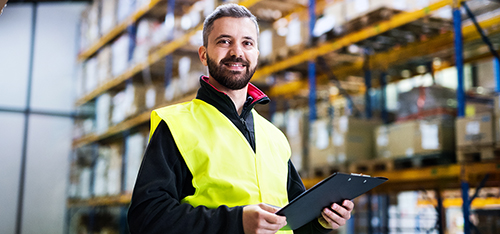
Supply chain disruptions can lead to economic and productivity losses across all industries. The disruptions have been caused by companies' failure to manage risk effectively.
In the face of growing internationalization, the defence industry has been affected by this trend. Many technologies, such as high-quality carbon fiber and advanced semiconductors may run out of supply. This can lead both to increased dependence and oligopolistic behavior. Additionally, dual products are more likely to be used. These products can pose safety and reliability concerns.
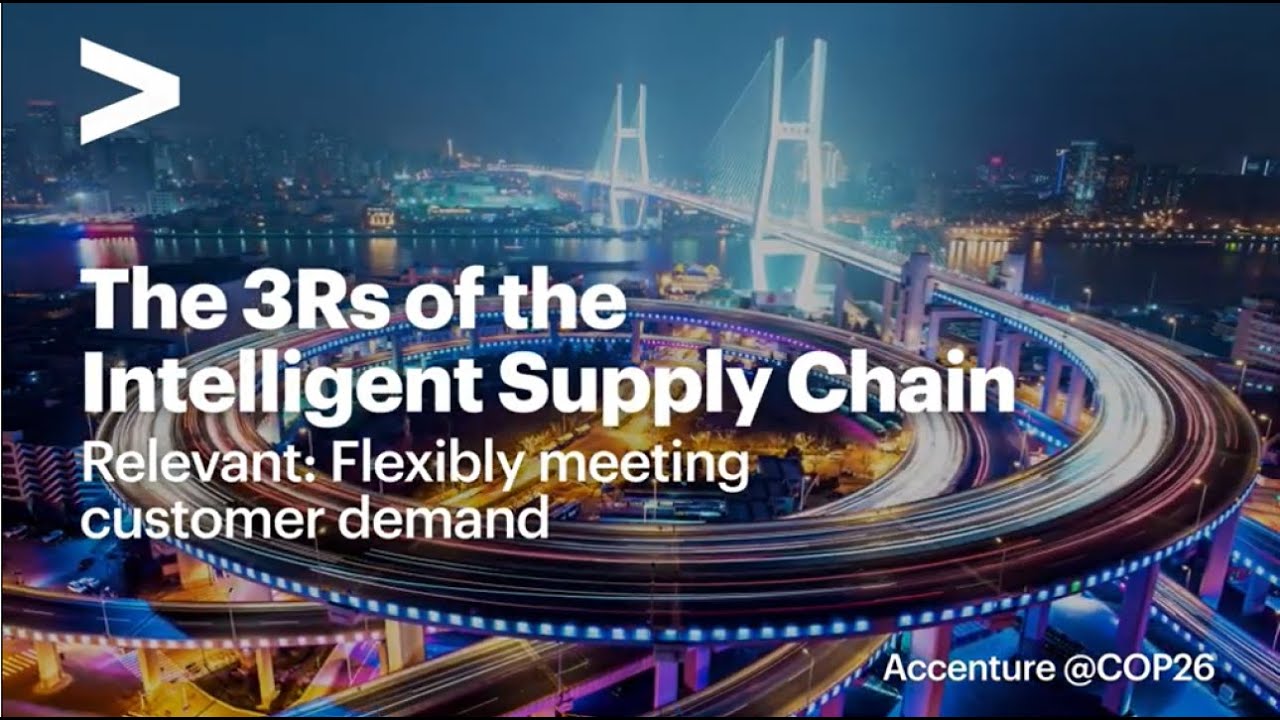
The security of vital minerals is crucial to modern industrial systems development in the age of globalization. Some minerals are distributed in economically underdeveloped countries and can be vulnerable to political instability. Under different circumstances, the global optimal allocation of critical mineral resources changes. China is a key node in the global critical mineral value chain. However, the industry is heavily dependent on other countries. It is crucial that governments create a global critical mineral allocation system that covers multiple countries rather than concentrating resources on a single country.
The European Union (EU) has been engaged in discussions about its defence technology and industrial base (DTIB). To help create a framework for a European defense industry, the European Commission launched the European Defence Agency (EDA). This new approach will see a number of improvements in the EU's military industry. For example, certain technologies can only be supplied by a limited number of non-EU companies. In the EU's defense sector, there will be both oligopoly as well as monopoly structures. In addition, it will become easier to buy certain raw materials from non-EU companies. This will enable the development of a new type of sourcing strategy, called bundled volumes.
