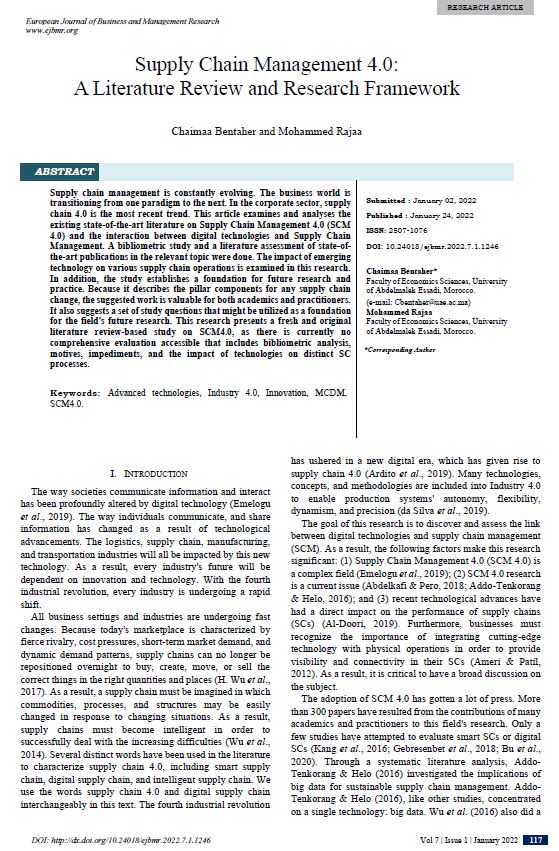
Biomedical engineering is a promising career that can improve the health of the people who choose it. These engineers are skilled in many fields including pharmaceutical manufacturing, laboratory science, and health care facilities. These engineers are able to develop new products and techniques that can help patients.
To become a biomedical engineering, you will need a bachelor's degree. Biomedical engineers need to have a strong foundation in science and math. In addition, they must possess excellent problem-solving skills and strong analytical abilities. Internships are another option. A master's degree may be required by some employers.
Due to the aging population, medical technology advances, and rising demand for biomedical engineering professionals, the demand for these engineers will increase over the next few decades. To develop and test new technologies, biomedical engineers collaborate with medical professionals. Biomedical engineers can also design, build, and repair medical devices. They can be employed by healthcare facilities, research centers, medical equipment sales companies and biomedical research firms.
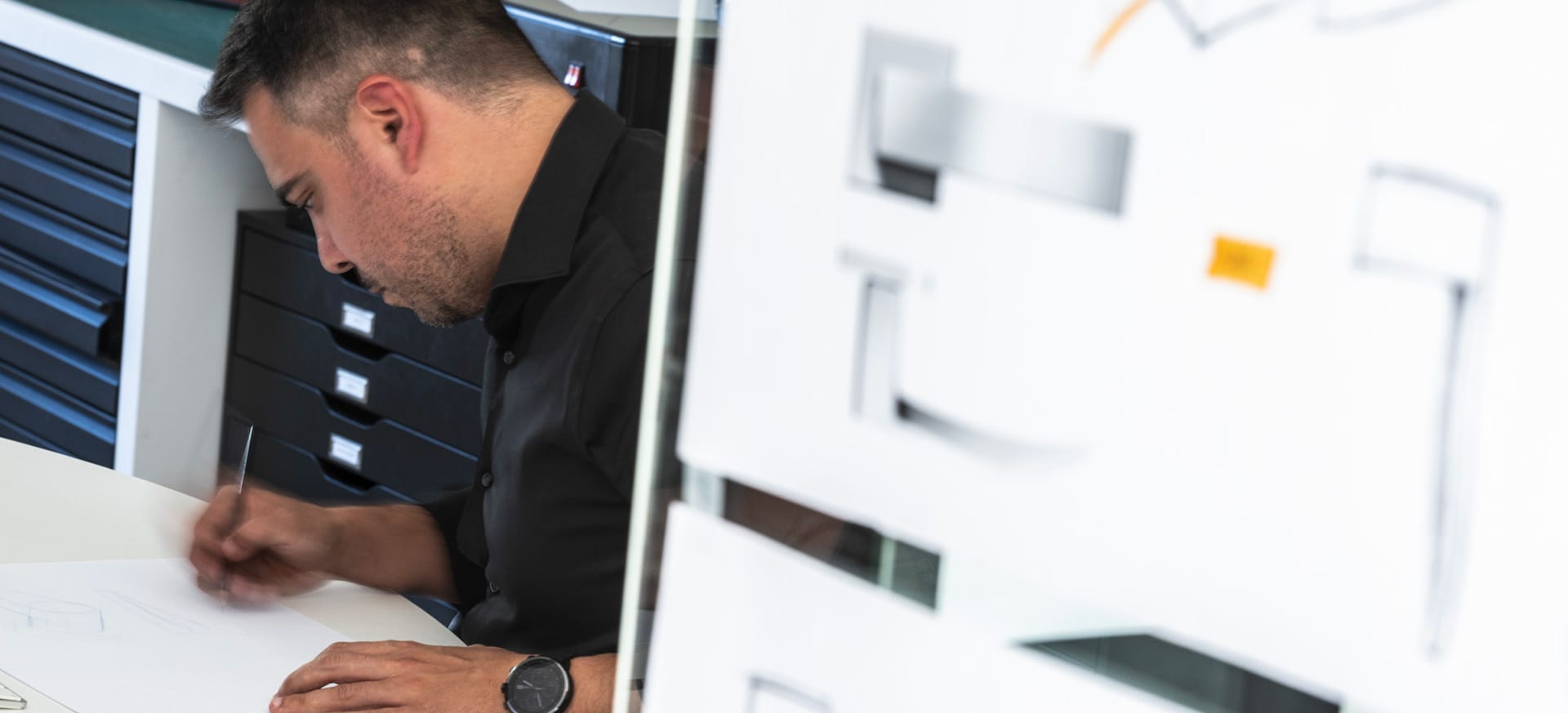
Biomedical engineers use advanced math and science to design equipment, computer software, and other solutions to biological science problems. They also use statistics and advanced math to create models and build complex medical devices. Biomedical engineers are also responsible, in addition to developing new devices and processes for patients, for testing and approving new medication and drug therapies. They are responsible for ensuring medical equipment performs at its peak performance.
There is a high demand in biomedical engineering, just like any other engineering field. The field is expected to grow at a faster rate than other engineering specialties. According to the Bureau of Labor Statistics (BLS), biomedical engineers' jobs will increase by six percent between 2020-2030. This rate is higher than the average for all occupations. The number of biomedical engineers employed in 2010 was approximately 15,700. The BLS predicts that there will be 1,400 openings each year through 2029. These openings are expected to be available in the following industries: healthcare services, medical equipment and supplies manufacturing, and research services.
Internships are a great way to get experience as a biomedical engineering professional. These internships are an opportunity to see how biomedical engineers work and to gain real-life experience. It is a smart idea to study computer programming, drafting and mechanical drawing as a student. People who are passionate about science may also be interested in studying physiology and human anatomy.
Those who are interested in becoming a biomedical engineer should start preparing for the career as early as high school. While a bachelor’s degree in biomedical engineer is essential, many employers prefer a Master’s degree. A master's degree is a great way to expand your opportunities and get you into supervisory positions in this field.
