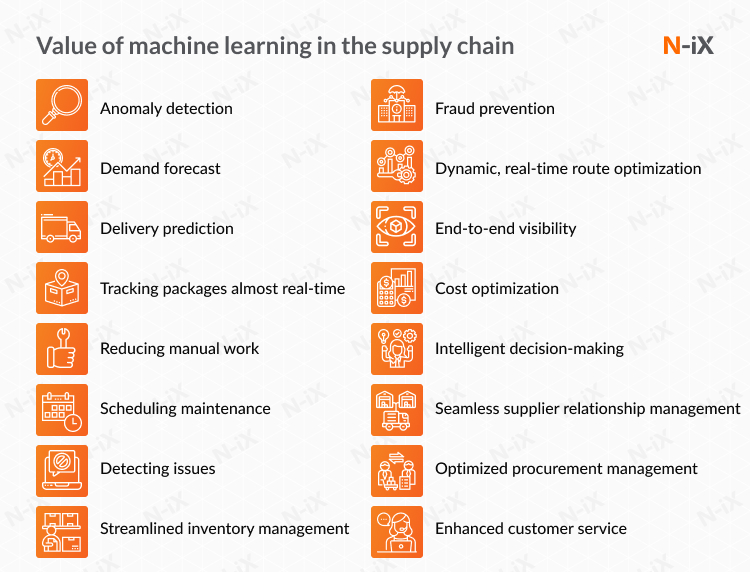
Industrial engineers are experts who use their knowledge in manufacturing technology and improve processes. They develop new methods and analyze existing systems. As a result of their expertise, they are highly valuable in research and development firms, engineering services, and consulting.
Industrial engineers can work in many settings, but they are focused on reducing waste, improving production processes and reducing internal cost. This group uses creativity and logic to develop new production processes. Some industrial engineers are involved in automated manufacturing processes.
A vast knowledge base in mathematics and scientific principles is required for industrial engineers. They must also be skilled at problem-solving as well as critical thinking. They should also be able to communicate well and work with others. Ideally, industrial engineers will be able to take a broad system's view and identify weaknesses and strengths of alternative solutions.

If you want to pursue an industrial engineering career, you'll need to complete a bachelor's degree and gain at least four years of experience. After that, you will be eligible to apply for certification by the Society of Manufacturing Engineers. The master's degree will enable you to specialize in your chosen field.
They are highly sought-after and are expected to see their employment opportunities grow faster than average over the next ten. During this time, employment of this professional is projected to increase by 10 percent. The majority of the work can be done on a full-time basis. Hours may vary depending on what the project calls for. Nashville's median industrial engineer salary is $73,856 However, depending on your geographic location, the employer, and your personal qualifications, the wage could vary from one employer the next.
When looking for an industrial engineering job in Nashville, it's important to highlight your educational and professional credentials. Industry-specific certifications are also required. A professional engineer license is required if you plan to work for a government agency.
Many companies offer internships for interns to help with industrial engineering. Interns are taught about lean manufacturing and value stream mapping. You might be able to climb the ladder to management depending on your abilities and the company.
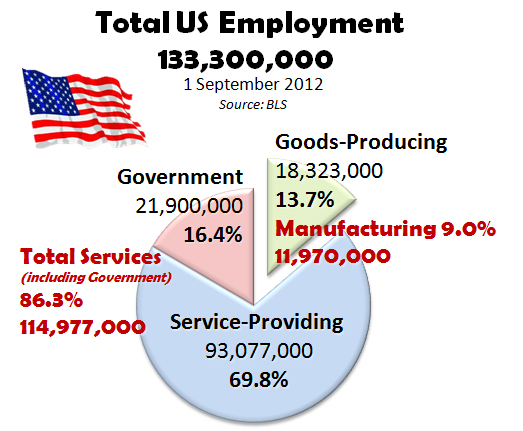
No matter where you are working, interpersonal communication skills will be essential to help you communicate effectively with your managers and colleagues. Besides communicating with fellow workers, you'll also need to be able to work with customers and vendors.
A variety of industries are looking for skilled industrial engineers. These include transportation equipment manufacturers, computer and electronics manufacturers, and engineering service firms. Numerous colleges offer 5-year programs in industrial engineering. While many graduates are able to find entry-level positions in multiple industries, a few are more focused on certain specialty areas, such as automated manufacturing processes.
FAQ
What can I do to learn more about manufacturing?
Experience is the best way for you to learn about manufacturing. However, if that's not possible, you can always read books or watch educational videos.
What do we need to know about Manufacturing Processes in order to learn more about Logistics?
No. No. But, being familiar with manufacturing processes will give you a better understanding about how logistics works.
What are the essential elements of running a logistics firm?
You need to have a lot of knowledge and skills to manage a successful logistic business. To communicate effectively with clients and suppliers, you must be able to communicate well. You must be able analyze data and draw out conclusions. You must be able to work well under pressure and handle stressful situations. You need to be innovative and creative to come up with new ways to increase efficiency. You need to have strong leadership qualities to motivate team members and direct them towards achieving organizational goals.