A greater emphasis is being placed on developing a resilient and secure supply chain. There are many strategies to mitigate supply chain disruptions. One of these is the introduction of a formal risk management approach. A formal risk management approach is a way to allow the supply chain not only to survive but thrive. It should be inclusive of both internal and externe key stakeholders. This includes suppliers, investors, and governments. Management of the supply chain should be in line with global supply-chain dynamics.
Security of the 99m/99mtc supply network is another critical policy issue. The policy approach that was developed by the High-Level Group on Medical Radioisotopes, (HLG-MR), ensures long-term security in the supply of these radioisotopes. This included a review the global 99 M/99 M Tc supply chain, analysis of the economic effects of the supply, as well a policy approach.
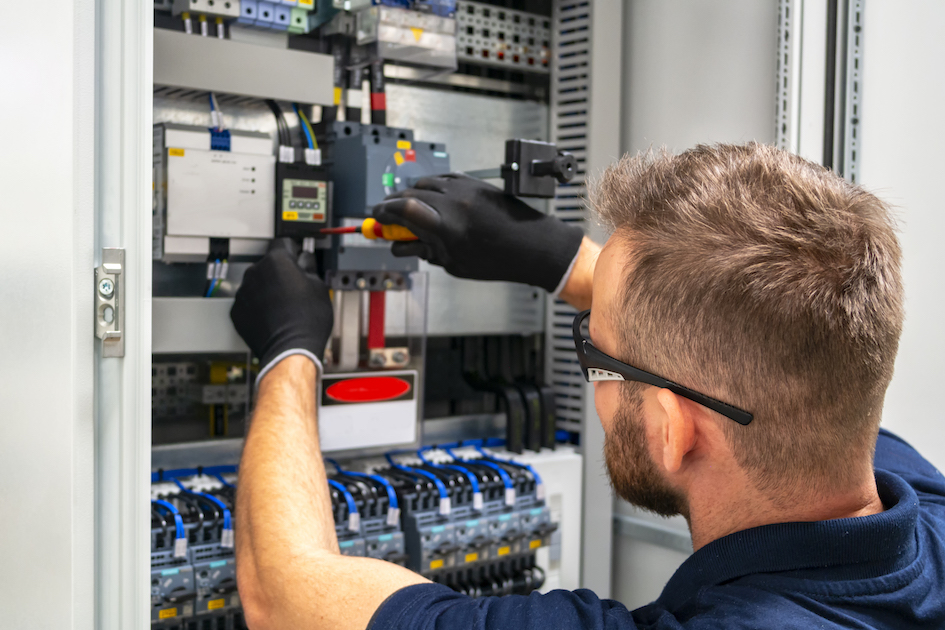
The HLG-MR identified two main areas of vulnerability that should be addressed in order to enhance the security of the 99 Mo/99m supply chain. These areas include monopolistic behavior as well as foreign capital. These factors can cause significant risks and price increases. The policy approach developed by HLG-MR also identified key steps that should be taken to address these vulnerabilities.
FAQ
How can excess manufacturing production be reduced?
In order to reduce excess production, you need to develop better inventory management methods. This would reduce the amount of time spent on unnecessary activities such as purchasing, storing, and maintaining excess stock. We could use these resources to do other productive tasks.
One way to do this is to adopt a Kanban system. A Kanban board, a visual display to show the progress of work, is called a Kanban board. A Kanban system allows work items to move through several states before reaching their final destination. Each state represents an individual priority level.
If work is moving from one stage to the other, then the current task can be completed and moved on to the next. If a task is still in its beginning stages, it will continue to be so until it reaches the end.
This allows you to keep work moving along while making sure that no work gets neglected. Managers can monitor the work being done by Kanban boards to see what is happening at any given time. This data allows them adjust their workflow based upon real-time data.
Another way to control inventory levels is to implement lean manufacturing. Lean manufacturing is about eliminating waste from all stages of the production process. Waste includes anything that does not add value to the product. Here are some examples of common types.
-
Overproduction
-
Inventory
-
Unnecessary packaging
-
Materials in excess
By implementing these ideas, manufacturers can improve efficiency and cut costs.
Is it necessary to be familiar with Manufacturing Processes before we learn about Logistics.
No. It doesn't matter if you don't know anything about manufacturing before you learn about logistics. It is important to know about the manufacturing processes in order to understand how logistics works.
What are the 7 Rs of logistics?
The acronym 7Rs of Logistics refers to the seven core principles of logistics management. It was developed by International Association of Business Logisticians (IABL), and published as part of their "Seven Principles of Logistics Management Series" in 2004.
The following letters make up the acronym:
-
Responsive - ensure all actions are legal and not harmful to others.