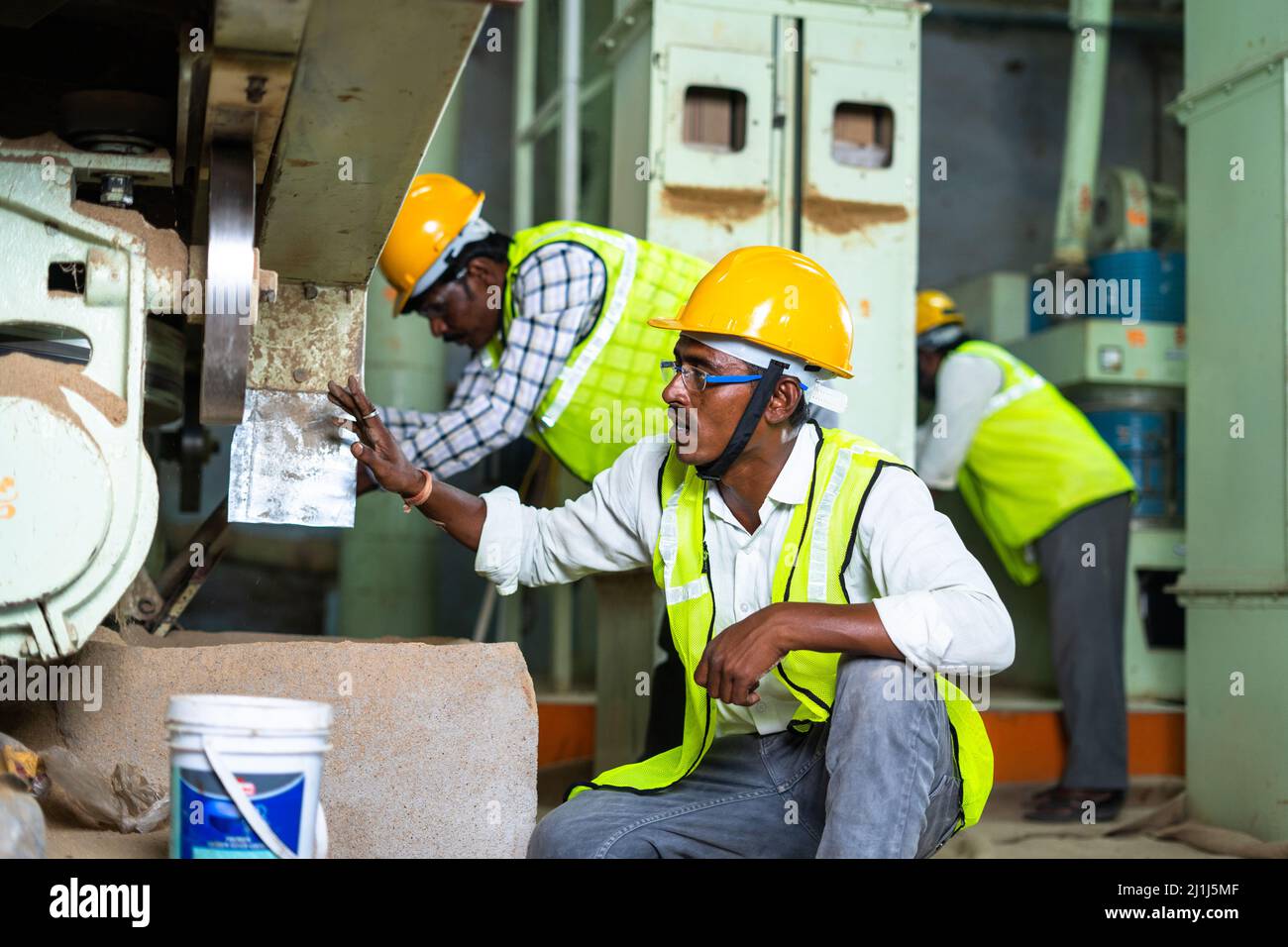
Biology, chemistry, mathematics, and physics are required for biomedical engineers. Students studying biomedical engineers study human anatomy, molecular biology, physiology and pharmacology during their undergraduate studies. They also work on capstone projects that integrate their engineering skills with problems of biological science.
FAQ
Why is logistics so important in manufacturing?
Logistics is an integral part of every business. They help you achieve great results by helping you manage all aspects of product flow, from raw materials to finished goods.
Logistics play an important role in reducing costs as well as increasing efficiency.
What skills is required for a production planner?
To become a successful production planner, you need to be organized, flexible, and able to multitask. It is also important to be able communicate with colleagues and clients.
How can manufacturing prevent production bottlenecks?
You can avoid bottlenecks in production by making sure that everything runs smoothly throughout the production cycle, from the moment you receive an order to the moment the product is shipped.
This includes both planning for capacity and quality control.
This can be done by using continuous improvement techniques, such as Six Sigma.
Six Sigma is a management system used to improve quality and reduce waste in every aspect of your organization.
It is focused on creating consistency and eliminating variation in your work.
How can I learn about manufacturing?
Hands-on experience is the best way to learn more about manufacturing. But if that is not possible you can always read books and watch educational videos.
What kind of jobs are there in logistics?
There are different kinds of jobs available in logistics. Here are some:
-
Warehouse workers – They load, unload and transport pallets and trucks.
-
Transportation drivers – They drive trucks or trailers to transport goods and perform pick-ups.
-
Freight handlers: They sort and package freight in warehouses.
