
We need to know why things went wrong. These moments are when we turn to a process called the five whys, which is all about asking a series of questions to discover the root cause of a problem.
The 5 Whys can help teams solve problems by helping them communicate. It helps to foster curiosity and help teams understand each others' perspectives, so they can work with one another to find solutions. It also provides a fall-back interrogation system for when team members aren't sure why an issue occurred or what to do about it.
What is Five Whys Method Methodology?
It is easy to use, but very effective. This method is most useful for solving simple to moderate issues but can be used even in more complicated cases.
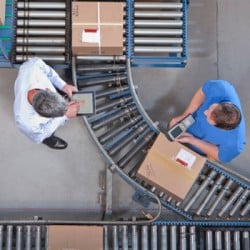
In some cases, the nature of a problem may require more than five possible reasons to be used during the investigation. This is especially true when there are several potential root causes.
How to Use 5 Whys Method
The first step in completing a successful five whys analysis is to assemble a team of individuals who are familiar with the issue at hand. You can bring together people from different industries and departments. It will enable them to offer a diverse range of perspectives and ideas that may help better pinpoint the root cause of any problem.
After the team has been assembled, the members should begin by discussing the issue and asking the five Whys questions. This will enable them to pinpoint the issue's root cause, and determine whether an immediate fix is possible or if long-term measures are needed to stop it happening again.
Next, they must carefully review each question and determine if a reasonable reply is produced. This step is crucial because it will help them feel confident that their analysis is going well.
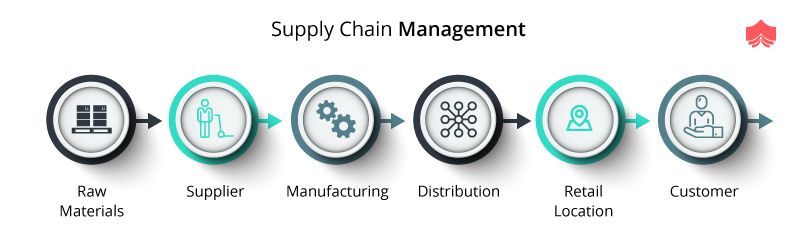
Continue asking the five whys, until you are able determine the root of the problem. Next, come up with countermeasures which will stop the issue from happening in the future. Once the root problem is identified, assign each corrective action to the person who will be responsible for it.
The five whys can be used to determine the root causes of any issue that is causing problems within your organization. It is most effective when used with other tools to understand root causes, like FMEA analysis or cause-and effect analysis.
FAQ
How can overproduction in manufacturing be reduced?
It is essential to find better ways to manage inventory to reduce overproduction. This would reduce the time needed to manage inventory. This would allow us to use our resources for more productive tasks.
You can do this by adopting a Kanban method. A Kanban board can be used to monitor work progress. Work items are moved through various states to reach their destination in a Kanban system. Each state represents a different priority.
As an example, if work is progressing from one stage of the process to another, then the current task is complete and can be transferred to the next. However, if a task is still at the beginning stages, it will remain so until it reaches the end of the process.
This allows work to move forward and ensures that no work is missed. Managers can monitor the work being done by Kanban boards to see what is happening at any given time. This information allows managers to adjust their workflow based off real-time data.
Another way to control inventory levels is to implement lean manufacturing. Lean manufacturing seeks to eliminate waste from every step of the production cycle. Any product that isn't adding value can be considered waste. Some common types of waste include:
-
Overproduction
-
Inventory
-
Unnecessary packaging
-
Materials in excess
These ideas can help manufacturers improve efficiency and reduce costs.
Why automate your warehouse
Modern warehouses have become more dependent on automation. The rise of e-commerce has led to increased demand for faster delivery times and more efficient processes.
Warehouses need to adapt quickly to meet changing needs. In order to do this, they need to invest in technology. Automation of warehouses offers many benefits. Here are some benefits of investing in automation
-
Increases throughput/productivity
-
Reduces errors
-
Increases accuracy
-
Safety Boosts
-
Eliminates bottlenecks
-
Companies can scale up more easily
-
Workers are more productive
-
The warehouse can be viewed from all angles.
-
Enhances customer experience
-
Improves employee satisfaction
-
It reduces downtime, and increases uptime
-
You can be sure that high-quality products will arrive on time
-
Eliminates human error
-
It helps ensure compliance with regulations
What is the best way to learn about manufacturing?
