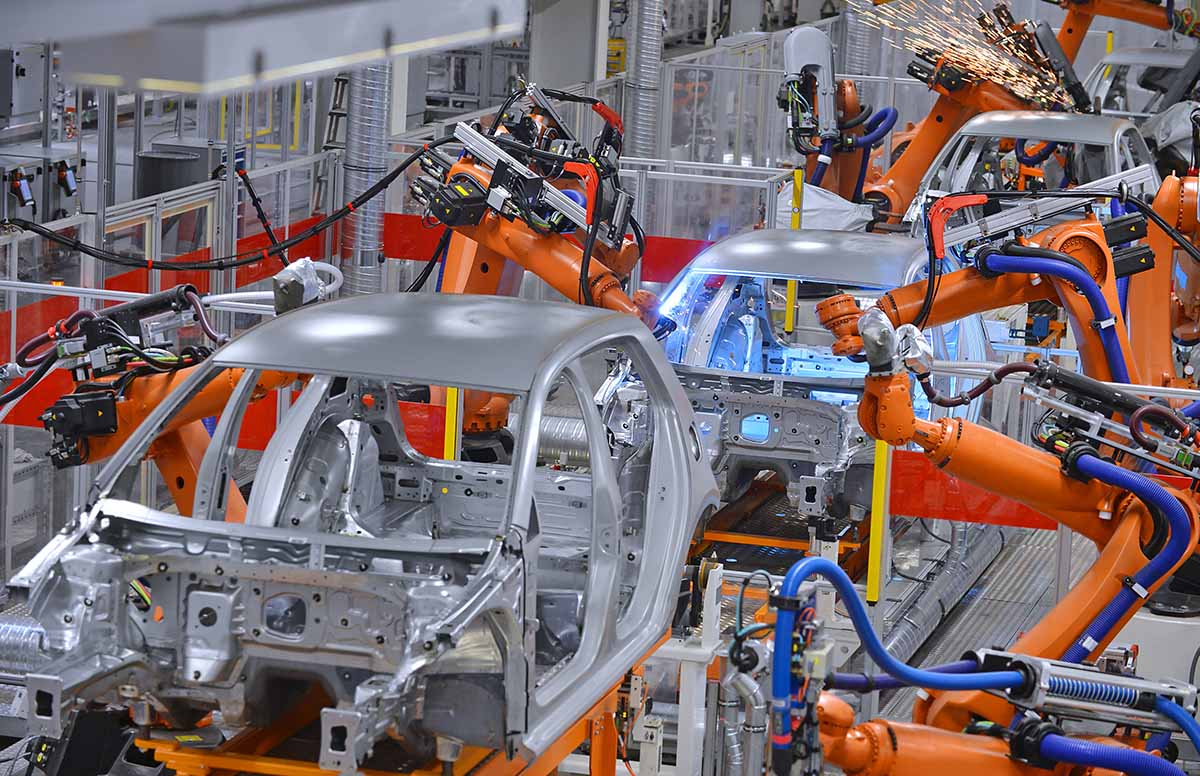
Whether it is for a new project or a routine work, Industrial Engineering Managers are a critical member of the team. They play an important role in leading staff members and improving production output. This includes managing the factory floor's layout and design, and overseeing implementation of processes and procedures. Additionally, they offer technical knowledge and expertise that can be used to aid in the development of new products or processes.
Industrial Engineering Managers are responsible for developing and maintaining efficient manufacturing processes. This requires an in-depth knowledge of current trends in automation, robotics, and other related technologies. They must also monitor and maintain industrial processes and ensure that they comply with safety and health standards. They are responsible for ensuring that raw materials and consumables are used properly. They also conduct space and workflow studies. The manager supervises all work projects including product cost reduction, cycle time and process improvement. They also oversee preventative maintenance.
The manager works in collaboration with other teams to develop new processes, improve efficiency, and streamline operations. The manager is responsible for overseeing the installation and redesign of equipment as well as facility renovations. Managers communicate technical information to non-technical parties as part of the project management process. Additionally, the manager ensures that resources are available to teams and makes site visits at suppliers' facilities. He/she advocates for team members, and ensures that quality compliance guidelines are followed.
