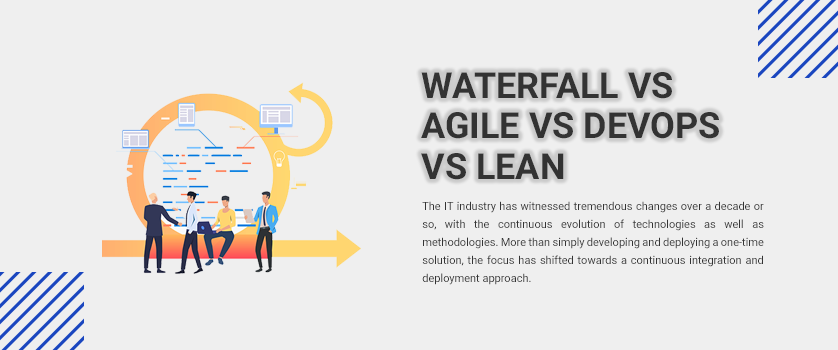
Lean is a term used in manufacturing to describe a series of principles and techniques. It can also be a motivational word that encourages improvement in the process.
The Definition of Lean
When a business is aiming to be more efficient, it may have to eliminate certain activities that don't add value to the product or service it creates. This can include unused equipment or idle time.
Lean management is a system designed to eliminate waste in production. It is an ongoing process, so it will need to be constantly adjusted and improved.
Lean is a concept that focuses on what the customer wants and makes it a priority to provide this value. It does not focus on what the business thinks they need. In this way, businesses can avoid wasting time or money creating products their customers don't want.
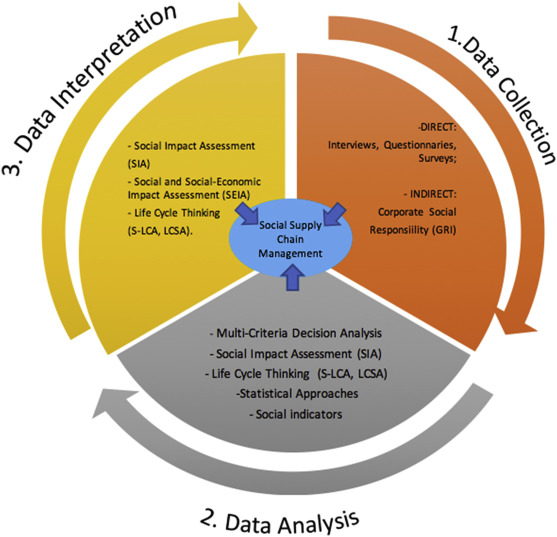
You should be aware that the lean concept can be adapted to any type of industry or production process. It is for this reason that it has been so widely adopted by many industries.
Lean production, which has existed for quite some time, is a way of focusing on delivering quality products in the right quantities and at the right times. It's also a powerful tool to create efficiencies in manufacturing.
Toyoda defined lean as a concept that aims to eliminate waste from the production process. This can include things such as defects that are unacceptable to customers.
Toyoda's solution to this was a flow process, which involved workers stopping the production line to inspect a part and removing it if necessary. This process allowed Toyoda's engineers to adjust each step in production so that they could eliminate any defects as soon as they appeared, and increase their productivity.
Jidoka is a system that automatically comes to a stop when there is an abnormality in the production process. Kaizen is the name of this system, and it's an essential part in lean manufacturing.
