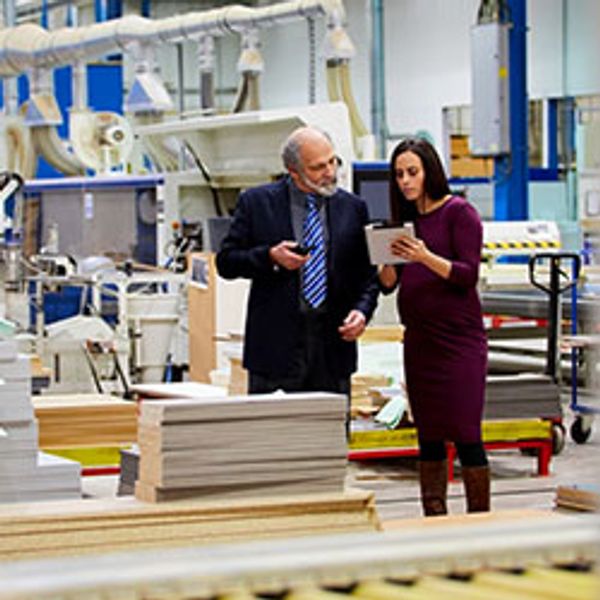
The United States is seeing a decrease in manufacturing jobs. This trend has also affected non-college educated workers. This includes Black workers, women, and minorities. These groups are being left behind by the declines in manufacturing employment. Here's a look into how many people are being left behind.
Trends in manufacturing jobs
Globalization's impact on US manufacturing employment is a key question in 2019. Despite the fact that the industry employs more than 40 million people each year, it continues to lose 3.5 millions jobs each year. This decline in employment is due to macroeconomic factors such as taxation, government spending, and Federal Reserve actions.
There is increased competition in the manufacturing sector for entry-level workers. Since the peak of the twentieth-century, the number of manufacturing jobs is steadily decreasing. Manufacturing was nearly 30% of the total workforce by 1952. That figure has dropped to 8 percent by 2019. A few economists don't consider this to be a manufacturing slump. However, it is lower than the average during a recession. For example, the ISM Index is 47.2 which is higher than the low 40s in a recession.
The eight census regions had wildly different levels of manufacturing employment in the United States. Northeast has the highest concentration. The mid Atlantic states, however, had the lowest concentrations in manufacturing employment.
Trends in manufacturing output
The US manufacturing sector is a key indicator of the economy. The economic recovery that occurred in the third quarter of 2016 is a sign of sustained growth. However, manufacturers face many challenges. Not only are rising costs increasing, but it's also becoming more difficult for manufacturers to find the right raw materials and components. AbhijitBhide examines five key trends affecting the US manufacturing sector. He also discusses what these changes mean for small and mid-sized businesses.
Younger people tend to believe that US manufacturing output has increased. Older people, however are less likely to believe it has dropped. About half of those aged 50-64 believe that manufacturing output has increased over the past three years, while 39% of those between 18 and 29 are more optimistic. In addition, income levels appear to have an effect on the perception of manufacturing output. The perception of manufacturing output is affected by income levels. Those who earn $100,000 per year are more likely than those who earn $30,000 to 49999 to believe that manufacturing output is lower.
FAQ
What can I do to learn more about manufacturing?
Experience is the best way for you to learn about manufacturing. You can also read educational videos or take classes if this isn't possible.
How can manufacturing excess production be decreased?
It is essential to find better ways to manage inventory to reduce overproduction. This would reduce the time spent on unproductive activities like purchasing, storing and maintaining excess stock. We could use these resources to do other productive tasks.
One way to do this is to adopt a Kanban system. A Kanban board is a visual display used to track work in progress. Kanban systems are where work items travel through a series of states until reaching their final destination. Each state represents a different priority.
As an example, if work is progressing from one stage of the process to another, then the current task is complete and can be transferred to the next. However, if a task is still at the beginning stages, it will remain so until it reaches the end of the process.
This allows for work to continue moving forward, while also ensuring that there is no work left behind. Managers can see how much work has been done and the status of each task at any time with a Kanban Board. This data allows them adjust their workflow based upon real-time data.
Lean manufacturing is another option to control inventory levels. Lean manufacturing works to eliminate waste throughout every stage of the production chain. Waste includes anything that does not add value to the product. The following are examples of common waste types:
-
Overproduction
-
Inventory
-
Unnecessary packaging
-
Overstock materials
Manufacturers can increase efficiency and decrease costs by implementing these ideas.
