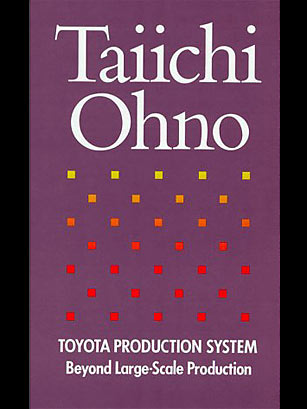
Supply chain management is crucial to maintaining a solid operation, regardless of whether you are a small businessperson or the enterprise arm for a major corporation. Risks vary from the mundane to the downright disastrous. Your organization can be protected from losses with a well-planned plan and an effective implementation strategy.
Data sharing is an essential part of a supply chain continuity program. If your organization is dependent on a single supplier it can lead to supplier disputes and vendor failures. You will be more likely to avoid supply interruptions if your company is part-of a multisupplier group. You might also be able negotiate with an alternative supplier.
Similarly, if your company has a complex network of contractors, you are at greater risk of vendor fraud, duplicate billing, and improper related-party billing. To mitigate these risks, you may develop a risk assessment process that can include a complete assessment your suppliers, partners and other tier 1 components.
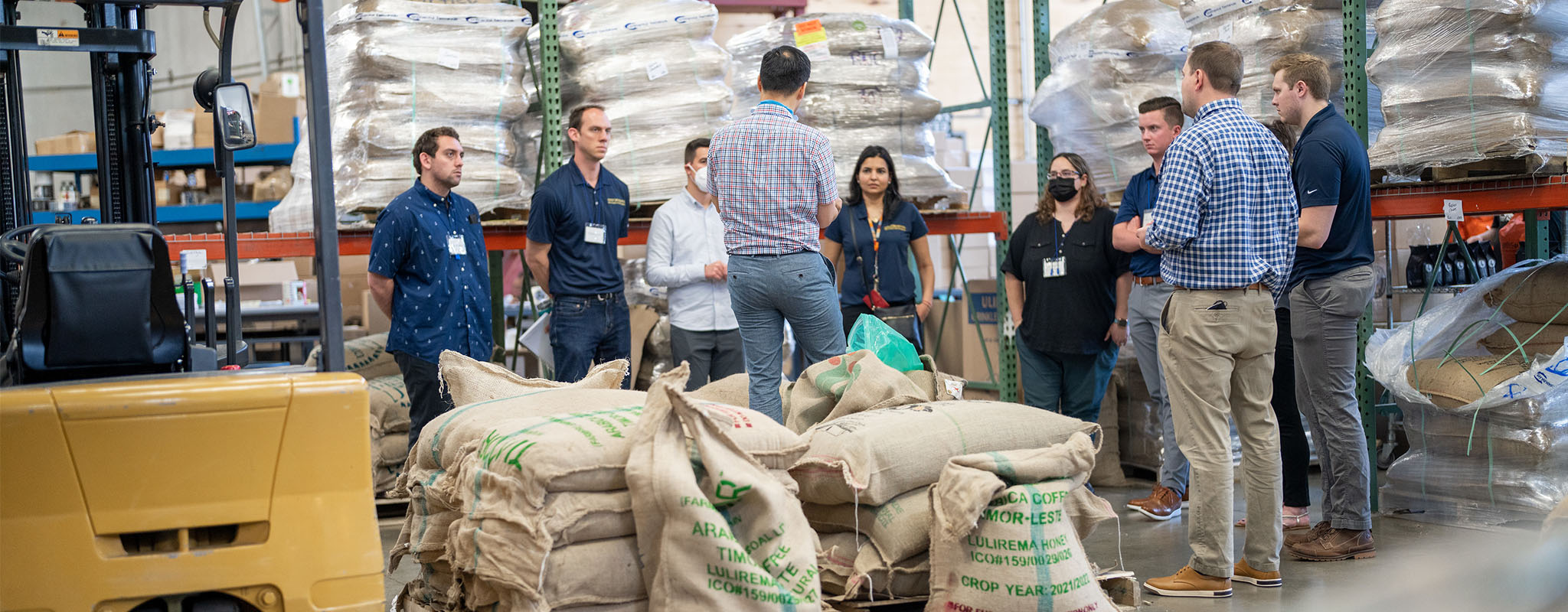
When developing a good supply chain risk management program, you should first identify the important elements of a good supply chain, then quantify and measure them, and then devise an action plan. These items should be combined with a few additional. Proactive monitoring systems are the most important aspect. That is, a system that gives your executives real-time, accurate information on supply chain risk. Real-time supply chain risk tracking will help you make informed decisions and respond promptly.
When assessing and quantifying risks, you must remember that resilience of your supply chain is a function governance. In particular, you need to consider the role of stakeholders. A properly scorecarded supplier system could have saved the pharmacy from a bankruptcy.
