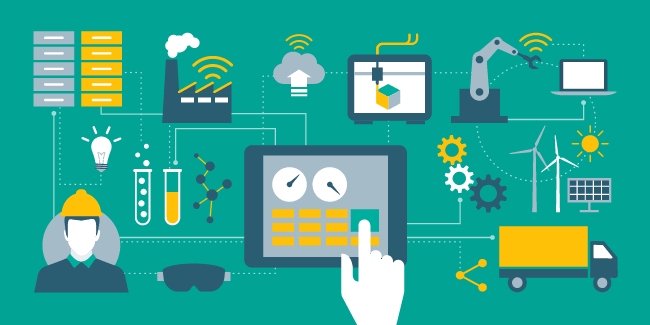
Lean 5 principles emphasize the elimination of waste, including those that do not add value to the product. They also encourage value stream mapping to identify areas that can be performed more efficiently. The key to eliminating waste is to separate value-added, (necessary), waste from non-value added (unnecessary). The most efficient process uses less energy, time and materials by eliminating redundant steps. This ensures that customers are satisfied and high quality products are produced in the shortest time possible.
Valuable
The Value of lean 5 principles will help you improve manufacturing flow by eliminating waste. You can improve the flow of production from manufacturing to shipping by removing steps that don't add value. This eliminates inventory that is not needed and allows you to reduce your work and save time.
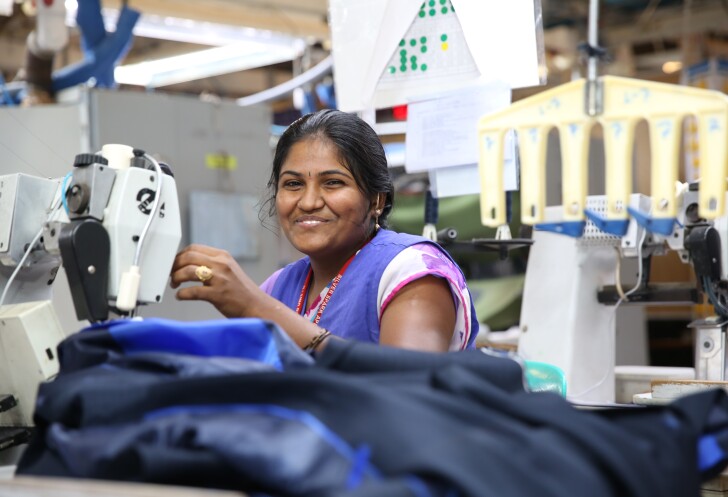
Value stream
The value stream in lean manufacturing is a technique to eliminate waste from manufacturing processes. This process maps out each step in a process to identify the elements that are necessary and eliminate those that are not. The entire value stream is the product's entire life cycle, including its creation and use. This is how you eliminate waste. There are three types or wastes in a value-stream.
Flow
The first principle of lean 5, Flow, is to identify and evaluate the customer's actual needs. This is an important step in the design process for new products and/or services. Customers do not always articulate their needs clearly. The second step involves defining the value stream or the sequence of activities that will complete a project. This requires close collaboration among all project participants.
Pull
In a pull system, the process begins only when there is an order from a customer. A pizza joint would not make extra pizzas without a customer order. Otherwise, they would be wasting time, resources, and ingredients.
Perfection
One of 5 principles of lean is the pursuit for perfection. According to this concept perfection is an ideal state which is accurate, complete, and consistent. It is impossible to achieve perfection. This concept encourages continuous improvement. The result is a better performance for organizations.
