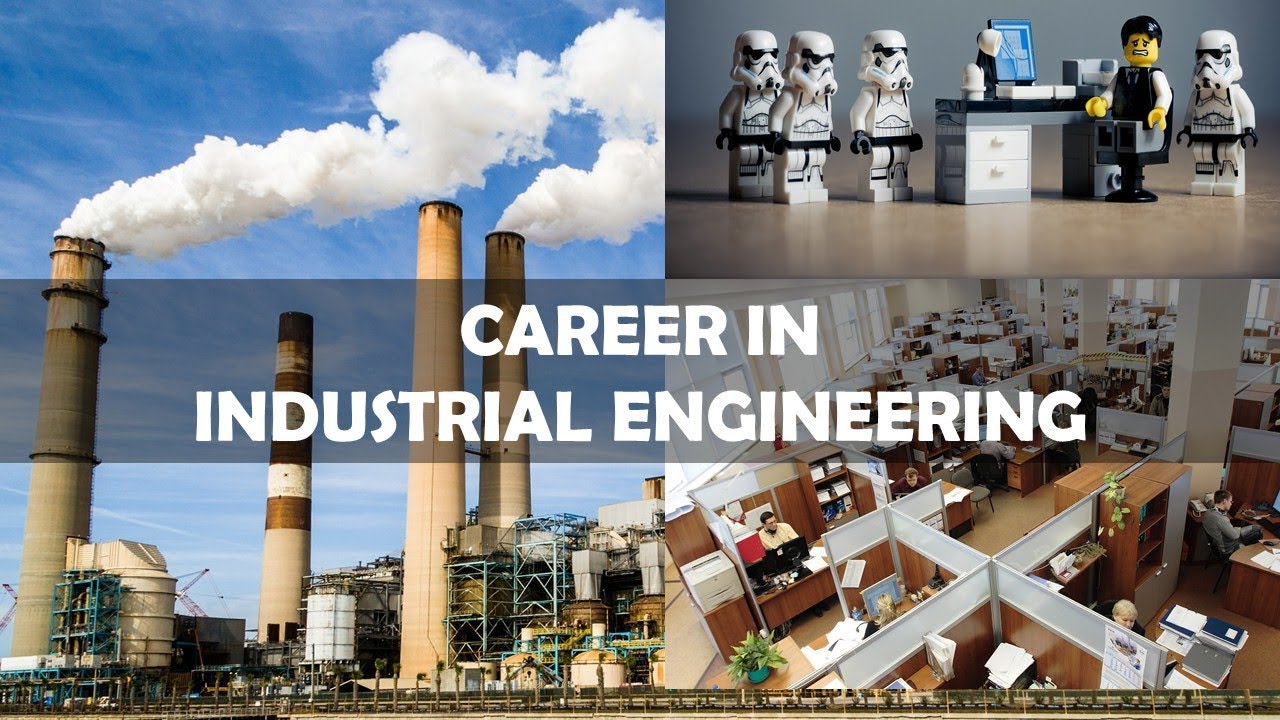
Visual management is the process of conveying information through the use of visual signals. This helps increase efficiency and clarity as the information can be immediately recognized. There are several kinds of visual control. Below are some of the more common examples. You can also learn about visual control in Lean Manufacturing. Read on to learn more. This method is a great way to get your company on track with lean manufacturing.
Lean manufacturing
One of the many methods used for visual management in lean manufacturing is the use of Andon, a Japanese word for status-display visualization. This technique allows supervisors and workers alike to see work-in progress, process flow, or any other pertinent information. Visual management allows for the easy labeling and marking of workspaces, materials or parts. This helps identify inefficiencies and streamlines processes. Below are some of the many benefits of visual control in lean manufacturing.
Visible tools for visual management are a crucial component of the Lean methodology. Operators and supervisors are able to see clearly and identify waste. They can also improve the process flow and prevent errors. It can also reduce safety concerns. By using visual indicators and floor markings, forklift operators can make sure they stay in the correct areas. Visual management is a key component of lean manufacturing. Workers will be able to work more efficiently if they use visual management. Visual management not only reduces waste but also reduces safety risks.

