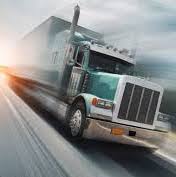
If you want to lower costs, increase lead times, and reduce set-up time and turnaround time while also reducing setup and turn-around time, lean manufacturing may be for you. Lean manufacturing offers many benefits. It reduces costs and leads time, while improving customer satisfaction. Lean manufacturing is a great way to grow your business. If you're still not convinced, read on for three reasons why it's the best way to make products and cut costs:
Reduces costs
Lean manufacturing can lead to significant efficiencies. Lean manufacturing can help manufacturers save money by reducing labor costs and reducing defects. This makes labor costs less motivating in decision-making. Eliminating hazardous waste is another advantage. The cost of direct labor in many industries is less than 15%. This makes outsourcing to low-cost areas more difficult. This can help reduce manufacturing costs and improve customer service.
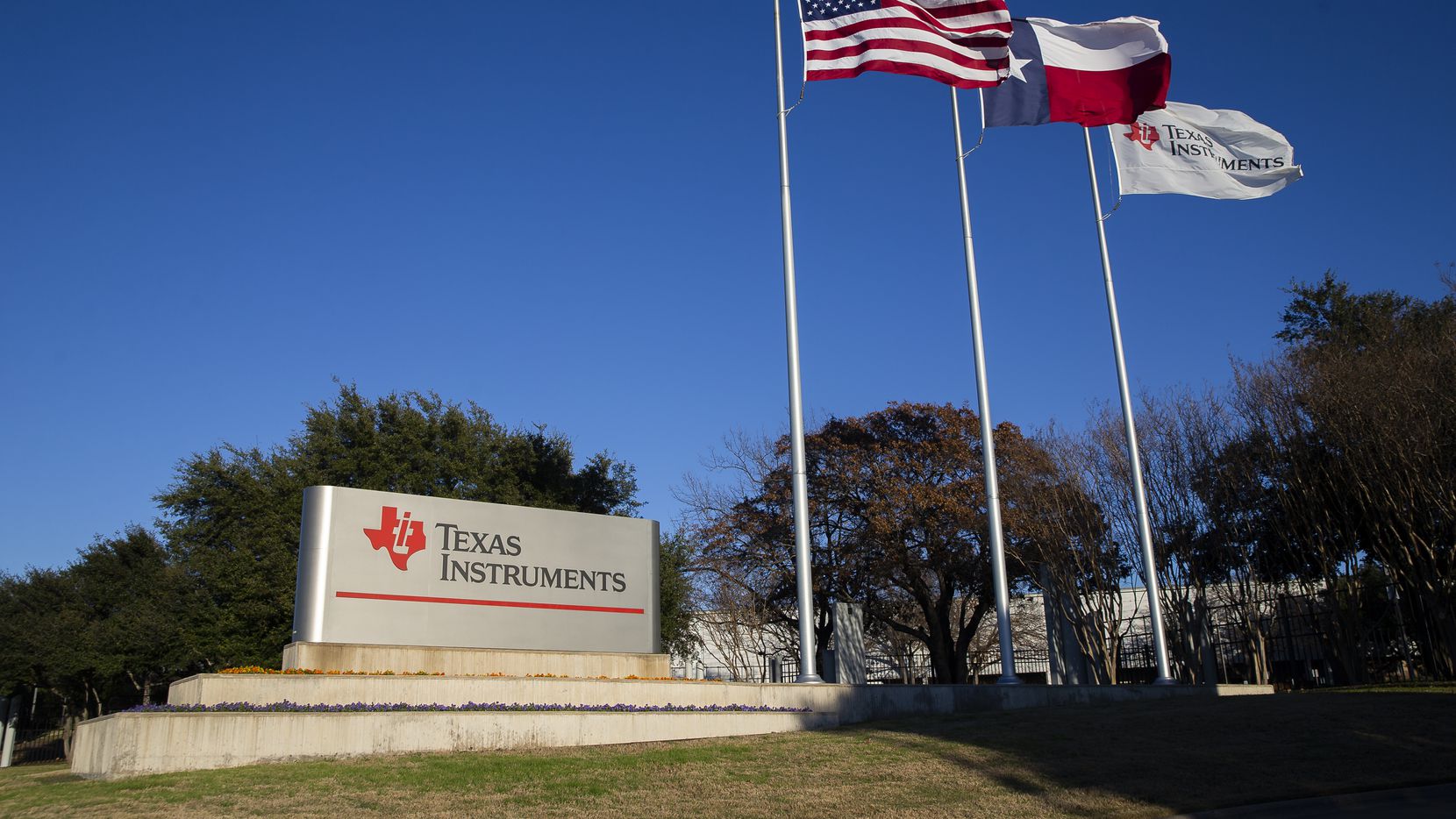
Improves lead times
There are many benefits to using lean manufacturing. These include the ability to reduce waste, improve lead times and lower costs. It is a philosophy that promotes continuous improvement, or "kaizen". It combines the talents of employees and encourages collaboration and accountability. The process can decrease lead times by as high as 20% Lean manufacturing's most important feature is its ability to make small, but significant improvements to product quality and efficiency.
Shortens set-up times
It is possible to reduce the time taken to create a product by reducing setup times. Setup time is the time taken to move from the last product on an order to the next good item. Setting up time covers preparation, replacement, location, and other activities. These activities can be either internal or external. While some activities such as the moving of a machine or placing an item requires an inactive process to be completed, others can be carried out while the process continues to operate.
Reduces time to market
The concept of Lean manufacturing, or the process of continuous improvement, was developed in Japan during the rebuilding period after World War II. It was developed to improve competition and reduce lead time. By shortening the time it takes for a product to reach the market, companies can meet customer demands and increase profitability. This production approach can improve the efficiency of the manufacturing process and make the facility more efficient.
