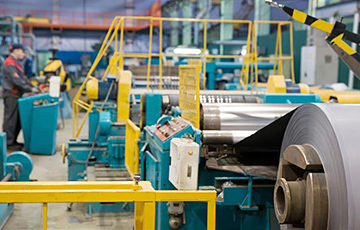
To become a drafter, one must have technical knowledge and the ability to translate design ideas into technical drawings. They also need to be able to work with other people to help produce the best results. They may also need to learn how to read engineering plans and how to work with specific software programs. They might also need an understanding of engineering formulas that can be used to calculate measurement.
Drafters typically work for architectural and engineering firms. They are responsible for creating plans for buildings, structures, as well as other products, using computer-aided engineering (CAD) software. These professionals often work independently on projects, but they also work in teams to produce innovative designs. They often work full-time, but they also can take on a variety of jobs. Depending on the company they work for, they may be required to work overtime to meet deadlines.
An associate's degree is typically earned by drafting professionals from a community or technical college. Then, they can continue their education by enrolling in a 4-year university program. It is possible to transfer their degree, depending on the course taken.
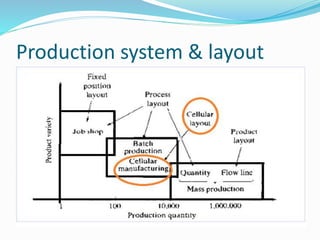
Drafters will need to have professional experience in addition to a degree in drafting. They may be asked to complete an internship with a firm in order to gain practical experience. This experience can help drafters land a job. You may also be asked for a portfolio to showcase your drafting skills.
A certification is also available to drafters. The American Design Drafting Association (ADDA) offers certification exams that test drafting knowledge. These tests can be used to evaluate your ability to tolerate and design geometrically. Many certifications are valid three years. Candidates will need to take new exams. The ADDA offers certification in many drafting specialties.
Drafters are typically employed by engineering, manufacturing, and construction companies. They may also work in factories and with electrics. They may also work on a regular schedule, but some drafters work more than 40 hours a week. They need to know how to use computer aided drafting (CAD), and manage their time.
Drafters can profit from the growing use of technology in order to increase their efficiency. To remain competitive, they will need to be able to use CAD and other software programs and keep up to date on building codes. If you are interested in becoming an architect, a master's is a good option. When it comes to being hired, those with a master's will be more successful than other candidates. They will also be better qualified to present technical information for clients.
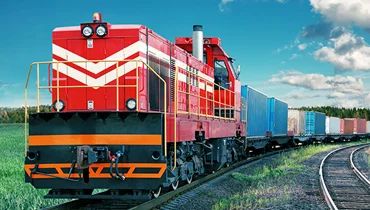
Drafters may also be able to work as an assistant for professional drafters. They may also volunteer to work on community projects to gain experience. Before you register for classes, decide what type of project is most important to you. Some clients prefer pencil sketches, while others prefer computer-generated drawings.
Draft technicians can gain work experience after they graduate from highschool. A special focus should be given to computer and math classes.
FAQ
What does manufacturing mean?
Manufacturing Industries is a group of businesses that produce goods for sale. The people who buy these products are called consumers. These companies use a variety processes such as distribution, retailing and management to accomplish their purpose. These companies produce goods using raw materials and other equipment. This includes all types manufactured goods such as clothing, building materials, furniture, electronics, tools and machinery.
What does warehouse refer to?
A warehouse is a place where goods are stored until they are sold. It can be indoors or out. It could be one or both.
What is it like to manage a logistics company?
It takes a lot of skills and knowledge to run a successful logistics business. For clients and suppliers to be successful, you need to have excellent communication skills. You need to understand how to analyze data and draw conclusions from it. You need to be able work under pressure and manage stressful situations. You need to be innovative and creative to come up with new ways to increase efficiency. Strong leadership qualities are essential to motivate your team and help them achieve their organizational goals.
To meet tight deadlines, you must also be efficient and organized.
What is the role and responsibility of a Production Planner?
Production planners ensure all aspects of the project are delivered within time and budget. They also ensure the quality of the product and service meets the client's requirements.
Do we need to know about Manufacturing Processes before learning about Logistics?
No. You don't have to know about manufacturing processes before learning about logistics. Understanding the manufacturing process will allow you to better understand logistics.
Statistics
- It's estimated that 10.8% of the U.S. GDP in 2020 was contributed to manufacturing. (investopedia.com)
- (2:04) MTO is a production technique wherein products are customized according to customer specifications, and production only starts after an order is received. (oracle.com)
- In 2021, an estimated 12.1 million Americans work in the manufacturing sector.6 (investopedia.com)
- Job #1 is delivering the ordered product according to specifications: color, size, brand, and quantity. (netsuite.com)
- According to a Statista study, U.S. businesses spent $1.63 trillion on logistics in 2019, moving goods from origin to end user through various supply chain network segments. (netsuite.com)
External Links
How To
How to Use 5S for Increasing Productivity in Manufacturing
5S stands for "Sort", 'Set In Order", 'Standardize', & Separate>. The 5S methodology was developed at Toyota Motor Corporation in 1954. It helps companies achieve higher levels of efficiency by improving their work environment.
The idea behind standardizing production processes is to make them repeatable and measurable. This means that tasks such as cleaning, sorting, storing, packing, and labeling are performed daily. Workers can be more productive by knowing what to expect.
Five steps are required to implement 5S: Sort, Set In Order, Standardize. Separate. Each step involves a different action which leads to increased efficiency. By sorting, for example, you make it easy to find the items later. Once you have placed items in an ordered fashion, you will put them together. After you have divided your inventory into groups you can store them in easy-to-reach containers. Make sure everything is correctly labeled when you label your containers.
Employees must be able to critically examine their work practices. Employees must understand why they do certain tasks and decide if there's another way to accomplish them without relying on the old ways of doing things. To be successful in the 5S system, employees will need to acquire new skills and techniques.
In addition to improving efficiency, the 5S system also increases morale and teamwork among employees. They feel more motivated to work towards achieving greater efficiency as they see the results.