Process control charts
Process control charts can provide a visual tool to help visualize performance metrics, create a baseline, and improve output. These charts help operators, managers, and other stakeholders to get on the same page. They identify common causes of variation, set the right path for improvement, and help them communicate with each other. These charts are especially useful for processes with unusual patterns of variation. These process control charts are useful for visual management. They are easy to create, and can be used as visual indicators to see the status of any process.
The control chart serves the primary purpose of tracking process performance over time. These charts provide information about the sequence of measurements and samples taken. Managers can see if the process remains stable or not. These charts can also be used as an analytical tool to spot potential problems and offer solutions. The control chart's centerline is typically a line segment. It allows the operator to compare the process with its baseline. The control limits usually have three standard deviations from the centerline.
FIFO Lane
FIFO lanes may increase throughput or utilization of a system. Consider a fast food restaurant or assembly line. It is likely that you have felt the frustration of having to wait in long lines for something. FiFo lanes help you manage work flow by prioritizing queues using visual management. You can create these lanes by using paint lines, marking roller conveyors or clearly marking shelves. The first job from Process A would move into the first FIFO lane. The next job would be moved into the next open position.
One solution to improve FIFO lane visual management is to implement time registration. When carts are loaded into a FIFO lane, employees can log the time and date the items are put into the slot. Some employees count the products using digital clocks right after putting them into the FIFO lane. To record time on carts you can use whiteboard stickers. These whiteboard stickers will allow downstream employees to refer to the times and determine which order they should take.
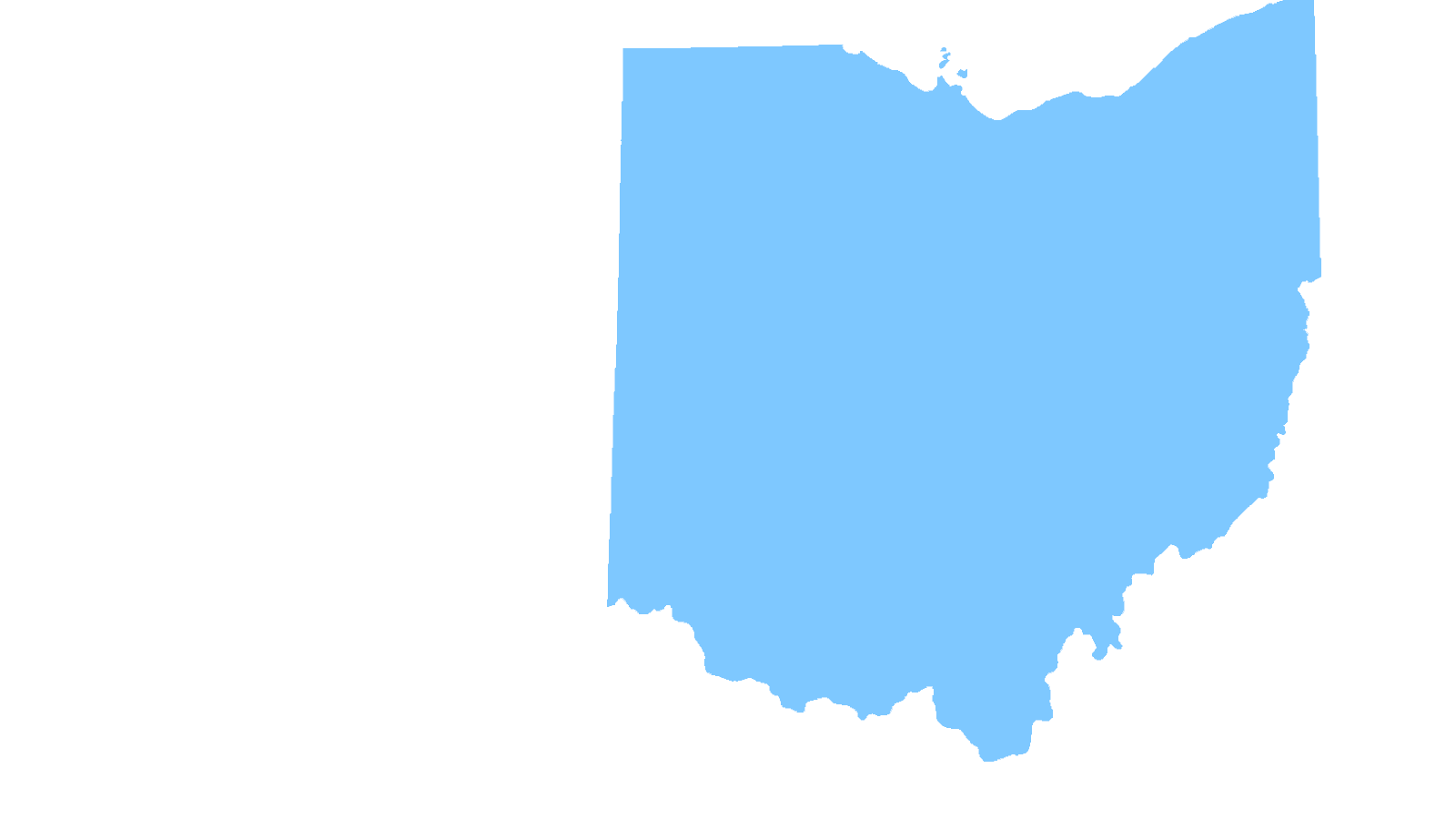
Lean daily management board
A multidisciplinary team developed the Lean Daily Management Board. It was based on five predetermined measures: patient outcomes (documentation adherence), employee engagement, productivity, and documentation adherence. This team met daily to review progress in each area. To verify every daily activity, the team used a checklist. To address any problems, they also used a problem-solving tool. Initial data from January 2014 showed a 75% medication scan and a fall of 1.32/1000 patients days. These initial data weren't specific to patient care nor continuing education.
