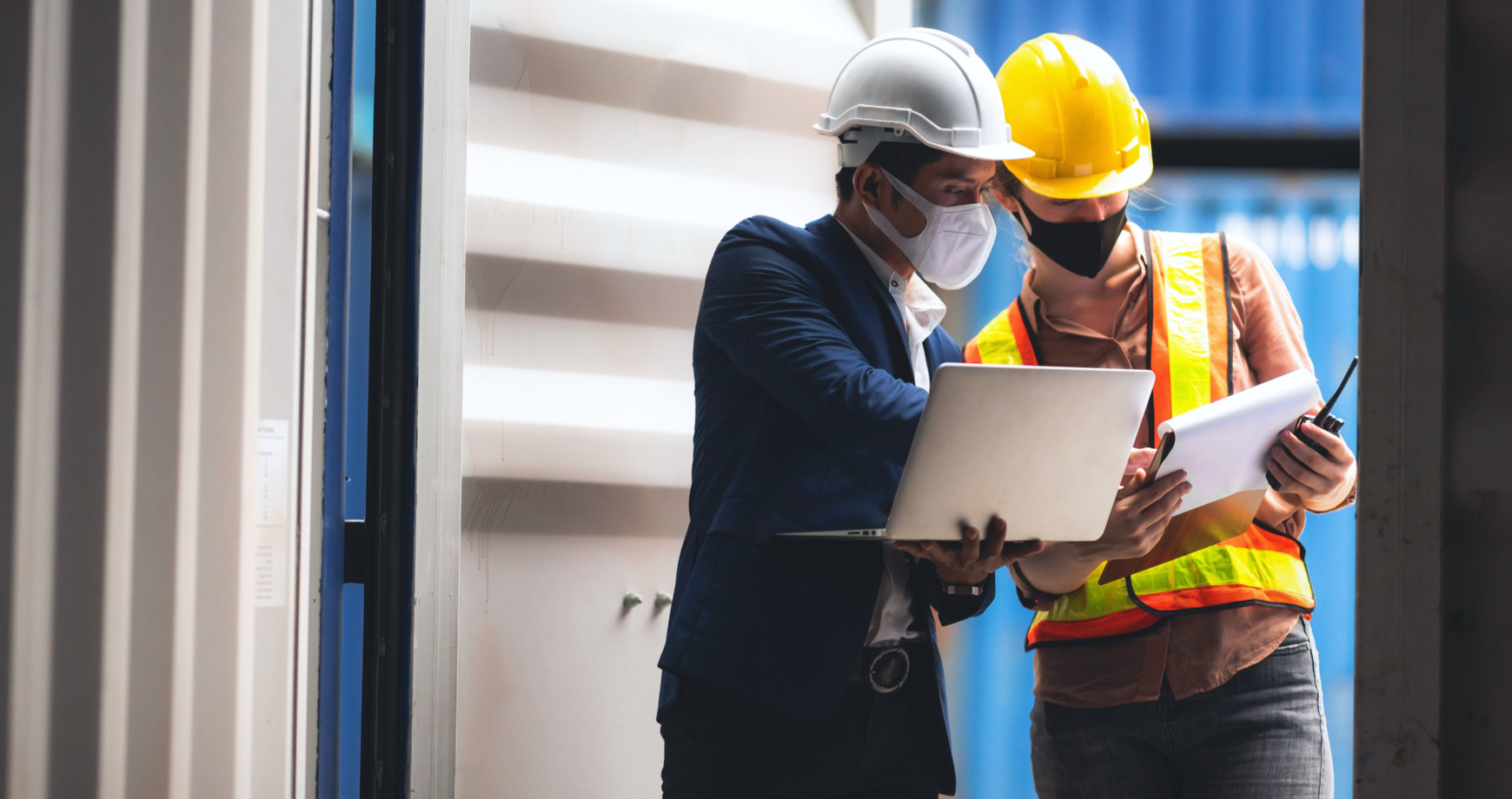
Are you searching for jobs in logistics in New Jersey? These jobs can be in any setting and require many skills. A bachelor's degree is preferable. You need these qualifications to become a logistics manager. These skills include the ability to work independently and problem-solve. You must have a positive outlook and be a problem-solver naturally.