-
Inventory managers – They manage the inventory in warehouses.
-
Sales representatives - They sell products to customers.
-
Logistics coordinators – They plan and coordinate logistics operations.
-
Purchasing agents – They buy goods or services necessary to run a company.
-
Customer service representatives - Answer calls and email from customers.
-
Shipping clerks – They process shipping orders, and issue bills.
-
Order fillers are people who fill orders based only on what was ordered.
-
Quality control inspectors: They inspect outgoing and incoming products for any defects.
-
Others – There are many other types available in logistics. They include transport supervisors, cargo specialists and others.
Are there any Manufacturing Processes that we should know before we can learn about Logistics?
No. It doesn't matter if you don't know anything about manufacturing before you learn about logistics. Understanding the manufacturing process will allow you to better understand logistics.
Statistics
- It's estimated that 10.8% of the U.S. GDP in 2020 was contributed to manufacturing. (investopedia.com)
- According to the United Nations Industrial Development Organization (UNIDO), China is the top manufacturer worldwide by 2019 output, producing 28.7% of the total global manufacturing output, followed by the United States, Japan, Germany, and India.[52][53] (en.wikipedia.org)
- (2:04) MTO is a production technique wherein products are customized according to customer specifications, and production only starts after an order is received. (oracle.com)
- In 2021, an estimated 12.1 million Americans work in the manufacturing sector.6 (investopedia.com)
- You can multiply the result by 100 to get the total percent of monthly overhead. (investopedia.com)
External Links
How To
How to use Lean Manufacturing in the production of goods
Lean manufacturing is an approach to management that aims for efficiency and waste reduction. It was developed in Japan between 1970 and 1980 by Taiichi Ohno. TPS founder Kanji Tyoda gave him the Toyota Production System, or TPS award. Michael L. Watkins published the first book on lean manufacturing in 1990.
Lean manufacturing is often defined as a set of principles used to improve the quality, speed, and cost of products and services. It emphasizes the elimination of defects and waste throughout the value stream. The five-steps of Lean Manufacturing are just-in time (JIT), zero defect and total productive maintenance (TPM), as well as 5S. Lean manufacturing is about eliminating activities that do not add value, such as inspection, rework, and waiting.
Lean manufacturing is a way for companies to achieve their goals faster, improve product quality, and lower costs. Lean manufacturing is a great way to manage the entire value chain including customers, suppliers, distributors and retailers as well as employees. Lean manufacturing is widely practiced in many industries around the world. Toyota's philosophy is a great example of this. It has helped to create success in automobiles as well electronics, appliances and healthcare.
Five principles are the basis of lean manufacturing:
-
Define Value: Identify the social value of your business and what sets you apart.
-
Reduce Waste - Eliminate any activity that doesn't add value along the supply chain.
-
Create Flow - Make sure work runs smoothly without interruptions.
-
Standardize & simplify - Make processes consistent and repeatable.
-
Build Relationships - Establish personal relationships with both internal and external stakeholders.
Lean manufacturing, although not new, has seen renewed interest in the economic sector since 2008. Many businesses have adopted lean production techniques to make them more competitive. Economists think that lean manufacturing is a crucial factor in economic recovery.
With many benefits, lean manufacturing is becoming more common in the automotive industry. These include higher customer satisfaction levels, reduced inventory levels as well as lower operating costs.
Any aspect of an enterprise can benefit from Lean manufacturing. Because it makes sure that all value chains are efficient and effectively managed, Lean Manufacturing is particularly helpful for organizations.
There are three main types:
-
Just-in Time Manufacturing (JIT), also known as "pull system": This form of lean manufacturing is often referred to simply as "pull". JIT is a method in which components are assembled right at the moment of use, rather than being manufactured ahead of time. This approach reduces lead time, increases availability and reduces inventory.
-
Zero Defects Manufacturing - ZDM: ZDM focuses its efforts on making sure that no defective units leave a manufacturing facility. If a part needs to be fixed during the assembly line, it should be repaired rather than scrapped. This applies to finished products, which may need minor repairs before they are shipped.
-
Continuous Improvement (CI),: Continuous improvement aims improve the efficiency and effectiveness of operations by continuously identifying issues and making changes to reduce waste. Continuous Improvement (CI) involves continuous improvement in processes, people, tools, and infrastructure.