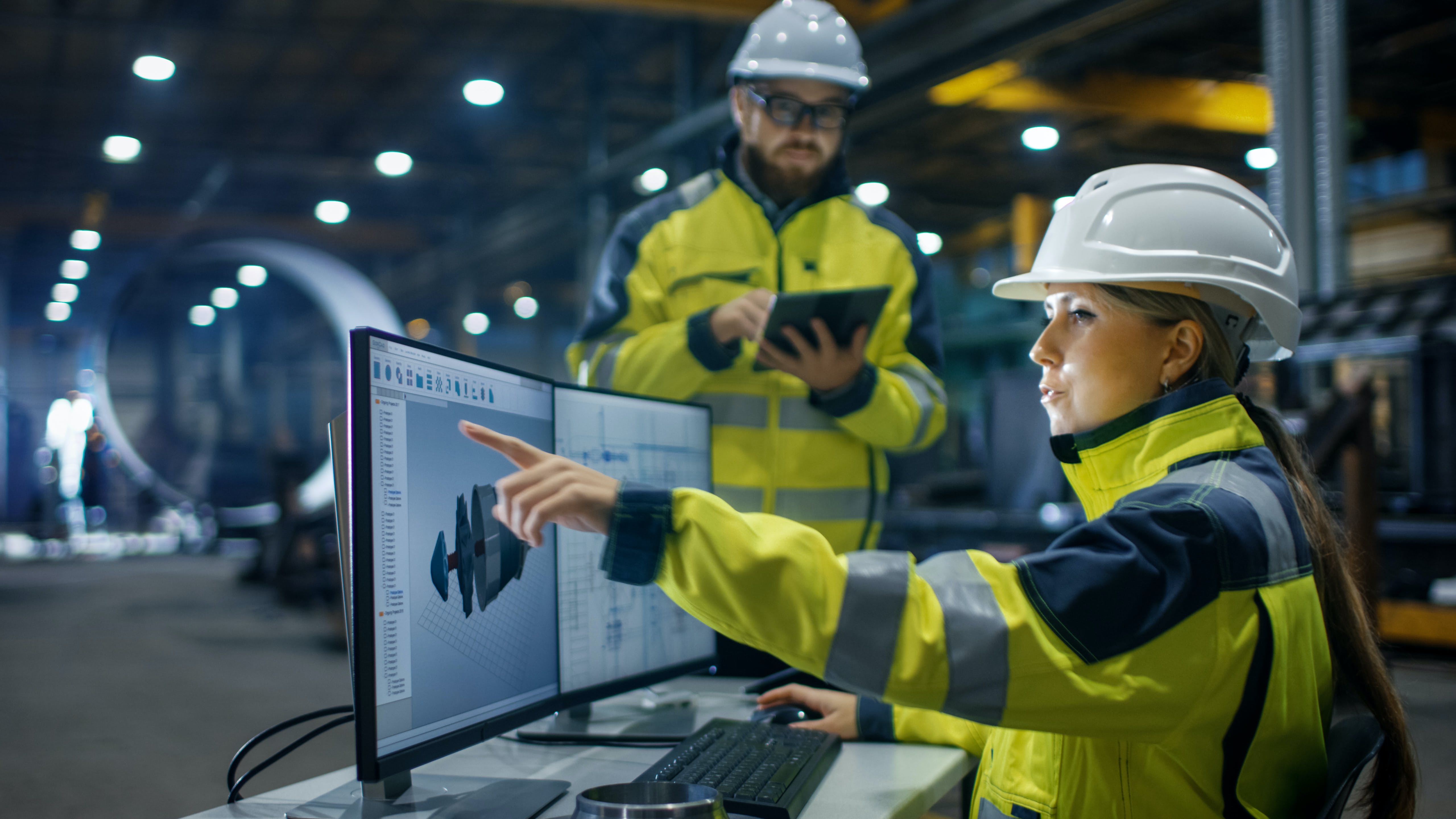
Orlando is home of a number top logistics companies that provide services to both small and large businesses. There are many opportunities to begin a career in the logistics sector. These include entry-level jobs to management positions that pay more than $100,000 per year.
Various logistics jobs are offered in Orlando. They include shipping clerks as well as truck drivers and warehouse associates. You can gain experience in many different areas with these jobs, including planning and organizing large jobs or overseeing a company's day-to-day operation.
Orlando's logistics industry is worth $1.5billion and specializes on the movement of goods. Its central location makes it a hub for several major shipping centers.
These hubs allow companies to easily reach customers in Orlando. They also make it easier for companies to transport cargo from different parts of the country and around the world.
