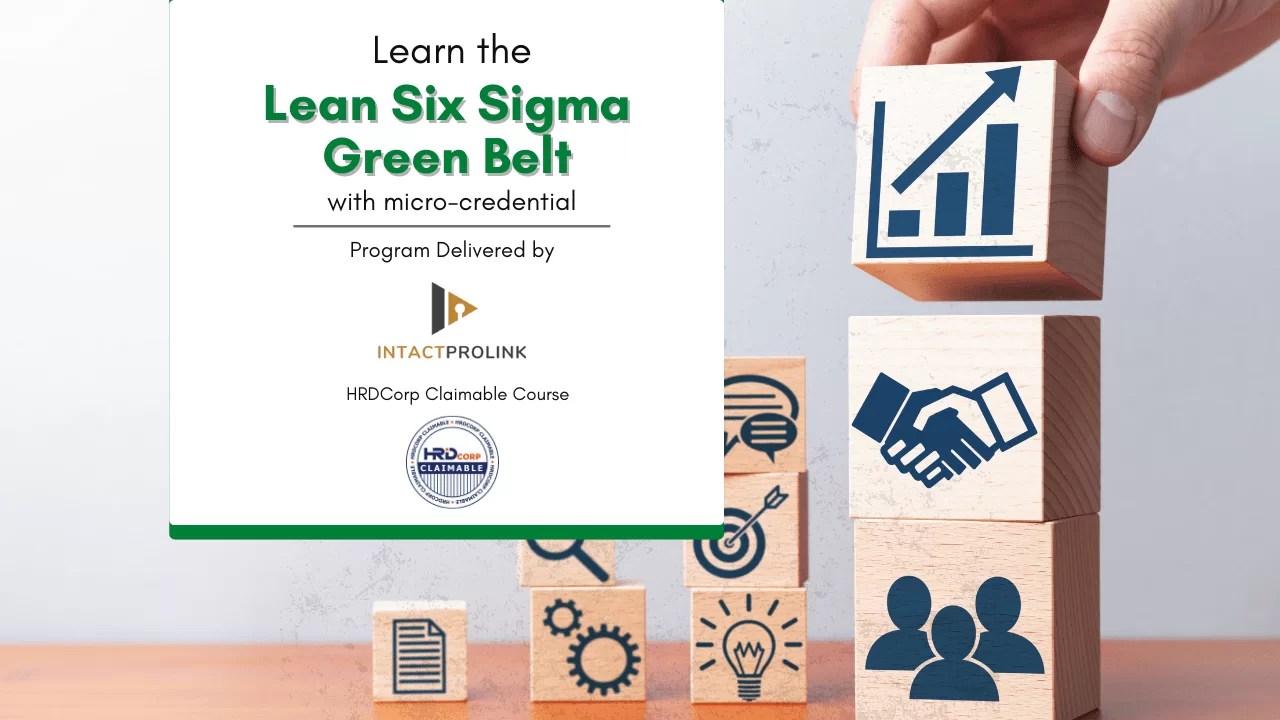
You can expect to earn a lot, no matter whether you're seeking work or looking for a career in industrial engineering. You can expect to earn different amounts depending on your education, industry, and experience. The average industrial engineer income is $95,300. But salaries can be higher in top-paying areas.
The job of an industrial engineer is to develop, design and install systems that improve the efficiency of production processes. They also devise ways to make the workplace safer. An industrial engineer may also design equipment and plan facilities. This can be done by evaluating how changes in design affect the costs of producing the product.
With experience in the field, industrial engineers may be able to earn a high-paying job. They can also earn a higher salary if they have a master's degree in industrial engineering. This degree is popular with international students. It can lead them to careers in manufacturing, healthcare, and engineering services.
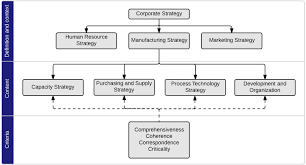
Also, industrial engineers will experience a high rate of employment growth over the next decade. The employment of industrial engineers is expected to rise 10 percent between 2021 and 2031. This is higher than what the average salary for all occupations. The top 10 percent earn over $85,000 annually. Managers can expect to earn higher salaries. Industrial engineers who have advanced degrees in industrial engineering can perform cost-benefit analyses, evaluate cost distribution in operational processes, negotiate for purchasing decisions, and even conduct cost-benefit reviews.
Industrial engineers are able to think outside the box and come up with innovative ways to improve processes. Many industrial engineers work in offices, and they may interact with production workers. Industrial engineers may also interact with production workers via email, telephone and face to face discussions. They might also give oral or written presentations of their plans.
