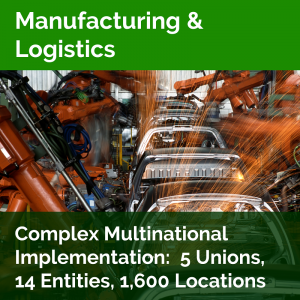
The creation of a "Smart Factory", however, is not just about installing new technology. It is about adapting to changing demands and changing the factory's mindset. The right technology will allow you to help customers and enable your business to succeed in a new manufacturing phase.
The first step is to decide what you want to achieve. A smart factory could be built to respond to extreme fluctuations in demand. Perhaps you are looking to build a smart facility that can support your global supply network partners. Or you may want to create a smart factory that responds to an industry that is heavily reliant on manual labor. The next step is to create an ecosystem that supports your goal, no matter what it may be.
A lack of internet connectivity is one major obstacle to creating a smart factory. This is especially true if your equipment and machinery are old. You might also have difficulty accessing the correct information regarding your systems and machines. According to the study, 33% of smart factory leaders believed that lack of IT infrastructure was a major obstacle to their ability build smart factories.
Technology is the next most important factor. There are many advanced manufacturing technologies that are currently available. These technologies can be used to improve your quality and productivity. These technologies can also be used to increase the value of your plant.
Another important aspect to think about is people. You need to make investments in the right skill sets at the right times. You must have the right people available, as well a sophisticated talent strategy. It is essential to establish a clear scope of work, and for everyone to agree on their priorities and timeframes. You must make sure the right people do the right things on the right project.
Process is the third most important aspect to be considered. You must ensure that your applications are able connect to a networking. This will make it possible to share information with other factories and systems. Lastly, you need to make sure that you have data and analytics in place. This will allow for data-driven decisions that can be used to your advantage and enable self-healing.
The fourth most important factor is people. Your executive team should be fully committed to the initiative. A convener is able to coordinate and align efforts among multiple vendors. This can help ensure that your executive team is aware of the scope of the project.
Security is the fifth most critical factor. There are many new technologies that can be used to decrease the likelihood of cyberattacks in manufacturing settings. It is important to have a cybersecurity strategy. A cybersecurity strategy must be maintained.
You should also consider how you will connect your equipment and machines. You can use your current solutions, but you might want to look into new ones. This will allow you to create new data sets to support your smart factories initiatives.
FAQ
What are the 7 R's of logistics?
The acronym 7Rs of Logistics refers to the seven core principles of logistics management. It was developed by the International Association of Business Logisticians (IABL) and published in 2004 as part of its "Seven Principles of Logistics Management" series.
The following letters form the acronym:
-
Responsible – ensure that all actions are legal and don't cause harm to anyone else.
-
Reliable - You can have confidence that you will fulfill your promises.
-
Reasonable - make sure you use your resources well and don't waste them.
-
Realistic – Consider all aspects, including cost-effectiveness as well as environmental impact.
-
Respectful – Treat others fairly and equitably.
-
Resourceful - look for opportunities to save money and increase productivity.
-
Recognizable - provide customers with value-added services.
Why is logistics important in manufacturing?
Logistics are essential to any business. They are essential to any business's success.
Logistics also play a major role in reducing costs and increasing efficiency.
What is production planning?
Production Planning is the creation of a plan to cover all aspects, such as scheduling, budgeting. Location, crew, equipment, props and other details. This document ensures that everything is prepared and available when you are ready for shooting. It should also provide information about how best to produce the best results while on set. This information includes locations, crew details and equipment requirements.
It is important to first outline the type of film you would like to make. You may already know where you want the film to be shot, or perhaps you have specific locations and sets you wish to use. Once you have identified your locations and scenes, you can start working out which elements you require for each scene. Perhaps you have decided that you need to buy a car but aren't sure which model. If this is the case, you might start searching online for car models and then narrow your options by selecting from different makes.
