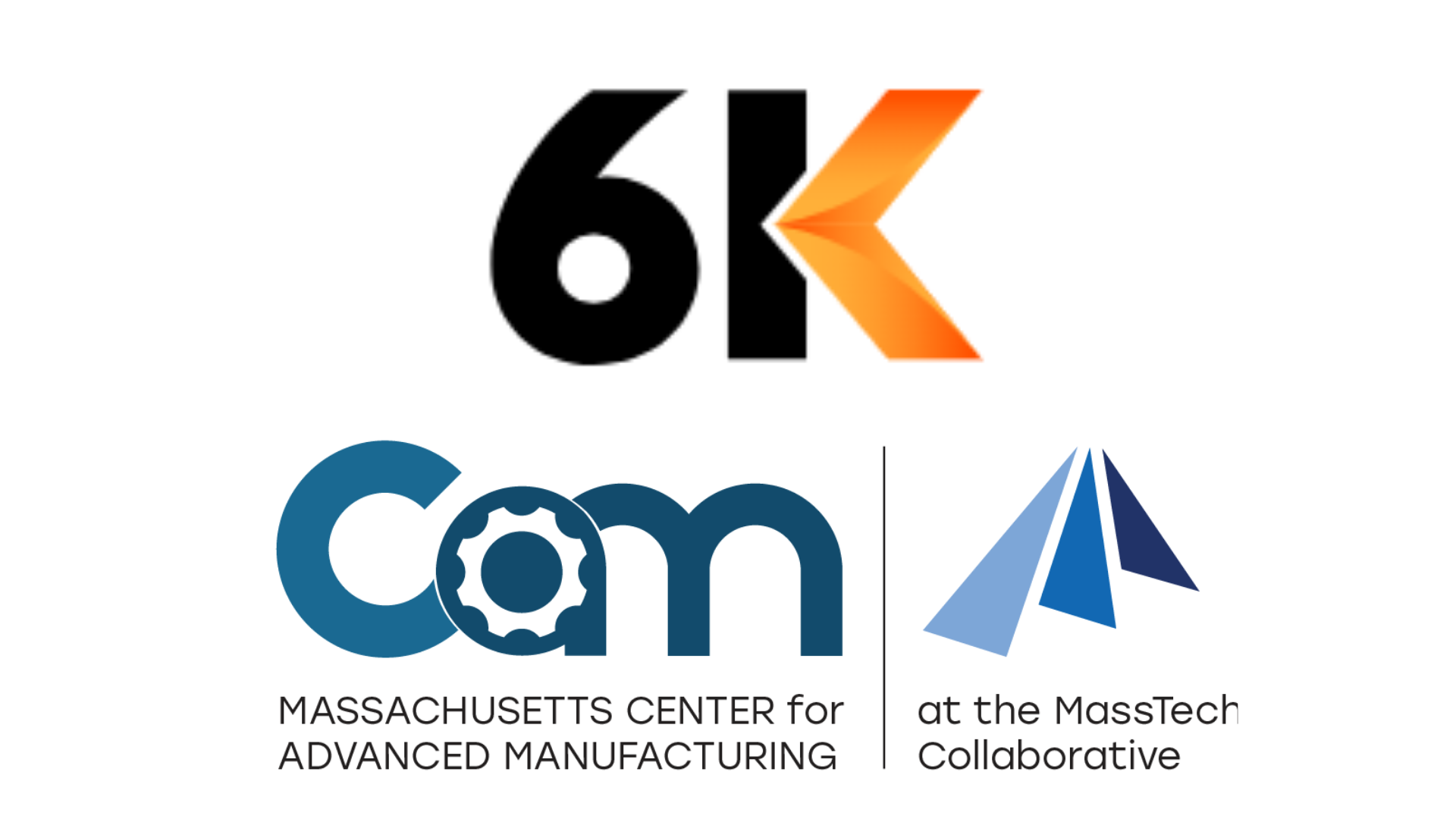
Heijunka was originally developed by Toyota, the Japanese automaker. It is a lean production technique that increases efficiency in multi-step production. This reduces waste by making sure that the production schedule matches customer demand. This reduces production fluctuations and helps to reduce waste. Heijunka allows manufacturers to respond to customer needs and maximize their profits.
Heijunka is a process of coordinating small production batches across manufacturing lines. It is used to improve efficiency in multi-step production processes, especially when just-in-time principles are used. It is also part in the Toyota Production System. It helps reduce waste by leveling production, mixing products and minimizing batch sizes.
