method to improve quality through standardization and elimination of defects. Many companies have adopted Six Sigma in recent years because they believe that there are no perfect products and services. Six Sigma aims to reduce variation in the production's mean value. This means that if you take a sample of your product, then measure its performance against the average, you can find out what percentage of the time the process deviates from the norm. If the deviation is excessive, it's likely that something needs to be fixed.
Understanding how your business' variability is a key step towards Six Sigma implementation is the first. Once you've understood that, you'll want to identify sources of variation. These variations can also be classified as random or systematic. Random variations happen when people make errors; systematic variations are caused externally. For example, if you're making widgets, and some of them fall off the assembly line, those would be considered random variations. It would be considered a systematic problem if every widget that you build falls apart at the same location each time.
Once you've identified the problem areas you need to find solutions. That solution might involve changing the way you do things or redesigning the process altogether. Test them again once you've implemented the changes. If they don't work, you will need to go back to the drawing boards and create a new plan.