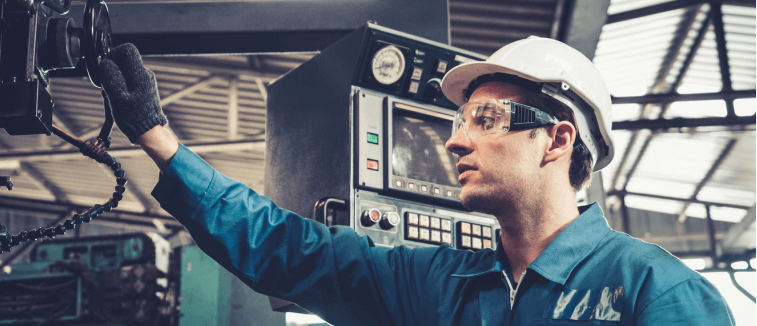
Until recently "Made in Japan", meant low quality consumer goods. Japanese products are known for their reliability, precision and durability. Japanese manufacturers are also imposing stricter standards. This has created increased cost pressure and increased competition. Japanese companies are also being asked how fast they can adapt to changing market conditions.
Japanese factories are highly controlled. They manage the work content, labor, as well as working relationships. This is possible by training their employees to make high-quality products. They also encourage feedback from their customers, quality inspectors, and vendors.
Japan's manufacturing culture stems from its strict cultural adherence to discipline. It has been influenced by technology. Many Japanese companies employ artificial intelligence to supplement their non-manufacturing labor. The next wave in technology promises to enhance non-manufacturing workers. Robots will be able to work in hospitals, factories, schools, temples, and nursing homes.
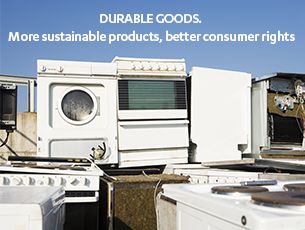
There have been many safety scandals. One incident involved a 13 year-old girl who died due to a virus contracted in her factory. Another case involved a company which admitted to having improper vehicle inspection protocols. These scandals have put the Japanese factory floor under scrutiny. A number of workers' strikes also changed the working environment. As a result, the government introduced new regulations such closed loop management. It isolates workers and prevents them from contracting viruses.
Another important factor affecting Japan's manufacturing industry is the aging population. Japanese birth rates are decreasing which means there is an acute shortage of labor. This demand is not being met by enough labor in Japan. Japanese manufacturing requires foreign workers to grow. Many factories are not able to source supplies. This is causing problems for their supply chain.
Japanese manufacturers work closely with their suppliers in order to solve problems. Japanese companies sometimes hold seminars for their suppliers to teach them how they can better meet customer demands. To make sure they meet specifications, they screen all incoming parts. They use advanced technology like automatic checkers to spot defects before they occur.
Their products show the best of Japanese production. Japanese automobiles are known for their fuel efficiency and durability as well as quality. The Japanese auto industry is also one the largest in world. Japan is home to six of the top 10 automakers, including Toyota and Honda. They are known for producing vehicles with higher quality features at a cheaper price.
