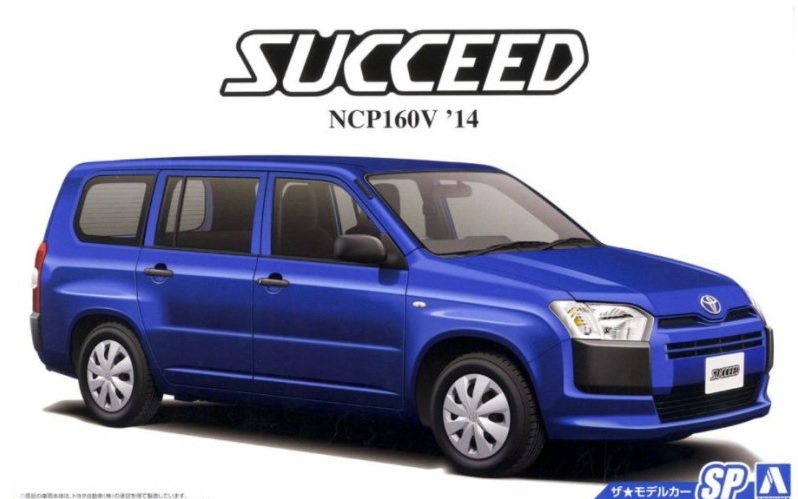
Industrial engineers design efficient systems that integrate workers, machines, materials, information and energy to make a product or provide a service. They may work in an office or in a production setting, such as a manufacturing facility or warehouse.
Industrial Engineer Entry Level in Texas
You will be responsible for making sure that the production process runs smoothly. You'll be responsible to analyze problems, troubleshoot issues and implement changes in order to improve efficiency. You may also be responsible for training and supporting technicians who use systems and equipment that you designed.
Your job duties vary depending on the type of company you work for and what their needs are. Some manufacturers may require you to create a system for the handling of hazardous waste. Some require you to design a system of monitoring and controlling raw materials.
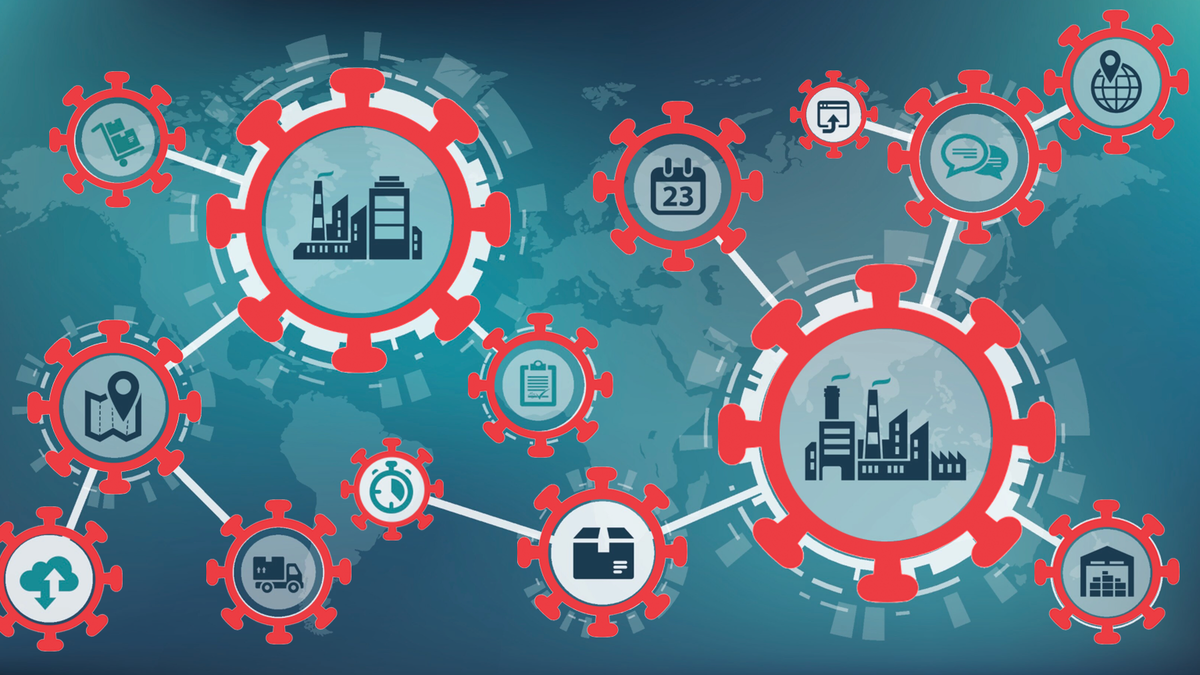
As manufacturers are constantly looking for ways of cutting costs and increasing efficiency, you may be working on projects that reduce waste in the production process. This could involve reducing the amount of inventory in a warehouse, improving the efficiency of machinery or identifying and eliminating any wasteful practices.
