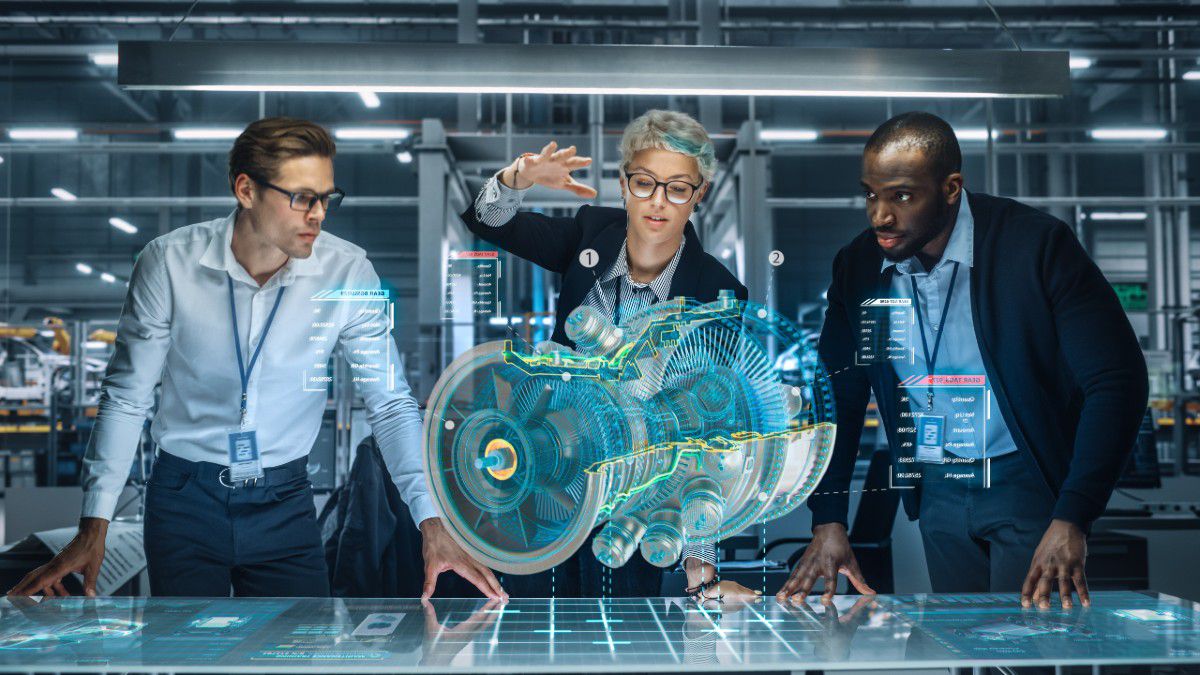
Advanced manufacturing is the application of new technology to improve products and processes. The technology used to achieve this can be classified as "advanced," "innovative," or "cutting edge." This is because advanced manufacturing has become more common in the manufacturing industry. Below are examples of advanced production. Listed below are some of the most common technologies used in advanced manufacturing.
Continuous manufacturing
Continuous manufacturing is first mentioned in the 1700s as a method of making pig iron in blast ovens. The concept has since spread across various industries, including the automotive, food, oil and refining, chemicals, and pulp and paper industries. Continuous manufacturing has captured the attention of CMOs from top pharma and other big players in the biopharmaceutical market.
Recent commentary by the FDA and its partner organizations discussed the benefits that continuous manufacturing can bring to the production of therapeutic protein. This legislation would create national centres to promote the field and assist companies in creating standards. The industry's goal is to improve the process for creating and using medical devices. It would encourage companies to use continuous production to improve and develop products. It is important to make sure that continuous manufacturing is safe.
Automated processes
The benefits of automating processes in advanced manufacturing cannot be overstated. Automation is often the best way to maximize floor space and increase production efficiency. Utilizing automation technologies and data collection, manufacturers can lower costs and increase productivity through better equipment use. Automation of the process industry can also help save time and money. The initial investment is not cheap, but it will ultimately increase the bottom line for a manufacturing company.
