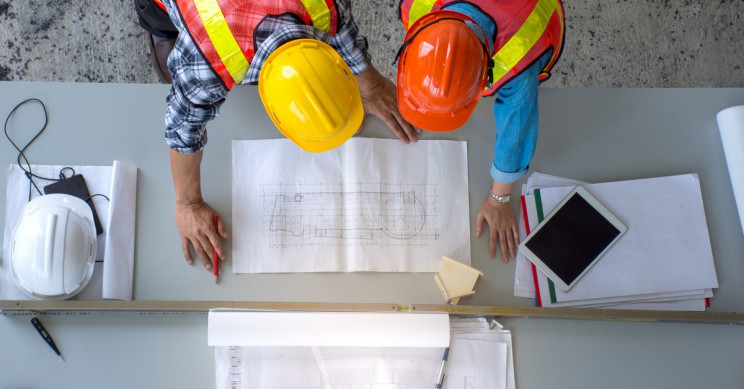
As the Internet of Things (IoT) transforms the manufacturing industry, cybersecurity for manufacturers is critical. Companies need to ensure their assets, customer data, and designs are secure in the face of increasing cyberattacks. Companies can use the right technology to respond to threats and keep their assets secure. Industrial equipment can be protected with a physical security system that includes cameras, locks, and access cards.
Kaspersky Labs claims that 33% of cybersecurity incidents are directed at manufacturers. These threats are increasingly complex and widespread. These can include malware, ransomware, and phishing attacks. Protecting intellectual property, designs, products, and formulas is essential for manufacturers. It's important to devise a strategy that reduces the risk of cyberattacks.
Cybersecurity is vital for protecting confidential data and information such as customer orders and product specifications. Cybersecurity plans should include a plan for how to deal with a cyberattack, which can be as costly as $3 million to $6 million. Companies are more vulnerable to data breaches, theft, and disruption of production. Many manufacturers find it difficult to keep up with cyberattacks.
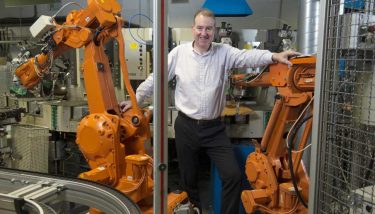
Protecting customer and employee information as well protecting the company's reputation is a key part of cybersecurity investment for manufacturers. You must conduct an audit of your system to determine vulnerabilities and your overall readiness to ensure your cybersecurity plan succeeds.
You can contact your local Manufacturing Executive Program Center (MEP) for advice and resources. You'll receive expert advice on how to make your business safer from cyberattacks.
In addition to conducting an audit of your systems, it's critical to set up a back-up plan. Regular testing of your system is essential to make sure it functions as intended. You can lower the chance of an attack by creating hard copies of key documents, and setting up a process to test the effectiveness of your system.
Many manufacturers haven't implemented cybersecurity measures, including data standards. A majority of OEMs are still using non-compliant processes, hardware, and software. However, increasing numbers of companies are investing digital technology. Data-related technologies, such as networked machines, sensors, and cloud computing, are transforming the industry. A cybersecurity strategy can protect your company from the risks posed by the Internet of Things and increased globalization of this industry.
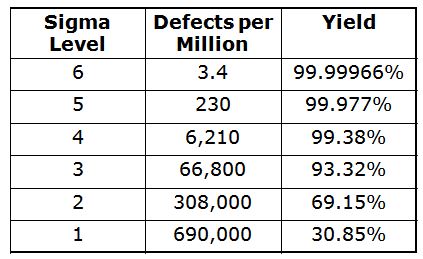
When developing a cybersecurity plan, it's important to understand the varying requirements for different manufacturing industries. For example, international manufacturers with long supply chain must follow standards based on their country, region, or partner. However, small and medium-sized businesses often have more stringent cybersecurity policies. Regardless of your size, you should invest in a comprehensive strategy to safeguard your business from cyberattacks.
Cybersecurity Framework for Manufacturers (NIST) provides a tool to help manufacturers defend their businesses against cyberattacks. This framework gives a blueprint for managing cybersecurity activities in many sectors, including industrial production.
FAQ
How can excess manufacturing production be reduced?