Daily management is more than just looking at the performance of a process over a long time. It makes it visible so managers can respond to any problems that arise. Poor performers will not accept more work. Poor performers will have to make their stretching work visible in order to take into account the extra effort and time it takes. Daily management is not meant to be harsh, but it can highlight inefficient or ineffective processes. People issues should be considered for those who are unable to point out a failure in a process.
FAQ
How can manufacturing reduce production bottlenecks?
You can avoid bottlenecks in production by making sure that everything runs smoothly throughout the production cycle, from the moment you receive an order to the moment the product is shipped.
This includes both planning for capacity and quality control.
Continuous improvement techniques like Six Sigma are the best way to achieve this.
Six Sigma is a management method that helps to improve quality and reduce waste.
It's all about eliminating variation and creating consistency in work.
How can manufacturing overproduction be reduced?
Improved inventory management is the key to reducing overproduction. This would reduce the time spent on unproductive activities like purchasing, storing and maintaining excess stock. We could use these resources to do other productive tasks.
A Kanban system is one way to achieve this. A Kanban board is a visual display used to track work in progress. Kanban systems allow work items to move through different states until they reach their final destination. Each state represents an individual priority level.
To illustrate, work can move from one stage or another when it is complete enough for it to be moved to a new stage. But if a task remains in the beginning stages it will stay that way until it reaches its end.
This allows for work to continue moving forward, while also ensuring that there is no work left behind. Managers can see how much work has been done and the status of each task at any time with a Kanban Board. This data allows them adjust their workflow based upon real-time data.
Another way to control inventory levels is to implement lean manufacturing. Lean manufacturing works to eliminate waste throughout every stage of the production chain. Anything that does nothing to add value to a product is waste. Here are some examples of common types.
-
Overproduction
-
Inventory
-
Unnecessary packaging
-
Material surplus
By implementing these ideas, manufacturers can improve efficiency and cut costs.
What is the job of a logistics manger?
A logistics manager ensures that all goods are delivered on time and without damage. This is done by using his/her experience and knowledge of the company's products. He/she should also ensure enough stock is available to meet demand.
Is automation important in manufacturing?