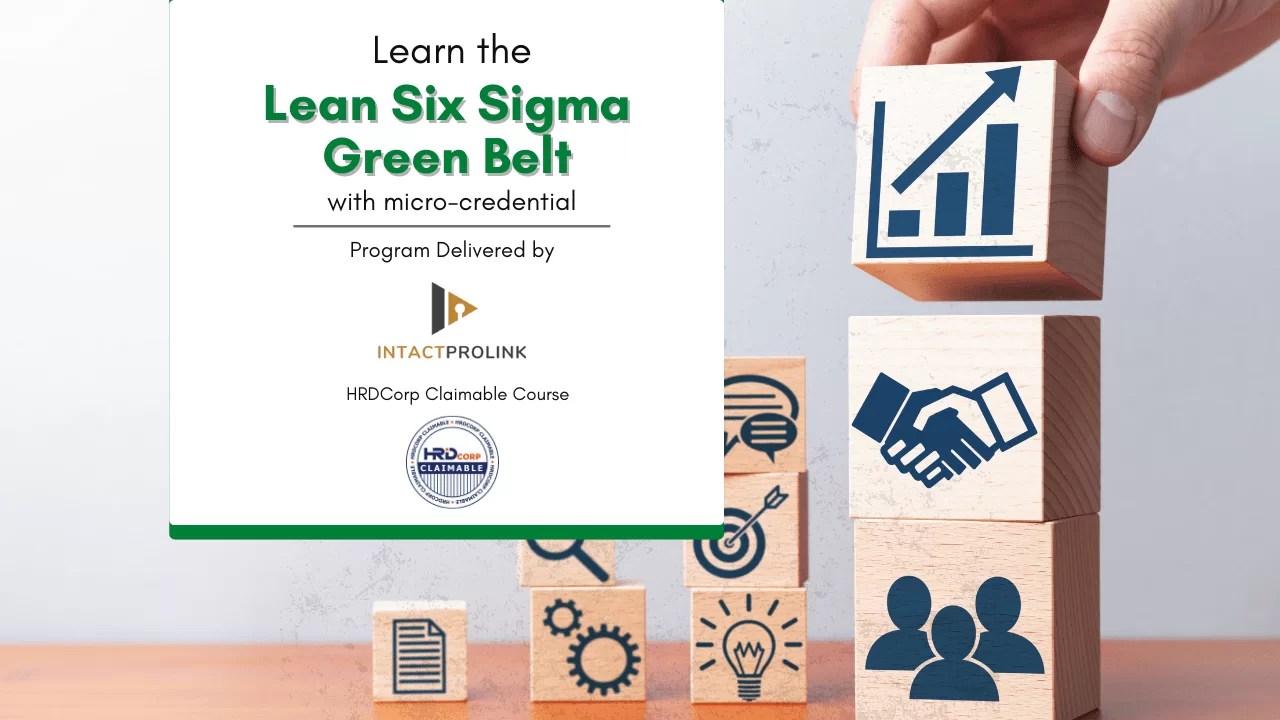
Industrial Engineering Managers are expected to be highly motivated, creative, and able to solve problems. They should be able work in both hot and cold environments and be physically fit to climb and walk for between 8 and 12 hours per day. They must also be able communicate with all levels of employees.
Industrial Engineering Managers must have a degree in engineering or a related field. They must also have at least five years experience in this field. Many employers prefer candidates with postgraduate training. These candidates may also require specific skills such as project management and logistics.
Industrial Engineering Managers are responsible for the development and creation of new products. They have a strong background in problem-solving and quality improvement. They thrive in a team environment. A manager can be most successful if he or she can encourage employees' growth.
Industrial Engineers excel at streamlining operations, and cutting down costs. They are well-versed in manufacturing processes and love meeting deadlines. They also have experience with recruiting, human resources, logistics, and vendor / supplier relations. They are adept at setting goals, managing processes, and creating budgets. They can also prepare strategies to improve the efficiency of engineering projects.