Many industries include construction, manufacturing, transport, energy, utilities, pharmaceuticals and other. They may also be responsible for developing systems that reduce waste in production, depending on their industry.
A bachelor's level in industrial engineering is required for most industrial engineers. Industrial engineers can also pursue a master's degree in industrial engineering, which can lead to a career in engineering consulting or manufacturing. Most programs include courses in mathematics, science, and general engineering. The program can take anywhere from two to seven to complete.
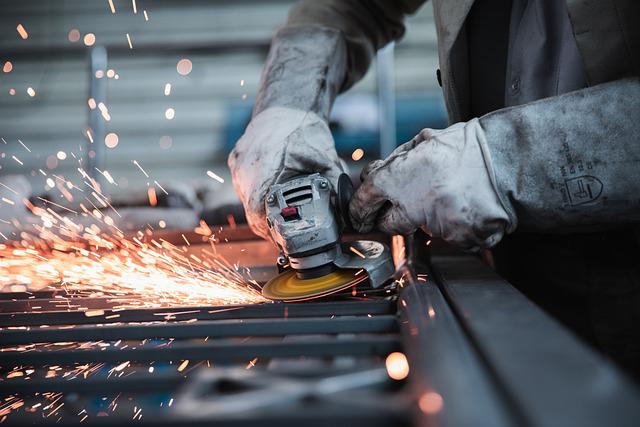
The average salary for an entry-level industrial engineer is $65,000 to $75,000, although the range of salary increases with experience. The salary for an experienced industrial engineer is $86,809 a year. If an industrial engineer has a master's in engineering or doctorate, their salary may be higher.
A good technical and communication skill is essential for industrial engineers. They must be able solve problems outside of their usual scope. They must know how to work with workers, equipment and materials to create efficient systems. They should also be able to communicate well with others. This job is rewarding and challenging.
FAQ
What is production management?
Production planning is the process of creating a plan that covers all aspects of production. This includes scheduling, budgeting and crew, location, equipment, props, and more. This document will ensure everything is in order and ready to go when you need it. This document should include information about how to achieve the best results on-set. This includes shooting schedules, locations, cast lists, crew details, and equipment requirements.
First, you need to plan what you want to film. You may already know where you want the film to be shot, or perhaps you have specific locations and sets you wish to use. Once you've identified the locations and scenes you want to use, you can begin to plan what elements you need for each scene. For example, you might decide that you need a car but don't know exactly what model you want. To narrow your options, you can search online for available models.
Once you have found the right vehicle, you can think about adding accessories. Do you need people sitting in the front seats? You might also need someone to help you get around the back. You might want to change your interior color from black and white. These questions will help determine the look and feel you want for your car. Also, think about what kind of shots you would like to capture. Will you be filming close-ups or wide angles? Maybe you want the engine or the steering wheels to be shown. This will allow you to determine the type of car you want.
Once you have made all the necessary decisions, you can start to create a schedule. You will know when you should start and when you should finish shooting. Each day will include the time when you need to arrive at the location, when you need to leave and when you need to return home. This way, everyone knows what they need to do and when. Hire extra staff by booking them ahead of time. There is no point in hiring someone who won't turn up because you didn't let him know.
You will need to factor in the days that you have to film when creating your schedule. Some projects may only take a couple of days, while others could last for weeks. It is important to consider whether you require more than one photo per day when you create your schedule. Multiple takes of the same location will lead to higher costs and take more time. You can't be certain if you will need multiple takes so it is better not to shoot too many.
Another important aspect of production planning is setting budgets. Setting a realistic budget is essential as it will allow you to work within your means. It is possible to reduce the budget at any time if you experience unexpected problems. You shouldn't underestimate the amount you'll spend. Underestimating the cost will result in less money after you have paid for other items.
Production planning can be a complex process. However, once you know how everything works together it will become easier to plan future projects.
What are the 4 types manufacturing?
Manufacturing refers the process of turning raw materials into useful products with machines and processes. It includes many different activities like designing, building and testing, packaging, shipping and selling, as well as servicing.
What are manufacturing and logistics?
Manufacturing is the process of creating goods from raw materials by using machines and processes. Logistics manages all aspects of the supply chain, including procurement, production planning and distribution, inventory control, transportation, customer service, and transport. Sometimes manufacturing and logistics are combined to refer to a wider term that includes both the process of creating products as well as their delivery to customers.
What skills are required to be a production manager?
You must be flexible and organized to become a productive production planner. It is also important to be able communicate with colleagues and clients.
What jobs are available in logistics?
There are many jobs available in logistics. Some examples are:
-
Warehouse workers - They load and unload trucks and pallets.
-
Transportation drivers: They drive trucks and trailers and deliver goods and make pick-ups.
