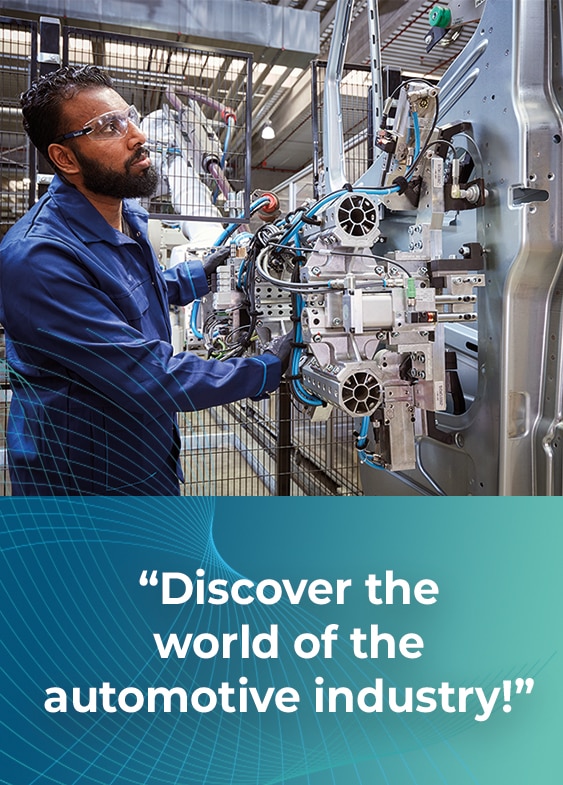
Six-Sigma, lean and Lean are complementary methods of improving processes. They both use the same tools for problem-solving, but each has different strengths and weaknesses. Six-Sigma, a statistical process control technique that uses statistical processes, is used in Lean. It starts with the idea that a product must have value and not just be produced. Lean is about reducing waste and improving the quality of products as they are being made.
Problem solving for PDCA
While there are differences between DMAIC and PDCA, both approaches are based on DMAIC. The PDCA cycle is more complex and requires more analysis. PDCA isn't as efficient for solving urgent issues like DMAIC. This approach requires technical skills and a lead problem-solver. Six Sigma's problem-solving leader will need to be a Six Sigma "green belt" practitioner.
Six Sigma uses a cycle introduced by W. Edwards Deming in the 1950s to solve problems. It was created to be used in combination with continuous improvement methods to rebuild Japan's industrial sectors. In the P (Plan) stage, real data must be gathered, and a clear mission statement must be created. After the PDCA phase, the team must agree on a solution.
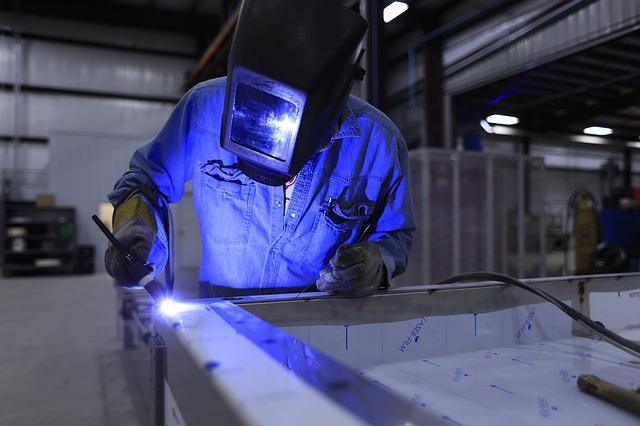
Process maps
One key difference between Six Sigma processes maps and Lean is the way each describes them. While both methods emphasize the importance of defining a process clearly, each method focuses on different aspects. Lean is a method of mapping actual processes, not standard operating protocols. Make sure to include major activities, decisions, approvals, and other sources of approval when creating process maps. Include areas that require multiple methods and factors. Match roles carefully and examine the flow of the process.
A process map should show steps, symbols, and even arrows. Each process should be reviewed by several people to ensure that it accurately reflects the actual process. Process maps should contain the date they were created as well as who to contact for questions. Overall, process maps can improve a process. They can be too complex.
Analyse Cause and Effect
Six Sigma and Lean project management techniques combine statistical analysis with stochastic optimization. The Cause and Effect Matrix or CAE is a method that links the outputs and inputs of a process. Customers' requirements are listed in order they are most important to them. Inputs and outputs are then ranked according to their impact on the outcome. Key process input variables and their ranking should be determined.
Although each technique may have its own set of benefits they are not all the same. Lean Six Sigma uses a process management methodology that is based around Frederick Winslow Taylor’s Principles of Scientific Management. Taylor saw business processes as interconnected processes and workflows. He also recommended reducing variation. Six-Sigma and Lean complement each other in the reduction of waste.
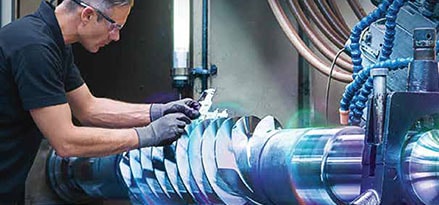
Elimination of variation
Variability is a normal part of any manufacturing process. This variability can create uncertainty in the result. It is important to maintain consistency in order to deliver professional results. Elimination of variation in Six Sigma and Lean manufacturing methods aims to achieve predictable output. Although some variation is normal, excessive variation can lead to problems, rework, or even worse, business consequences. It is best to identify the root causes of variation.
Look for variations at decision points first. Process maps, which are represented in diamonds, identify decision points. Six Sigma teams are able to identify decision points and begin eliminating variations. This information can be obtained from the Six Sigma team or the process owner. The Six Sigma Team cannot focus on any process that the owner isn't following a standardized process. A process map might not work if the Six Sigma team lacks the technical capability to make necessary adjustments.