The first step to reducing supply chain disruptions is having a plan. However, implementing the right contingency plans is not always easy. Many businesses fail to take the time to develop an appropriate number of contingency plans for each risk they are managing. These plans should begin with the most significant potential impact.
The PPPR, or preventive preparedness, readiness, response and recovery, is a global standard for supply-chain risk management. It is a solid approach that will improve your ability to react to supply-chain disruptions and can be used with other strategies to protect you organization from them. Using a PPPR can make the difference between surviving or thriving in today’s market.
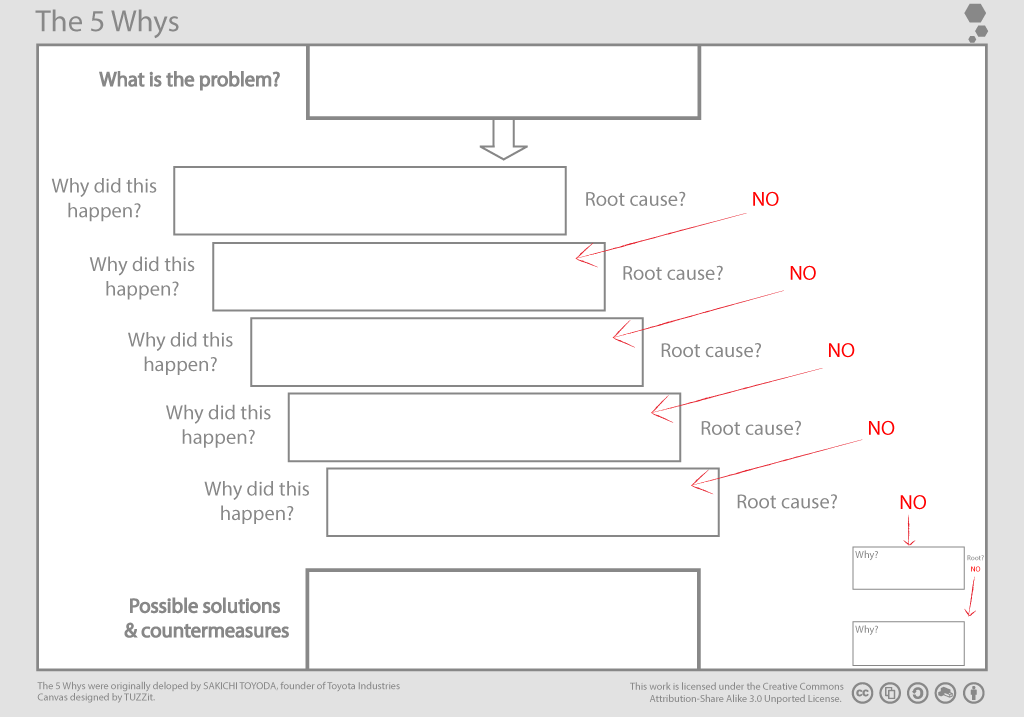
It is possible to get the right information from your suppliers to help you understand their history and offer. This information will help you to make better decisions whether you are trying to increase your sourcing efforts or just tweaking your current processes. You can give your insurers the right premiums by using reliable data.
FAQ
How can excess manufacturing production be reduced?
It is essential to find better ways to manage inventory to reduce overproduction. This would decrease the time that is spent on inefficient activities like purchasing, storing, or maintaining excess stock. By doing this, we could free up resources for other productive tasks.
A Kanban system is one way to achieve this. A Kanban board can be used to monitor work progress. Kanban systems allow work items to move through different states until they reach their final destination. Each state represents a different priority.
As an example, if work is progressing from one stage of the process to another, then the current task is complete and can be transferred to the next. It is possible to keep a task in the beginning stages until it gets to the end.
This allows you to keep work moving along while making sure that no work gets neglected. Managers can see how much work has been done and the status of each task at any time with a Kanban Board. This information allows managers to adjust their workflow based off real-time data.
Lean manufacturing is another way to manage inventory levels. Lean manufacturing emphasizes eliminating waste in all phases of production. Anything that does nothing to add value to a product is waste. Here are some examples of common types.
-
Overproduction
-
Inventory
-
Unnecessary packaging
-
Excess materials
These ideas will help manufacturers increase efficiency and lower costs.
What makes a production planner different from a project manger?
A production planner is more involved in the planning phase of the project than a project manger.
Why should you automate your warehouse?
Modern warehousing has seen automation take center stage. With the rise of ecommerce, there is a greater demand for faster delivery times as well as more efficient processes.
