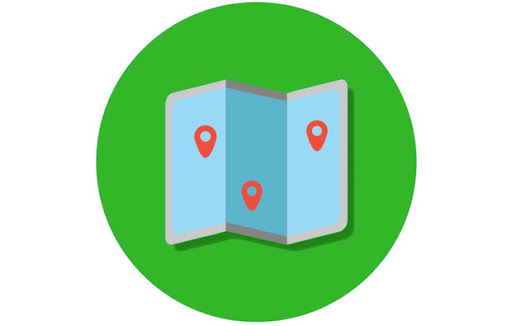
SIPOC is a visual tool to help define inputs and outcomes of a business. The SIPOC diagram allows team members identify any gaps or improvements to business operations.
The sipoc diagram is often a part of the DMAIC process improvement cycle, which is a framework used for creating a business process that can be improved through analysis and continuous improvement. It helps teams and sponsor agree on project boundaries and the scope of a project, along with Key Process Input Variables and Key Process Output Variables.
What Is SIPOC?
SIPOC is a visually simple representation of the inputs to a process. The primary purpose of this diagram is to assist the team in understanding and analyzing the business processes at a higher level. This includes providing a picture that clearly shows the steps required to transform inputs to desired outputs.
What is the background of the sipoc diagrams?
The sipoc was first used in the late 1980s to improve business processes using the Six Sigma and total quality model. Since then, its use in lean manufacturing programs and business process improvements has expanded. It is a valuable tool for streamlining and identifying processes and potential improvements.
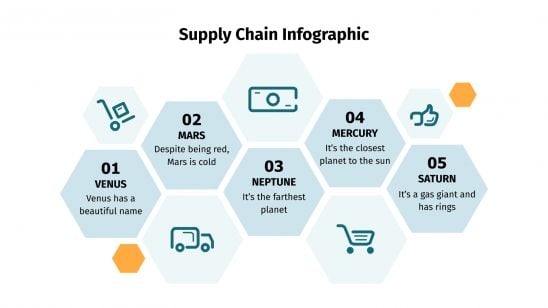
How to Make SIPOCs?
In order to construct a SIPOC chart, the first thing you need to do is choose which business process you would like to analyze. This will allow you and your team members to focus on important areas, and make sure that important details are not overlooked.
The next step is to determine what inputs are required for the process to work, and who provides them. You should list each supplier and their contact information, along with the raw materials that they provide to the process.
Including internal and external customers, you can list all the recipients of the process outputs. This can help ensure that the company delivers high-quality products.
Inputs This is the very first section on a SIPOC and it contains all the requirements for material or information. Materials can be tangible goods like products, or they can be informational, such a report.
Outputs: This is the second section of a SIPOC diagram and is typically a list of products, services, or completed actions that are produced as a result of the process. The outputs should reflect the value that customers expect from the process, and they should respond to customer needs.
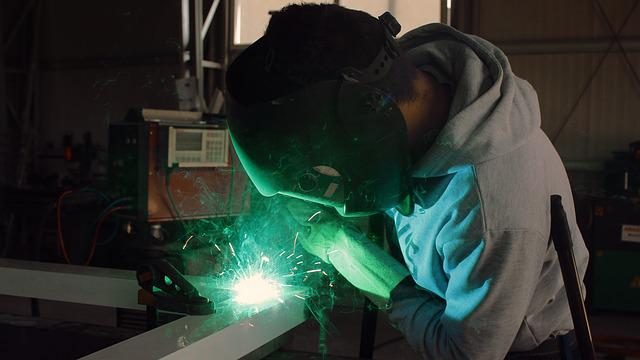
Customers: The final section in a SIPOC chart identifies both the internal and external customers who receive the outputs of the process. This could include the maintenance staff, line operators, or other internal and/or external clients.
SIPOCs are powerful visual tools that can be used for improving business processes and communication among all stakeholders. It's easy to create and is a great way to get team members to understand the business processes that are being examined. It's recommended to use a template that includes all the key components of the diagram, such as inputs and outputs. Using a template can save time and effort, as you can quickly draw the diagram with ease.
FAQ
What is the difference between Production Planning and Scheduling?
Production Planning (PP), is the process of deciding what production needs to take place at any given time. Forecasting and identifying production capacity are two key elements to this process.
Scheduling refers to the process of allocating specific dates to tasks in order that they can be completed within a specified timeframe.
What are manufacturing and logistic?
Manufacturing is the production of goods using raw materials. Logistics manages all aspects of the supply chain, including procurement, production planning and distribution, inventory control, transportation, customer service, and transport. Manufacturing and logistics are often considered together as a broader term that encompasses both the process of creating products and delivering them to customers.
