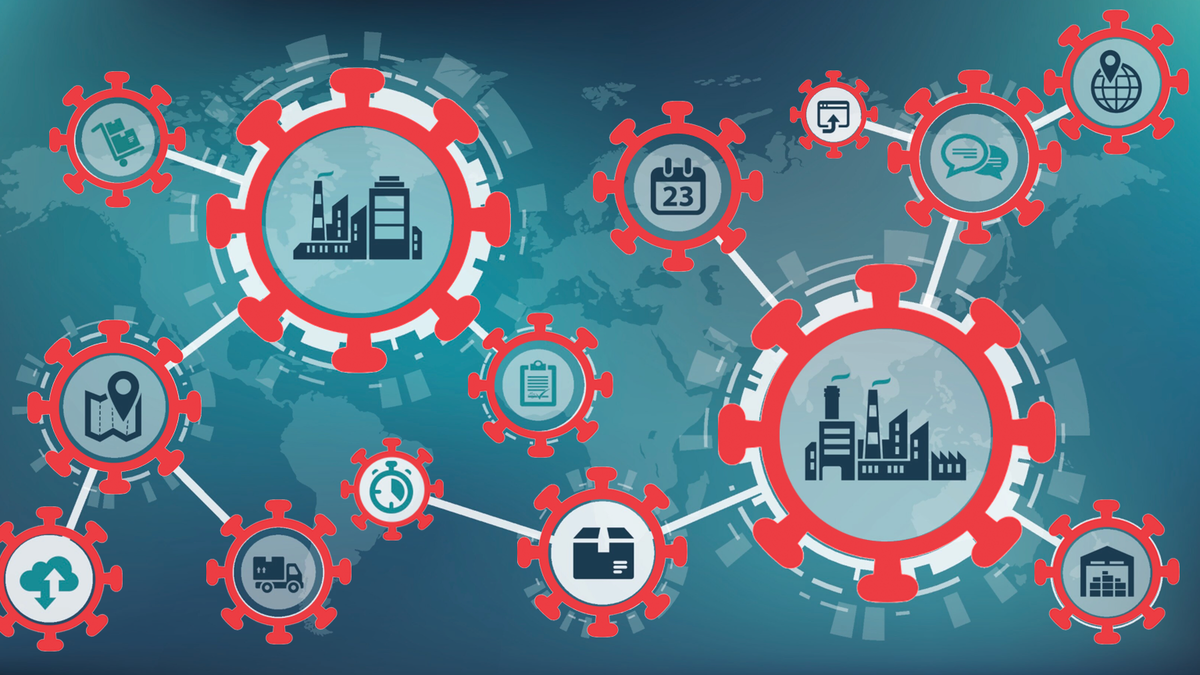
Industrial Engineering Managers play a vital role in the team, no matter if it's for a new project or routine work. They are responsible for directing staff and improving production output. This includes coordination of the factory floor layout and supervision of the implementation process and procedures. Aside from their technical expertise, they can help companies develop new products or processes.
They are responsible in developing and maintaining effective manufacturing processes. This requires an in-depth knowledge of current trends in automation, robotics, and other related technologies. They also need to monitor and maintain industrial procedures and ensure compliance to health and safety standards. They oversee the consumption of raw materials and consumables. They also do studies to optimize workflow and maximize space usage. The manager supervises all work projects including product cost reduction, cycle time and process improvement. They also manage preventative maintenance schedules.
This manager collaborates with other groups to develop new processes, improve efficiency, streamline operations, and create new partnerships. He or she is also responsible for the design and installation, as well as renovations to facilities. Managers communicate technical information to non-technical parties as part of the project management process. Additionally, the manager ensures that resources are available to teams and makes site visits at suppliers' facilities. He or she represents the team members and ensures compliance with quality guidelines.
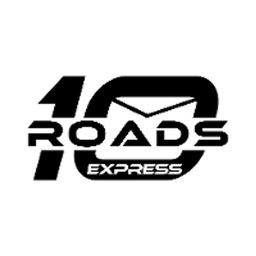
Industrial Engineering Managers must be highly motivated and creative to solve problems. They should be able work in both hot and cold environments and be physically fit to climb and walk for between 8 and 12 hours per day. In addition, they should be able interact with all levels.
