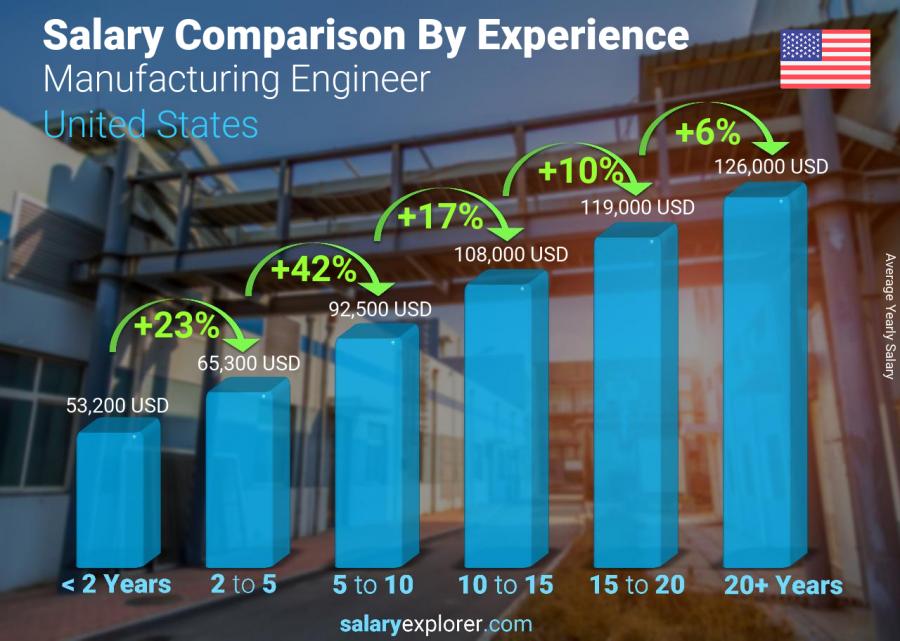
A validation engineer salary is a person's pay for working as a validity engineer. The amount they receive is usually based on experience, education, and skills. It can be affected by their job and company.
What is the role of a validation engineer?
Validation engineers are engineering professionals who use equipment, procedures and processes to monitor product quality. They work in manufacturing and testing environments, as well as research and development.
What is a Validation engineer's job?
A validation engineer monitors equipment and system performance used in manufacturing pharmaceutical products. In order to do so, the engineers analyze, inspect and test equipment and machines. The engineers also look into any anomalies and malfunctions that might lead to the failure of a product.
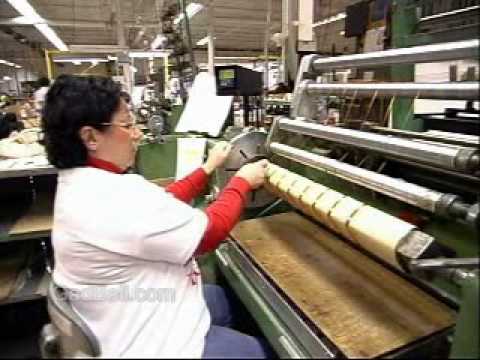
What does a Validation Engineer Salary look like?
A Validation Engineer salary is usually high, but it depends upon the type of company that you work for. Apple and Google are two companies that pay the highest salaries in the technology sector. In the pharmaceutical industry these engineers are expected to make on average $89130 per year.
What are the common skills needed for this career?
The skills needed for a validation engineer career include an ability to write, execute and coordinate commissioning and qualification protocols. It is also important that they have good technical knowledge about manufacturing, software, and process engineering.
How to Become a Validation Engineer
You can become a validation engineer in a number of ways, including by earning a degree and/or through an apprenticeship. Employers require that candidates hold a bachelor's in a relevant discipline of engineering, such electrical, mechanical or computer software.
You can then gain valuable experience by participating in a graduate-level engineering program or an internship. Find jobs online, through newspapers and recruitment agencies.
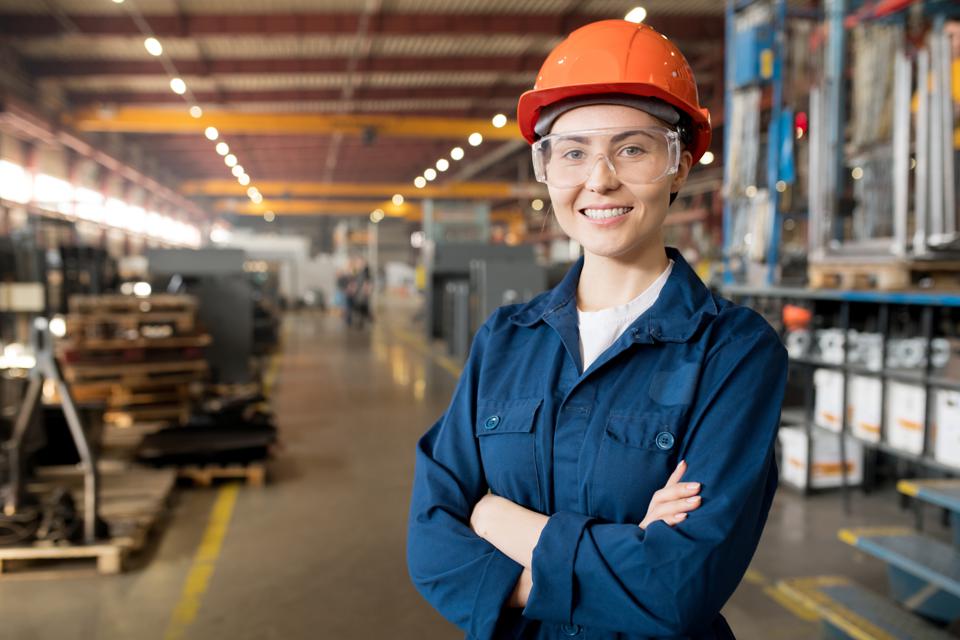
How to Become a Pharmaceutical Validation Engineer
For a career as a validation engineering, the right combination is required of academic qualifications and experience. A degree in science, engineering or pharmacology is required. It is not an easy path, but you should persevere to find a career that fits your qualifications.