Improves product quality
The process of reducing waste, improving product quality, and minimizing costs are all important to the success of lean manufacturing. It has been used by many companies, large and small. It can reduce lead time, cost, as well as labor. Continue reading to learn more about how lean manufacturing can help your business. Here are some areas that you need to be focused on. Lean principles will reduce lead time by 90% and increase product quality. It can also reduce costs.
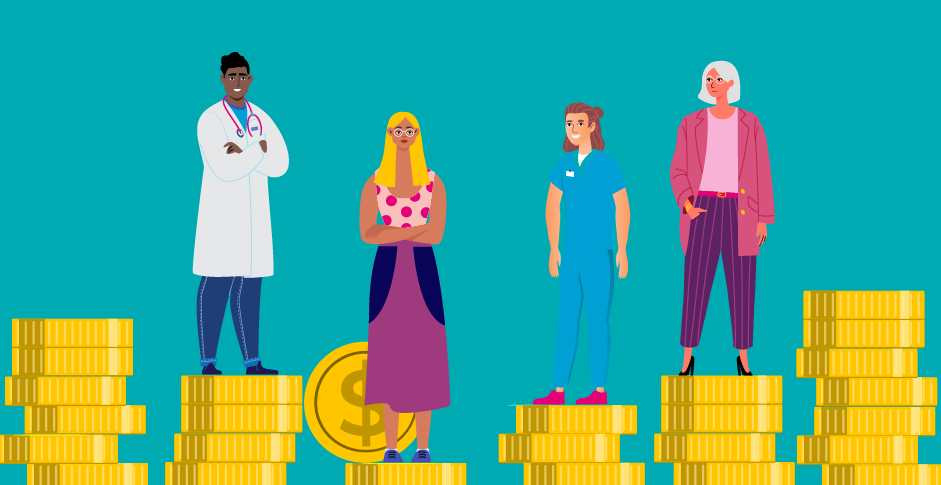
Indirect labor costs are reduced
Lean manufacturing's low hanging fruit is the reduction of indirect labor cost. True lean companies pay scant attention to direct labor efficiency and instead look for ways to cut indirect labor costs. This means eliminating material handling and inspection jobs. Toyota and other lean manufacturers use this same approach. This article will examine how lean manufacturing helps lower indirect labor costs.
FAQ
What are the 7 Rs of logistics.
The acronym 7R's of Logistic is an acronym that stands for seven fundamental principles of logistics management. It was developed and published by the International Association of Business Logisticians in 2004 as part of the "Seven Principles of Logistics Management".
The following letters form the acronym:
-
Responsible – ensure that all actions are legal and don't cause harm to anyone else.
-
Reliable - Have confidence in your ability to fulfill all of your commitments.
-
Use resources effectively and sparingly.
-
Realistic - Consider all aspects of operations, including environmental impact and cost effectiveness.
-
Respectful – Treat others fairly and equitably.
-
Be resourceful: Look for opportunities to save money or increase productivity.
-
Recognizable provides value-added products and services to customers
What are manufacturing and logistics?
Manufacturing refers the process of producing goods from raw materials through machines and processes. Logistics includes all aspects related to supply chain management, such as procurement, distribution planning, inventory control and transportation. Sometimes manufacturing and logistics are combined to refer to a wider term that includes both the process of creating products as well as their delivery to customers.
What are the responsibilities of a logistic manager?
Logistics managers make sure all goods are delivered on schedule and without damage. This is accomplished by using the experience and knowledge gained from working with company products. He/she should make sure that enough stock is on hand to meet the demands.
What is the role and responsibility of a Production Planner?
Production planners ensure that all project aspects are completed on time, within budget and within the scope. A production planner ensures that the service and product meet the client's expectations.
Statistics
- It's estimated that 10.8% of the U.S. GDP in 2020 was contributed to manufacturing. (investopedia.com)
- Job #1 is delivering the ordered product according to specifications: color, size, brand, and quantity. (netsuite.com)
- (2:04) MTO is a production technique wherein products are customized according to customer specifications, and production only starts after an order is received. (oracle.com)
- In the United States, for example, manufacturing makes up 15% of the economic output. (twi-global.com)
- According to a Statista study, U.S. businesses spent $1.63 trillion on logistics in 2019, moving goods from origin to end user through various supply chain network segments. (netsuite.com)
External Links
How To
Six Sigma in Manufacturing
Six Sigma is "the application statistical process control (SPC), techniques for continuous improvement." Motorola's Quality Improvement Department created Six Sigma at their Tokyo plant, Japan in 1986. The basic idea behind Six Sigma is to improve quality by improving processes through standardization and eliminating defects. Many companies have adopted Six Sigma in recent years because they believe that there are no perfect products and services. Six Sigma's main objective is to reduce variations from the production average. It is possible to measure the performance of your product against an average and find the percentage of time that it differs from the norm. If it is too large, it means that there are problems.
The first step toward implementing Six Sigma is understanding how variability works in your business. Once you have a good understanding of the basics, you can identify potential sources of variation. These variations can also be classified as random or systematic. Random variations are caused when people make mistakes. While systematic variations are caused outside of the process, they can occur. For example, if you're making widgets, and some of them fall off the assembly line, those would be considered random variations. If however, you notice that each time you assemble a widget it falls apart in exactly the same spot, that is a problem.
Once you've identified the problem areas you need to find solutions. It might mean changing the way you do business or redesigning it entirely. After implementing the new changes, you should test them again to see if they worked. If they didn't work, then you'll need to go back to the drawing board and come up with another plan.