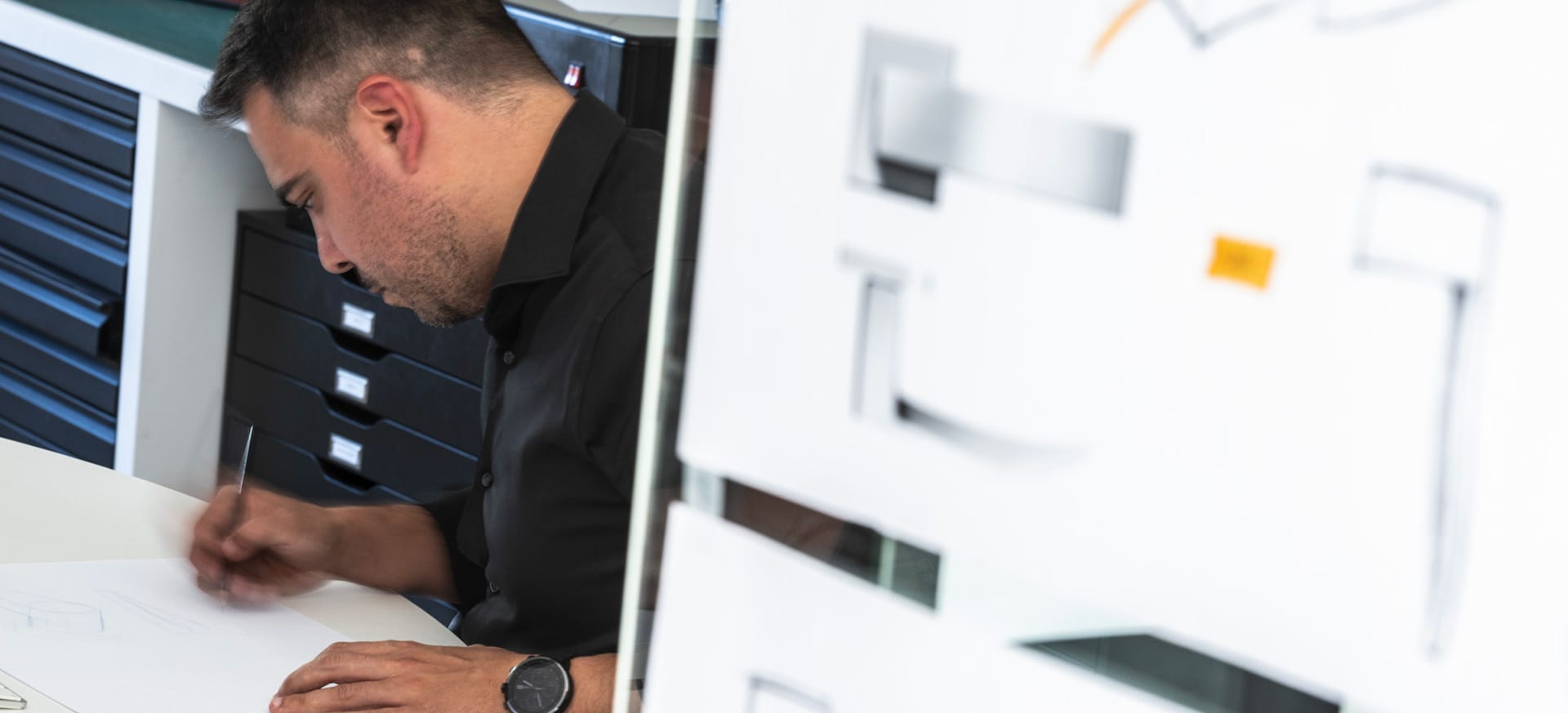
The next wave of technology will also have a big impact on the industry, especially in terms of wages. Robots are already replacing field workers in service organizations. These workers report directly towards sales and manufacturing managers. The future of robotics will go beyond Japanese factories. Robots can even be used in train stations and hospitals.
Japan is also having problems with its supply chain. This has slowed down exports and made it more difficult to access the port. Other problems include the proliferation of non-regular workers, which have lowered standards and shaved off costs.
FAQ
What are the essential elements of running a logistics firm?
To run a successful logistics company, you need a lot knowledge and skills. Good communication skills are essential to effectively communicate with your suppliers and clients. You should be able analyse data and draw inferences. You must be able to work well under pressure and handle stressful situations. To improve efficiency, you must be innovative and creative. You will need strong leadership skills to motivate and direct your team members towards achieving their organizational goals.
It is important to be organized and efficient in order to meet tight deadlines.
What are the 7 Rs of logistics management?
The acronym 7R's for Logistics stands to represent the seven basic principles in logistics management. It was published in 2004 by the International Association of Business Logisticians as part of their "Seven Principles of Logistics Management" series.
The acronym is composed of the following letters.
-
Responsible - ensure that all actions taken are within legal requirements and are not harmful to others.
-
Reliable - Have confidence in your ability to fulfill all of your commitments.
-
Use resources effectively and sparingly.
-
Realistic – consider all aspects of operations, from cost-effectiveness to environmental impact.
