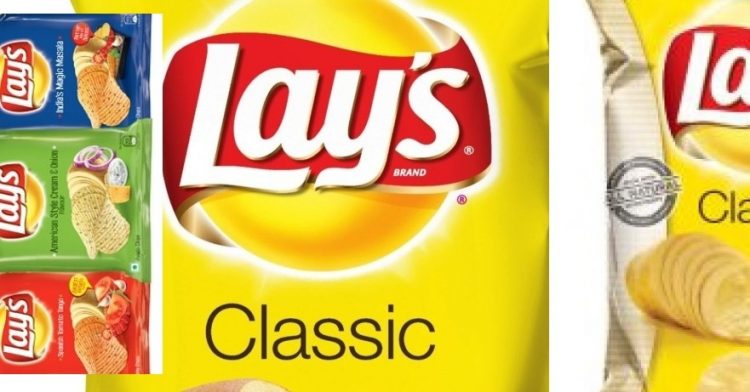
It can be intimidating to enter the logistics field. Some people will need to take extra courses or intern before they can start their new job. Good news is that you can find entry-level jobs in logistics to help get your foot in this field.
Most of these positions require an associate's degree, but a bachelor's degree is also beneficial. You will gain a deeper understanding of the supply chain. A degree is a prerequisite for professional certifications. Online classes are also available in specialized subjects. Sometimes, reimbursements may be available for graduate programs.
Entry level logistics jobs can be found in a variety of industries. For instance, you can work in aerospace manufacturing, oil and gas, or in a freight transportation arrangement. International opportunities exist in many different industries.
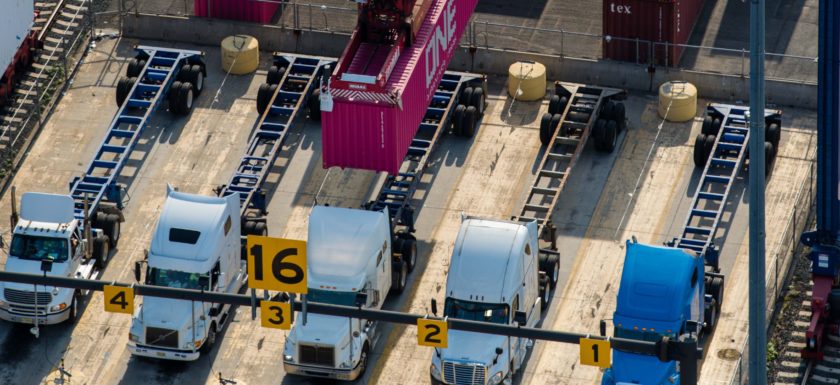
Logistics professionals are able to use both their intellects and both their hands to solve problems. They use their skills to create sustainable supply chains. They can influence both the executive as well as the operational decision-making processes. This job can be difficult, but rewarding. The logistics industry is growing quickly in a booming market.
Strong leadership and management skills are essential for logistics workers. They also need to be able to communicate effectively. They also need to be able use specialized software. They could be responsible for finding storage spaces near shipping ports. They may also be responsible to make sure that the goods are cleared at customs.
Logistics is continuously evolving. The industry is constantly changing with new technologies and business models. It's important to have an understanding of these changes. A bachelor's degree will help you become a well-rounded logistics professional. This degree will also allow you to develop a professional network. Participation in industry conferences and seminars is also possible. An accredited institution can also award your degree.
A variety of administrative roles are available, and require communication and analytical skills. Some of these roles may be within the company itself, while others may involve customers, suppliers, or other business functions.
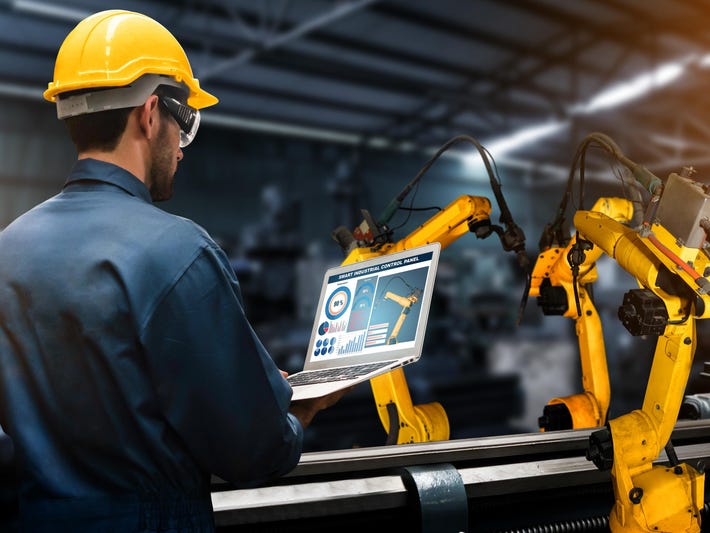
If you are looking to start a career in logistics, consider becoming a member of an industry association. These associations can provide information on professional certifications, industry news and job boards. They may also be able to help you find a mentor. Some of these organizations even offer graduate fellowship positions for students.