It is also important to be efficient and well organized in order meet deadlines.
Why is logistics important for manufacturing?
Logistics are essential to any business. They help you achieve great results by helping you manage all aspects of product flow, from raw materials to finished goods.
Logistics play a key role in reducing expenses and increasing efficiency.
How can overproduction in manufacturing be reduced?
Improved inventory management is the key to reducing overproduction. This would reduce time spent on activities such as purchasing, stocking, and maintaining excess stock. We could use these resources to do other productive tasks.
This can be done by using a Kanban system. A Kanban Board is a visual display that tracks work progress. Kanban systems allow work items to move through different states until they reach their final destination. Each state represents an individual priority level.
To illustrate, work can move from one stage or another when it is complete enough for it to be moved to a new stage. However, if a task is still at the beginning stages, it will remain so until it reaches the end of the process.
This keeps work moving and ensures no work is lost. With a Kanban board, managers can see exactly how much work is being done at any given moment. This data allows them adjust their workflow based upon real-time data.
Lean manufacturing is another way to manage inventory levels. Lean manufacturing seeks to eliminate waste from every step of the production cycle. Anything that does not contribute to the product's value is considered waste. These are some of the most common types.
-
Overproduction
-
Inventory
-
Packaging that is not necessary
-
Excess materials
By implementing these ideas, manufacturers can improve efficiency and cut costs.
Statistics
- It's estimated that 10.8% of the U.S. GDP in 2020 was contributed to manufacturing. (investopedia.com)
- You can multiply the result by 100 to get the total percent of monthly overhead. (investopedia.com)
- Job #1 is delivering the ordered product according to specifications: color, size, brand, and quantity. (netsuite.com)
- (2:04) MTO is a production technique wherein products are customized according to customer specifications, and production only starts after an order is received. (oracle.com)
- According to a Statista study, U.S. businesses spent $1.63 trillion on logistics in 2019, moving goods from origin to end user through various supply chain network segments. (netsuite.com)
External Links
How To
How to use Lean Manufacturing in the production of goods
Lean manufacturing is a management system that aims at increasing efficiency and reducing waste. It was first developed in Japan in the 1970s/80s by Taiichi Ahno, who was awarded the Toyota Production System (TPS), award from KanjiToyoda, the founder of TPS. Michael L. Watkins published the original book on lean manufacturing, "The Machine That Changed the World," in 1990.
Lean manufacturing is often described as a set if principles that help improve the quality and speed of products and services. It emphasizes the elimination of defects and waste throughout the value stream. Just-in-time (JIT), zero defect (TPM), and 5S are all examples of lean manufacturing. Lean manufacturing focuses on eliminating non-value-added activities such as rework, inspection, and waiting.
In addition to improving product quality and reducing costs, lean manufacturing helps companies achieve their goals faster and reduces employee turnover. Lean manufacturing is considered one of the most effective ways to manage the entire value chain, including suppliers, customers, distributors, retailers, and employees. Many industries worldwide use lean manufacturing. Toyota's philosophy is a great example of this. It has helped to create success in automobiles as well electronics, appliances and healthcare.
Five principles are the basis of lean manufacturing:
-
Define Value: Identify the social value of your business and what sets you apart.
-
Reduce Waste – Eliminate all activities that don't add value throughout the supply chain.
-
Create Flow: Ensure that the work process flows without interruptions.
-
Standardize & Simplify - Make processes as consistent and repeatable as possible.
-
Build relationships - Develop and maintain personal relationships with both your internal and external stakeholders.
Lean manufacturing, although not new, has seen renewed interest in the economic sector since 2008. Many companies have adopted lean manufacturing methods to increase their marketability. In fact, some economists believe that lean manufacturing will be an important factor in economic recovery.
Lean manufacturing is now becoming a common practice in the automotive industry, with many benefits. These include improved customer satisfaction, reduced inventory levels, lower operating costs, increased productivity, and better overall safety.
You can apply Lean Manufacturing to virtually any aspect of your organization. Because it makes sure that all value chains are efficient and effectively managed, Lean Manufacturing is particularly helpful for organizations.
There are three main types:
-
Just-in Time Manufacturing (JIT), also known as "pull system": This form of lean manufacturing is often referred to simply as "pull". JIT is a process in which components can be assembled at the point they are needed, instead of being made ahead of time. This method reduces lead times, increases availability, and decreases inventory.
-
Zero Defects Manufacturing (ZDM): ZDM focuses on ensuring that no defective units leave the manufacturing facility. If a part is required to be repaired on the assembly line, it should not be scrapped. This also applies to finished products that need minor repairs before being shipped.
-
Continuous Improvement: Continuous Improvement aims to improve efficiency by continually identifying problems and making adjustments to eliminate or minimize waste. Continuous improvement refers to continuous improvement of processes as well people and tools.