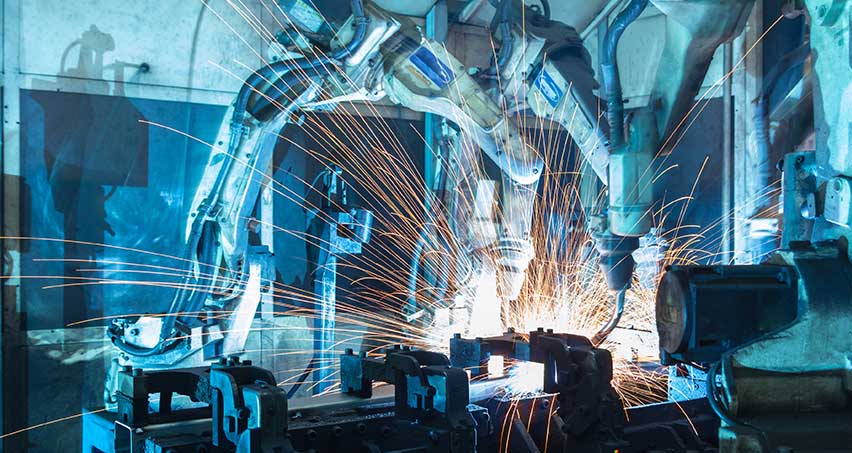
US manufacturing has been the most dynamic and largest sector in our economy. It also is one of the key drivers for economic development. The US manufacturing sector adds $2 trillion in value to the economy each year. It creates jobs and supports hundreds of local economies throughout the country.
Since the global crisis, there has been a drastic decline in manufacturing employment. Although the underlying issue - that of the loss of American manufacturing jobs to China - is difficult to comprehend, the impact these issues have had on the economy has been significant.
The US manufacturing economy supports an estimated 17 million jobs, and its output adds a significant contribution to the US GDP. It is a vital part of our economy. It accounts 20 percent for our capital expenditure, 35 percent for productivity growth, 60% of exports, 70% of R&D spend by businesses (Exhibit 1 ).
The US manufacturing sector has undergone a transformation. While some of these industries have experienced declines or disruptions, others are undergoing significant changes. Low-cost manufacturers in Asia are a threat to the US manufacturing industry, which may be undergoing a transformation that could boost US growth.
Rebuilding our battered sector of manufacturing will require long-term commitments to support the industry. It will also take people working in the field. This will require a long-term commitment to support our workforce, innovation, technology and the infrastructure.
It is important to create a manufacturing industry that is more innovative and competitive to help our economy compete and grow. This is a long-term commitment to rebuilding the strength of our industry and ensuring that we can continue to be a global leader in industrial production, technological innovation, and other areas.
A robust and sustainable manufacturing industry can help to strengthen our economy, contribute to national security, create important employment opportunities and unlock vital advancement pathways for many people. It can also recalibrate US economy.
There are numerous ways to support our manufacturing industry. And there are several important programs in place that will help achieve this goal. A manufacturing council provides advice to the Secretary of Commerce on manufacturing policies, as well as other government agencies.
Manufacturing is a major economic engine for the country. It creates jobs and drives growth in some of its most diverse communities. It employs a broader-than-average swath of the workforce and provides a retraining path for many workers without four-year degrees.
The average earnings of workers without a college degree in manufacturing, for example, are 10.9 percent greater than the average earnings of workers with a similar education in the overall economy. This has helped to rebalance the distribution of income and wealth in the U.S. The manufacturing sector has also been a critical route for the working class to the middle class, providing a route from poverty into the economic ladder.
FAQ
What is the difference in Production Planning and Scheduling, you ask?
Production Planning (PP), also known as forecasting and identifying production capacities, is the process that determines what product needs to be produced at any particular time. This can be done by forecasting demand and identifying production capabilities.
Scheduling refers the process by which tasks are assigned dates so that they can all be completed within the given timeframe.
What does warehouse refer to?
A warehouse or storage facility is where goods are stored before they are sold. It can be an outdoor or indoor area. In some cases it could be both indoors and outdoors.
Is automation important in manufacturing?
Not only are service providers and manufacturers important, but so is automation. It enables them to provide services faster and more efficiently. It also helps to reduce costs and improve productivity.
How can manufacturing avoid production bottlenecks
Avoiding production bottlenecks is as simple as keeping all processes running smoothly, from the time an order is received until the product ships.
This includes planning for capacity requirements as well as quality control measures.
Continuous improvement techniques such Six Sigma are the best method to accomplish this.
Six Sigma can be used to improve the quality and decrease waste in all areas of your company.