How to Be a Validation Engineer for Pharma
Validation engineers have a defined career path, with positions at different levels of responsibility. Senior engineers have managerial responsibilities and can travel internationally. You can also take on roles that will allow you to specialize in a certain field, like CSV or drugs delivery technologies.
Salary can vary for a validation engineer in pharmaceuticals depending on what industry they are working in and which products they deal with. The average salary for pharmaceutical validation engineers in the United States is $98,150. But some cities have higher salaries than others. Hayward, CA for instance, is $18,034 higher than the national average, while San Jose, CA comes in at number one with $21,856.
FAQ
What is the distinction between Production Planning or Scheduling?
Production Planning (PP), also known as forecasting and identifying production capacities, is the process that determines what product needs to be produced at any particular time. This can be done by forecasting demand and identifying production capabilities.
Scheduling involves the assignment of dates and times to tasks in order to complete them within the timeframe.
What does warehouse mean?
A warehouse or storage facility is where goods are stored before they are sold. It can be either an indoor or outdoor space. It could be one or both.
How can manufacturing efficiency improved?
First, identify the factors that affect production time. Then we need to find ways to improve these factors. If you aren't sure where to begin, think about the factors that have the greatest impact on production time. Once you have identified the factors, then try to find solutions.
What are the four types of manufacturing?
Manufacturing refers to the transformation of raw materials into useful products by using machines and processes. It includes many different activities like designing, building and testing, packaging, shipping and selling, as well as servicing.
Why is logistics important for manufacturing?
Logistics is an integral part of every business. They enable you to achieve outstanding results by helping manage product flow from raw materials through to finished goods.
Logistics also play a major role in reducing costs and increasing efficiency.
Statistics
- According to a Statista study, U.S. businesses spent $1.63 trillion on logistics in 2019, moving goods from origin to end user through various supply chain network segments. (netsuite.com)
- (2:04) MTO is a production technique wherein products are customized according to customer specifications, and production only starts after an order is received. (oracle.com)
- It's estimated that 10.8% of the U.S. GDP in 2020 was contributed to manufacturing. (investopedia.com)
- Many factories witnessed a 30% increase in output due to the shift to electric motors. (en.wikipedia.org)
- Job #1 is delivering the ordered product according to specifications: color, size, brand, and quantity. (netsuite.com)
External Links
How To
How to Use Lean Manufacturing in the Production of Goods
Lean manufacturing refers to a method of managing that seeks to improve efficiency and decrease waste. It was developed in Japan during the 1970s and 1980s by Taiichi Ohno, who received the Toyota Production System (TPS) award from TPS founder Kanji Toyoda. Michael L. Watkins published the book "The Machine That Changed the World", which was the first to be published about lean manufacturing.
Lean manufacturing refers to a set of principles that improve the quality, speed and costs of products and services. It emphasizes the elimination and minimization of waste in the value stream. Lean manufacturing is also known as just in time (JIT), zero defect total productive maintenance(TPM), and five-star (S). Lean manufacturing is about eliminating activities that do not add value, such as inspection, rework, and waiting.
Lean manufacturing can help companies improve their product quality and reduce costs. Additionally, it helps them achieve their goals more quickly and reduces employee turnover. Lean manufacturing is considered one of the most effective ways to manage the entire value chain, including suppliers, customers, distributors, retailers, and employees. Lean manufacturing practices are widespread in many industries. Toyota's philosophy has been a key driver of success in many industries, including automobiles and electronics.
Five basic principles of Lean Manufacturing are included in lean manufacturing
-
Define Value - Identify the value your business adds to society and what makes you different from competitors.
-
Reduce waste - Get rid of any activity that does not add value to the supply chain.
-
Create Flow - Make sure work runs smoothly without interruptions.
-
Standardize and simplify – Make processes as repeatable and consistent as possible.
-
Build Relationships- Develop personal relationships with both internal as well as external stakeholders.
Lean manufacturing isn’t new, but it has seen a renewed interest since 2008 due to the global financial crisis. Many businesses are now using lean manufacturing to improve their competitiveness. Many economists believe lean manufacturing will play a major role in economic recovery.
Lean manufacturing is now becoming a common practice in the automotive industry, with many benefits. These include higher customer satisfaction levels, reduced inventory levels as well as lower operating costs.
Lean manufacturing can be applied to almost every aspect of an organization. Because it makes sure that all value chains are efficient and effectively managed, Lean Manufacturing is particularly helpful for organizations.
There are three main types:
-
Just-in Time Manufacturing: This lean manufacturing method is commonly called "pull systems." JIT refers to a system in which components are assembled at the point of use instead of being produced ahead of time. This method reduces lead times, increases availability, and decreases inventory.
-
Zero Defects Manufacturing (ZDM): ZDM focuses on ensuring that no defective units leave the manufacturing facility. If a part is required to be repaired on the assembly line, it should not be scrapped. This is also true for finished products that require minor repairs before shipping.
-
Continuous Improvement (CI),: Continuous improvement aims improve the efficiency and effectiveness of operations by continuously identifying issues and making changes to reduce waste. Continuous Improvement involves continuous improvement of processes.