What are the responsibilities of a manufacturing manager
A manufacturing manager has to ensure that all manufacturing processes work efficiently and effectively. They should be aware of any issues within the company and respond accordingly.
They should also learn how to communicate effectively with other departments, including sales and marketing.
They should be informed about industry trends and be able make use of this information to improve their productivity and efficiency.
What are the responsibilities of a logistic manager?
Logistics managers ensure that goods arrive on time and are unharmed. This is accomplished by using the experience and knowledge gained from working with company products. He/she should also ensure enough stock is available to meet demand.
Why is logistics important in manufacturing?
Logistics is an integral part of every business. Logistics can help you achieve amazing results by helping to manage product flow from raw materials to finished products.
Logistics play a key role in reducing expenses and increasing efficiency.
What is the responsibility of a production planner?
Production planners ensure all aspects of the project are delivered within time and budget. They ensure that the product or service is of high quality and meets client requirements.
Statistics
- It's estimated that 10.8% of the U.S. GDP in 2020 was contributed to manufacturing. (investopedia.com)
- In 2021, an estimated 12.1 million Americans work in the manufacturing sector.6 (investopedia.com)
- Many factories witnessed a 30% increase in output due to the shift to electric motors. (en.wikipedia.org)
- According to the United Nations Industrial Development Organization (UNIDO), China is the top manufacturer worldwide by 2019 output, producing 28.7% of the total global manufacturing output, followed by the United States, Japan, Germany, and India.[52][53] (en.wikipedia.org)
- (2:04) MTO is a production technique wherein products are customized according to customer specifications, and production only starts after an order is received. (oracle.com)
External Links
How To
How to use Lean Manufacturing in the production of goods
Lean manufacturing refers to a method of managing that seeks to improve efficiency and decrease waste. It was created in Japan by Taiichi Ohno during the 1970s and 80s. He received the Toyota Production System award (TPS), from Kanji Toyoda, founder of TPS. Michael L. Watkins published the first book on lean manufacturing in 1990.
Lean manufacturing refers to a set of principles that improve the quality, speed and costs of products and services. It is about eliminating defects and waste from all stages of the value stream. Lean manufacturing is called just-in-time (JIT), zero defect, total productive maintenance (TPM), or 5S. Lean manufacturing seeks to eliminate non-value added activities, such as inspection, work, waiting, and rework.
Lean manufacturing can help companies improve their product quality and reduce costs. Additionally, it helps them achieve their goals more quickly and reduces employee turnover. Lean manufacturing has been deemed one of the best ways to manage the entire value-chain, including customers, distributors as well retailers and employees. Lean manufacturing practices are widespread in many industries. Toyota's philosophy, for example, is what has enabled it to be successful in electronics, automobiles, medical devices, healthcare and chemical engineering as well as paper and food.
Lean manufacturing is based on five principles:
-
Define Value - Identify the value your business adds to society and what makes you different from competitors.
-
Reduce waste - Stop any activity that isn't adding value to the supply chains.
-
Create Flow. Ensure that your work is uninterrupted and flows seamlessly.
-
Standardize and simplify - Make your processes as consistent as possible.
-
Build Relationships- Develop personal relationships with both internal as well as external stakeholders.
Although lean manufacturing isn't a new concept in business, it has gained popularity due to renewed interest in the economy after the 2008 global financial crisis. Many businesses are now using lean manufacturing to improve their competitiveness. Many economists believe lean manufacturing will play a major role in economic recovery.
Lean manufacturing is now becoming a common practice in the automotive industry, with many benefits. These include higher customer satisfaction, lower inventory levels, lower operating expenses, greater productivity, and improved overall safety.
Lean manufacturing can be applied to almost every aspect of an organization. Lean manufacturing is most useful in the production sector of an organisation because it ensures that each step in the value-chain is efficient and productive.
There are three types of lean manufacturing.
-
Just-in Time Manufacturing (JIT), also known as "pull system": This form of lean manufacturing is often referred to simply as "pull". JIT stands for a system where components are assembled on the spot rather than being made in advance. This method reduces lead times, increases availability, and decreases inventory.
-
Zero Defects Manufacturing: ZDM ensures that no defective units leave the manufacturing plant. It is better to repair a part than have it removed from the production line if it needs to be fixed. This is also true for finished products that require minor repairs before shipping.
-
Continuous Improvement (CI: Continuous improvement aims to increase the efficiency of operations by constantly identifying and making improvements to reduce or eliminate waste. Continuous Improvement (CI) involves continuous improvement in processes, people, tools, and infrastructure.