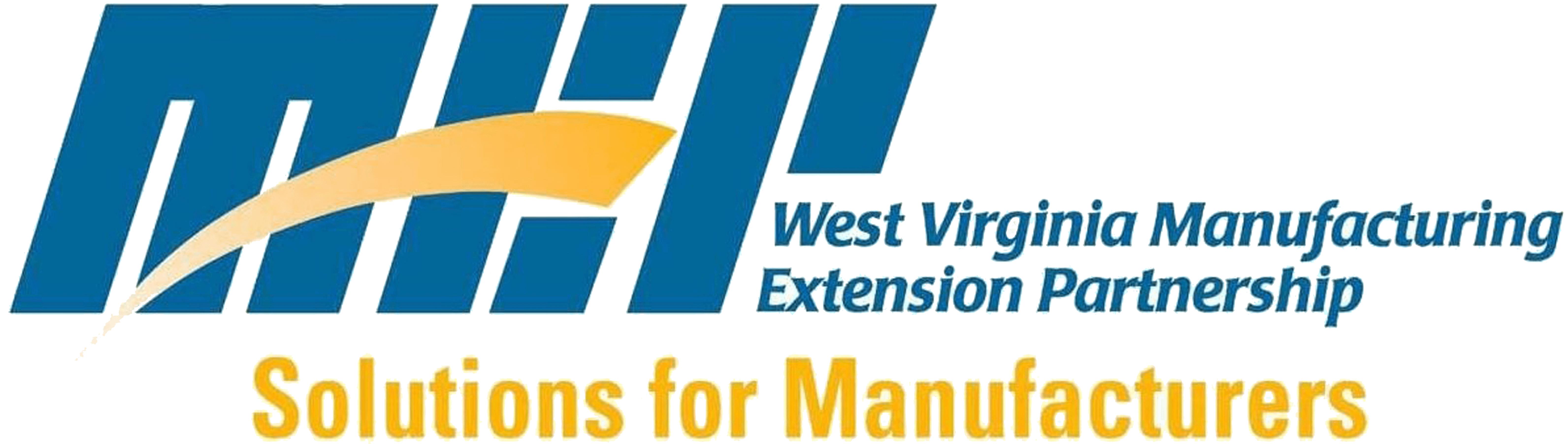
Collaborative efforts of all stakeholders
Stakeholder collaboration is a key element of lean project management. Collaboration between project team members is essential to solving problems and increasing project value. Teams need to identify potential problems and areas for improvement during the planning stage. The doing stage is more about data gathering and execution than it is about executing. The team should also consider the organizational structure for collaboration.
FAQ
Can certain manufacturing steps be automated?
Yes! Yes. Automation has been around since ancient time. The Egyptians created the wheel thousands years ago. We now use robots to help us with assembly lines.
There are many uses of robotics today in manufacturing. They include:
-
Automation line robots
-
Robot welding
-
Robot painting
-
Robotics inspection
-
Robots that create products
Automation can be applied to manufacturing in many other ways. For instance, 3D printing allows us make custom products and not have to wait for months or even weeks to get them made.
What skills does a production planner need?
A production planner must be organized, flexible, and able multitask to succeed. Also, you must be able and willing to communicate with clients and coworkers.
What does manufacturing mean?
Manufacturing Industries refers to businesses that manufacture products. These products are sold to consumers. These companies use a variety processes such as distribution, retailing and management to accomplish their purpose. They make goods from raw materials with machines and other equipment. This includes all types and varieties of manufactured goods, such as food items, clothings, building supplies, furnitures, toys, electronics tools, machinery vehicles, pharmaceuticals medical devices, chemicals, among others.
What makes a production planner different from a project manger?
The primary difference between a producer planner and a manager of a project is that the manager usually plans and organizes the whole project, while a production planner is only involved in the planning stage.
What is the role of a logistics manager
A logistics manager ensures that all goods are delivered on time and without damage. This is done by using his/her experience and knowledge of the company's products. He/she should also ensure enough stock is available to meet demand.
What are the logistics products?
Logistics involves the transportation of goods from point A and point B.
They cover all aspects of transportation, such as packing, loading, transporting and unloading.
Logisticians ensure that the right product reaches the right place at the right time and under safe conditions. They help companies manage their supply chain efficiency by providing information on demand forecasts, stock levels, production schedules, and availability of raw materials.
They keep track and monitor the transit of shipments, maintain quality standards, order replenishment and inventories, coordinate with suppliers, vendors, and provide support for sales and marketing.