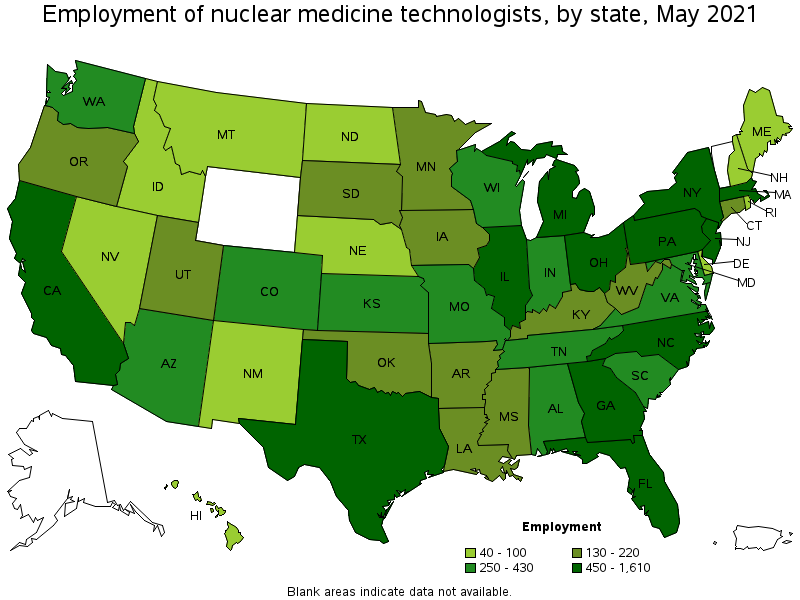
Companies combine automated processes with advanced manufacturing techniques today. Audi is one example. They use automated welding and bonding processes to reduce their production time while also saving energy and weight. Advanced manufacturing techniques, such as regenerative braking for conveyor systems are used. 3D printing represents the greatest advancement in manufacturing. It has been around for a while, but it is only now that it is mainstream. What is it that makes 3D printing so appealing?
Internet of Things (IoT)
The IIoT revolution has transformed manufacturing with the help of sensors that monitor machines and their operations. These sensors gather data from many parts of manufacturing and feed this data to a central center station. This data is then processed and analyzed, which can be used to improve processes and eliminate waste. Advanced manufacturers use IIoT to monitor production processes and optimize their output. The IIoT can be described as the industrial equivalent of key fobs.
To deploy IIoT effectively and efficiently, you need a roadmap and the development capabilities to create use cases. The following roadmap is provided by an automaker. It shows three phases of deployment.
Cost-effectiveness
Costs of advanced manufacturing may not be directly comparable to traditional production systems. Instead, traditional cost-benefit analyses are not enough to determine economic benefits. A holistic model that incorporates both benefits and costs can be used to identify new advantages and speed decision-making. Munker and Schroer present a cost-benefit analysis that addresses the most important issues related to AMS implementation.
Advances in information technology are rapidly changing the face of manufacturing and their costs. As production systems become more networked and smart, they are also becoming more efficient. Cost pressures are increasing the focus on productivity and the ability of companies to respond to customers' needs. The adoption of modern manufacturing technologies will accelerate the development of new technologies and increase their cost-effectiveness. The industry will continue to digitize, which will lead to an increase in the adoption rate of such technologies.
Human error reduction
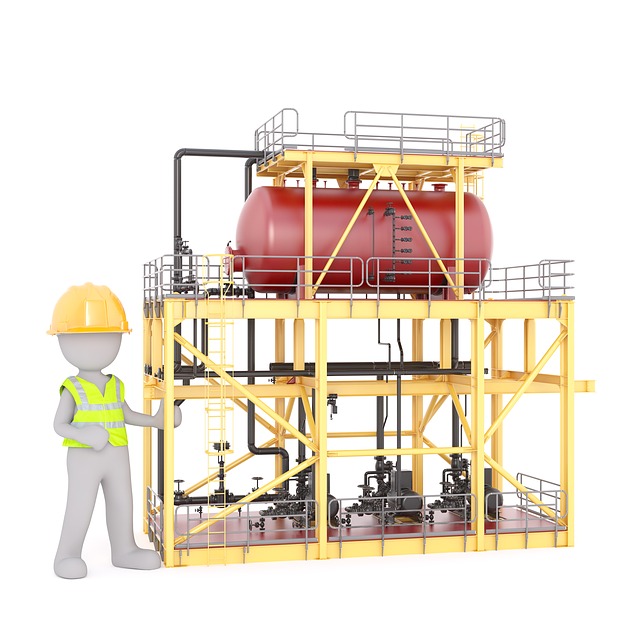
Although humans can make mistakes, the manufacturing process used to create a product is designed to minimize them. Employees can make mistakes if they don't follow instructions or fail to understand the written process. Pharmaceutical laboratories, for example, have to follow very specific procedures when they are making drugs. Some employees believe they are familiar with a process and know how to use the correct ingredients. They then proceed to make the compound without consulting the written instructions.
A way to reduce human errors is to communicate effectively between junior and senior employees. Employers who are treated harshly will make mistakes. Therefore, managers should avoid punishing employees who ask questions. Employees should feel at ease asking questions. If they don't feel comfortable asking questions they won't be inclined to take corrective action. Maintain a healthy dialog between junior and senior employees and resolve communication problems in a professional and courteous manner.
FAQ
What do you mean by warehouse?
A warehouse is a place where goods are stored until they are sold. It can be indoors or out. It may also be an indoor space or an outdoor area.
Why is logistics important in manufacturing
Logistics is an integral part of every business. They can help you achieve great success by helping you manage product flow from raw material to finished goods.
Logistics also play a major role in reducing costs and increasing efficiency.