You could work for a manufacturer of transportation equipment, or an electronics and computer firm. These are usually full-time jobs, and employment growth is expected to be 10% in the next decade.
Manufacturing Engineering Jobs in Texas
Start your career in industrial engineering by taking a job at a company that makes heavy machinery, or energy equipment. This is a great way to learn about industrial engineering, and many plant managers seek out candidates with this experience.
While working at the facility, you are expected to attend seminars and participate in training. You will be able to become a better member of the team by participating in these training programs. You may also be asked to conduct specialized research, which helps you improve your skills as an Industrial Engineer.
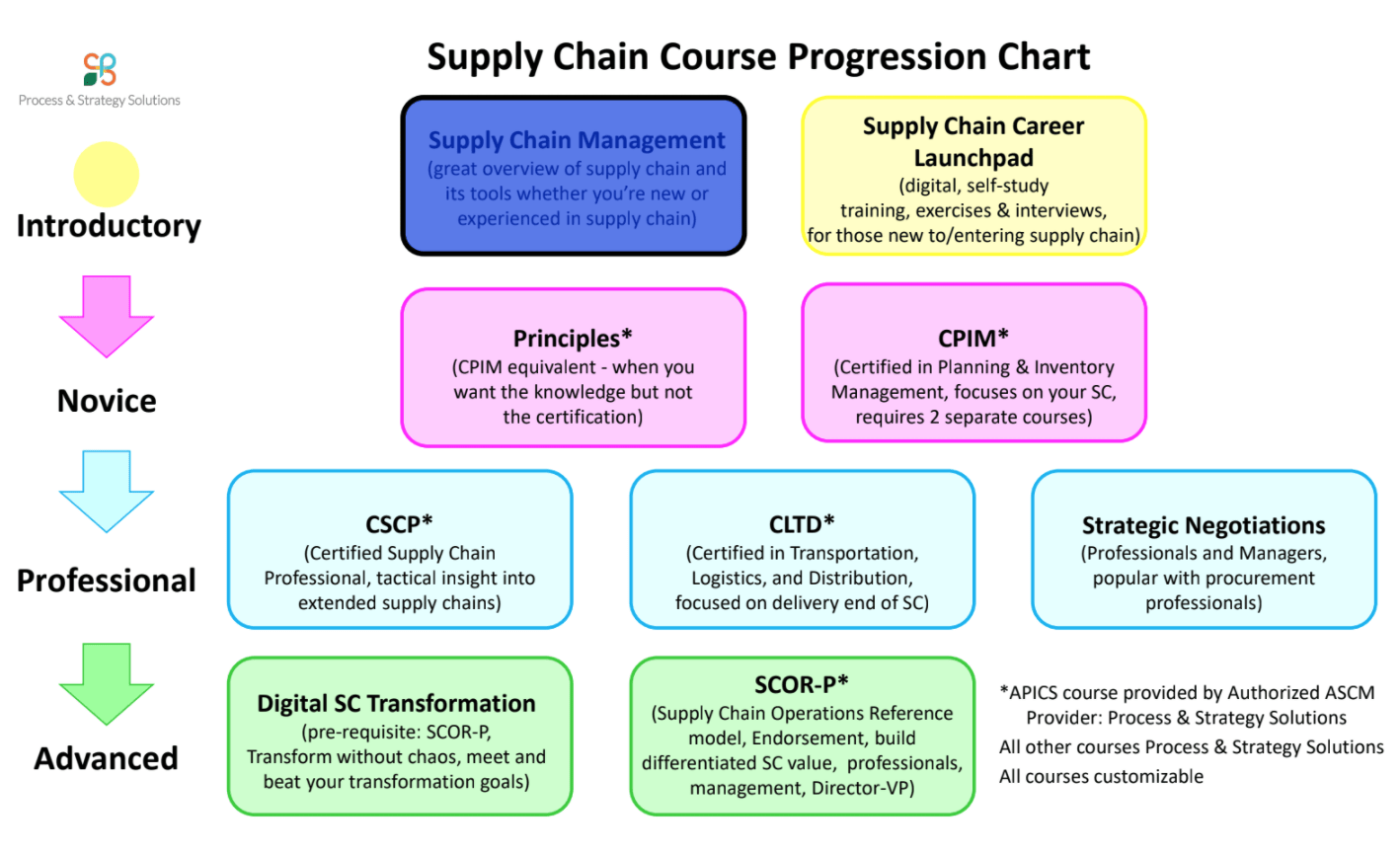
Eastman is a Manufacturing Engineer
If your skills are in the right place, you could be offered a position as an industrial engineer at Eastman Chemical in Mcallen, Texas. This fast-paced, rewarding job offers you the chance to work for a leading energy and technology company.