Warehouses need to adapt quickly to meet changing needs. They must invest heavily in technology to do this. Automation warehouses can bring many benefits. Here are some reasons why it's worth investing in automation:
-
Increases throughput/productivity
-
Reduces errors
-
Increases accuracy
-
Safety Boosts
-
Eliminates bottlenecks
-
Allows companies to scale more easily
-
It makes workers more efficient
-
This gives you visibility into what happens in the warehouse
-
Enhances customer experience
-
Improves employee satisfaction
-
It reduces downtime, and increases uptime
-
You can be sure that high-quality products will arrive on time
-
Eliminates human error
-
Assure compliance with regulations
What are the products of logistics?
Logistics refers to the movement of goods from one place to another.
They encompass all aspects transport, including packaging and loading, transporting, storage, unloading.
Logisticians ensure that products reach the right destination at the right moment and under safe conditions. Logisticians assist companies in managing their supply chains by providing information such as demand forecasts, stock levels and production schedules.
They keep track and monitor the transit of shipments, maintain quality standards, order replenishment and inventories, coordinate with suppliers, vendors, and provide support for sales and marketing.
What is production planning?
Production planning is the process of creating a plan that covers all aspects of production. This includes scheduling, budgeting and crew, location, equipment, props, and more. It is important to have everything ready and planned before you start shooting. This document should also include information on how to get the best result on set. This includes location information, crew details, equipment specifications, and casting lists.
The first step is to outline what you want to film. You might have an idea of where you want to film, or you may have specific locations or sets in mind. Once you have determined your scenes and locations, it is time to start figuring out the elements that you will need for each scene. You might decide you need a car, but not sure what make or model. This is where you can look up car models online and narrow down your options by choosing from different makes and models.
After you have selected the car you want, you can begin to think about additional features. Do you need people sitting in the front seats? Or maybe you just need someone to push the car around. You might want to change your interior color from black and white. These questions will help you determine the exact look and feel of your car. Also, think about what kind of shots you would like to capture. Are you going to be shooting close-ups? Or wide angles? Maybe the engine or steering wheel is what you are looking to film. These things will help you to identify the car that you are looking for.
Once you have made all the necessary decisions, you can start to create a schedule. You can create a schedule that will outline when you must start and finish your shoots. A schedule for each day will detail when you should arrive at the location and when you need leave. So everyone is clear about what they need to do. If you need to hire extra staff, you can make sure you book them in advance. There is no point in hiring someone who won't turn up because you didn't let him know.
Your schedule will also have to be adjusted to reflect the number of days required to film. Some projects only take one or two days, while others may last weeks. It is important to consider whether you require more than one photo per day when you create your schedule. Multiple takes of the same location will lead to higher costs and take more time. If you are unsure if you need multiple takes, it is better to err on the side of caution and shoot fewer takes rather than risk wasting money.
Budget setting is another important aspect in production planning. A realistic budget will help you work within your means. You can always lower the budget if you encounter unexpected problems. You shouldn't underestimate the amount you'll spend. You'll end up with less money after paying for other things if the cost is underestimated.
Planning production is a tedious process. Once you have a good understanding of how everything works together, planning future projects becomes easy.
Statistics
- In the United States, for example, manufacturing makes up 15% of the economic output. (twi-global.com)
- (2:04) MTO is a production technique wherein products are customized according to customer specifications, and production only starts after an order is received. (oracle.com)
- According to the United Nations Industrial Development Organization (UNIDO), China is the top manufacturer worldwide by 2019 output, producing 28.7% of the total global manufacturing output, followed by the United States, Japan, Germany, and India.[52][53] (en.wikipedia.org)
- It's estimated that 10.8% of the U.S. GDP in 2020 was contributed to manufacturing. (investopedia.com)
- In 2021, an estimated 12.1 million Americans work in the manufacturing sector.6 (investopedia.com)
External Links
How To
How to use 5S to increase Productivity in Manufacturing
5S stands for "Sort", "Set In Order", "Standardize", "Separate" and "Store". Toyota Motor Corporation developed the 5S method in 1954. This methodology helps companies improve their work environment to increase efficiency.
This method aims to standardize production processes so that they are repeatable, measurable and predictable. This means that every day tasks such cleaning, sorting/storing, packing, and labeling can be performed. Because workers know what they can expect, this helps them perform their jobs more efficiently.
Implementing 5S involves five steps: Sort, Set in Order, Standardize Separate, Store, and Each step has a different action and leads to higher efficiency. Sorting things makes it easier to find them later. When items are ordered, they are put together. After you have divided your inventory into groups you can store them in easy-to-reach containers. Labeling your containers will ensure that everything is correctly labeled.
Employees will need to be more critical about their work. Employees need to understand the reasons they do certain jobs and determine if there is a better way. To implement the 5S system, employees must acquire new skills and techniques.
The 5S method not only increases efficiency but also boosts morale and teamwork. They are more motivated to achieve higher efficiency levels as they start to see improvement.