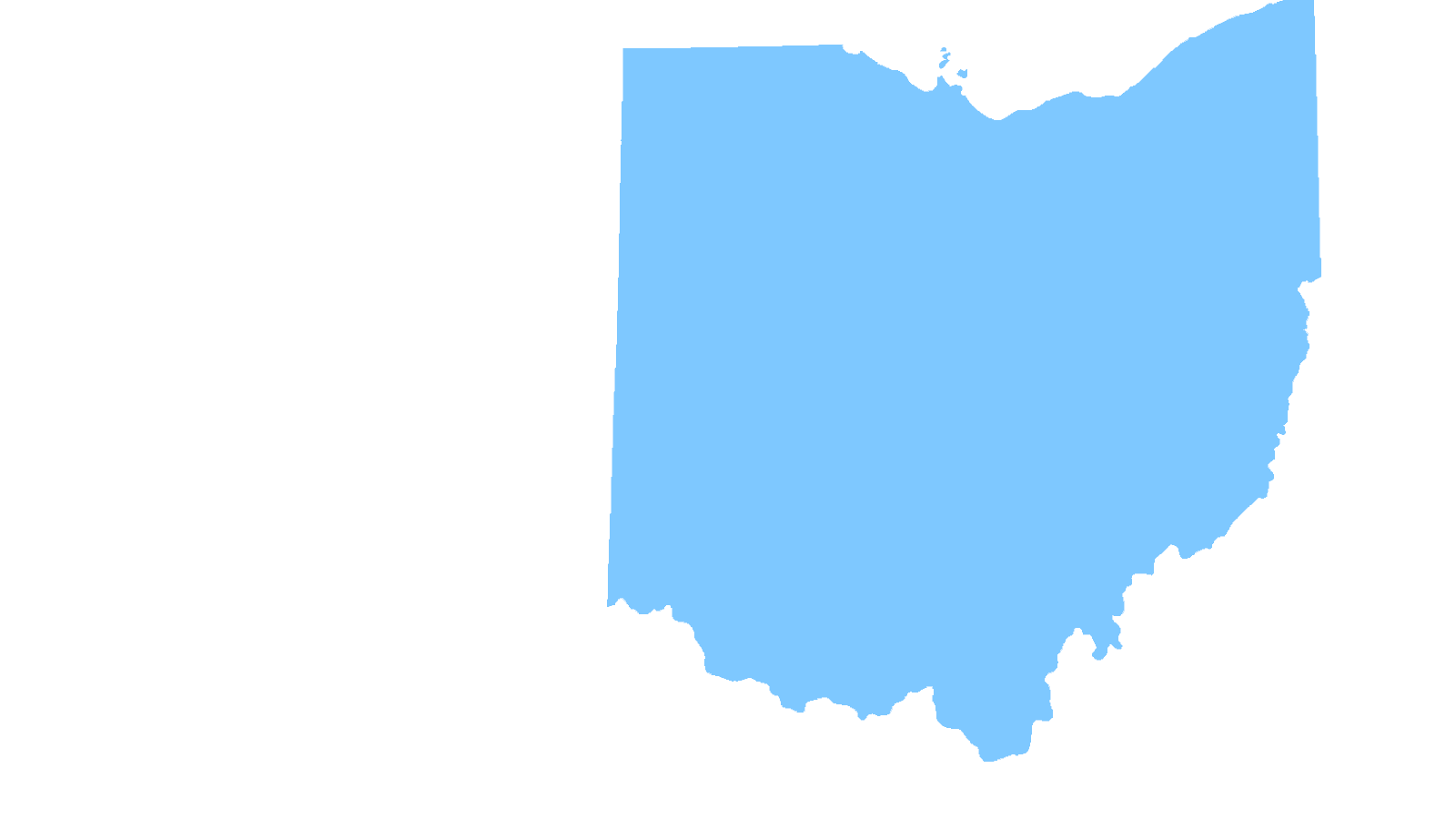
For those who want to work as a logistician, there are certain things they should know. Start by learning how to handle large amounts of cargo. This includes negotiating contracts, and making sure that the supplies are given to the correct people when they need them.
Know about the security and safety measures of the cargos you transport. Orlando's leading logistics firms offer advanced tracking and security technology, along with cargo certifications.
Before choosing a company to handle your logistics, it is important that you also consider the company's customer service and reputation. To do this, you can read reviews from previous customers or speak to company representatives.
A good logistics company in Orlando is one that has a reputation for quality and reliability. They must be able to give accurate information to customers and provide reliable shipping services at affordable prices.
AIT, Roadrunner Transportation Systems and Worldwide Express are a few of the best Orlando-based logistics companies. All of these companies specialize in helping small and medium-sized business ship smarter.