After you have selected the car you want, you can begin to think about additional features. Do you have people who need to be seated in the front seat? Maybe you need someone to move around in the back. Perhaps you would like to change the interior colour from black to white. These questions will help guide you in determining the ideal look and feel for your car. Also, think about what kind of shots you would like to capture. Are you going to be shooting close-ups? Or wide angles? Perhaps you want to show the engine or the steering wheel? All of these things will help you identify the exact style of car you want to film.
Once you have established all the details, you can create a schedule. You can use a schedule to determine when and where you need it to be shot. Each day will include the time when you need to arrive at the location, when you need to leave and when you need to return home. Everyone will know what they need and when. It is possible to make arrangements in advance for additional staff if you are looking to hire. You don't want to hire someone who won't show up because he didn't know.
It is important to calculate the amount of filming days when you are creating your schedule. Some projects may only take a couple of days, while others could last for weeks. While creating your schedule, it is important to remember whether you will require more than one shot per day. Multiple takes at the same place will result in higher costs and longer completion times. It is better to be cautious and take fewer shots than you risk losing money if you are not sure if multiple takes are necessary.
Budget setting is another important aspect in production planning. You will be able to manage your resources if you have a realistic budget. Keep in mind that you can always reduce your budget if you face unexpected difficulties. However, you shouldn't overestimate the amount of money you will spend. You will end up spending less money if you underestimate the cost of something.
Production planning is a detailed process. But, once you understand the workings of everything, it becomes easier for future projects to be planned.
What is the job of a manufacturer manager?
Manufacturing managers must ensure that manufacturing processes are efficient, effective, and cost-effective. They should be aware of any issues within the company and respond accordingly.
They must also be able to communicate with sales and marketing departments.
They should be up to date on the latest trends and be able apply this knowledge to increase productivity and efficiency.
What is the role of a production manager?
A production planner ensures all aspects of the project are delivered on time, within budget, and within scope. They also ensure the quality of the product and service meets the client's requirements.
What does manufacturing industry mean?
Manufacturing Industries is a group of businesses that produce goods for sale. These products are sold to consumers. This is accomplished by using a variety of processes, including production, distribution and retailing. They produce goods from raw materials by using machines and other machinery. This includes all types if manufactured goods.
Statistics
- In the United States, for example, manufacturing makes up 15% of the economic output. (twi-global.com)
- You can multiply the result by 100 to get the total percent of monthly overhead. (investopedia.com)
- [54][55] These are the top 50 countries by the total value of manufacturing output in US dollars for its noted year according to World Bank.[56] (en.wikipedia.org)
- It's estimated that 10.8% of the U.S. GDP in 2020 was contributed to manufacturing. (investopedia.com)
- (2:04) MTO is a production technique wherein products are customized according to customer specifications, and production only starts after an order is received. (oracle.com)
External Links
How To
Six Sigma and Manufacturing
Six Sigma is defined as "the application of statistical process control (SPC) techniques to achieve continuous improvement." Motorola's Quality Improvement Department in Tokyo, Japan developed Six Sigma in 1986. Six Sigma is a method to improve quality through standardization and elimination of defects. This method has been adopted by many companies in recent years as they believe there are no perfect products or services. Six Sigma aims to reduce variation in the production's mean value. This means that if you take a sample of your product, then measure its performance against the average, you can find out what percentage of the time the process deviates from the norm. If it is too large, it means that there are problems.
Understanding the dynamics of variability within your business is the first step in Six Sigma. Once you understand this, you can then identify the causes of variation. This will allow you to decide if these variations are random and systematic. Random variations occur when people do mistakes. Symmetrical variations are caused due to factors beyond the process. These are, for instance, random variations that occur when widgets are made and some fall off the production line. However, if you notice that every time you assemble a widget, it always falls apart at exactly the same place, then that would be a systematic problem.
After identifying the problem areas, you will need to devise solutions. That solution might involve changing the way you do things or redesigning the process altogether. After implementing the new changes, you should test them again to see if they worked. If they don’t work, you’ll need to go back and rework the plan.