Improved inventory management is the key to reducing overproduction. This would reduce the amount of time spent on unnecessary activities such as purchasing, storing, and maintaining excess stock. By doing this, we could free up resources for other productive tasks.
One way to do this is to adopt a Kanban system. A Kanban board, a visual display to show the progress of work, is called a Kanban board. A Kanban system allows work items to move through several states before reaching their final destination. Each state represents a different priority level.
As an example, if work is progressing from one stage of the process to another, then the current task is complete and can be transferred to the next. It is possible to keep a task in the beginning stages until it gets to the end.
This allows work to move forward and ensures that no work is missed. Managers can monitor the work being done by Kanban boards to see what is happening at any given time. This allows them the ability to adjust their workflow using real-time data.
Lean manufacturing is another way to manage inventory levels. Lean manufacturing works to eliminate waste throughout every stage of the production chain. Anything that does not contribute to the product's value is considered waste. The following are examples of common waste types:
-
Overproduction
-
Inventory
-
Unnecessary packaging
-
Excess materials
Manufacturers can increase efficiency and decrease costs by implementing these ideas.
Do we need to know about Manufacturing Processes before learning about Logistics?
No. It doesn't matter if you don't know anything about manufacturing before you learn about logistics. But, being familiar with manufacturing processes will give you a better understanding about how logistics works.
What is the distinction between Production Planning or Scheduling?
Production Planning (PP), or production planning, is the process by which you determine what products are needed at any given time. This can be done by forecasting demand and identifying production capabilities.
Scheduling is the process that assigns dates to tasks so they can get completed within a given timeframe.
Can we automate some parts of manufacturing?
Yes! Automation has been around since ancient times. The Egyptians invent the wheel thousands of year ago. Nowadays, we use robots for assembly lines.
There are many applications for robotics in manufacturing today. These include:
-
Robots for assembly line
-
Robot welding
-
Robot painting
-
Robotics inspection
-
Robots that produce products
Manufacturing can also be automated in many other ways. 3D printing is a way to make custom products quickly and without waiting weeks or months for them to be manufactured.
How can manufacturing prevent production bottlenecks?
To avoid production bottlenecks, ensure that all processes run smoothly from the moment you receive your order to the time the product ships.
This includes both planning for capacity and quality control.
The best way to do this is to use continuous improvement techniques such as Six Sigma.
Six Sigma can be used to improve the quality and decrease waste in all areas of your company.
It is focused on creating consistency and eliminating variation in your work.
Statistics
- In 2021, an estimated 12.1 million Americans work in the manufacturing sector.6 (investopedia.com)
- It's estimated that 10.8% of the U.S. GDP in 2020 was contributed to manufacturing. (investopedia.com)
- According to a Statista study, U.S. businesses spent $1.63 trillion on logistics in 2019, moving goods from origin to end user through various supply chain network segments. (netsuite.com)
- You can multiply the result by 100 to get the total percent of monthly overhead. (investopedia.com)
- (2:04) MTO is a production technique wherein products are customized according to customer specifications, and production only starts after an order is received. (oracle.com)
External Links
How To
How to Use 5S to Increase Productivity in Manufacturing
5S stands for "Sort", "Set In Order", "Standardize", "Separate" and "Store". Toyota Motor Corporation invented the 5S strategy in 1954. It assists companies in improving their work environments and achieving higher efficiency.
This approach aims to standardize production procedures, making them predictable, repeatable, and easily measurable. It means tasks like cleaning, sorting or packing, labeling, and storing are done every day. These actions allow workers to perform their job more efficiently, knowing what to expect.
Implementing 5S involves five steps: Sort, Set in Order, Standardize Separate, Store, and Each step involves a different action which leads to increased efficiency. By sorting, for example, you make it easy to find the items later. When you set items in an order, you put items together. Once you have separated your inventory into groups and organized them, you will store these groups in easily accessible containers. Finally, when you label your containers, you ensure everything is labeled correctly.
Employees need to reflect on how they do their jobs. Employees must understand why they do certain tasks and decide if there's another way to accomplish them without relying on the old ways of doing things. To be successful in the 5S system, employees will need to acquire new skills and techniques.
The 5S Method not only improves efficiency, but it also helps employees to be more productive and happier. They are more motivated to achieve higher efficiency levels as they start to see improvement.