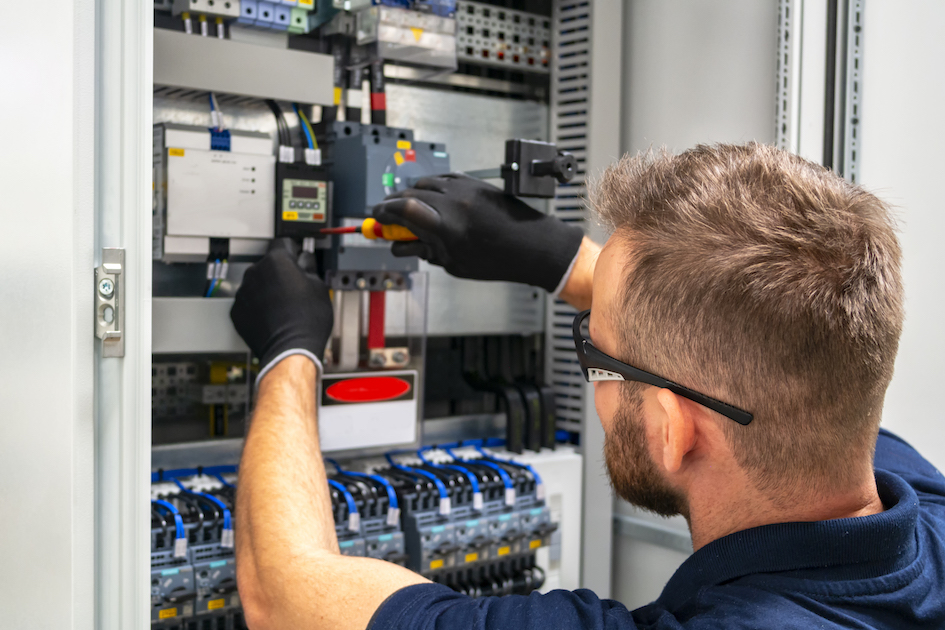
Continuous improvement is built on the principles of PDCA (Plan, Do, Check, Act). If it's done correctly, this method of improving can be highly effective and produce substantial results. Continuous improvement is only possible with employee involvement. This requires a range of resources. Although measurement and costs are crucial to the process they are not the only benefits. The PDCA cycle is not complete without the involvement of employees and customers.
PDCA cycle
Continuous improvement requires you to apply the PDCA cycles to every facet of your company. This cycle works by continuously improving a process and building on past improvements. The team may find new patterns in data, or they may discover a baseline. Both of these can reveal areas that need improvement. Although the PDCA cycle can be a powerful tool for identifying improvement opportunities it is important that you use it in a controlled and careful manner.
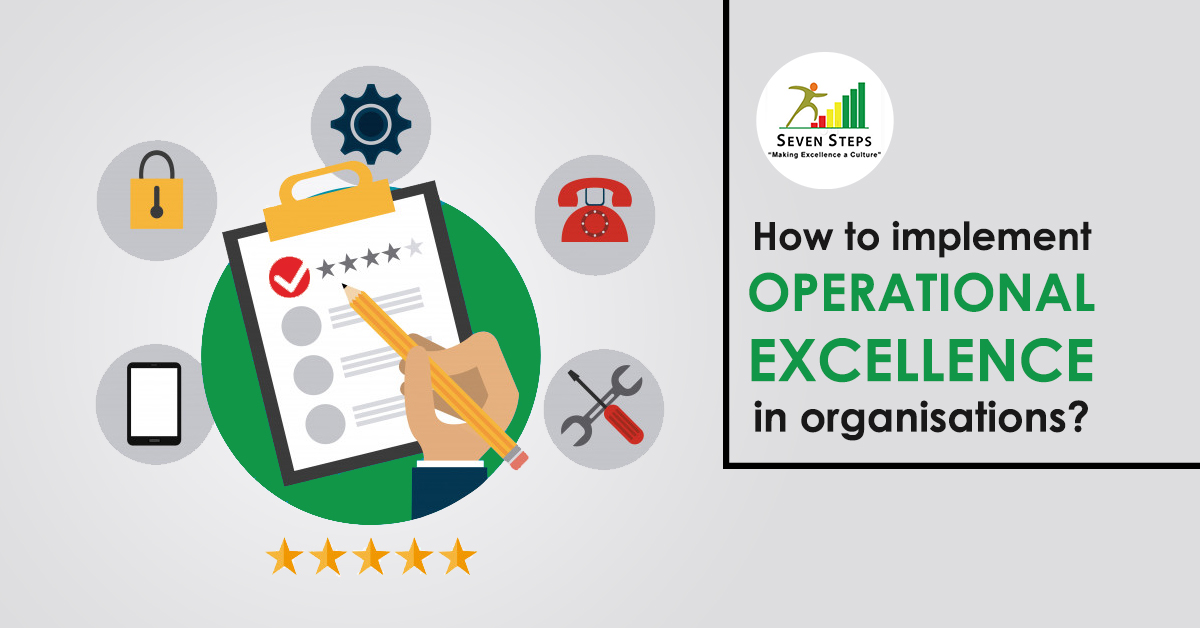
Employee involvement
Although employee involvement is often called many things, it is a concept that all organizations recognize as important. Research has shown that employee engagement is directly linked to positive work outcomes. There are four types of employee involvement. They can be classified as: representative participation through unions; direct communication; upward problem solving; and teamwork. These forms of employee involvement are often reinforced through the culture, environment, and leadership of an organization. Here are some examples of effective employee involvement practices.