-
Reliable: Have faith in your ability or the ability to honor any promises made.
-
Reasonable - make sure you use your resources well and don't waste them.
-
Realistic - consider all aspects of operations, including cost-effectiveness and environmental impact.
-
Respectful - show respect and treat others fairly and fairly
-
You are resourceful and look for ways to save money while increasing productivity.
-
Recognizable is a company that provides customers with value-added solutions.
What are the four types in manufacturing?
Manufacturing is the process that transforms raw materials into useful products. It includes many different activities like designing, building and testing, packaging, shipping and selling, as well as servicing.
How can manufacturing avoid production bottlenecks
The key to avoiding bottlenecks in production is to keep all processes running smoothly throughout the entire production cycle, from the time you receive an order until the time when the product ships.
This includes planning for both capacity requirements and quality control measures.
Continuous improvement techniques such Six Sigma can help you achieve this.
Six Sigma can be used to improve the quality and decrease waste in all areas of your company.
It is focused on creating consistency and eliminating variation in your work.
What does warehouse refer to?
A warehouse or storage facility is where goods are stored before they are sold. You can have it indoors or outdoors. Sometimes, it can be both an indoor and outdoor space.
Why is logistics important in manufacturing
Logistics are an essential component of any business. They are essential to any business's success.
Logistics plays a significant role in reducing cost and increasing efficiency.
Statistics
- (2:04) MTO is a production technique wherein products are customized according to customer specifications, and production only starts after an order is received. (oracle.com)
- According to the United Nations Industrial Development Organization (UNIDO), China is the top manufacturer worldwide by 2019 output, producing 28.7% of the total global manufacturing output, followed by the United States, Japan, Germany, and India.[52][53] (en.wikipedia.org)
- Job #1 is delivering the ordered product according to specifications: color, size, brand, and quantity. (netsuite.com)
- It's estimated that 10.8% of the U.S. GDP in 2020 was contributed to manufacturing. (investopedia.com)
- According to a Statista study, U.S. businesses spent $1.63 trillion on logistics in 2019, moving goods from origin to end user through various supply chain network segments. (netsuite.com)
External Links
How To
How to use the Just In-Time Production Method
Just-in-time is a way to cut costs and increase efficiency in business processes. It's the process of obtaining the right amount and timing of resources when you need them. This means that you only pay the amount you actually use. The term was first coined by Frederick Taylor, who developed his theory while working as a foreman in the early 1900s. He observed how workers were paid overtime if there were delays in their work. He decided that workers would be more productive if they had enough time to complete their work before they started to work.
JIT is an acronym that means you need to plan ahead so you don’t waste your money. It is important to look at your entire project from beginning to end and ensure that you have enough resources to handle any issues that may arise. If you expect problems to arise, you will be able to provide the necessary equipment and personnel to address them. This will ensure that you don't spend more money on things that aren't necessary.
There are different types of JIT methods:
-
Demand-driven: This is a type of JIT where you order the parts/materials needed for your project regularly. This will let you track the amount of material left over after you've used it. You'll also be able to estimate how long it will take to produce more.
-
Inventory-based: You stock materials in advance to make your projects easier. This allows you to predict how much you can expect to sell.
-
Project-driven : This is a method where you make sure that enough money is set aside to pay the project's cost. When you know how much you need, you'll purchase the appropriate amount of materials.
-
Resource-based: This is the most common form of JIT. Here, you allocate certain resources based on demand. For instance, if you have a lot of orders coming in, you'll assign more people to handle them. If you don't have many orders, you'll assign fewer people to handle the workload.
-
Cost-based: This is a similar approach to resource-based but you are not only concerned with how many people you have, but also how much each one costs.
-
Price-based: This is very similar to cost-based, except that instead of looking at how much each individual worker costs, you look at the overall price of the company.
-
Material-based is an alternative to cost-based. Instead of looking at the total cost in the company, this method focuses on the average amount of raw materials that you consume.
-
Time-based JIT: This is another variant of resource-based JIT. Instead of focusing only on how much each employee is costing, you should focus on how long it takes to complete your project.
-
Quality-based: This is yet another variation of resource-based JIT. Instead of focusing on the cost of each worker or how long it takes, think about how high quality your product is.
-
Value-based JIT: This is the latest form of JIT. In this case, you're not concerned with how well the products perform or whether they meet customer expectations. Instead, your goal is to add value to the market.
-
Stock-based: This inventory-based approach focuses on how many items are being produced at any one time. This is used to increase production and minimize inventory.
-
Just-intime (JIT), planning is a combination JIT management and supply chain management. It is the process of scheduling components' delivery as soon as they have been ordered. It's important because it reduces lead times and increases throughput.