What is the difference between manufacturing and logistics
Manufacturing is the act of producing goods from raw materials using machines and processes. Logistics encompasses the management of all aspects associated with supply chain activities such as procurement, production planning, distribution and inventory control. It also includes customer service. Sometimes manufacturing and logistics are combined to refer to a wider term that includes both the process of creating products as well as their delivery to customers.
What is the job of a manufacturer manager?
A manufacturing manager must ensure that all manufacturing processes are efficient and effective. They should be alert for any potential problems in the company and react accordingly.
They should also be able and comfortable communicating with other departments like sales and marketing.
They should also be aware of the latest trends in their industry and be able to use this information to help improve productivity and efficiency.
How can I find out more about manufacturing?
The best way to learn about manufacturing is through hands-on experience. If that is not possible, you could always read books or view educational videos.
What does the term manufacturing industries mean?
Manufacturing Industries are companies that manufacture products. Consumers are people who purchase these goods. To accomplish this goal, these companies employ a range of processes including distribution, sales, management, and production. These companies produce goods using raw materials and other equipment. This covers all types of manufactured goods including clothing, food, building supplies and furniture, as well as electronics, tools, machinery, vehicles and pharmaceuticals.
Is automation important for manufacturing?
Automating is not just important for manufacturers, but also for service providers. Automation allows them to deliver services quicker and more efficiently. They can also reduce their costs by reducing human error and improving productivity.
Statistics
- According to a Statista study, U.S. businesses spent $1.63 trillion on logistics in 2019, moving goods from origin to end user through various supply chain network segments. (netsuite.com)
- Job #1 is delivering the ordered product according to specifications: color, size, brand, and quantity. (netsuite.com)
- According to the United Nations Industrial Development Organization (UNIDO), China is the top manufacturer worldwide by 2019 output, producing 28.7% of the total global manufacturing output, followed by the United States, Japan, Germany, and India.[52][53] (en.wikipedia.org)
- In 2021, an estimated 12.1 million Americans work in the manufacturing sector.6 (investopedia.com)
- It's estimated that 10.8% of the U.S. GDP in 2020 was contributed to manufacturing. (investopedia.com)
External Links
How To
How to use lean manufacturing in the production of goods
Lean manufacturing is an approach to management that aims for efficiency and waste reduction. It was developed by Taiichi Okono in Japan, during the 1970s & 1980s. TPS founder Kanji Takoda awarded him the Toyota Production System Award (TPS). Michael L. Watkins published the original book on lean manufacturing, "The Machine That Changed the World," in 1990.
Lean manufacturing is often described as a set if principles that help improve the quality and speed of products and services. It emphasizes the elimination of defects and waste throughout the value stream. Lean manufacturing is also known as just in time (JIT), zero defect total productive maintenance(TPM), and five-star (S). Lean manufacturing seeks to eliminate non-value added activities, such as inspection, work, waiting, and rework.
Lean manufacturing not only improves product quality but also reduces costs. Companies can also achieve their goals faster by reducing employee turnover. Lean manufacturing can be used to manage all aspects of the value chain. Customers, suppliers, distributors, retailers and employees are all included. Lean manufacturing practices are widespread in many industries. For example, Toyota's philosophy underpins its success in automobiles, electronics, appliances, healthcare, chemical engineering, aerospace, paper, food, etc.
Lean manufacturing is based on five principles:
-
Define Value- Identify the added value your company brings to society. What makes you stand out from your competitors?
-
Reduce Waste – Eliminate all activities that don't add value throughout the supply chain.
-
Create Flow - Ensure work moves smoothly through the process without interruption.
-
Standardize & simplify - Make processes consistent and repeatable.
-
Develop Relationships: Establish personal relationships both with internal and external stakeholders.
Lean manufacturing is not a new concept, but it has been gaining popularity over the last few years due to a renewed interest in the economy following the global financial crisis of 2008. Many businesses have adopted lean manufacturing techniques to help them become more competitive. Many economists believe lean manufacturing will play a major role in economic recovery.
Lean manufacturing, which has many benefits, is now a standard practice in the automotive industry. These include better customer satisfaction and lower inventory levels. They also result in lower operating costs.
Lean manufacturing can be applied to almost every aspect of an organization. However, it is particularly useful when applied to the production side of an organization because it ensures that all steps in the value chain are efficient and effective.
There are three types principally of lean manufacturing:
-
Just-in Time Manufacturing (JIT), also known as "pull system": This form of lean manufacturing is often referred to simply as "pull". JIT refers to a system in which components are assembled at the point of use instead of being produced ahead of time. This approach reduces lead time, increases availability and reduces inventory.
-
Zero Defects Manufacturing (ZDM),: ZDM is a system that ensures no defective units are left the manufacturing facility. It is better to repair a part than have it removed from the production line if it needs to be fixed. This is true even for finished products that only require minor repairs prior to shipping.
-
Continuous Improvement (CI), also known as Continuous Improvement, aims at improving the efficiency of operations through continuous identification and improvement to minimize or eliminate waste. It involves continuous improvement of processes, people, and tools.