You will be an integral part of the industrial engineering team, responsible for implementing and maintaining engineered work standards in distribution centers throughout the country. As a member of an industrial engineering team, you will be responsible for providing engineering labor standard to associates in these facilities.
FAQ
How can manufacturing prevent production bottlenecks?
Avoiding production bottlenecks is as simple as keeping all processes running smoothly, from the time an order is received until the product ships.
This includes planning to meet capacity requirements and quality control.
Continuous improvement techniques like Six Sigma are the best way to achieve this.
Six Sigma Management System is a method to increase quality and reduce waste throughout your organization.
It is focused on creating consistency and eliminating variation in your work.
What is the importance of automation in manufacturing?
Automation is important not only for manufacturers but also for service providers. They can provide services more quickly and efficiently thanks to automation. In addition, it helps them reduce costs by reducing human errors and improving productivity.
What skills does a production planner need?
A production planner must be organized, flexible, and able multitask to succeed. It is also important to be able communicate with colleagues and clients.
Why is logistics so important in manufacturing?
Logistics are an essential component of any business. They enable you to achieve outstanding results by helping manage product flow from raw materials through to finished goods.
Logistics plays a significant role in reducing cost and increasing efficiency.
Statistics
- It's estimated that 10.8% of the U.S. GDP in 2020 was contributed to manufacturing. (investopedia.com)
- (2:04) MTO is a production technique wherein products are customized according to customer specifications, and production only starts after an order is received. (oracle.com)
- Job #1 is delivering the ordered product according to specifications: color, size, brand, and quantity. (netsuite.com)
- You can multiply the result by 100 to get the total percent of monthly overhead. (investopedia.com)
- [54][55] These are the top 50 countries by the total value of manufacturing output in US dollars for its noted year according to World Bank.[56] (en.wikipedia.org)
External Links
How To
How to use Lean Manufacturing in the production of goods
Lean manufacturing refers to a method of managing that seeks to improve efficiency and decrease waste. It was developed in Japan between 1970 and 1980 by Taiichi Ohno. TPS founder Kanji Tyoda gave him the Toyota Production System, or TPS award. Michael L. Watkins published the "The Machine That Changed the World", the first book about lean manufacturing. It was published in 1990.
Lean manufacturing refers to a set of principles that improve the quality, speed and costs of products and services. It emphasizes the elimination of defects and waste throughout the value stream. Lean manufacturing is called just-in-time (JIT), zero defect, total productive maintenance (TPM), or 5S. Lean manufacturing seeks to eliminate non-value added activities, such as inspection, work, waiting, and rework.
Lean manufacturing not only improves product quality but also reduces costs. Companies can also achieve their goals faster by reducing employee turnover. Lean manufacturing can be used to manage all aspects of the value chain. Customers, suppliers, distributors, retailers and employees are all included. Many industries worldwide use lean manufacturing. Toyota's philosophy is a great example of this. It has helped to create success in automobiles as well electronics, appliances and healthcare.
Five fundamental principles underlie lean manufacturing.
-
Define Value - Determine the value that your business brings to society. Also, identify what sets you apart from your competitors.
-
Reduce Waste - Eliminate any activity that doesn't add value along the supply chain.
-
Create Flow: Ensure that the work process flows without interruptions.
-
Standardize and Simplify – Make processes as consistent, repeatable, and as simple as possible.
-
Develop Relationships: Establish personal relationships both with internal and external stakeholders.
Although lean manufacturing isn't a new concept in business, it has gained popularity due to renewed interest in the economy after the 2008 global financial crisis. Many businesses have adopted lean production techniques to make them more competitive. In fact, some economists believe that lean manufacturing will be an important factor in economic recovery.
With many benefits, lean manufacturing is becoming more common in the automotive industry. These include higher customer satisfaction levels, reduced inventory levels as well as lower operating costs.
You can apply Lean Manufacturing to virtually any aspect of your organization. Because it makes sure that all value chains are efficient and effectively managed, Lean Manufacturing is particularly helpful for organizations.
There are three types principally of lean manufacturing:
-
Just-in Time Manufacturing: This lean manufacturing method is commonly called "pull systems." JIT is a method in which components are assembled right at the moment of use, rather than being manufactured ahead of time. This approach is designed to reduce lead times and increase the availability of components. It also reduces inventory.
-
Zero Defects Manufacturing - ZDM: ZDM focuses its efforts on making sure that no defective units leave a manufacturing facility. If a part is required to be repaired on the assembly line, it should not be scrapped. This applies to finished products, which may need minor repairs before they are shipped.
-
Continuous Improvement: Continuous Improvement aims to improve efficiency by continually identifying problems and making adjustments to eliminate or minimize waste. It involves continuous improvement of processes, people, and tools.