A degree in engineering or another related field is necessary for industrial engineering managers. They must also have at minimum five years of relevant experience. Some employers prefer candidates with a postgraduate degree. They may also need to have specific skills, such as project management or logistics.
Managers in Industrial Engineering oversee the development and design of new products and processes. They have a strong background for problem-solving and quality improvements. They thrive in a collaborative atmosphere. Managers are more successful when they are able to encourage employee growth.
Industrial Engineers have the ability to streamline operations and reduce costs. They are well-versed in manufacturing processes and love meeting deadlines. They have extensive experience in recruiting, human resource, logistics, and vendor / Supplier relations. They can set goals, manage procedures, and create budgets. They can also plan strategies to improve efficiency of engineering projects.
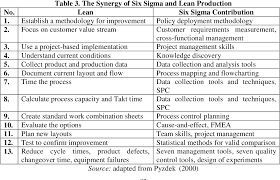
The Industrial Engineering Manager may be responsible to oversee the design and implementation new manufacturing processes or equipment. They have to create plans for new equipment, and operate according to existing guidelines and standards. They are responsible for overseeing the implementation of waste elimination plans. They are also responsible to assess the labor productivity in the factory.
Industrial Engineering Managers can help improve productivity and develop new products. They also have the expertise to manage human resources. They can also assist in improving the efficiency of existing processes.
FAQ
What are the products and services of logistics?
Logistics involves the transportation of goods from point A and point B.
They encompass all aspects transport, including packaging and loading, transporting, storage, unloading.
Logisticians ensure that the product is delivered to the correct place, at the right time, and under safe conditions. They help companies manage their supply chain efficiency by providing information on demand forecasts, stock levels, production schedules, and availability of raw materials.
They coordinate with vendors and suppliers, keep track of shipments, monitor quality standards and perform inventory and order replenishment.
What can I do to learn more about manufacturing?
Practical experience is the best way of learning about manufacturing. But if that is not possible you can always read books and watch educational videos.
Is automation important for manufacturing?
Automation is essential for both manufacturers and service providers. It enables them to provide services faster and more efficiently. It also helps to reduce costs and improve productivity.
What is the role of a production manager?
Production planners ensure all aspects of the project are delivered within time and budget. They ensure that the product or service is of high quality and meets client requirements.
Statistics
- You can multiply the result by 100 to get the total percent of monthly overhead. (investopedia.com)
- Many factories witnessed a 30% increase in output due to the shift to electric motors. (en.wikipedia.org)
- It's estimated that 10.8% of the U.S. GDP in 2020 was contributed to manufacturing. (investopedia.com)
- (2:04) MTO is a production technique wherein products are customized according to customer specifications, and production only starts after an order is received. (oracle.com)
- According to the United Nations Industrial Development Organization (UNIDO), China is the top manufacturer worldwide by 2019 output, producing 28.7% of the total global manufacturing output, followed by the United States, Japan, Germany, and India.[52][53] (en.wikipedia.org)
External Links
How To
Six Sigma in Manufacturing
Six Sigma is defined by "the application SPC (statistical process control) techniques to achieve continuous improvements." Motorola's Quality Improvement Department, Tokyo, Japan, developed it in 1986. Six Sigma's basic concept is to improve quality and eliminate defects through standardization. This method has been adopted by many companies in recent years as they believe there are no perfect products or services. Six Sigma's primary goal is to reduce variation from the average value of production. It is possible to measure the performance of your product against an average and find the percentage of time that it differs from the norm. If you notice a large deviation, then it is time to fix it.
Understanding the dynamics of variability within your business is the first step in Six Sigma. Once you have a good understanding of the basics, you can identify potential sources of variation. These variations can also be classified as random or systematic. Random variations occur when people do mistakes. Symmetrical variations are caused due to factors beyond the process. For example, if you're making widgets, and some of them fall off the assembly line, those would be considered random variations. However, if you notice that every time you assemble a widget, it always falls apart at exactly the same place, then that would be a systematic problem.
Once you've identified where the problems lie, you'll want to design solutions to eliminate those problems. That solution might involve changing the way you do things or redesigning the process altogether. After implementing the new changes, you should test them again to see if they worked. If they didn't work, then you'll need to go back to the drawing board and come up with another plan.