Numerous countries also offer vocational certificates, which do not require any prior logistics experience. These certifications will be highly valued by businesses with in-house transportation fleets. An additional certificate that can be obtained is the Certificate of Professional Competence In Road Transport Operations. This certification is highly sought after by businesses with in house transportation fleets.
Entry level logistics jobs can be found throughout the nation. There are also a variety of online resources for job hunters. You can also use your social network to help you.
FAQ
What is the job of a logistics manger?
Logistics managers make sure all goods are delivered on schedule and without damage. This is done using his/her knowledge of the company's products. He/she must also ensure sufficient stock to meet the demand.
What is the best way to learn about manufacturing?
Experience is the best way for you to learn about manufacturing. You can also read educational videos or take classes if this isn't possible.
How can manufacturing efficiency improved?
First, determine which factors have the greatest impact on production time. Then we need to find ways to improve these factors. If you aren't sure where to begin, think about the factors that have the greatest impact on production time. Once you have identified the factors, then try to find solutions.
What does "warehouse" mean?
A warehouse or storage facility is where goods are stored before they are sold. It can be either an indoor or outdoor space. It could be one or both.
What is the responsibility of a production planner?
Production planners ensure all aspects of the project are delivered within time and budget. They also ensure the quality of the product and service meets the client's requirements.
How can overproduction in manufacturing be reduced?
The key to reducing overproduction lies in developing better ways to manage inventory. This would reduce the time spent on unproductive activities like purchasing, storing and maintaining excess stock. This would allow us to use our resources for more productive tasks.
This can be done by using a Kanban system. A Kanban board can be used to monitor work progress. In a Kanban system, work items move through a sequence of states until they reach their final destination. Each state represents an individual priority level.
As an example, if work is progressing from one stage of the process to another, then the current task is complete and can be transferred to the next. But if a task remains in the beginning stages it will stay that way until it reaches its end.
This allows you to keep work moving along while making sure that no work gets neglected. With a Kanban board, managers can see exactly how much work is being done at any given moment. This information allows them to adjust their workflow based on real-time data.
Another way to control inventory levels is to implement lean manufacturing. Lean manufacturing emphasizes eliminating waste in all phases of production. Anything that does nothing to add value to a product is waste. These are some of the most common types.
-
Overproduction
-
Inventory
-
Unnecessary packaging
-
Materials in excess
Manufacturers can reduce their costs and improve their efficiency by using these ideas.
Statistics
- [54][55] These are the top 50 countries by the total value of manufacturing output in US dollars for its noted year according to World Bank.[56] (en.wikipedia.org)
- In 2021, an estimated 12.1 million Americans work in the manufacturing sector.6 (investopedia.com)
- According to a Statista study, U.S. businesses spent $1.63 trillion on logistics in 2019, moving goods from origin to end user through various supply chain network segments. (netsuite.com)
- Job #1 is delivering the ordered product according to specifications: color, size, brand, and quantity. (netsuite.com)
- In the United States, for example, manufacturing makes up 15% of the economic output. (twi-global.com)
External Links
How To
Six Sigma: How to Use it in Manufacturing
Six Sigma refers to "the application and control of statistical processes (SPC) techniques in order to achieve continuous improvement." Motorola's Quality Improvement Department created Six Sigma at their Tokyo plant, Japan in 1986. Six Sigma's core idea is to improve the quality of processes by standardizing and eliminating defects. Since there are no perfect products, or services, this approach has been adopted by many companies over the years. The main goal of Six Sigma is to reduce variation from the mean value of production. You can calculate the percentage of deviation from the norm by taking a sample of your product and comparing it to the average. If this deviation is too big, you know something needs fixing.
Understanding how variability works in your company is the first step to Six Sigma. Once you understand this, you can then identify the causes of variation. You'll also want to determine whether these variations are random or systematic. Random variations occur when people do mistakes. Symmetrical variations are caused due to factors beyond the process. These are, for instance, random variations that occur when widgets are made and some fall off the production line. However, if you notice that every time you assemble a widget, it always falls apart at exactly the same place, then that would be a systematic problem.
Once you've identified where the problems lie, you'll want to design solutions to eliminate those problems. It might mean changing the way you do business or redesigning it entirely. To verify that the changes have worked, you need to test them again. If they don’t work, you’ll need to go back and rework the plan.