You can learn the most about manufacturing by getting involved in it. However, if that's not possible, you can always read books or watch educational videos.
What are the jobs in logistics?
There are many jobs available in logistics. Here are some examples:
-
Warehouse workers - They load trucks and pallets.
-
Transportation drivers – These drivers drive trucks and wagons to transport goods and pick up the goods.
-
Freight handlers, - They sort out and pack freight in warehouses.
-
Inventory managers - They oversee the inventory of goods in warehouses.
-
Sales reps - They sell products and services to customers.
-
Logistics coordinators: They plan and manage logistics operations.
-
Purchasing agents: They are responsible for purchasing goods and services to support company operations.
-
Customer service representatives - They answer calls and emails from customers.
-
Shipping clerks: They process shipping requests and issue bills.
-
Order fillers: They fill orders based off what has been ordered and shipped.
-
Quality control inspectors – They inspect incoming and outgoing products to ensure that there are no defects.
-
Others - There are many other types of jobs available in logistics, such as transportation supervisors, cargo specialists, etc.
How can manufacturing reduce production bottlenecks?
Production bottlenecks can be avoided by ensuring that processes are running smoothly during the entire production process, starting with the receipt of an order and ending when the product ships.
This includes both quality control and capacity planning.
Continuous improvement techniques such Six Sigma can help you achieve this.
Six Sigma can be used to improve the quality and decrease waste in all areas of your company.
It seeks to eliminate variation and create consistency in your work.
What are the responsibilities of a manufacturing manager
Manufacturing managers must ensure that manufacturing processes are efficient, effective, and cost-effective. They must also be alert to any potential problems and take appropriate action.
They should also know how to communicate with other departments such as sales and marketing.
They should be up to date on the latest trends and be able apply this knowledge to increase productivity and efficiency.
What are the goods of logistics?
Logistics refers to the movement of goods from one place to another.
They cover all aspects of transportation, such as packing, loading, transporting and unloading.
Logisticians make sure that the right product arrives at the right place at the correct time and in safe conditions. Logisticians help companies improve their supply chain efficiency by providing information about demand forecasts and stock levels, production schedules, as well as availability of raw materials.
They keep track and monitor the transit of shipments, maintain quality standards, order replenishment and inventories, coordinate with suppliers, vendors, and provide support for sales and marketing.
Statistics
- You can multiply the result by 100 to get the total percent of monthly overhead. (investopedia.com)
- It's estimated that 10.8% of the U.S. GDP in 2020 was contributed to manufacturing. (investopedia.com)
- [54][55] These are the top 50 countries by the total value of manufacturing output in US dollars for its noted year according to World Bank.[56] (en.wikipedia.org)
- According to the United Nations Industrial Development Organization (UNIDO), China is the top manufacturer worldwide by 2019 output, producing 28.7% of the total global manufacturing output, followed by the United States, Japan, Germany, and India.[52][53] (en.wikipedia.org)
- (2:04) MTO is a production technique wherein products are customized according to customer specifications, and production only starts after an order is received. (oracle.com)
External Links
How To
How to use 5S to increase Productivity in Manufacturing
5S stands for "Sort", "Set In Order", "Standardize", "Separate" and "Store". Toyota Motor Corporation was the first to develop the 5S approach in 1954. It improves the work environment and helps companies to achieve greater efficiency.
This approach aims to standardize production procedures, making them predictable, repeatable, and easily measurable. This means that tasks such as cleaning, sorting, storing, packing, and labeling are performed daily. Because workers know what they can expect, this helps them perform their jobs more efficiently.
Implementing 5S requires five steps. These are Sort, Set In Order, Standardize. Separate. And Store. Each step is a different action that leads to greater efficiency. By sorting, for example, you make it easy to find the items later. Once you have placed items in an ordered fashion, you will put them together. Once you have separated your inventory into groups and organized them, you will store these groups in easily accessible containers. Make sure everything is correctly labeled when you label your containers.
Employees must be able to critically examine their work practices. Employees should understand why they do the tasks they do, and then decide if there are better ways to accomplish them. To be successful in the 5S system, employees will need to acquire new skills and techniques.
The 5S method increases efficiency and morale among employees. They are more motivated to achieve higher efficiency levels as they start to see improvement.