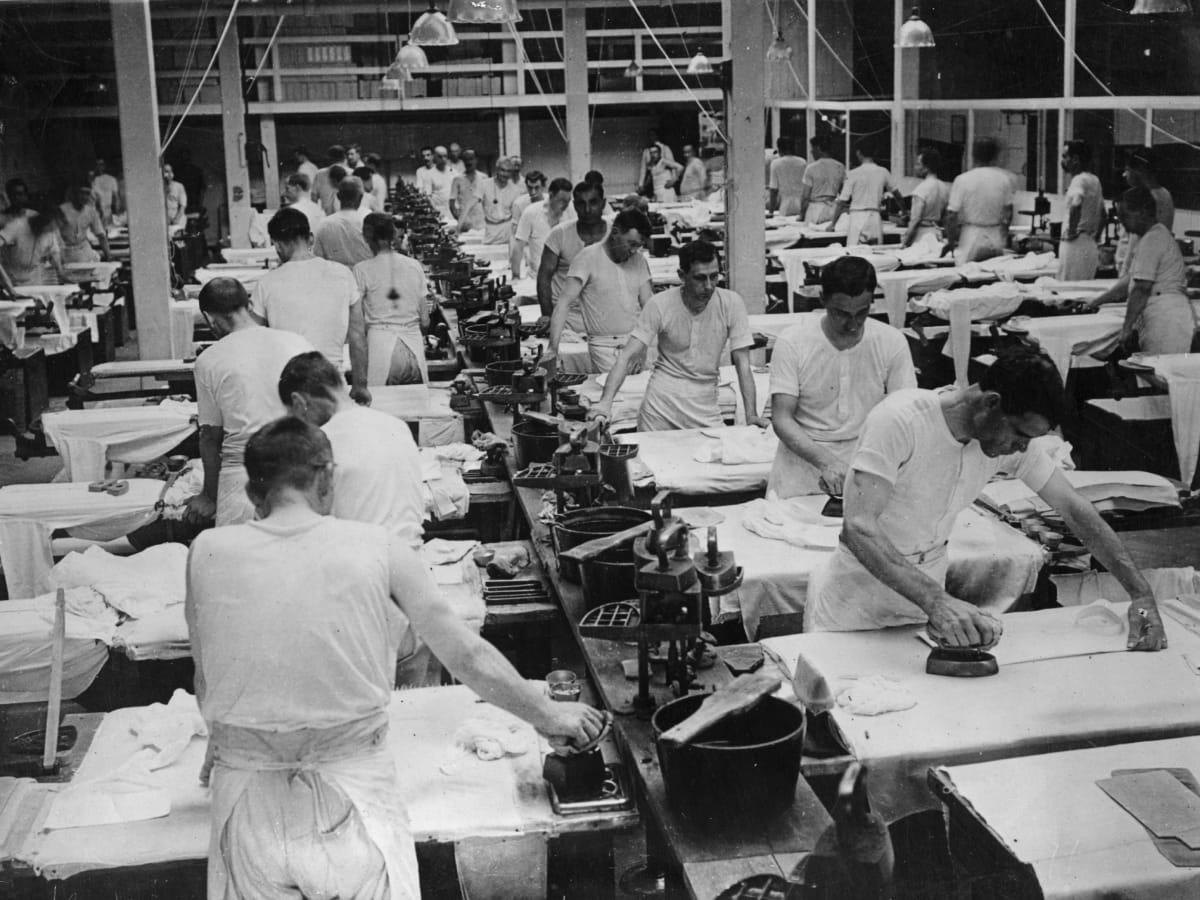
It is a continuous improvement process for any business process. This process can be applied in any area of business, whether it is the production of products.
Lean is not well understood by many people, but it's a wonderful concept that improves the way businesses are run. Lean helps companies save time and resources by improving their business processes. They can also build a good reputation among customers.
Lean isn't an isolated process; it is a system that must be improved on all levels within a company to achieve success. It's important to involve everyone in the process. This way, they can each contribute their own ideas and help ensure that things run smoothly.
FAQ
What is the importance of logistics in manufacturing?
Logistics are essential to any business. They can help you achieve great success by helping you manage product flow from raw material to finished goods.
Logistics plays a significant role in reducing cost and increasing efficiency.
What is the responsibility of a logistics manager?
A logistics manager makes sure that all goods are delivered on-time and in good condition. This is done by using his/her experience and knowledge of the company's products. He/she also needs to ensure adequate stock to meet demand.
What jobs are available in logistics?
There are different kinds of jobs available in logistics. Here are some:
-
Warehouse workers – They load and unload pallets and trucks.
-
Transportation drivers: They drive trucks and trailers and deliver goods and make pick-ups.
-
Freight handlers are people who sort and pack freight into warehouses.
-
Inventory managers - These are responsible for overseeing the stock of goods in warehouses.
-
Sales reps - They sell products and services to customers.
-
Logistics coordinators – They plan and coordinate logistics operations.
-
Purchasing agents – They buy goods or services necessary to run a company.
-
Customer service representatives - Answer calls and email from customers.
-
Shipping clerks – They process shipping orders, and issue bills.
-
Order fillers - These people fill orders based on what has been ordered.
-
Quality control inspectors are responsible for inspecting incoming and outgoing products looking for defects.
-
Others - There are many types of jobs in logistics such as transport supervisors and cargo specialists.
Why automate your warehouse
Modern warehousing is becoming more automated. E-commerce has increased the demand for quicker delivery times and more efficient processes.