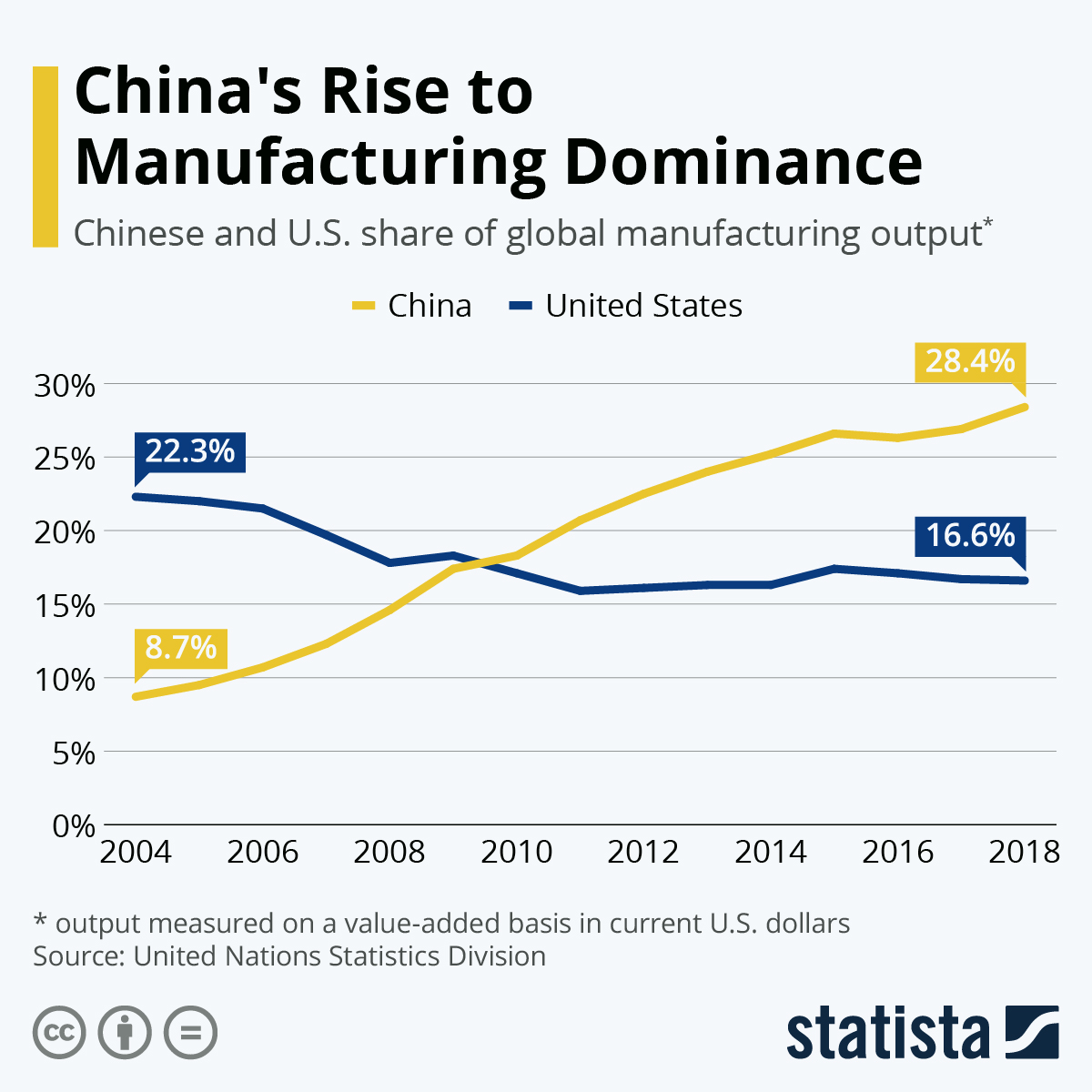
Industrial Engineering Managers may be responsible for overseeing the design and implementation of new manufacturing sequences or operating equipment. They are responsible for developing plans to implement new equipment or operating methods according to established standards and guidelines. They must also oversee the process of implementing waste elimination plans. They also have to analyze the factory's labor productivity.
Industrial Engineering Managers are able to share their knowledge and help develop strategies for increasing productivity, developing new products, managing human resources, and other tasks. They can also help develop and improve the efficiency of existing processes.
FAQ
What is the job of a manufacturer manager?
A manufacturing manager must ensure that all manufacturing processes are efficient and effective. They should also be aware of any problems within the company and act accordingly.