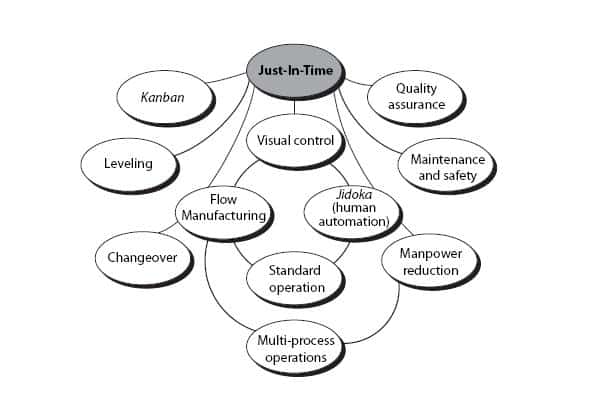
There are two possible ways to use heijunka. The first is to use a heijunkabox, which is a grid made up of small boxes that can be fixed or mounted on a wall. It serves as a visual management tool to allow production personnel schedule and visualize the production processes. Magnetic cards can also be used to implement Heijunka.
Toyota dealers use Heijunka as a production method to speed up changeover times. It is also an important method in the Toyota Lean framework. Heijunka helps manufacturers reduce inventory and increase production. Heijunka makes it easier to use labor and equipment. It provides a lean production system that reduces waste, thereby making better products available to customers.
You must be able to understand the takt time (also known as the customer purchasing rate) before you can use heijunka. This is the time required to produce a product in order to satisfy customer demand. Heijunka uses this takt to determine the production rate. You can calculate how many products you want to make and at what rate customers will buy your products using the takttime. Back-office settings can also use the Takt Time to determine the rate at which customers purchase company products.
Production personnel can visual plan and schedule the production process with the help of the heijunkabox. The heijunka container can also be used on the shop floor to visualize production processes. The heijunka box is made up of rows and columns which represent each product type or component. The column of boxes represents each time period of the day, and the rows of boxes represent each product type.
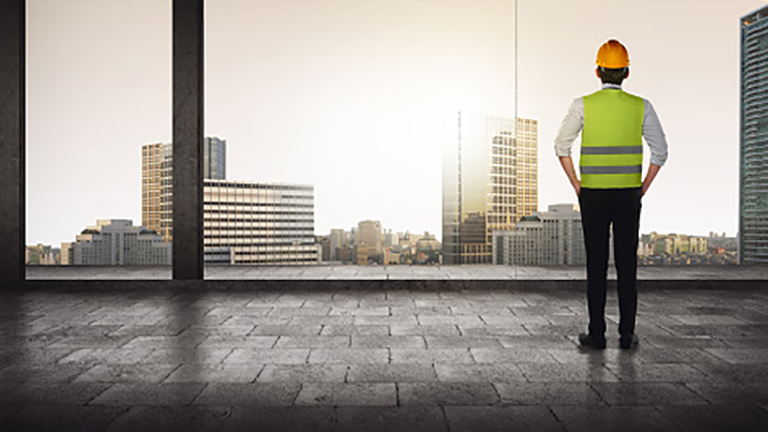
Heijunka Box is one of the most common visual management tools used in production. This tool allows you to see the relationships between component production and product production. It also provides a visual representation of the production workload for the week. It is used together with the kanban deck, which is a set of colored cards that represents the product required for each production step. Kanban card are usually removed from the heijunka box within a given time frame and delivered to the designated production area.
FAQ
How is a production manager different from a producer planner?
The major difference between a Production Planner and a Project Manager is that a Project Manager is often the person responsible for organizing and planning the entire project. While a Production Planner is involved mainly in the planning stage,
Can we automate some parts of manufacturing?
Yes! Yes. The Egyptians discovered the wheel thousands and years ago. We now use robots to help us with assembly lines.
There are many applications for robotics in manufacturing today. They include:
-
Robots for assembly line
-
Robot welding
-
Robot painting
-
Robotics inspection
-
Robots that make products
There are many other examples of how manufacturing could benefit from automation. 3D printing, for example, allows us to create custom products without waiting for them to be made.
What does "warehouse" mean?
A warehouse or storage facility is where goods are stored before they are sold. It can be an indoor space or an outdoor area. In some cases, it may be a combination of both.