Automating is not just important for manufacturers, but also for service providers. Automation allows them to deliver services quicker and more efficiently. It reduces human errors and improves productivity, which in turn helps them lower their costs.
What are the 4 types of manufacturing?
Manufacturing is the process that transforms raw materials into useful products. Manufacturing can include many activities such as designing and building, testing, packaging shipping, selling, servicing, and other related activities.
Statistics
- Job #1 is delivering the ordered product according to specifications: color, size, brand, and quantity. (netsuite.com)
- According to the United Nations Industrial Development Organization (UNIDO), China is the top manufacturer worldwide by 2019 output, producing 28.7% of the total global manufacturing output, followed by the United States, Japan, Germany, and India.[52][53] (en.wikipedia.org)
- [54][55] These are the top 50 countries by the total value of manufacturing output in US dollars for its noted year according to World Bank.[56] (en.wikipedia.org)
- Many factories witnessed a 30% increase in output due to the shift to electric motors. (en.wikipedia.org)
- In the United States, for example, manufacturing makes up 15% of the economic output. (twi-global.com)
External Links
How To
How to use Lean Manufacturing in the production of goods
Lean manufacturing (or lean manufacturing) is a style of management that aims to increase efficiency, reduce waste and improve performance through continuous improvement. It was first developed in Japan in the 1970s/80s by Taiichi Ahno, who was awarded the Toyota Production System (TPS), award from KanjiToyoda, the founder of TPS. Michael L. Watkins published the book "The Machine That Changed the World", which was the first to be published about lean manufacturing.
Lean manufacturing is often defined as a set of principles used to improve the quality, speed, and cost of products and services. It emphasizes eliminating waste and defects throughout the value stream. Lean manufacturing is called just-in-time (JIT), zero defect, total productive maintenance (TPM), or 5S. Lean manufacturing seeks to eliminate non-value added activities, such as inspection, work, waiting, and rework.
Lean manufacturing improves product quality and costs. It also helps companies reach their goals quicker and decreases employee turnover. Lean manufacturing can be used to manage all aspects of the value chain. Customers, suppliers, distributors, retailers and employees are all included. Lean manufacturing is widely practiced in many industries around the world. Toyota's philosophy is the foundation of its success in automotives, electronics and appliances, healthcare, chemical engineers, aerospace, paper and food, among other industries.
Five basic principles of Lean Manufacturing are included in lean manufacturing
-
Define Value- Identify the added value your company brings to society. What makes you stand out from your competitors?
-
Reduce Waste – Eliminate all activities that don't add value throughout the supply chain.
-
Create Flow – Ensure that work flows smoothly throughout the process.
-
Standardize and simplify - Make your processes as consistent as possible.
-
Build relationships - Develop and maintain personal relationships with both your internal and external stakeholders.
Although lean manufacturing has always been around, it is gaining popularity in recent years because of a renewed interest for the economy after 2008's global financial crisis. Many companies have adopted lean manufacturing methods to increase their marketability. Some economists even believe that lean manufacturing can be a key factor in economic recovery.
Lean manufacturing is becoming a popular practice in automotive. It has many advantages. These benefits include increased customer satisfaction, reduced inventory levels and lower operating costs.
It can be applied to any aspect of an organisation. Lean manufacturing is most useful in the production sector of an organisation because it ensures that each step in the value-chain is efficient and productive.
There are three types of lean manufacturing.
-
Just-in-Time Manufacturing (JIT): This type of lean manufacturing is commonly referred to as "pull systems." JIT is a process in which components can be assembled at the point they are needed, instead of being made ahead of time. This approach reduces lead time, increases availability and reduces inventory.
-
Zero Defects Manufacturing (ZDM): ZDM focuses on ensuring that no defective units leave the manufacturing facility. Repairing a part that is damaged during assembly should be done, not scrapping. This is true even for finished products that only require minor repairs prior to shipping.
-
Continuous Improvement (CI: Continuous improvement aims to increase the efficiency of operations by constantly identifying and making improvements to reduce or eliminate waste. Continuous Improvement involves continuous improvement of processes.