They should also be able communicate with other departments, such as sales or marketing.
They should be up to date on the latest trends and be able apply this knowledge to increase productivity and efficiency.
How does manufacturing avoid bottlenecks in production?
The key to avoiding bottlenecks in production is to keep all processes running smoothly throughout the entire production cycle, from the time you receive an order until the time when the product ships.
This includes planning for capacity requirements as well as quality control measures.
The best way to do this is to use continuous improvement techniques such as Six Sigma.
Six Sigma Management System is a method to increase quality and reduce waste throughout your organization.
It emphasizes consistency and eliminating variance in your work.
What does it mean to warehouse?
A warehouse is an area where goods are stored before being sold. You can have it indoors or outdoors. It may also be an indoor space or an outdoor area.
What jobs are available in logistics?
There are many kinds of jobs available within logistics. Some of them are:
-
Warehouse workers - They load and unload trucks and pallets.
-
Transportation drivers - They drive trucks and trailers to deliver goods and carry out pick-ups.
-
Freight handlers - They sort and pack freight in warehouses.
-
Inventory managers - These are responsible for overseeing the stock of goods in warehouses.
-
Sales reps are people who sell products to customers.
-
Logistics coordinators - They plan and organize logistics operations.
-
Purchasing agents - They purchase goods and services needed for company operations.
-
Customer service agents - They answer phone calls and respond to emails.
-
Shippers clerks - They process shipping order and issue bills.
-
Order fillers: They fill orders based off what has been ordered and shipped.
-
Quality control inspectors are responsible for inspecting incoming and outgoing products looking for defects.
-
Others - There are many types of jobs in logistics such as transport supervisors and cargo specialists.
What are the products and services of logistics?
Logistics are the activities involved in moving goods from point A to point B.
They include all aspects associated with transport including packaging, loading transporting, unloading storage, warehousing inventory management customer service, distribution returns and recycling.
Logisticians ensure that the product is delivered to the correct place, at the right time, and under safe conditions. They provide information on demand forecasts as well stock levels, production schedules and availability of raw material.
They also keep track of shipments in transit, monitor quality standards, perform inventories and order replenishment, coordinate with suppliers and vendors, and provide support services for sales and marketing.
How can I find out more about manufacturing?
You can learn the most about manufacturing by getting involved in it. If that is not possible, you could always read books or view educational videos.
Statistics
- Many factories witnessed a 30% increase in output due to the shift to electric motors. (en.wikipedia.org)
- According to the United Nations Industrial Development Organization (UNIDO), China is the top manufacturer worldwide by 2019 output, producing 28.7% of the total global manufacturing output, followed by the United States, Japan, Germany, and India.[52][53] (en.wikipedia.org)
- It's estimated that 10.8% of the U.S. GDP in 2020 was contributed to manufacturing. (investopedia.com)
- [54][55] These are the top 50 countries by the total value of manufacturing output in US dollars for its noted year according to World Bank.[56] (en.wikipedia.org)
- According to a Statista study, U.S. businesses spent $1.63 trillion on logistics in 2019, moving goods from origin to end user through various supply chain network segments. (netsuite.com)
External Links
How To
How to use 5S to increase Productivity in Manufacturing
5S stands in for "Sort", the "Set In Order", "Standardize", or "Separate". The 5S methodology was developed at Toyota Motor Corporation in 1954. It assists companies in improving their work environments and achieving higher efficiency.
The idea behind standardizing production processes is to make them repeatable and measurable. Cleaning, sorting and packing are all done daily. Through these actions, workers can perform their jobs more efficiently because they know what to expect from them.
Five steps are required to implement 5S: Sort, Set In Order, Standardize. Separate. Each step has a different action and leads to higher efficiency. If you sort items, it makes them easier to find later. When you arrange items, you place them together. You then organize your inventory in groups. Labeling your containers will ensure that everything is correctly labeled.
This process requires employees to think critically about how they do their job. Employees must understand why they do certain tasks and decide if there's another way to accomplish them without relying on the old ways of doing things. In order to use the 5S system effectively, they must be able to learn new skills.
The 5S method increases efficiency and morale among employees. As they begin to see improvements, they feel motivated to continue working towards the goal of achieving higher levels of efficiency.