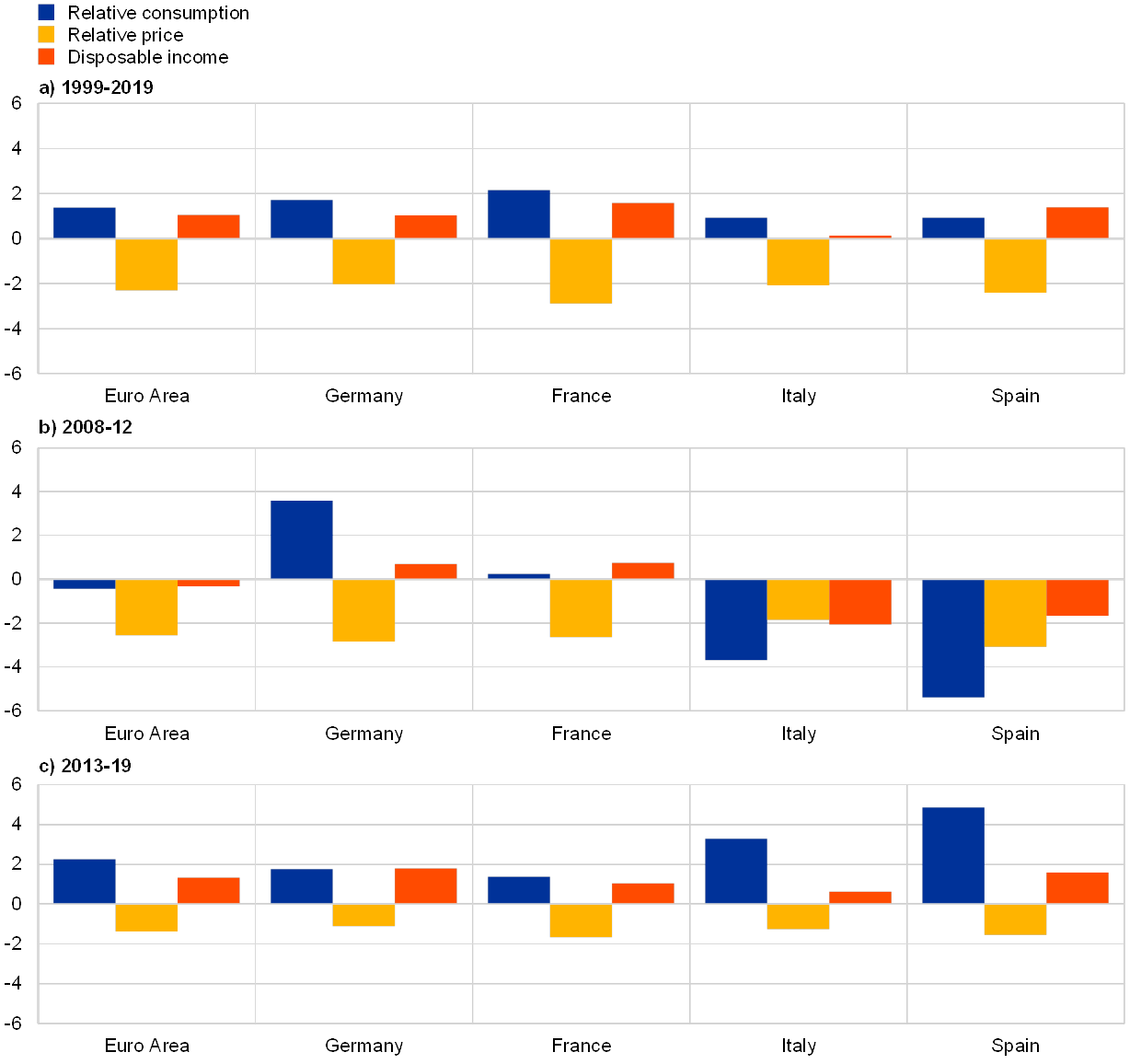
These companies provide a variety of services such as inventory management, supply chain management and freight forwarding. These companies also offer a 24/7 service, so that you can get all the help you need even when your office hours are over.
Orlando shipping firms should be capable of handling any job. The company should have the equipment and personnel to handle any move, regardless of how large or small.
Orlando's population is large, and it has a strong labor pool. The area has easy access to air, rail, and sea transportation. It is a great location for any logistics company who wants to be near the most popular destinations in the country.
FAQ
How can manufacturing overproduction be reduced?
In order to reduce excess production, you need to develop better inventory management methods. This would reduce time spent on activities such as purchasing, stocking, and maintaining excess stock. By doing this, we could free up resources for other productive tasks.
One way to do this is to adopt a Kanban system. A Kanban board can be used to monitor work progress. Work items are moved through various states to reach their destination in a Kanban system. Each state represents a different priority.
