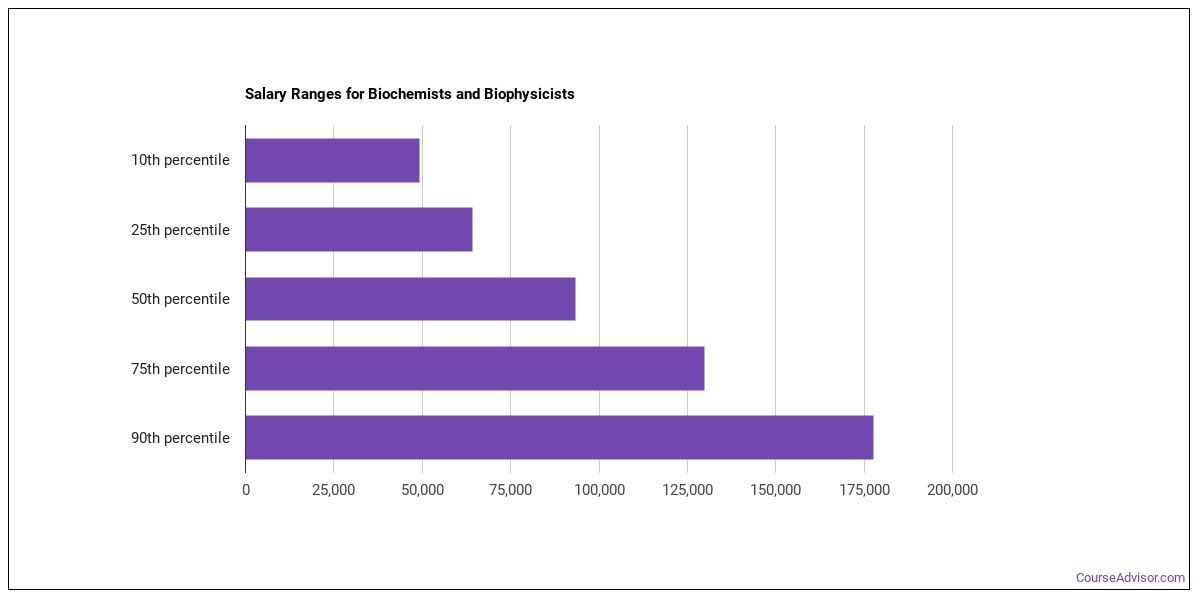
Those who work as nuclear technicians are responsible for monitoring, maintaining, and analyzing a variety of machines and equipment used in nuclear energy production and testing. A nuclear technician typically works at a power plant. They can gain more responsibility as they get experience. They might perform radiation testing, troubleshoot devices, or collect data to assess the system's quality.
To become a nuclear technician, you'll need to complete an associate's degree or bachelor's degree in nuclear technology. You will also need to take training. Most employers require two years of specialized training to qualify for a nuclear technician job. You can apply for jobs as a nuclear technician with a laboratory, power plant, or any other organization once you have completed the program. You can also become a nuclear engineer by specializing in nuclear waste management.
A nuclear technician usually works alongside scientists involved in nuclear energy production and research. They can also monitor radiation levels in nuclear power plants and make records of them. Additionally, they may be able to operate specialized equipment like remote-control instrument panel panels. They also instruct staff regarding radiation safety procedures.
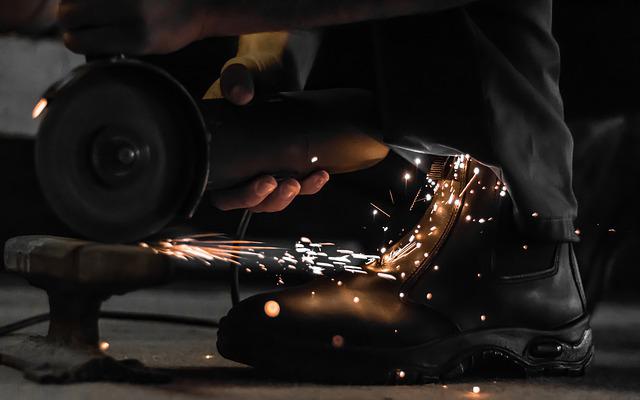
Additional to the general duties of a nuclear technician, they may be skilled in radiation protection or waste management. Nuclear technicians may be required to obtain security clearance and take advanced math or science courses in order to work on restricted projects.
You may also be eligible to apply for government jobs as a nuclear technician. These jobs require you to be able to think creatively, search for facts, and decipher complicated situations. This means that the average national salary of $38,10 an hour for nuclear technicians may be higher.
In addition to being a technical specialist, nuclear technicians can become supervisors, instructors, and nuclear engineers. If they move up to higher levels of authority, they might earn more. This is a field that offers good pay in many industries.