-
Freight handlers – They sort and package freight at warehouses.
-
Inventory managers – These people oversee inventory at warehouses.
-
Sales representatives - They sell products to customers.
-
Logistics coordinators - They plan and organize logistics operations.
-
Purchasing agents: They are responsible for purchasing goods and services to support company operations.
-
Customer service representatives - They answer calls and emails from customers.
-
Shipping clerks: They process shipping requests and issue bills.
-
Order fillers – They fill orders based upon what was ordered and shipped.
-
Quality control inspectors are responsible for inspecting incoming and outgoing products looking for defects.
-
Others - There is a variety of other jobs in logistics. These include transportation supervisors and cargo specialists.
How can manufacturing efficiency be improved?
First, identify the factors that affect production time. We must then find ways that we can improve these factors. If you don’t know how to start, look at which factors have the greatest impact upon production time. Once you have identified them, it is time to identify solutions.
Statistics
- Job #1 is delivering the ordered product according to specifications: color, size, brand, and quantity. (netsuite.com)
- According to the United Nations Industrial Development Organization (UNIDO), China is the top manufacturer worldwide by 2019 output, producing 28.7% of the total global manufacturing output, followed by the United States, Japan, Germany, and India.[52][53] (en.wikipedia.org)
- [54][55] These are the top 50 countries by the total value of manufacturing output in US dollars for its noted year according to World Bank.[56] (en.wikipedia.org)
- Many factories witnessed a 30% increase in output due to the shift to electric motors. (en.wikipedia.org)
- According to a Statista study, U.S. businesses spent $1.63 trillion on logistics in 2019, moving goods from origin to end user through various supply chain network segments. (netsuite.com)
External Links
How To
How to use Lean Manufacturing in the production of goods
Lean manufacturing is a management system that aims at increasing efficiency and reducing waste. It was developed in Japan during the 1970s and 1980s by Taiichi Ohno, who received the Toyota Production System (TPS) award from TPS founder Kanji Toyoda. Michael L. Watkins published the "The Machine That Changed the World", the first book about lean manufacturing. It was published in 1990.
Lean manufacturing, often described as a set and practice of principles, is aimed at improving the quality, speed, cost, and efficiency of products, services, and other activities. It emphasizes the elimination of defects and waste throughout the value stream. Lean manufacturing can be described as just-in–time (JIT), total productive maintenance, zero defect (TPM), or even 5S. Lean manufacturing emphasizes reducing non-value-added activities like inspection, rework and waiting.
Lean manufacturing not only improves product quality but also reduces costs. Companies can also achieve their goals faster by reducing employee turnover. Lean manufacturing can be used to manage all aspects of the value chain. Customers, suppliers, distributors, retailers and employees are all included. Lean manufacturing is widely used in many industries. For example, Toyota's philosophy underpins its success in automobiles, electronics, appliances, healthcare, chemical engineering, aerospace, paper, food, etc.
Five fundamental principles underlie lean manufacturing.
-
Define Value- Identify the added value your company brings to society. What makes you stand out from your competitors?
-
Reduce Waste - Remove any activity which doesn't add value to your supply chain.
-
Create Flow: Ensure that the work process flows without interruptions.
-
Standardize and Simplify – Make processes as consistent, repeatable, and as simple as possible.
-
Build relationships - Develop and maintain personal relationships with both your internal and external stakeholders.
Although lean manufacturing isn't a new concept in business, it has gained popularity due to renewed interest in the economy after the 2008 global financial crisis. Many businesses have adopted lean production techniques to make them more competitive. In fact, some economists believe that lean manufacturing will be an important factor in economic recovery.
Lean manufacturing is now becoming a common practice in the automotive industry, with many benefits. These include better customer satisfaction and lower inventory levels. They also result in lower operating costs.
You can apply Lean Manufacturing to virtually any aspect of your organization. Lean manufacturing is most useful in the production sector of an organisation because it ensures that each step in the value-chain is efficient and productive.
There are three types principally of lean manufacturing:
-
Just-in Time Manufacturing: This lean manufacturing method is commonly called "pull systems." JIT stands for a system where components are assembled on the spot rather than being made in advance. This approach is designed to reduce lead times and increase the availability of components. It also reduces inventory.
-
Zero Defects Manufacturing: ZDM ensures that no defective units leave the manufacturing plant. Repairing a part that is damaged during assembly should be done, not scrapping. This also applies to finished products that need minor repairs before being shipped.
-
Continuous Improvement: Continuous Improvement aims to improve efficiency by continually identifying problems and making adjustments to eliminate or minimize waste. Continuous improvement refers to continuous improvement of processes as well people and tools.