It focuses on eliminating variation and creating consistency in your work.
What are the four types in manufacturing?
Manufacturing refers to the transformation of raw materials into useful products by using machines and processes. It involves many different activities such as designing, building, testing, packaging, shipping, selling, servicing, etc.
Is it possible to automate certain parts of manufacturing
Yes! Yes. Automation has been around since ancient time. The wheel was invented by the Egyptians thousands of years ago. We now use robots to help us with assembly lines.
Robotics is used in many manufacturing processes today. These include:
-
Line robots
-
Robot welding
-
Robot painting
-
Robotics inspection
-
Robots that produce products
Manufacturing can also be automated in many other ways. 3D printing is a way to make custom products quickly and without waiting weeks or months for them to be manufactured.
What is the difference between a production planner and a project manager?
A production planner is more involved in the planning phase of the project than a project manger.
Statistics
- In 2021, an estimated 12.1 million Americans work in the manufacturing sector.6 (investopedia.com)
- (2:04) MTO is a production technique wherein products are customized according to customer specifications, and production only starts after an order is received. (oracle.com)
- According to the United Nations Industrial Development Organization (UNIDO), China is the top manufacturer worldwide by 2019 output, producing 28.7% of the total global manufacturing output, followed by the United States, Japan, Germany, and India.[52][53] (en.wikipedia.org)
- Many factories witnessed a 30% increase in output due to the shift to electric motors. (en.wikipedia.org)
- It's estimated that 10.8% of the U.S. GDP in 2020 was contributed to manufacturing. (investopedia.com)
External Links
How To
How to use lean manufacturing in the production of goods
Lean manufacturing (or lean manufacturing) is a style of management that aims to increase efficiency, reduce waste and improve performance through continuous improvement. It was developed in Japan during the 1970s and 1980s by Taiichi Ohno, who received the Toyota Production System (TPS) award from TPS founder Kanji Toyoda. The first book published on lean manufacturing was titled "The Machine That Changed the World" written by Michael L. Watkins and published in 1990.
Lean manufacturing is often described as a set if principles that help improve the quality and speed of products and services. It emphasizes the elimination and minimization of waste in the value stream. The five-steps of Lean Manufacturing are just-in time (JIT), zero defect and total productive maintenance (TPM), as well as 5S. Lean manufacturing focuses on eliminating non-value-added activities such as rework, inspection, and waiting.
Lean manufacturing can help companies improve their product quality and reduce costs. Additionally, it helps them achieve their goals more quickly and reduces employee turnover. Lean manufacturing has been deemed one of the best ways to manage the entire value-chain, including customers, distributors as well retailers and employees. Lean manufacturing is widely used in many industries. Toyota's philosophy is the foundation of its success in automotives, electronics and appliances, healthcare, chemical engineers, aerospace, paper and food, among other industries.
Five basic principles of Lean Manufacturing are included in lean manufacturing
-
Define Value- Identify the added value your company brings to society. What makes you stand out from your competitors?
-
Reduce Waste – Eliminate all activities that don't add value throughout the supply chain.
-
Create Flow. Ensure that your work is uninterrupted and flows seamlessly.
-
Standardize and simplify – Make processes as repeatable and consistent as possible.
-
Develop Relationships: Establish personal relationships both with internal and external stakeholders.
Lean manufacturing isn’t new, but it has seen a renewed interest since 2008 due to the global financial crisis. Many companies have adopted lean manufacturing methods to increase their marketability. According to some economists, lean manufacturing could be a significant factor in the economic recovery.
Lean manufacturing has many benefits in the automotive sector. These benefits include increased customer satisfaction, reduced inventory levels and lower operating costs.
Any aspect of an enterprise can benefit from Lean manufacturing. Lean manufacturing is most useful in the production sector of an organisation because it ensures that each step in the value-chain is efficient and productive.
There are three main types of lean manufacturing:
-
Just-in Time Manufacturing (JIT), also known as "pull system": This form of lean manufacturing is often referred to simply as "pull". JIT is a process in which components can be assembled at the point they are needed, instead of being made ahead of time. This method reduces lead times, increases availability, and decreases inventory.
-
Zero Defects Manufacturing (ZDM),: ZDM is a system that ensures no defective units are left the manufacturing facility. If a part is required to be repaired on the assembly line, it should not be scrapped. This is also true for finished products that require minor repairs before shipping.
-
Continuous Improvement (CI),: Continuous improvement aims improve the efficiency and effectiveness of operations by continuously identifying issues and making changes to reduce waste. Continuous Improvement (CI) involves continuous improvement in processes, people, tools, and infrastructure.