FAQ
What are the products and services of logistics?
Logistics are the activities involved in moving goods from point A to point B.
These include all aspects related to transport such as packaging, loading and transporting, storing, transporting, unloading and warehousing inventory management, customer service. Distribution, returns, recycling are some of the options.
Logisticians make sure that the right product arrives at the right place at the correct time and in safe conditions. Logisticians assist companies in managing their supply chains by providing information such as demand forecasts, stock levels and production schedules.
They coordinate with vendors and suppliers, keep track of shipments, monitor quality standards and perform inventory and order replenishment.
Can we automate some parts of manufacturing?
Yes! Yes. Automation has been around since ancient time. The Egyptians invented the wheel thousands of years ago. We now use robots to help us with assembly lines.
There are many uses of robotics today in manufacturing. These include:
-
Line robots
-
Robot welding
-
Robot painting
-
Robotics inspection
-
Robots that produce products
Manufacturing can also be automated in many other ways. For example, 3D printing allows us to make custom products without having to wait for weeks or months to get them manufactured.
What are the jobs in logistics?
There are many jobs available in logistics. Some examples are:
-
Warehouse workers: They load and unload trucks, pallets, and other cargo.
-
Transportation drivers – These drivers drive trucks and wagons to transport goods and pick up the goods.
-
Freight handlers, - They sort out and pack freight in warehouses.
-
Inventory managers – These people oversee inventory at warehouses.
-
Sales representatives: They sell products to customers.
-
Logistics coordinators: They plan and manage logistics operations.
-
Purchasing agents are those who purchase goods and services for the company.
-
Customer service representatives are available to answer customer calls and emails.
-
Shipping clerks – They process shipping orders, and issue bills.
-
Order fillers - They fill orders based on what is ordered and shipped.
-
Quality control inspectors are responsible for inspecting incoming and outgoing products looking for defects.
-
Others - There are many other types of jobs available in logistics, such as transportation supervisors, cargo specialists, etc.
What does manufacturing mean?
Manufacturing Industries are those businesses that make products for sale. Consumers are those who purchase these products. To accomplish this goal, these companies employ a range of processes including distribution, sales, management, and production. These companies produce goods using raw materials and other equipment. This includes all types and varieties of manufactured goods, such as food items, clothings, building supplies, furnitures, toys, electronics tools, machinery vehicles, pharmaceuticals medical devices, chemicals, among others.
Statistics
- According to a Statista study, U.S. businesses spent $1.63 trillion on logistics in 2019, moving goods from origin to end user through various supply chain network segments. (netsuite.com)
- You can multiply the result by 100 to get the total percent of monthly overhead. (investopedia.com)
- [54][55] These are the top 50 countries by the total value of manufacturing output in US dollars for its noted year according to World Bank.[56] (en.wikipedia.org)
- (2:04) MTO is a production technique wherein products are customized according to customer specifications, and production only starts after an order is received. (oracle.com)
- It's estimated that 10.8% of the U.S. GDP in 2020 was contributed to manufacturing. (investopedia.com)
External Links
How To
How to Use the Just In Time Method in Production
Just-intime (JIT), a method used to lower costs and improve efficiency in business processes, is called just-in-time. This is where you have the right resources at the right time. This means you only pay what you use. Frederick Taylor developed the concept while working as foreman in early 1900s. After observing how workers were paid overtime for late work, he realized that overtime was a common practice. He realized that workers should have enough time to complete their jobs before they begin work. This would help increase productivity.
JIT teaches you to plan ahead and prepare everything so you don’t waste time. Also, you should look at the whole project from start-to-finish and make sure you have the resources necessary to address any issues. You will have the resources and people to solve any problems you anticipate. This will prevent you from spending extra money on unnecessary things.
There are different types of JIT methods:
-
Demand-driven: This type of JIT allows you to order the parts/materials required for your project on a regular basis. This will let you track the amount of material left over after you've used it. You'll also be able to estimate how long it will take to produce more.
-
Inventory-based: You stock materials in advance to make your projects easier. This allows you to forecast how much you will sell.
-
Project-driven : This is a method where you make sure that enough money is set aside to pay the project's cost. You will be able to purchase the right amount of materials if you know what you need.
-
Resource-based JIT: This type of JIT is most commonly used. Here, you allocate certain resources based on demand. For example, if there is a lot of work coming in, you will have more people assigned to them. If you don't have many orders, you'll assign fewer people to handle the workload.
-
Cost-based: This is a similar approach to resource-based but you are not only concerned with how many people you have, but also how much each one costs.
-
Price-based pricing: This is similar in concept to cost-based but instead you look at how much each worker costs, it looks at the overall company's price.
-
Material-based is an alternative to cost-based. Instead of looking at the total cost in the company, this method focuses on the average amount of raw materials that you consume.
-
Time-based JIT: This is another variant of resource-based JIT. Instead of worrying about how much each worker costs, you can focus on how long the project takes.
-
Quality-based JIT: Another variation on resource-based JIT. Instead of worrying about the costs of each employee or how long it takes for something to be made, you should think about how quality your product is.
-
Value-based JIT: This is the latest form of JIT. This is where you don't care about how the products perform or whether they meet customers' expectations. Instead, you're focused on how much value you add to the market.
-
Stock-based: This is an inventory-based method that focuses on the actual number of items being produced at any given time. It's used when you want to maximize production while minimizing inventory.
-
Just-in-time (JIT) planning: This is a combination of JIT and supply chain management. It's the process of scheduling delivery of components immediately after they are ordered. It is essential because it reduces lead-times and increases throughput.