The salary for nuclear technicians varies depending on the level of education and experience. An entry-level technician will typically make an average salary of $31,000 annually. A nuclear technician who has been employed for more than a decade may make a $115,000. This field is expected grow at a rapid rate over the next ten years. This means that there will be approximately 1,400 openings in the field.
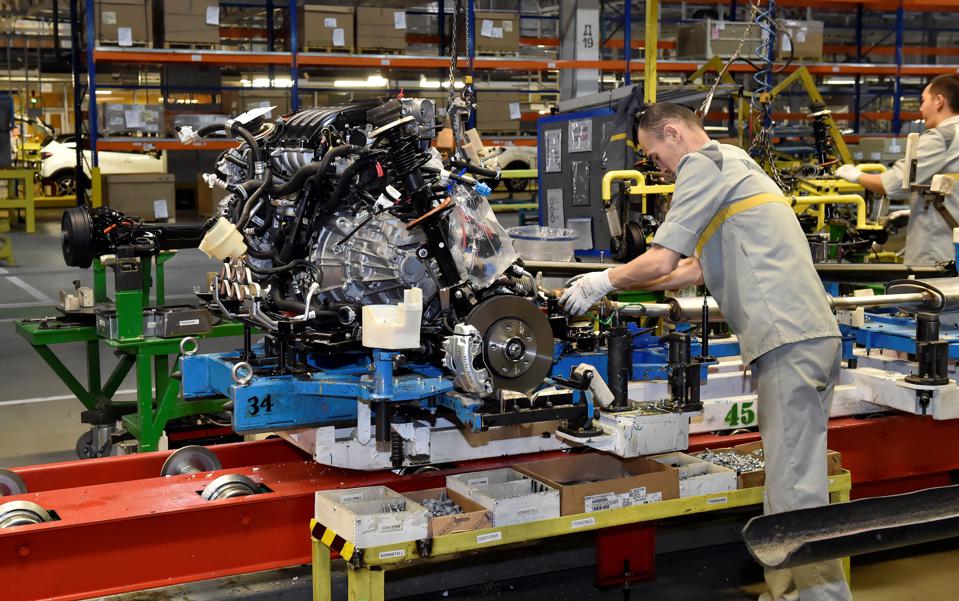
The average salary for nuclear technicians varies from one state or another. For example, the annual average salary for nuclear technicians in Illinois is $121,020. California has the highest nuclear technician salary. While it may vary from state to state, the national average is $126,600 per year. Higher salaries may be available for those with advanced degrees and nuclear technician degrees.
The Nuclear Technician salary is among the highest in the field, but it doesn't mean that this job is the best. It is important to be able to deduce and reason well, have a passion for science, and be able to think critically. You will also need to learn how you can operate specialized equipment. Many nuclear technicians seek further education to become certified.
FAQ
Is automation necessary in manufacturing?
Automating is not just important for manufacturers, but also for service providers. It allows them provide faster and more efficient services. It helps them to lower costs by reducing human errors, and improving productivity.
What skills does a production planner need?
Being a production planner is not easy. You need to be organized and flexible. Communication skills are essential to ensure that you can communicate effectively with clients, colleagues, and customers.
What is production planning?
Production Planning refers to the development of a plan for every aspect of production. This document aims to ensure that everything is planned and ready when you are ready to shoot. It should also contain information on achieving the best results on set. This includes location information, crew details, equipment specifications, and casting lists.
The first step in filming is to define what you want. You may have already decided where you would like to shoot, or maybe there are specific locations or sets that you want to use. Once you have identified your locations and scenes, you can start working out which elements you require for each scene. Perhaps you have decided that you need to buy a car but aren't sure which model. You could look online for cars to see what options are available, and then narrow down your choices by selecting between different makes or models.
After you've found the perfect car, it's time to start thinking about adding extras. Do you need people sitting in the front seats? Perhaps you have someone who needs to be able to walk around the back of your car. Maybe you want to change the interior color from black to white? These questions will help to determine the style and feel of your car. Another thing you can do is think about what type of shots are desired. Are you going to be shooting close-ups? Or wide angles? Maybe the engine or steering wheel is what you are looking to film. All of these things will help you identify the exact style of car you want to film.
Once you have determined all of the above, you can move on to creating a schedule. You can create a schedule that will outline when you must start and finish your shoots. You will need to know when you have to be there, what time you have to leave and when your return home. It will help everyone know exactly what they have to do and when. If you need to hire extra staff, you can make sure you book them in advance. There is no point in hiring someone who won't turn up because you didn't let him know.