How can manufacturing reduce production bottlenecks?
Production bottlenecks can be avoided by ensuring that processes are running smoothly during the entire production process, starting with the receipt of an order and ending when the product ships.
This includes both quality control and capacity planning.
Continuous improvement techniques such Six Sigma can help you achieve this.
Six Sigma is a management method that helps to improve quality and reduce waste.
It is focused on creating consistency and eliminating variation in your work.
What do you mean by warehouse?
A warehouse or storage facility is where goods are stored before they are sold. It can be an indoor space or an outdoor area. In some cases, it may be a combination of both.
Is automation important in manufacturing?
Automation is important not only for manufacturers but also for service providers. It enables them to provide services faster and more efficiently. They can also reduce their costs by reducing human error and improving productivity.
What is the responsibility for a logistics manager
Logistics managers are responsible for ensuring that all goods arrive in perfect condition and on time. This is accomplished by using the experience and knowledge gained from working with company products. He/she also needs to ensure adequate stock to meet demand.
Statistics
- Job #1 is delivering the ordered product according to specifications: color, size, brand, and quantity. (netsuite.com)
- (2:04) MTO is a production technique wherein products are customized according to customer specifications, and production only starts after an order is received. (oracle.com)
- In the United States, for example, manufacturing makes up 15% of the economic output. (twi-global.com)
- [54][55] These are the top 50 countries by the total value of manufacturing output in US dollars for its noted year according to World Bank.[56] (en.wikipedia.org)
- In 2021, an estimated 12.1 million Americans work in the manufacturing sector.6 (investopedia.com)
External Links
How To
How to Use Lean Manufacturing for the Production of Goods
Lean manufacturing (or lean manufacturing) is a style of management that aims to increase efficiency, reduce waste and improve performance through continuous improvement. It was developed in Japan between 1970 and 1980 by Taiichi Ohno. TPS founder Kanji Tyoda gave him the Toyota Production System, or TPS award. Michael L. Watkins published the original book on lean manufacturing, "The Machine That Changed the World," in 1990.
Lean manufacturing is often described as a set if principles that help improve the quality and speed of products and services. It emphasizes the elimination and minimization of waste in the value stream. Lean manufacturing is also known as just in time (JIT), zero defect total productive maintenance(TPM), and five-star (S). Lean manufacturing seeks to eliminate non-value added activities, such as inspection, work, waiting, and rework.
Lean manufacturing can help companies improve their product quality and reduce costs. Additionally, it helps them achieve their goals more quickly and reduces employee turnover. Lean manufacturing is considered one of the most effective ways to manage the entire value chain, including suppliers, customers, distributors, retailers, and employees. Lean manufacturing is widely practiced in many industries around the world. For example, Toyota's philosophy underpins its success in automobiles, electronics, appliances, healthcare, chemical engineering, aerospace, paper, food, etc.
Five basic principles of Lean Manufacturing are included in lean manufacturing
-
Define Value - Identify the value your business adds to society and what makes you different from competitors.
-
Reduce waste - Stop any activity that isn't adding value to the supply chains.
-
Create Flow - Make sure work runs smoothly without interruptions.
-
Standardize & simplify - Make processes consistent and repeatable.
-
Build Relationships- Develop personal relationships with both internal as well as external stakeholders.
Although lean manufacturing isn't a new concept in business, it has gained popularity due to renewed interest in the economy after the 2008 global financial crisis. Many businesses have adopted lean manufacturing techniques to help them become more competitive. Some economists even believe that lean manufacturing can be a key factor in economic recovery.
With many benefits, lean manufacturing is becoming more common in the automotive industry. These include better customer satisfaction and lower inventory levels. They also result in lower operating costs.
Lean manufacturing can be applied to almost every aspect of an organization. Lean manufacturing is most useful in the production sector of an organisation because it ensures that each step in the value-chain is efficient and productive.
There are three types principally of lean manufacturing:
-
Just-in Time Manufacturing (JIT), also known as "pull system": This form of lean manufacturing is often referred to simply as "pull". JIT means that components are assembled at the time of use and not manufactured in advance. This strategy aims to decrease lead times, increase availability of parts and reduce inventory.
-
Zero Defects Manufacturing: ZDM ensures that no defective units leave the manufacturing plant. It is better to repair a part than have it removed from the production line if it needs to be fixed. This applies to finished goods that may require minor repairs before shipment.
-
Continuous Improvement (CI),: Continuous improvement aims improve the efficiency and effectiveness of operations by continuously identifying issues and making changes to reduce waste. Continuous improvement involves continuous improvement of processes and people as well as tools.