Measuring
Many companies have begun to incorporate measurements in their continuous improvement plans. The Deming cycle, which was introduced by W. Edwards Deming, includes a Check phase that evaluates the progress of an improvement initiative against its objectives. If results are not as expected, the process is modified to make it better. The cycle is repeated unless the results are satisfactory. These processes are part of continuous improvement.
Costs
It is important to conduct an enterprise-wide cost assessment for CI efforts in order to determine if the benefits outweigh any potential costs. The cost-benefit analysis should be based on the business imperative of achieving the highest possible customer satisfaction and employee engagement scores. To ensure success, the cost-benefit analysis must also consider the ROI of CI initiatives as well as the fine-tuning budgets. The cost-benefit analysis should focus on improving the performance of key business processes and key performance areas by benchmarking them with leading competitors and industry averages.
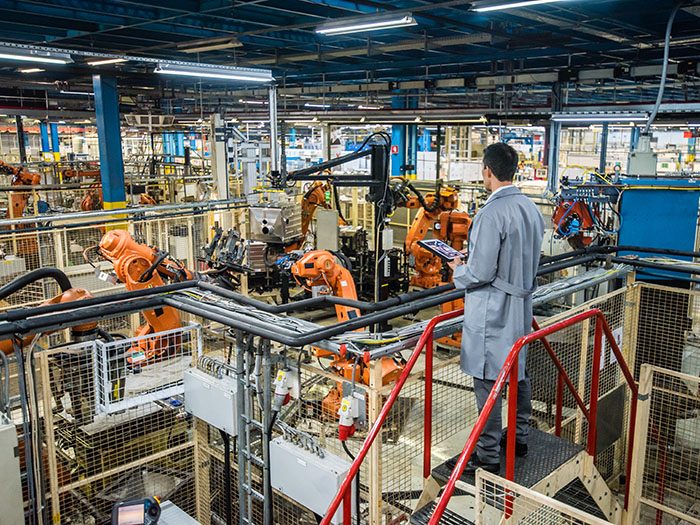
Benefits
Continuous improvement has many benefits. It is more likely that major breakthroughs will be achieved if the process is focused on learning and failing. Employees will feel more invested in the company if they are encouraged to look for ways to improve. Also, employees who are more involved in testing new technologies and tools might be empowered. You will also save money by focusing on continuous improvement. Successful changes increase employee satisfaction, and make employees' lives easier.
FAQ
What are the differences between these four types?
Manufacturing refers the process of turning raw materials into useful products with machines and processes. It can involve many activities like designing, manufacturing, testing packaging, shipping, selling and servicing.
How can manufacturing excess production be decreased?
Better inventory management is key to reducing excess production. This would reduce time spent on activities such as purchasing, stocking, and maintaining excess stock. We could use these resources to do other productive tasks.
Kanban systems are one way to achieve this. A Kanban board, a visual display to show the progress of work, is called a Kanban board. Work items are moved through various states to reach their destination in a Kanban system. Each state represents a different priority.
If work is moving from one stage to the other, then the current task can be completed and moved on to the next. It is possible to keep a task in the beginning stages until it gets to the end.
This helps to keep work moving forward while ensuring that no work is left behind. Managers can view the Kanban board to see how much work they have done. This allows them the ability to adjust their workflow using real-time data.
Lean manufacturing, another method to control inventory levels, is also an option. Lean manufacturing is about eliminating waste from all stages of the production process. Any product that isn't adding value can be considered waste. There are several types of waste that you might encounter:
-
Overproduction
-
Inventory
-
Unnecessary packaging
-
Overstock materials
These ideas will help manufacturers increase efficiency and lower costs.