How can manufacturing overproduction be reduced?
The key to reducing overproduction lies in developing better ways to manage inventory. This would reduce the amount of time spent on unnecessary activities such as purchasing, storing, and maintaining excess stock. By doing this, we could free up resources for other productive tasks.
A Kanban system is one way to achieve this. A Kanbanboard is a visual tool that allows you to keep track of the work being done. Work items are moved through various states to reach their destination in a Kanban system. Each state is assigned a different priority.
For instance, when work moves from one stage to another, the current task is complete enough to be moved to the next stage. A task that is still in the initial stages of a process will be considered complete until it moves on to the next stage.
This allows you to keep work moving along while making sure that no work gets neglected. A Kanban board allows managers to monitor how much work is being completed at any given moment. This allows them the ability to adjust their workflow using real-time data.
Lean manufacturing is another way to manage inventory levels. Lean manufacturing seeks to eliminate waste from every step of the production cycle. Anything that doesn't add value to the product is considered waste. The following are examples of common waste types:
-
Overproduction
-
Inventory
-
Packaging that is not necessary
-
Exceed materials
These ideas can help manufacturers improve efficiency and reduce costs.
What types of jobs can you find in logistics
There are many jobs available in logistics. Here are some:
-
Warehouse workers – They load and unload pallets and trucks.
-
Transportation drivers – These drivers drive trucks and wagons to transport goods and pick up the goods.
-
Freight handlers: They sort and package freight in warehouses.
-
Inventory managers - They oversee the inventory of goods in warehouses.
-
Sales representatives - They sell products to customers.
-
Logistics coordinators – They plan and coordinate logistics operations.
-
Purchasing agents - They buy goods and services that are necessary for company operations.
-
Customer service agents - They answer phone calls and respond to emails.
-
Shipping clerks: They process shipping requests and issue bills.
-
Order fillers: They fill orders based off what has been ordered and shipped.
-
Quality control inspectors are responsible for inspecting incoming and outgoing products looking for defects.
-
Others – There are many other types available in logistics. They include transport supervisors, cargo specialists and others.
What does manufacturing industry mean?
Manufacturing Industries are businesses that produce products for sale. Consumers are the people who purchase these products. This is accomplished by using a variety of processes, including production, distribution and retailing. They make goods from raw materials with machines and other equipment. This covers all types of manufactured goods including clothing, food, building supplies and furniture, as well as electronics, tools, machinery, vehicles and pharmaceuticals.
Statistics
- [54][55] These are the top 50 countries by the total value of manufacturing output in US dollars for its noted year according to World Bank.[56] (en.wikipedia.org)
- Job #1 is delivering the ordered product according to specifications: color, size, brand, and quantity. (netsuite.com)
- According to the United Nations Industrial Development Organization (UNIDO), China is the top manufacturer worldwide by 2019 output, producing 28.7% of the total global manufacturing output, followed by the United States, Japan, Germany, and India.[52][53] (en.wikipedia.org)
- (2:04) MTO is a production technique wherein products are customized according to customer specifications, and production only starts after an order is received. (oracle.com)
- You can multiply the result by 100 to get the total percent of monthly overhead. (investopedia.com)
External Links
How To
How to Use 5S to Increase Productivity in Manufacturing
5S stands in for "Sort", the "Set In Order", "Standardize", or "Separate". The 5S methodology was developed at Toyota Motor Corporation in 1954. This methodology helps companies improve their work environment to increase efficiency.
The idea behind standardizing production processes is to make them repeatable and measurable. This means that daily tasks such as cleaning and sorting, storage, packing, labeling, and packaging are possible. This knowledge allows workers to be more efficient in their work because they are aware of what to expect.
Implementing 5S requires five steps. These are Sort, Set In Order, Standardize. Separate. And Store. Each step requires a different action to increase efficiency. By sorting, for example, you make it easy to find the items later. When you arrange items, you place them together. Once you have separated your inventory into groups and organized them, you will store these groups in easily accessible containers. You can also label your containers to ensure everything is properly labeled.
Employees must be able to critically examine their work practices. Employees should understand why they do the tasks they do, and then decide if there are better ways to accomplish them. To implement the 5S system, employees must acquire new skills and techniques.
The 5S method not only increases efficiency but also boosts morale and teamwork. They feel more motivated to work towards achieving greater efficiency as they see the results.