A bachelor's degree in engineering is required
To be eligible for jobs in logistics, you need a Bachelor’s degree from an accredited college, plus 4+ years relevant experience. You also need proven time-management and organizational skills. Strong communication skills are essential, as well as a command of English. Furthermore, you will need to be proficient in data analysis, have demonstrated leadership skills, and possess excellent interpersonal skills.
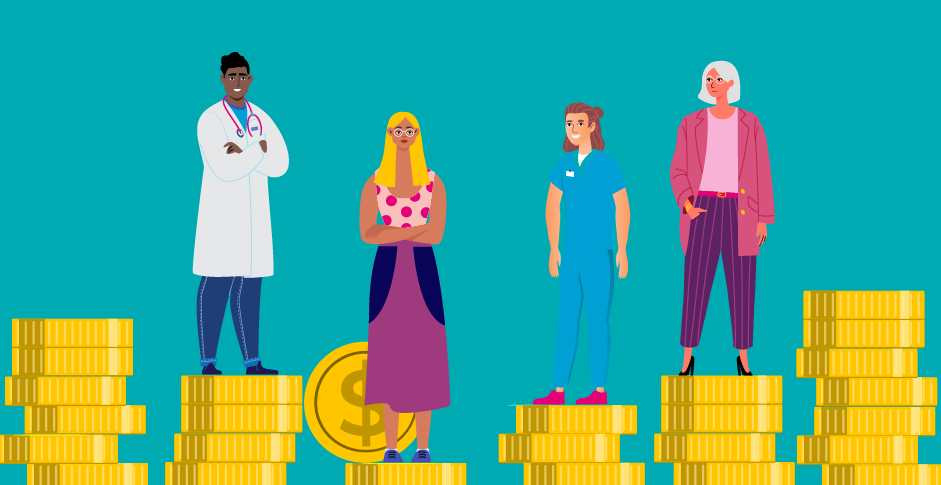
For many of these jobs, a bachelor's degree is required in New Jersey in logistics. The majority of jobs in this area are mid-skill but you can still make lots of money by applying what you know to different industries. New Jersey is home to many middle-skill jobs, which require workers who have received specialized training. NJCU's Center for Workforce and Community Development has one of these middle skill programs.
Employers may consider working in logistics if you have prior experience. Prior experience can make you more marketable and increase your chances of getting hired. A bachelor's degree in logistics can get you a job working as a customer service representative, or as a freight agent. With experience and advanced credentials, higher-level positions in logistics will open up, such as in management. Additionally, you may be able to pursue further education in logistics such as teaching or research.
It is preferable to have a bachelor’s degree
Some logistics positions require a bachelor’s education. Bachelor’s degrees in related fields are often preferred. A bachelor's degree in logistics is preferable by most employers as it allows them the ability to handle complicated supply chain and transportation laws. Additionally, bachelor's degrees give students a solid background in logistics which allows them to expand their professional network. You could work as a customer representative or freight agent in a entry-level logistic position. Management positions may become possible if you have an advanced education and are qualified. Research, consulting, and teaching are all options for higher-level logistics jobs.
Most employers prefer a bachelor's in logistics. However, an associate's may be acceptable. Sometimes, work experience can be substituted for education in certain situations. Work experience in specific areas, such as warehouse management or data analysis, can also be helpful to job seekers. However, a bachelor's degree will still be preferred for logistics jobs in New Jersey. A bachelor's level in logistics will enable you to fully understand the supply chain. Numerous companies, especially those who deal with large-scale transactions, require a bachelor’s degree in logistic.