What is production planning?
Production planning is the process of creating a plan that covers all aspects of production. This includes scheduling, budgeting and crew, location, equipment, props, and more. It is important to have everything ready and planned before you start shooting. It should also contain information on achieving the best results on set. This information includes locations, crew details and equipment requirements.
The first step is to outline what you want to film. You might have an idea of where you want to film, or you may have specific locations or sets in mind. Once you have determined your scenes and locations, it is time to start figuring out the elements that you will need for each scene. Perhaps you have decided that you need to buy a car but aren't sure which model. This is where you can look up car models online and narrow down your options by choosing from different makes and models.
Once you have found the right car, you can start thinking about extras. Do you need people sitting in the front seats? Or maybe you just need someone to push the car around. You might want to change your interior color from black and white. These questions will help determine the look and feel you want for your car. You can also think about the type of shots you want to get. Do you want to film close-ups, or wider angles? Maybe you want to show the engine and the steering wheel. These details will help identify the exact car you wish to film.
Once you have determined all of the above, you can move on to creating a schedule. You can use a schedule to determine when and where you need it to be shot. Every day will have a time for you to arrive at the location, leave when you are leaving and return home when you are done. This way, everyone knows what they need to do and when. Book extra staff ahead of time if you need them. You should not hire anyone who doesn't show up because of your inaction.
It is important to calculate the amount of filming days when you are creating your schedule. Some projects are quick and easy, while others take weeks. When creating your schedule, be aware of whether you need more shots per day. Multiple shots at the same location can increase costs and make it more difficult to complete. You can't be certain if you will need multiple takes so it is better not to shoot too many.
Budget setting is another important aspect in production planning. It is important to set a realistic budget so you can work within your budget. It is possible to reduce the budget at any time if you experience unexpected problems. However, you shouldn't overestimate the amount of money you will spend. Underestimating the cost will result in less money after you have paid for other items.
Production planning is a detailed process. But, once you understand the workings of everything, it becomes easier for future projects to be planned.
What is the difference between a production planner and a project manager?
A production planner is more involved in the planning phase of the project than a project manger.
What does manufacturing industry mean?
Manufacturing Industries are companies that manufacture products. The people who buy these products are called consumers. These companies use various processes such as production, distribution, retailing, management, etc., to fulfill this purpose. They make goods from raw materials with machines and other equipment. This covers all types of manufactured goods including clothing, food, building supplies and furniture, as well as electronics, tools, machinery, vehicles and pharmaceuticals.
What is the difference between Production Planning and Scheduling?
Production Planning (PP), or production planning, is the process by which you determine what products are needed at any given time. Forecasting demand is one way to do this.
Scheduling is the process of assigning specific dates to tasks so they can be completed within the specified timeframe.
Statistics
- [54][55] These are the top 50 countries by the total value of manufacturing output in US dollars for its noted year according to World Bank.[56] (en.wikipedia.org)
- Many factories witnessed a 30% increase in output due to the shift to electric motors. (en.wikipedia.org)
- In 2021, an estimated 12.1 million Americans work in the manufacturing sector.6 (investopedia.com)
- You can multiply the result by 100 to get the total percent of monthly overhead. (investopedia.com)
- Job #1 is delivering the ordered product according to specifications: color, size, brand, and quantity. (netsuite.com)
External Links
How To
How to Use 5S to Increase Productivity in Manufacturing
5S stands for "Sort", 'Set In Order", 'Standardize', & Separate>. Toyota Motor Corporation was the first to develop the 5S approach in 1954. It allows companies to improve their work environment, thereby achieving greater efficiency.
The idea behind standardizing production processes is to make them repeatable and measurable. This means that tasks such as cleaning, sorting, storing, packing, and labeling are performed daily. This knowledge allows workers to be more efficient in their work because they are aware of what to expect.
Implementing 5S involves five steps: Sort, Set in Order, Standardize Separate, Store, and Each step requires a different action to increase efficiency. Sorting things makes it easier to find them later. You arrange items by placing them in an order. Then, after you separate your inventory into groups, you store those groups in containers that are easy to access. Labeling your containers will ensure that everything is correctly labeled.
Employees need to reflect on how they do their jobs. Employees need to be able understand their motivations and discover alternative ways to do them. To implement the 5S system, employees must acquire new skills and techniques.
The 5S method increases efficiency and morale among employees. They will feel motivated to strive for higher levels of efficiency once they start to see results.