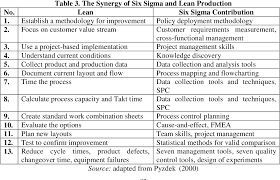
A wide variety of skills are required for railway logistics jobs. While some positions are simple to learn, others require years of experience and classroom training. These jobs require extensive product and computer knowledge. Other jobs might require substantial overseas travel.
A transport logistics specialist works to organize the transportation of people and goods. The specialist may assess the efficiency of the process and find solutions to specific problems. This could include a mechanical check or determining which route is best for a particular cargo.
The role of the rail logistic manager is to ensure trains and other transport means run on time and are properly maintained. They must also ensure that trains follow safety rules and regulations. Freight delivery is often part of the job. But this is only one part of the job.
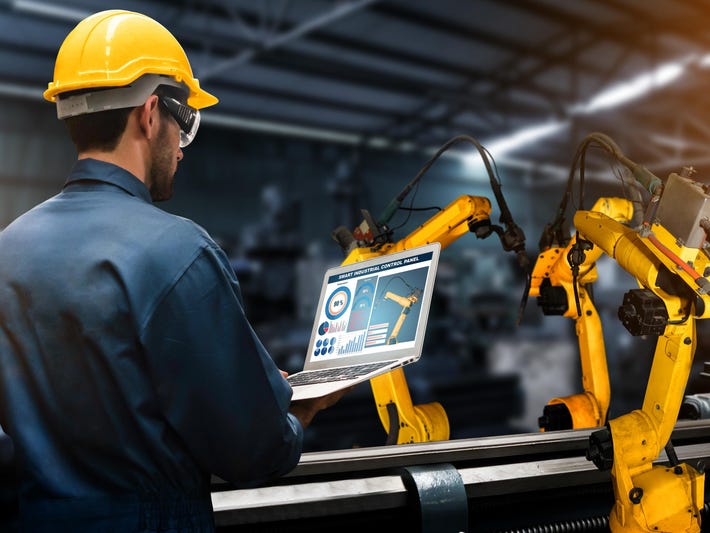
Intermodal dispatcher can be another entry-level role in the industry. This person coordinates a schedule for drivers and shipping companies. The person coordinates the schedule of a group of drivers and a shipping company. Administrative duties are not uncommon in this position.
The role of railway logistics manager can be done in private firms or government agencies. These roles pay well and offer opportunities for career growth. On average, you can earn approximately $45,000 per annum. These jobs don't require a bachelor’s degree. The average salary for a rail job is quite low, despite the high salaries.
Some common logistics titles are logistics manager, logistics coordinator and logistics analyst. These are all vital positions. Each role has its merits. However, there's a good chance you will find your talents more useful in one than the other.
Logistics managers must be able and willing to negotiate the best rates or terms for their clients' transportation needs. This involves analyzing the availability of equipment and services, negotiating with other parties, and analyzing service levels. A basic understanding of transportation management principles is required to help improve the efficiency of a company's logistics process.
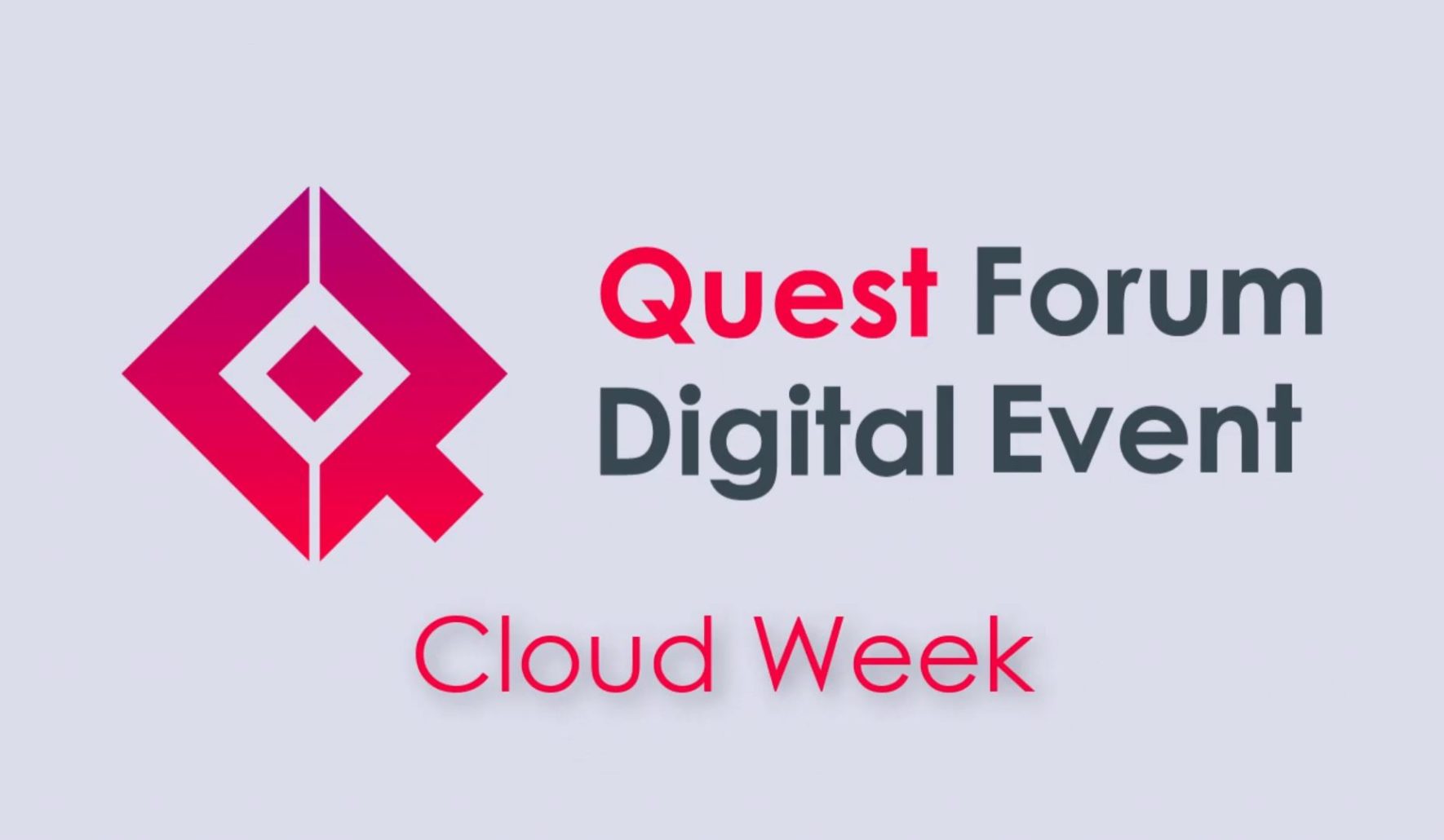
A rail logistics manager may also be responsible for the implementation of a stateof-the-art tracking program to track shipments, and ensure timely delivery. A tracking system is often used to notify customers about the location of a shipment.
The rail logistics manager might also be called upon to advise on ways to increase efficiency in transportation. He or she will be able help their company achieve more results in a less time.
Many of these roles can easily be learned from on-the-job experience and training. For example, a rail logistics coordinator requires a bachelor's degree along with years of experience in a related field.
FAQ
What are the main products of logistics?
Logistics refers to the movement of goods from one place to another.
They cover all aspects of transportation, such as packing, loading, transporting and unloading.
Logisticians make sure that the right product arrives at the right place at the correct time and in safe conditions. Logisticians help companies improve their supply chain efficiency by providing information about demand forecasts and stock levels, production schedules, as well as availability of raw materials.
They keep track and monitor the transit of shipments, maintain quality standards, order replenishment and inventories, coordinate with suppliers, vendors, and provide support for sales and marketing.
How does a Production Planner differ from a Project Manager?