When work is completed, it can be transferred to the next stage. If a task is still in its beginning stages, it will continue to be so until it reaches the end.
This allows you to keep work moving along while making sure that no work gets neglected. Managers can monitor the work being done by Kanban boards to see what is happening at any given time. This information allows them to adjust their workflow based on real-time data.
Lean manufacturing can also be used to reduce inventory levels. Lean manufacturing is about eliminating waste from all stages of the production process. Anything that does nothing to add value to a product is waste. These are some of the most common types.
-
Overproduction
-
Inventory
-
Unnecessary packaging
-
Materials in excess
These ideas will help manufacturers increase efficiency and lower costs.
What are the 7 Rs of logistics?
The acronym 7R's for Logistics stands to represent the seven basic principles in logistics management. It was developed and published by the International Association of Business Logisticians in 2004 as part of the "Seven Principles of Logistics Management".
The following letters make up the acronym:
-
Responsible - ensure that all actions taken are within legal requirements and are not harmful to others.
-
Reliable – have faith in your ability and capability to keep promises.
-
Use resources effectively and sparingly.
-
Realistic – consider all aspects of operations, from cost-effectiveness to environmental impact.
-
Respectful - treat people fairly and equitably.
-
Reliable - Find ways to save money and increase your productivity.
-
Recognizable - provide customers with value-added services.
Is automation necessary in manufacturing?
Automation is important not only for manufacturers but also for service providers. They can provide services more quickly and efficiently thanks to automation. It helps them to lower costs by reducing human errors, and improving productivity.
Statistics
- Many factories witnessed a 30% increase in output due to the shift to electric motors. (en.wikipedia.org)
- Job #1 is delivering the ordered product according to specifications: color, size, brand, and quantity. (netsuite.com)
- (2:04) MTO is a production technique wherein products are customized according to customer specifications, and production only starts after an order is received. (oracle.com)
- According to the United Nations Industrial Development Organization (UNIDO), China is the top manufacturer worldwide by 2019 output, producing 28.7% of the total global manufacturing output, followed by the United States, Japan, Germany, and India.[52][53] (en.wikipedia.org)
- You can multiply the result by 100 to get the total percent of monthly overhead. (investopedia.com)
External Links
How To
How to use the Just-In Time Method in Production
Just-in-time is a way to cut costs and increase efficiency in business processes. This is where you have the right resources at the right time. This means that you only pay the amount you actually use. Frederick Taylor was the first to coin this term. He developed it while working as a foreman during the early 1900s. He saw how overtime was paid to workers for work that was delayed. He decided that workers would be more productive if they had enough time to complete their work before they started to work.
The idea behind JIT is that you should plan ahead and have everything ready so you don't waste money. Look at your entire project, from start to end. Make sure you have enough resources in place to deal with any unexpected problems. You will have the resources and people to solve any problems you anticipate. You won't have to pay more for unnecessary items.
There are different types of JIT methods:
-
Demand-driven JIT: This is a JIT that allows you to regularly order the parts/materials necessary for your project. This will allow for you to track the material that you have left after using it. It will also allow you to predict how long it takes to produce more.
-
Inventory-based : You can stock the materials you need in advance. This allows you to forecast how much you will sell.
-
Project-driven: This is an approach where you set aside enough funds to cover the cost of your project. If you know the amount you require, you can buy the materials you need.
-
Resource-based JIT : This is probably the most popular type of JIT. You assign certain resources based off demand. You will, for example, assign more staff to deal with large orders. If you don't receive many orders, then you'll assign fewer employees to handle the load.
-
Cost-based: This is the same as resource-based except that you don't care how many people there are but how much each one of them costs.
-
Price-based: This is very similar to cost-based, except that instead of looking at how much each individual worker costs, you look at the overall price of the company.
-
Material-based: This approach is similar to cost-based. However, instead of looking at the total cost for the company, you look at how much you spend on average on raw materials.
-
Time-based JIT: A variation on resource-based JIT. Instead of focusing solely on the amount each employee costs, focus on how long it takes for the project to be completed.
-
Quality-based JIT - This is another form of resource-based JIT. Instead of thinking about how much each employee costs or how long it takes to manufacture something, you think about how good the quality of your product is.
-
Value-based JIT is the newest form of JIT. You don't worry about whether the products work or if they meet customer expectations. Instead, your goal is to add value to the market.
-
Stock-based: This inventory-based approach focuses on how many items are being produced at any one time. It's useful when you want maximum production and minimal inventory.
-
Just-in-time (JIT) planning: This is a combination of JIT and supply chain management. It is the process of scheduling components' delivery as soon as they have been ordered. It's important because it reduces lead times and increases throughput.