When creating your schedule, you will also need to consider the number of days you need to film. Some projects can be completed in a matter of days or weeks. Others may take several days. When you are creating your schedule, you should always keep in mind whether you need more than one shot per day or not. Multiple takes of the same location will lead to higher costs and take more time. If you are unsure if you need multiple takes, it is better to err on the side of caution and shoot fewer takes rather than risk wasting money.
Another important aspect of production planning is setting budgets. It is important to set a realistic budget so you can work within your budget. It is possible to reduce the budget at any time if you experience unexpected problems. It is important to not overestimate how much you will spend. If you underestimate the cost of something, you will have less money left after paying for other items.
Production planning is a detailed process. But, once you understand the workings of everything, it becomes easier for future projects to be planned.
How can excess manufacturing production be reduced?
In order to reduce excess production, you need to develop better inventory management methods. This would reduce time spent on activities such as purchasing, stocking, and maintaining excess stock. This would allow us to use our resources for more productive tasks.
This can be done by using a Kanban system. A Kanban board is a visual display used to track work in progress. Work items are moved through various states to reach their destination in a Kanban system. Each state represents an individual priority level.
For instance, when work moves from one stage to another, the current task is complete enough to be moved to the next stage. However, if a task is still at the beginning stages, it will remain so until it reaches the end of the process.
This keeps work moving and ensures no work is lost. With a Kanban board, managers can see exactly how much work is being done at any given moment. This allows them to adjust their workflows based on real-time information.
Lean manufacturing, another method to control inventory levels, is also an option. Lean manufacturing seeks to eliminate waste from every step of the production cycle. Waste includes anything that does not add value to the product. Some common types of waste include:
-
Overproduction
-
Inventory
-
Unnecessary packaging
-
Material surplus
Manufacturers can reduce their costs and improve their efficiency by using these ideas.
How can manufacturing avoid production bottlenecks
The key to avoiding bottlenecks in production is to keep all processes running smoothly throughout the entire production cycle, from the time you receive an order until the time when the product ships.
This includes both quality control and capacity planning.
Continuous improvement techniques like Six Sigma are the best way to achieve this.
Six Sigma Management System is a method to increase quality and reduce waste throughout your organization.
It is focused on creating consistency and eliminating variation in your work.
What type of jobs is there in logistics
Logistics can offer many different jobs. Some examples are:
-
Warehouse workers - They load and unload trucks and pallets.
-
Transportation drivers – They drive trucks or trailers to transport goods and perform pick-ups.
-
Freight handlers, - They sort out and pack freight in warehouses.
-
Inventory managers – These people oversee inventory at warehouses.
-
Sales representatives - They sell products.
-
Logistics coordinators – They plan and coordinate logistics operations.
-
Purchasing agents - They purchase goods and services needed for company operations.
-
Customer service representatives are available to answer customer calls and emails.
-
Ship clerks - They issue bills and process shipping orders.
-
Order fillers: They fill orders based off what has been ordered and shipped.
-
Quality control inspectors – They inspect incoming and outgoing products to ensure that there are no defects.
-
Other - Logistics has many other job opportunities, including transportation supervisors, logistics specialists, and cargo specialists.
Statistics
- [54][55] These are the top 50 countries by the total value of manufacturing output in US dollars for its noted year according to World Bank.[56] (en.wikipedia.org)
- In the United States, for example, manufacturing makes up 15% of the economic output. (twi-global.com)
- Many factories witnessed a 30% increase in output due to the shift to electric motors. (en.wikipedia.org)
- It's estimated that 10.8% of the U.S. GDP in 2020 was contributed to manufacturing. (investopedia.com)
- You can multiply the result by 100 to get the total percent of monthly overhead. (investopedia.com)
External Links
How To
How to use 5S to increase Productivity in Manufacturing
5S stands in for "Sort", the "Set In Order", "Standardize", or "Separate". Toyota Motor Corporation developed the 5S method in 1954. It improves the work environment and helps companies to achieve greater efficiency.
This method has the basic goal of standardizing production processes to make them repeatable. Cleaning, sorting and packing are all done daily. These actions allow workers to perform their job more efficiently, knowing what to expect.
There are five steps that you need to follow in order to implement 5S. Each step requires a different action, which increases efficiency. For example, when you sort things, you make them easy to find later. You arrange items by placing them in an order. You then organize your inventory in groups. Finally, label all containers correctly.
Employees must be able to critically examine their work practices. Employees should understand why they do the tasks they do, and then decide if there are better ways to accomplish them. They will need to develop new skills and techniques in order for the 5S system to be implemented.
The 5S method not only increases efficiency but also boosts morale and teamwork. Once they start to notice improvements, they are motivated to keep working towards their goal of increasing efficiency.