-
Respectful: Treat others with fairness and equity
-
Responsive - Look for ways to save time and increase productivity.
-
Recognizable: Provide customers with value-added service
What is production planning?
Production Planning is the creation of a plan to cover all aspects, such as scheduling, budgeting. Location, crew, equipment, props and other details. This document ensures that everything is prepared and available when you are ready for shooting. It should also contain information on achieving the best results on set. This includes information on shooting times, locations, cast lists and crew details.
It is important to first outline the type of film you would like to make. You may have already chosen the location you want, or there are locations or sets you prefer. Once you have identified the scenes and locations, you can start to determine which elements are required for each scene. Perhaps you have decided that you need to buy a car but aren't sure which model. To narrow your options, you can search online for available models.
Once you have found the right vehicle, you can think about adding accessories. You might need to have people in the front seats. Perhaps you have someone who needs to be able to walk around the back of your car. Perhaps you would like to change the interior colour from black to white. These questions will help guide you in determining the ideal look and feel for your car. You can also think about the type of shots you want to get. Do you want to film close-ups, or wider angles? Maybe you want to show the engine and the steering wheel. These details will help identify the exact car you wish to film.
Once you have determined all of the above, you can move on to creating a schedule. A schedule will tell you when you need to start shooting and when you need to finish. Every day will have a time for you to arrive at the location, leave when you are leaving and return home when you are done. Everyone knows exactly what they should do and when. Book extra staff ahead of time if you need them. It's not worth paying someone to show up if you haven't told him.
It is important to calculate the amount of filming days when you are creating your schedule. Some projects take only a few days while others can last several weeks. When you are creating your schedule, you should always keep in mind whether you need more than one shot per day or not. Multiple takes at the same place will result in higher costs and longer completion times. You can't be certain if you will need multiple takes so it is better not to shoot too many.
Budgeting is another crucial aspect of production plan. A realistic budget will help you work within your means. Keep in mind that you can always reduce your budget if you face unexpected difficulties. However, it is important not to overestimate the amount that you will spend. You'll end up with less money after paying for other things if the cost is underestimated.
Production planning is a complicated process. But once you understand how everything works together, it becomes much easier to plan future project.
Statistics
- It's estimated that 10.8% of the U.S. GDP in 2020 was contributed to manufacturing. (investopedia.com)
- Many factories witnessed a 30% increase in output due to the shift to electric motors. (en.wikipedia.org)
- According to the United Nations Industrial Development Organization (UNIDO), China is the top manufacturer worldwide by 2019 output, producing 28.7% of the total global manufacturing output, followed by the United States, Japan, Germany, and India.[52][53] (en.wikipedia.org)
- In 2021, an estimated 12.1 million Americans work in the manufacturing sector.6 (investopedia.com)
- In the United States, for example, manufacturing makes up 15% of the economic output. (twi-global.com)
External Links
How To
Six Sigma in Manufacturing
Six Sigma can be described as "the use of statistical process control (SPC), techniques to achieve continuous improvement." It was developed by Motorola's Quality Improvement Department at their plant in Tokyo, Japan, in 1986. Six Sigma's main goal is to improve process quality by standardizing processes and eliminating defects. Many companies have adopted this method in recent years. They believe there is no such thing a perfect product or service. Six Sigma's primary goal is to reduce variation from the average value of production. This means that you can take a sample from your product and then compare its performance to the average to find out how often the process differs from the norm. If you notice a large deviation, then it is time to fix it.
Understanding the nature of variability in your business is the first step to Six Sigma. Once you understand that, it is time to identify the sources of variation. You'll also want to determine whether these variations are random or systematic. Random variations occur when people make mistakes; systematic ones are caused by factors outside the process itself. You could consider random variations if some widgets fall off the assembly lines. But if you notice that every widget you make falls apart at the exact same place each time, this would indicate that there is a problem.
Once you've identified where the problems lie, you'll want to design solutions to eliminate those problems. The solution could involve changing how you do things, or redesigning your entire process. You should then test the changes again after they have been implemented. If they don’t work, you’ll need to go back and rework the plan.