How can manufacturing reduce production bottlenecks?
Avoiding production bottlenecks is as simple as keeping all processes running smoothly, from the time an order is received until the product ships.
This includes planning for both capacity requirements and quality control measures.
Continuous improvement techniques like Six Sigma are the best way to achieve this.
Six Sigma can be used to improve the quality and decrease waste in all areas of your company.
It is focused on creating consistency and eliminating variation in your work.
Statistics
- In 2021, an estimated 12.1 million Americans work in the manufacturing sector.6 (investopedia.com)
- (2:04) MTO is a production technique wherein products are customized according to customer specifications, and production only starts after an order is received. (oracle.com)
- [54][55] These are the top 50 countries by the total value of manufacturing output in US dollars for its noted year according to World Bank.[56] (en.wikipedia.org)
- According to a Statista study, U.S. businesses spent $1.63 trillion on logistics in 2019, moving goods from origin to end user through various supply chain network segments. (netsuite.com)
- Many factories witnessed a 30% increase in output due to the shift to electric motors. (en.wikipedia.org)
External Links
How To
How to use Lean Manufacturing in the production of goods
Lean manufacturing is an approach to management that aims for efficiency and waste reduction. It was created in Japan by Taiichi Ohno during the 1970s and 80s. He received the Toyota Production System award (TPS), from Kanji Toyoda, founder of TPS. The first book published on lean manufacturing was titled "The Machine That Changed the World" written by Michael L. Watkins and published in 1990.
Lean manufacturing, often described as a set and practice of principles, is aimed at improving the quality, speed, cost, and efficiency of products, services, and other activities. It emphasizes reducing defects and eliminating waste throughout the value chain. Just-in-time (JIT), zero defect (TPM), and 5S are all examples of lean manufacturing. Lean manufacturing seeks to eliminate non-value added activities, such as inspection, work, waiting, and rework.
Lean manufacturing not only improves product quality but also reduces costs. Companies can also achieve their goals faster by reducing employee turnover. Lean manufacturing can be used to manage all aspects of the value chain. Customers, suppliers, distributors, retailers and employees are all included. Lean manufacturing practices are widespread in many industries. For example, Toyota's philosophy underpins its success in automobiles, electronics, appliances, healthcare, chemical engineering, aerospace, paper, food, etc.
Five basic principles of Lean Manufacturing are included in lean manufacturing
-
Define Value: Identify the social value of your business and what sets you apart.
-
Reduce Waste – Eliminate all activities that don't add value throughout the supply chain.
-
Create Flow - Ensure work moves smoothly through the process without interruption.
-
Standardize and simplify – Make processes as repeatable and consistent as possible.
-
Build relationships - Develop and maintain personal relationships with both your internal and external stakeholders.
Lean manufacturing isn’t new, but it has seen a renewed interest since 2008 due to the global financial crisis. Many companies have adopted lean manufacturing methods to increase their marketability. Economists think that lean manufacturing is a crucial factor in economic recovery.
Lean manufacturing is becoming a popular practice in automotive. It has many advantages. These include higher customer satisfaction levels, reduced inventory levels as well as lower operating costs.
Any aspect of an enterprise can benefit from Lean manufacturing. Lean manufacturing is most useful in the production sector of an organisation because it ensures that each step in the value-chain is efficient and productive.
There are three types principally of lean manufacturing:
-
Just-in-Time Manufacturing: Also known as "pull systems", this type of lean manufacturing uses just-in-time manufacturing (JIT). JIT means that components are assembled at the time of use and not manufactured in advance. This method reduces lead times, increases availability, and decreases inventory.
-
Zero Defects Manufacturing, (ZDM): ZDM is focused on ensuring that no defective products leave the manufacturing facility. Repairing a part that is damaged during assembly should be done, not scrapping. This applies to finished products, which may need minor repairs before they are shipped.
-
Continuous Improvement (CI: Continuous improvement aims to increase the efficiency of operations by constantly identifying and making improvements to reduce or eliminate waste. Continuous Improvement involves continuous improvement of processes.