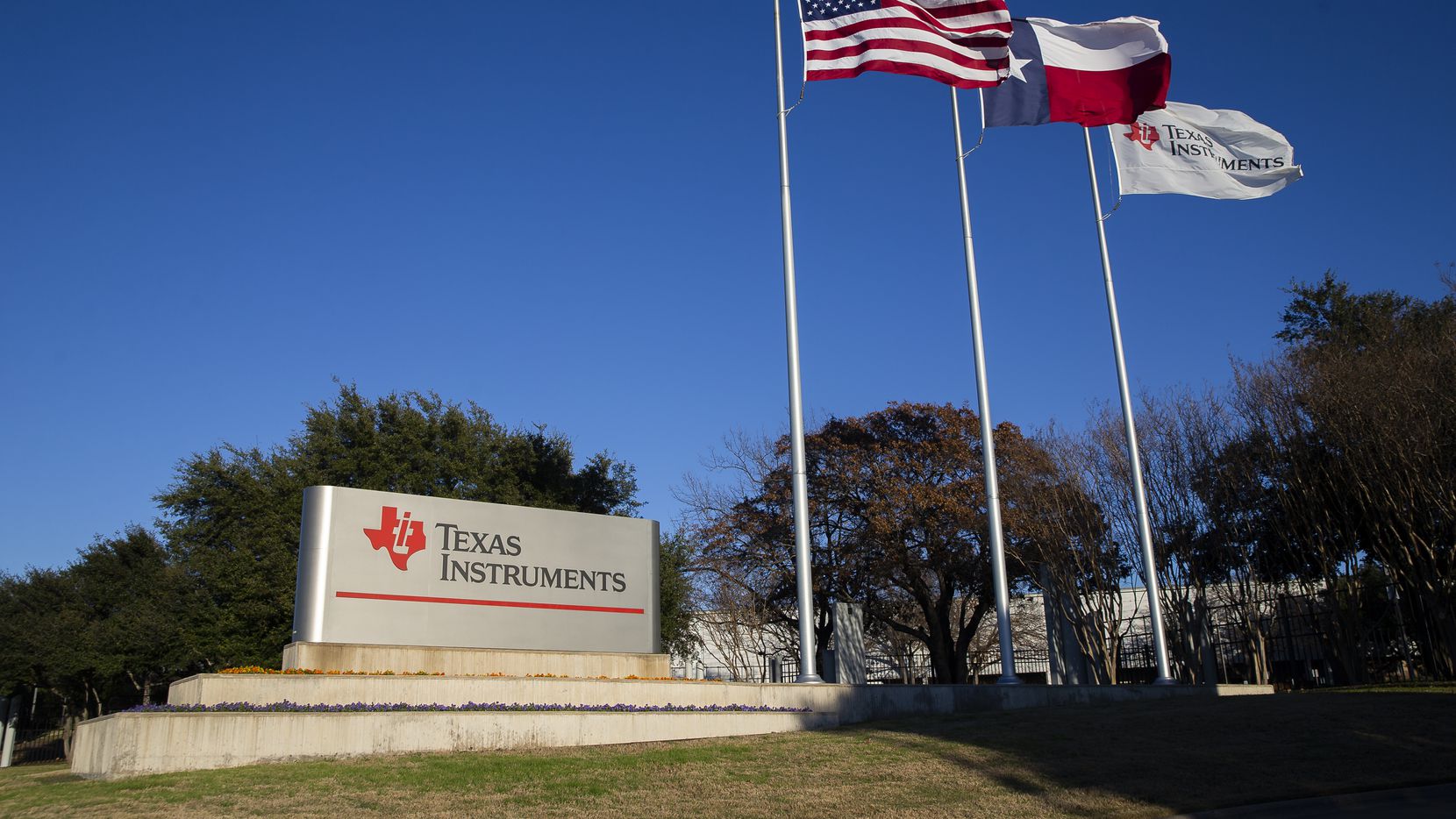
A bachelor's degree and experience in manufacturing are required if you want to be an Industrial Engineer. Furthermore, you should be able speak fluently with employees and have knowledge about municipal coding rules. A minimum of six years work experience is required for an Industrial Engineer. You should also be familiar with similar working conditions in other industries to which you are applying.
FAQ
What is the difference between Production Planning and Scheduling?
Production Planning (PP), is the process of deciding what production needs to take place at any given time. Forecasting and identifying production capacity are two key elements to this process.
Scheduling refers the process by which tasks are assigned dates so that they can all be completed within the given timeframe.
What are the 7 Rs of logistics management?
The 7R's of Logistics is an acronym for the seven basic principles of logistics management. It was developed by International Association of Business Logisticians (IABL), and published as part of their "Seven Principles of Logistics Management Series" in 2004.
The acronym is made up of the following letters:
-
Responsible - ensure that all actions taken are within legal requirements and are not harmful to others.
-
Reliable: Have faith in your ability or the ability to honor any promises made.
-
It is reasonable to use resources efficiently and not waste them.
-
Realistic - consider all aspects of operations, including cost-effectiveness and environmental impact.
