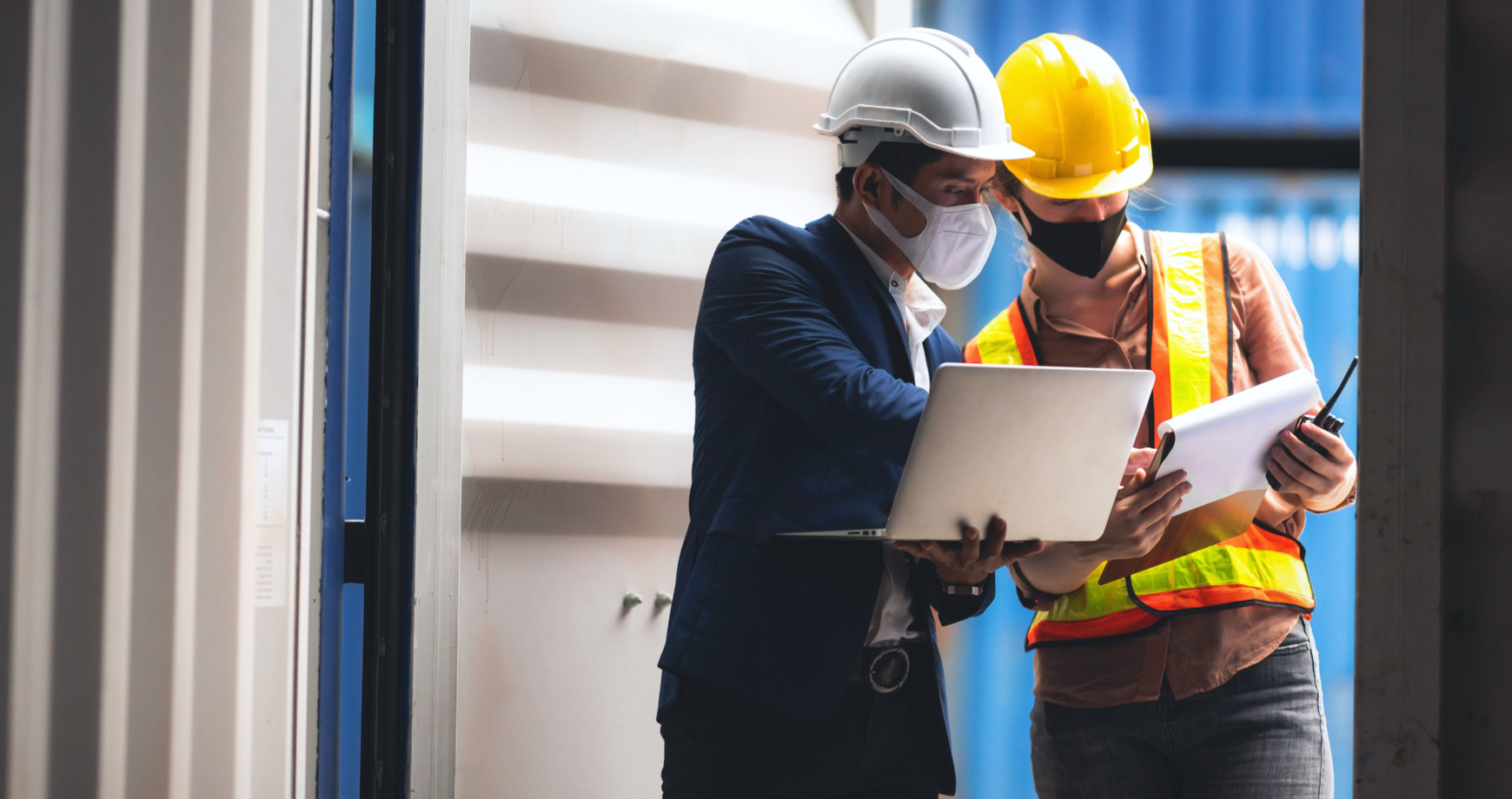
Whether you are running a small business or the enterprise arm of a major corporation, supply chain risk management is a necessary component to maintaining a robust operation. There are many risks that can occur, from the seemingly mundane to the potentially disastrous. An organization's protection against losses can be achieved by having a well-planned strategy and a solid implementation plan.
Data sharing is an essential part of a supply chain continuity program. You are more likely to have supplier disputes or vendor failures if your company relies solely on one supplier. Your company can avoid supply disruptions by being part of a multi-supplier network. You may also have the ability to negotiate with another supplier.
Similarly, if your company has a complex network of contractors, you are at greater risk of vendor fraud, duplicate billing, and improper related-party billing. You can create a risk assessment method to help reduce these risks. This can include a thorough assessment of your partners, suppliers, and other tier-one components.
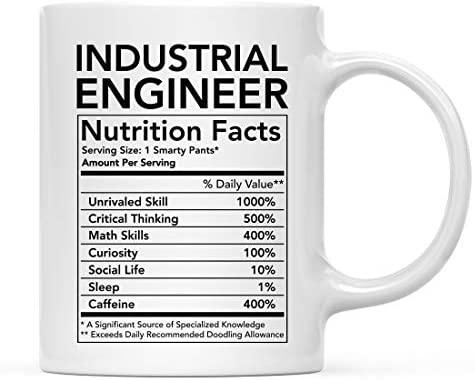
When developing a good supply chain risk management program, you should first identify the important elements of a good supply chain, then quantify and measure them, and then devise an action plan. The plan should include all the items mentioned above, as well some additional. A proactive monitoring program is essential. A proactive monitoring system is one that gives executives accurate, real-time information about supply chain risks. By tracking supply risks in real time, you are better equipped to make informed decisions and to react in a timely manner.