The major difference between a Production Planner and a Project Manager is that a Project Manager is often the person responsible for organizing and planning the entire project. While a Production Planner is involved mainly in the planning stage,
Why should you automate your warehouse?
Modern warehousing has seen automation take center stage. E-commerce has brought increased demand for more efficient and quicker delivery times.
Warehouses must adapt quickly to meet changing customer needs. Technology is essential for warehouses to be able to adapt quickly to changing needs. Automation warehouses can bring many benefits. Here are some of the reasons automation is worth your investment:
-
Increases throughput/productivity
-
Reduces errors
-
Increases accuracy
-
Boosts safety
-
Eliminates bottlenecks
-
Companies can scale more easily
-
Makes workers more efficient
-
Provides visibility into everything that happens in the warehouse
-
Enhances customer experience
-
Improves employee satisfaction
-
It reduces downtime, and increases uptime
-
You can be sure that high-quality products will arrive on time
-
Eliminates human error
-
It helps ensure compliance with regulations
Statistics
- Many factories witnessed a 30% increase in output due to the shift to electric motors. (en.wikipedia.org)
- You can multiply the result by 100 to get the total percent of monthly overhead. (investopedia.com)
- According to the United Nations Industrial Development Organization (UNIDO), China is the top manufacturer worldwide by 2019 output, producing 28.7% of the total global manufacturing output, followed by the United States, Japan, Germany, and India.[52][53] (en.wikipedia.org)
- It's estimated that 10.8% of the U.S. GDP in 2020 was contributed to manufacturing. (investopedia.com)
- (2:04) MTO is a production technique wherein products are customized according to customer specifications, and production only starts after an order is received. (oracle.com)
External Links
How To
Six Sigma in Manufacturing:
Six Sigma is defined by "the application SPC (statistical process control) techniques to achieve continuous improvements." Motorola's Quality Improvement Department in Tokyo, Japan developed Six Sigma in 1986. Six Sigma's main goal is to improve process quality by standardizing processes and eliminating defects. Many companies have adopted this method in recent years. They believe there is no such thing a perfect product or service. Six Sigma aims to reduce variation in the production's mean value. If you take a sample and compare it with the average, you will be able to determine how much of the production process is different from the norm. If it is too large, it means that there are problems.
The first step toward implementing Six Sigma is understanding how variability works in your business. Once you've understood that, you'll want to identify sources of variation. These variations can also be classified as random or systematic. Random variations occur when people make mistakes; systematic ones are caused by factors outside the process itself. If you make widgets and some of them end up on the assembly line, then those are considered random variations. However, if you notice that every time you assemble a widget, it always falls apart at exactly the same place, then that would be a systematic problem.
Once you identify the problem areas, it is time to create solutions. This could mean changing your approach or redesigning the entire process. To verify that the changes have worked, you need to test them again. If they don't work you need to rework them and come up a better plan.