-
Respectful – Treat others fairly and equitably.
-
Responsive - Look for ways to save time and increase productivity.
-
Recognizable: Provide customers with value-added service
What are the products and services of logistics?
Logistics refers to the movement of goods from one place to another.
They include all aspects associated with transport including packaging, loading transporting, unloading storage, warehousing inventory management customer service, distribution returns and recycling.
Logisticians make sure that the right product arrives at the right place at the correct time and in safe conditions. They assist companies with their supply chain efficiency through information on demand forecasts. Stock levels, production times, and availability.
They coordinate with vendors and suppliers, keep track of shipments, monitor quality standards and perform inventory and order replenishment.
How can we increase manufacturing efficiency?
The first step is to determine the key factors that impact production time. Then we need to find ways to improve these factors. You can start by identifying the most important factors that impact production time. Once you have identified them, it is time to identify solutions.
How does a Production Planner differ from a Project Manager?
The major difference between a Production Planner and a Project Manager is that a Project Manager is often the person responsible for organizing and planning the entire project. While a Production Planner is involved mainly in the planning stage,
What is the best way to learn about manufacturing?
Hands-on experience is the best way to learn more about manufacturing. You can read books, or watch instructional videos if you don't have the opportunity to do so.
Statistics
- Many factories witnessed a 30% increase in output due to the shift to electric motors. (en.wikipedia.org)
- You can multiply the result by 100 to get the total percent of monthly overhead. (investopedia.com)
- Job #1 is delivering the ordered product according to specifications: color, size, brand, and quantity. (netsuite.com)
- It's estimated that 10.8% of the U.S. GDP in 2020 was contributed to manufacturing. (investopedia.com)
- In the United States, for example, manufacturing makes up 15% of the economic output. (twi-global.com)
External Links
How To
How to Use the Just-In-Time Method in Production
Just-in-time (JIT) is a method that is used to reduce costs and maximize efficiency in business processes. This is where you have the right resources at the right time. This means that you only pay for what you actually use. Frederick Taylor developed the concept while working as foreman in early 1900s. He saw how overtime was paid to workers for work that was delayed. He decided to ensure workers have enough time to do their jobs before starting work to improve productivity.
JIT is an acronym that means you need to plan ahead so you don’t waste your money. You should also look at the entire project from start to finish and make sure that you have sufficient resources available to deal with any problems that arise during the course of your project. If you anticipate that there might be problems, you'll have enough people and equipment to fix them. This will ensure that you don't spend more money on things that aren't necessary.
There are several types of JIT techniques:
-
Demand-driven: This type of JIT allows you to order the parts/materials required for your project on a regular basis. This will allow to track how much material has been used up. This will allow you to calculate how long it will take to make more.
-
Inventory-based: You stock materials in advance to make your projects easier. This allows one to predict how much they will sell.
-
Project-driven: This approach involves setting aside sufficient funds to cover your project's costs. Once you have an idea of how much material you will need, you can purchase the necessary materials.
-
Resource-based JIT is the most widespread form. This is where you assign resources based upon demand. You will, for example, assign more staff to deal with large orders. If you don't have many orders, you'll assign fewer people to handle the workload.
-
Cost-based : This is similar in concept to resource-based. But here, you aren't concerned about how many people your company has but how much each individual costs.
-
Price-based: This approach is very similar to the cost-based method except that you don't look at individual workers costs but the total cost of the company.
-
Material-based: This is very similar to cost-based but instead of looking at total costs of the company you are concerned with how many raw materials you use on an average.
-
Time-based JIT: This is another variant of resource-based JIT. Instead of focusing solely on the amount each employee costs, focus on how long it takes for the project to be completed.
-
Quality-based JIT - This is another form of resource-based JIT. Instead of thinking about the cost of each employee or the time it takes to produce something, you focus on how good your product quality.
-
Value-based: This is one of the newest forms of JIT. This is where you don't care about how the products perform or whether they meet customers' expectations. Instead, your focus is on the value you bring to the market.
-
Stock-based: This inventory-based approach focuses on how many items are being produced at any one time. This is used to increase production and minimize inventory.
-
Just-in-time planning (JIT): This is a combination JIT and supply-chain management. This refers to the scheduling of the delivery of components as soon after they are ordered. It is essential because it reduces lead-times and increases throughput.