While you are assessing your risks and quantifying them, it is crucial to keep in view that your supply chain's ability to withstand disruption is a function if governance. It is important to take into account the role of stakeholders. For example, the supplier bankruptcy that led to a supply-chain disruption in the pharmaceutical industry could have been avoided if the company had properly scorecarded its suppliers.
A well-planned plan is essential for minimizing supply chain crises. But it can be difficult to put together the right contingency plans. Many businesses don't take the time and effort to create enough contingency plans to cover every risk they manage. The most important potential consequences should be considered when developing these plans.
The PPPR, or preventive preparedness, readiness, response and recovery, is a global standard for supply-chain risk management. It is a solid approach that will improve your ability to react to supply-chain disruptions and can be used with other strategies to protect you organization from them. Using a PPPR to guide your organization can be the difference between surviving and thriving in today's market.
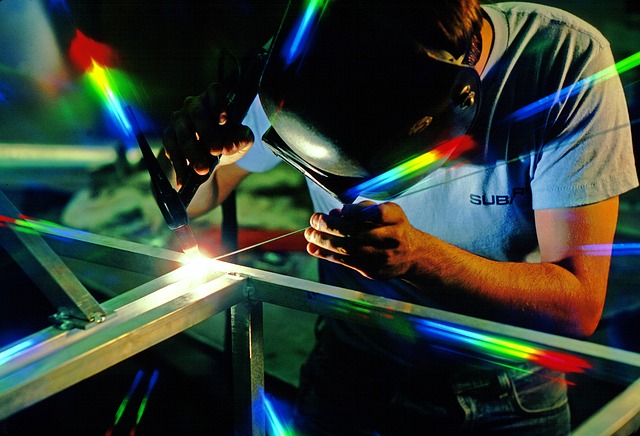
Getting the right data from your suppliers can help you to understand their history and what they have to offer. This can inform your decision-making, whether you are looking to expand your sourcing efforts or you are just fine-tuning your current processes. You can provide the right risk premiums to your insurers by having reliable data.
FAQ
What are the requirements to start a logistics business?
It takes a lot of skills and knowledge to run a successful logistics business. Good communication skills are essential to effectively communicate with your suppliers and clients. You must be able analyze data and draw out conclusions. You must be able and able to handle stress situations and work under pressure. To improve efficiency, you must be innovative and creative. Strong leadership qualities are essential to motivate your team and help them achieve their organizational goals.
To meet tight deadlines, you must also be efficient and organized.
Is automation important in manufacturing?
Automation is essential for both manufacturers and service providers. It allows them provide faster and more efficient services. It reduces human errors and improves productivity, which in turn helps them lower their costs.
What can I do to learn more about manufacturing?
Experience is the best way for you to learn about manufacturing. But if that is not possible you can always read books and watch educational videos.
What is manufacturing and logistics?
Manufacturing refers the process of producing goods from raw materials through machines and processes. Logistics includes all aspects related to supply chain management, such as procurement, distribution planning, inventory control and transportation. As a broad term, manufacturing and logistics often refer to both the creation and delivery of products.
What is the role of a logistics manager
A logistics manager ensures that all goods are delivered on time and without damage. This is done through his/her expertise and knowledge about the company's product range. He/she should also ensure enough stock is available to meet demand.
Statistics
- Many factories witnessed a 30% increase in output due to the shift to electric motors. (en.wikipedia.org)
- According to a Statista study, U.S. businesses spent $1.63 trillion on logistics in 2019, moving goods from origin to end user through various supply chain network segments. (netsuite.com)
- It's estimated that 10.8% of the U.S. GDP in 2020 was contributed to manufacturing. (investopedia.com)
- [54][55] These are the top 50 countries by the total value of manufacturing output in US dollars for its noted year according to World Bank.[56] (en.wikipedia.org)
- (2:04) MTO is a production technique wherein products are customized according to customer specifications, and production only starts after an order is received. (oracle.com)
External Links
How To
How to use 5S to increase Productivity in Manufacturing
5S stands as "Sort", Set In Order", Standardize", Separate" and "Store". Toyota Motor Corporation invented the 5S strategy in 1954. This methodology helps companies improve their work environment to increase efficiency.
The basic idea behind this method is to standardize production processes, so they become repeatable, measurable, and predictable. This means that tasks such as cleaning, sorting, storing, packing, and labeling are performed daily. Because workers know what they can expect, this helps them perform their jobs more efficiently.
There are five steps to implementing 5S, including Sort, Set In Order, Standardize, Separate and Store. Each step requires a different action, which increases efficiency. You can make it easy for people to find things later by sorting them. You arrange items by placing them in an order. Then, after you separate your inventory into groups, you store those groups in containers that are easy to access. Make sure everything is correctly labeled when you label your containers.
This requires employees to critically evaluate how they work. Employees must be able to see why they do what they do and find a way to achieve them without having to rely on their old methods. They must learn new skills and techniques in order to implement the 5S system.
In addition to improving efficiency, the 5S system also increases morale and teamwork among employees. Once they start to notice improvements, they are motivated to keep working towards their goal of increasing efficiency.