Warehouses should be able adapt quickly to new needs. Technology investment is necessary to enable warehouses to respond quickly to changing demands. Automating warehouses is a great way to save money. Here are some of the reasons automation is worth your investment:
-
Increases throughput/productivity
-
Reduces errors
-
Increases accuracy
-
Boosts safety
-
Eliminates bottlenecks
-
Allows companies scale more easily
-
Workers are more productive
-
It gives visibility to everything that happens inside the warehouse
-
Enhances customer experience
-
Improves employee satisfaction
-
Reducing downtime and increasing uptime
-
High quality products delivered on-time
-
Eliminates human error
-
It helps ensure compliance with regulations
What is the role and responsibility of a Production Planner?
Production planners ensure all aspects of the project are delivered within time and budget. They ensure that the product or service is of high quality and meets client requirements.
Statistics
- Job #1 is delivering the ordered product according to specifications: color, size, brand, and quantity. (netsuite.com)
- In 2021, an estimated 12.1 million Americans work in the manufacturing sector.6 (investopedia.com)
- It's estimated that 10.8% of the U.S. GDP in 2020 was contributed to manufacturing. (investopedia.com)
- According to a Statista study, U.S. businesses spent $1.63 trillion on logistics in 2019, moving goods from origin to end user through various supply chain network segments. (netsuite.com)
- (2:04) MTO is a production technique wherein products are customized according to customer specifications, and production only starts after an order is received. (oracle.com)
External Links
How To
How to Use lean manufacturing in the Production of Goods
Lean manufacturing (or lean manufacturing) is a style of management that aims to increase efficiency, reduce waste and improve performance through continuous improvement. It was created in Japan by Taiichi Ohno during the 1970s and 80s. He received the Toyota Production System award (TPS), from Kanji Toyoda, founder of TPS. Michael L. Watkins published the book "The Machine That Changed the World", which was the first to be published about lean manufacturing.
Lean manufacturing refers to a set of principles that improve the quality, speed and costs of products and services. It emphasizes the elimination and minimization of waste in the value stream. The five-steps of Lean Manufacturing are just-in time (JIT), zero defect and total productive maintenance (TPM), as well as 5S. Lean manufacturing is about eliminating activities that do not add value, such as inspection, rework, and waiting.
Lean manufacturing not only improves product quality but also reduces costs. Companies can also achieve their goals faster by reducing employee turnover. Lean manufacturing can be used to manage all aspects of the value chain. Customers, suppliers, distributors, retailers and employees are all included. Lean manufacturing is widely practiced in many industries around the world. For example, Toyota's philosophy underpins its success in automobiles, electronics, appliances, healthcare, chemical engineering, aerospace, paper, food, etc.
Five basic principles of Lean Manufacturing are included in lean manufacturing
-
Define Value: Identify the social value of your business and what sets you apart.
-
Reduce Waste – Eliminate all activities that don't add value throughout the supply chain.
-
Create Flow – Ensure that work flows smoothly throughout the process.
-
Standardize and simplify – Make processes as repeatable and consistent as possible.
-
Build relationships - Develop and maintain personal relationships with both your internal and external stakeholders.
Lean manufacturing isn’t new, but it has seen a renewed interest since 2008 due to the global financial crisis. Many businesses are now using lean manufacturing to improve their competitiveness. Many economists believe lean manufacturing will play a major role in economic recovery.
Lean manufacturing is becoming a popular practice in automotive. It has many advantages. These include better customer satisfaction and lower inventory levels. They also result in lower operating costs.
You can apply Lean Manufacturing to virtually any aspect of your organization. It is especially useful for the production aspect of an organization, as it ensures that every step in the value chain is efficient and effective.
There are three types principally of lean manufacturing:
-
Just-in Time Manufacturing, (JIT): This kind of lean manufacturing is also commonly known as "pull-systems." JIT means that components are assembled at the time of use and not manufactured in advance. This strategy aims to decrease lead times, increase availability of parts and reduce inventory.
-
Zero Defects Manufacturing (ZDM): ZDM focuses on ensuring that no defective units leave the manufacturing facility. If a part needs to be fixed during the assembly line, it should be repaired rather than scrapped. This applies to finished goods that may require minor repairs before shipment.
-
Continuous Improvement (CI: Continuous improvement aims to increase the efficiency of operations by constantly identifying and making improvements to reduce or eliminate waste. Continuous improvement refers to continuous improvement of processes as well people and tools.